What is the significance of a specific, potentially complex, and possibly controversial process related to a particular object? A thorough understanding of this process is crucial for comprehending the broader topic.
The term "carthon" in this context likely refers to a specific method or procedure used in the manipulation or handling of a material or object. Without further context, it is impossible to provide a precise definition. It could relate to a manufacturing process, a scientific technique, or a step within a specific workflow. For instance, if the context is automotive manufacturing, "ran carthon" might refer to a particular stage of car body assembly or painting. An example sentence could clarify this, like "Ran carthon steps were meticulously followed for the final assembly." A complete understanding requires more information about the specific object, process, and field of application.
The importance of this process hinges entirely on the context in which it is applied. Understanding the methodology behind it may be key to optimization, cost reduction, enhanced quality, or increased efficiency within the relevant domain. Historical context, if available, will provide additional insights into the process's development, evolution, and impact. The benefits of mastering this process would depend on its specific application.
To proceed with a detailed analysis, further context is needed. The article will now delve into the overall topic area, exploring the wider implications of this process within its relevant field.
Ran Carthon
Understanding the procedural elements of "ran carthon" is essential for comprehending its role in various processes. Precise definitions and operational considerations are crucial.
- Process Description
- Material Handling
- Quality Control
- Efficiency Metrics
- Safety Protocols
- Environmental Impact
- Cost Analysis
The key aspects of "ran carthon" illuminate different facets of its operational scope. Process description details the specific steps involved. Material handling emphasizes the movement and management of components. Quality control metrics ascertain the process's consistency and reliability. Efficiency measurements determine the effectiveness and yield of the procedure. Safety protocols underscore the importance of preventative measures. Environmental considerations analyze the procedure's impact on surrounding ecosystems. Cost analysis reveals the financial implications of implementation, highlighting potential savings or increases. Taken together, these elements provide a comprehensive understanding of "ran carthon" within its relevant domain. For example, meticulous quality control in "ran carthon" reduces defects and rework, leading to increased overall efficiency and profitability. Analyzing environmental impacts during the "ran carthon" process ensures sustainable practices within a particular industry.
- Best Osteria Consani Deals Reviews Experience Authentic Italian Cuisine
- Ultimate Buzzz Tube Guide Reviews
1. Process Description
A clear process description of "ran carthon" is fundamental to understanding its function and application. Precisely outlining the steps involved, including sequence, resources, and necessary personnel, directly influences operational efficiency and outcome. This detailed description enables effective analysis, improvement, and adaptation of the process.
- Step-by-Step Sequence
The sequential order of steps within "ran carthon" dictates the workflow. Deviation from this sequence can result in errors, delays, or production issues. Documentation of the exact steps allows for consistency, replication, and problem-solving when issues arise. Accurate sequencing is essential, for instance, in manufacturing processes where the order of component assembly critically impacts the final product quality. A misordering of steps in "ran carthon" could lead to damaged material or incorrect assembly.
- Resource Allocation
Identification of necessary resourcesequipment, materials, personnelis crucial for proper execution of "ran carthon." Insufficient resources directly impact the process's efficiency, leading to delays or poor quality. Understanding the specific equipment used in "ran carthon" is vital for maintenance, repair, and optimal performance. Precise allocation of staff according to their expertise ensures optimal results. Incorrect allocation of labor resources in "ran carthon" could result in bottlenecks and reduced throughput.
- Input and Output Specifications
Detailed specifications of input materials and expected output products are critical in "ran carthon." These specifications ensure the process adheres to established quality standards and that input materials and final products meet pre-defined criteria. Precise input and output specifications in "ran carthon" help to pinpoint areas of potential malfunction or waste generation.
- Safety Considerations
Safety protocols and procedures are integral to "ran carthon." Clearly outlining potential hazards and appropriate safety measures ensures the well-being of personnel involved. A clear description of safety protocols minimizes workplace injuries. Failure to include these critical elements in a "ran carthon" process description can lead to costly accidents and violations.
In conclusion, a comprehensive process description for "ran carthon" goes beyond simply listing steps. It encompasses critical aspects like sequencing, resource requirements, specification adherence, and safety considerations. A robust description of "ran carthon" fosters efficiency, reduces errors, and enhances safety within the operational workflow.
2. Material Handling
Material handling within the context of "ran carthon" is critical. Effective management of materials directly impacts process efficiency, quality, and safety. Proper handling protocols minimize damage, ensure timely movement, and reduce overall costs. This section explores key facets of material handling within the "ran carthon" procedure.
- Quantity and Type of Material
Accurate assessment of material quantity and precise identification of material types are paramount. Insufficient or excessive material can hinder the "ran carthon" process. Misidentification of material types can lead to errors in subsequent stages. Consistency and accuracy in material handling are crucial for quality control. For example, if "ran carthon" involves assembling components, mismatched parts due to inaccurate material handling significantly affect the final product and potentially require significant rework.
- Storage and Organization
Efficient storage and organization of materials before, during, and after the "ran carthon" process are crucial for optimal workflow. Proper organization minimizes searching time, reduces errors, and maintains an orderly work environment. Effective storage systems prevent material damage and maintain consistent access for the process. Poor organization can result in misplaced components leading to delays and rework, hindering the efficiency of "ran carthon."
- Transportation and Movement
Safe and efficient transportation of materials during the "ran carthon" process is essential. Adequate equipment for handling specific materials is vital for preventing damage and ensuring smooth movement. Careful consideration of material weight, fragility, and dimensions ensures damage-free transport during all stages of "ran carthon." Improper handling during transport can lead to component damage, delays, and significant loss in efficiency.
- Documentation and Tracking
Detailed documentation of material movements and handling procedures is integral to "ran carthon." This allows for accurate tracking, traceability, and audit capabilities. Maintaining comprehensive records assists in problem-solving and process improvement. Clear documentation also enables easy identification of issues or bottlenecks. Inadequate documentation hinders effective quality control and problem identification within "ran carthon." Missing documentation often leads to wasted time and resources, hindering the ability to improve the process.
In conclusion, effective material handling is intricately linked to the success of "ran carthon." Careful consideration of material types, storage, transportation, and documentation are essential to ensure efficiency, quality, and safety throughout the entire process. A thorough approach to material handling significantly contributes to the optimization of the "ran carthon" procedure.
3. Quality Control
Quality control (QC) is integral to the "ran carthon" process. Effective QC ensures adherence to standards, minimizes defects, and maximizes the overall value of the output. Without robust QC measures, the "ran carthon" process risks producing substandard results, leading to potential rework, increased costs, and compromised customer satisfaction. This section explores critical aspects of QC within the "ran carthon" framework.
- Inspection and Testing Protocols
Implementing standardized inspection and testing protocols at various stages of "ran carthon" is crucial. These protocols should clearly define acceptable standards for materials, components, and final products. Inspection protocols should encompass visual examinations, dimensional measurements, and functional tests, ensuring conformity to specifications. Failure to enforce rigorous testing procedures in "ran carthon" can result in the release of defective products or components, leading to downstream issues and cost overruns.
- Defect Detection and Prevention
Proactive identification and rectification of potential defects are key elements in quality control. Early detection of flaws during the "ran carthon" process minimizes their progression and impact. This may involve utilizing quality control checklists, employing advanced tools for defect analysis, or introducing preventative measures to reduce the likelihood of defects arising in the first place. Implementing an efficient defect tracking system is paramount for monitoring and managing identified issues, enabling targeted corrections and improvements in "ran carthon".
- Data Analysis and Process Improvement
Analyzing quality control data collected throughout the "ran carthon" process is vital for continuous improvement. Patterns and trends within the data can highlight areas needing attention, enabling process modifications to mitigate or eliminate recurring problems. Statistical process control (SPC) methods can aid in identifying fluctuations in quality, revealing underlying causes and opportunities for optimization. Utilizing this data in a feedback loop enhances quality control by implementing preventative measures and improving the overall efficiency of "ran carthon".
- Employee Training and Standardization
Adequate training for personnel involved in quality control is essential. Ensuring staff understands the critical parameters and procedures of the "ran carthon" process ensures consistency in quality control. Standardized training protocols minimize variation in inspection and testing procedures, maintaining an expected level of quality. Inconsistency in staff application of quality control methods can lead to varied quality outcomes in "ran carthon", affecting the overall standardization of the process.
Effective quality control in "ran carthon" is not a standalone activity but an integrated part of the entire process. The principles outlined above should be implemented consistently, allowing for continuous improvement, preventing defects, and ultimately enhancing the overall performance of "ran carthon." Comprehensive quality control measures contribute to the reliability, efficiency, and value of the products or outcomes originating from the "ran carthon" process.
4. Efficiency Metrics
Quantifying the efficiency of the "ran carthon" process is crucial for optimization and improvement. Metrics provide a standardized framework for evaluating performance, identifying bottlenecks, and driving cost-effective enhancements. Accurate measurement of key operational aspects within "ran carthon" facilitates informed decision-making and promotes consistent high-quality output. This analysis explores critical efficiency metrics relevant to the "ran carthon" process.
- Throughput Rate
Throughput rate, a core efficiency metric, measures the volume of output generated per unit of time. Calculating the rate of successful completions within "ran carthon" helps pinpoint areas of potential delay or excessive processing time. High throughput suggests efficient resource allocation and optimized workflows within the "ran carthon" process. For instance, in manufacturing, a low throughput rate might indicate a need for improved machinery maintenance or streamlined assembly procedures within "ran carthon".
- Cycle Time
Cycle time quantifies the total time required to complete a single unit or item within the "ran carthon" process. Optimizing cycle time leads to reduced lead times and higher productivity. Analysis of cycle time helps identify steps within "ran carthon" that might be prone to delays or inefficiencies, paving the way for process improvements and enhancements. In a production environment, a long cycle time within "ran carthon" could suggest needing to examine individual steps for potential speed improvements.
- Defect Rate
Defect rate measures the percentage of units or items produced that fail to meet quality standards within the "ran carthon" process. A high defect rate signifies a need for process improvements or additional quality control measures. Minimizing defects in "ran carthon" helps maintain product quality, reducing rework and associated costs. A low defect rate suggests high process reliability and fewer costly product corrections within "ran carthon".
- Resource Utilization
Resource utilization metrics quantify the degree to which available resources (personnel, equipment, materials) are effectively employed within the "ran carthon" process. Analyzing these metrics reveals potential under- or over-utilization of resources, contributing to more efficient allocation and better ROI. Determining the most appropriate utilization of machinery during each stage of "ran carthon" is pivotal to optimizing overall workflow.
In conclusion, various metrics, including throughput rate, cycle time, defect rate, and resource utilization, play vital roles in analyzing and improving the "ran carthon" process. By quantifying these key aspects, decision-makers can make data-driven decisions, resulting in a more efficient, cost-effective, and reliable "ran carthon" operation. Evaluating these metrics enables focused optimization efforts, ultimately enhancing productivity and output quality within the "ran carthon" context.
5. Safety Protocols
Safety protocols are indispensable components of any process, including "ran carthon." Adherence to these protocols is crucial for preventing workplace accidents, injuries, and property damage. Failure to prioritize safety can result in significant financial losses, legal liabilities, and a compromised work environment. This exploration examines the vital role of safety protocols within the "ran carthon" framework.
- Hazard Identification and Assessment
Thorough hazard identification and risk assessment are fundamental to establishing effective safety protocols. This involves proactively identifying potential dangers inherent in the "ran carthon" process, encompassing equipment malfunctions, material handling risks, environmental factors, and human error possibilities. Examples include identifying the potential for slips, trips, and falls on uneven surfaces during material transport; assessing the risk of equipment malfunction and associated pinch points; and identifying potential exposure to hazardous materials. Implementing safety measures tailored to these risks, such as providing appropriate safety footwear and installing safety guarding around machinery, directly relates to preventing accidents.
- Personal Protective Equipment (PPE) Requirements
Appropriate personal protective equipment (PPE) is vital for mitigating risks associated with specific tasks within "ran carthon." This might include specialized eyewear, hearing protection, gloves, respirators, or protective clothing, depending on the specific hazards involved in the "ran carthon" procedure. Appropriate PPE is crucial for safeguarding against chemical exposure, protecting against impacts and projections, and mitigating the risk of noise-induced hearing loss. For instance, utilizing appropriate respiratory protection during handling of certain materials is critical in "ran carthon" to prevent inhalation of hazardous substances. Failure to comply with PPE guidelines compromises worker safety.
- Emergency Procedures and Response Plans
Comprehensive emergency procedures and response plans are essential to manage potential incidents during "ran carthon." This includes establishing protocols for responding to fires, chemical spills, equipment malfunctions, or injuries. Plans should detail evacuation procedures, first aid protocols, and notification procedures. For instance, having a defined emergency response plan for spills of corrosive materials in "ran carthon" would mitigate further exposure or environmental damage. Proper emergency response systems minimize the impact of accidents.
- Training and Compliance
Regular training and strict adherence to safety regulations are crucial components of a strong safety program. Training equips personnel with the knowledge and skills to identify hazards, use safety equipment correctly, and follow emergency procedures. Compliance with safety protocols must be continuously monitored and reinforced. Consistency in applying training and protocols is vital for maintaining a safe work environment. Insufficient training or non-compliance with safety protocols directly increases the likelihood of accidents and injuries related to the "ran carthon" process.
Incorporating robust safety protocols into the "ran carthon" process is not merely a compliance requirement, but a fundamental aspect of workplace safety and responsible operational management. Prioritizing safety safeguards the well-being of personnel, protects company assets, and ensures the ongoing sustainability of the "ran carthon" procedures.
6. Environmental Impact
Assessing the environmental impact of "ran carthon" is paramount. The process's effects on air, water, and land necessitate careful consideration. Emissions, waste generation, and resource consumption all contribute to the overall environmental footprint. Understanding these interconnected factors is crucial for sustainability and responsible operation. Real-world examples illustrate the significance of this analysis. For example, industrial processes often generate significant air pollutants if not carefully managed. Likewise, improper waste disposal from "ran carthon" can contaminate water sources, posing threats to ecosystems. The resource intensity of the process further influences its environmental impact. A holistic approach, incorporating environmental considerations throughout the "ran carthon" design and execution stages, is vital for minimizing these effects. A failure to recognize and address these potential consequences can lead to ecological damage and create liabilities for the organization.
Practical applications of this understanding include implementing cleaner technologies, adopting sustainable material sourcing strategies, optimizing energy efficiency, and implementing comprehensive waste management systems. Furthermore, implementing robust monitoring and reporting procedures to track environmental indicators is crucial. Regular audits and environmental impact assessments can identify areas needing improvement and ensure compliance with relevant regulations. By integrating environmental considerations into decision-making, the long-term sustainability of "ran carthon" can be ensured. Examples include using renewable energy sources for power within the "ran carthon" process, utilizing recycled materials, or optimizing water usage to reduce water pollution.
In conclusion, the environmental impact of "ran carthon" is not a peripheral concern but a critical component of its overall performance. A thorough understanding of this impact, considering cause and effect and embracing sustainable practices, is crucial for long-term viability and societal well-being. This necessitates a shift toward processes that minimize pollution, conserve resources, and protect ecosystems. Addressing these environmental considerations directly improves the long-term sustainability of "ran carthon" and aligns the process with broader environmental responsibility. Challenges remain in achieving full sustainability across industries, but a proactive approach, like the detailed assessment of "ran carthon," remains a crucial step in meeting those challenges.
7. Cost Analysis
Cost analysis plays a critical role in evaluating the economic viability and efficiency of the "ran carthon" process. A thorough examination of costs associated with various stages, resources, and potential risks is essential for informed decision-making, optimizing resource allocation, and maximizing profitability. Understanding cost drivers, both direct and indirect, is key to streamlining operations and achieving sustainable cost management within the context of "ran carthon."
- Direct Material Costs
Direct material costs encompass the expenses of raw materials, components, and supplies directly consumed during the "ran carthon" process. Variances in material prices due to market fluctuations or supply chain disruptions can significantly affect these costs. In "ran carthon," accurate cost accounting for direct materials, like the specific type of metal sheets used in manufacturing, is crucial for budgeting and cost projections. Maintaining consistent supply sources and exploring alternative materials with comparable properties can mitigate the impact of price volatility on overall costs.
- Labor Costs
Labor costs related to "ran carthon" encompass wages, benefits, and overtime expenses of personnel involved in various stages, from material handling to quality control. Factors like skill level, labor market conditions, and employee turnover influence labor costs. Calculating labor costs accurately in "ran carthon" is essential for designing efficient workflows, evaluating the need for specialized personnel, and ensuring optimal utilization of labor resources. This analysis enables adjustments to staffing levels and optimization of employee productivity.
- Overhead Costs
Overhead costs associated with "ran carthon" include indirect expenses such as facility maintenance, utilities, rent, insurance, and administrative costs. These costs are often fixed or semi-fixed, adding consistent expense throughout the process. Understanding these overhead costs within "ran carthon" is essential for precisely determining the cost per unit produced and for making informed decisions regarding resource optimization and cost savings strategies.
- Quality Control and Rework Costs
Costs associated with quality control and rework are directly linked to the process's efficiency. A high defect rate in "ran carthon" leads to increased rework costs, requiring extra labor, materials, and potential scrap disposal. Effective quality control procedures, including rigorous testing protocols and process monitoring, reduce the probability of defects and mitigate the related costs. Identifying and addressing the root causes of defects within "ran carthon" significantly contributes to reducing overall costs.
A comprehensive cost analysis of "ran carthon" provides a clear picture of the process's economic performance. Thorough consideration of these cost components enables informed decisions related to resource allocation, process improvement, and overall profitability enhancement. By meticulously tracking and analyzing costs throughout the "ran carthon" process, organizations can identify areas for potential cost savings and optimize their operations for sustained profitability and competitiveness.
Frequently Asked Questions about "Ran Carthon"
This section addresses common inquiries regarding the "ran carthon" process. Clear and concise answers aim to provide comprehensive insights.
Question 1: What is "ran carthon"?
The term "ran carthon" likely refers to a specific method or procedure within a larger process, such as manufacturing or material handling. Without further context, a precise definition remains elusive. Its exact application and scope depend on the specific context. Additional details about the process are needed for a definitive understanding of "ran carthon."
Question 2: What are the key stages or steps involved in "ran carthon"?
The precise steps depend on the application of "ran carthon." A detailed process description is essential. This should include material handling, equipment specifications, sequence of operations, and personnel roles to understand the intricacies of the procedure.
Question 3: What are the potential benefits of implementing "ran carthon"?
The advantages of implementing "ran carthon" are directly related to its intended application. Potential benefits could range from increased efficiency, cost reductions, and improved quality to enhanced safety standards and environmental impact mitigation within specific operational contexts.
Question 4: What are the potential risks or challenges associated with "ran carthon"?
Potential risks and challenges vary according to the particular application of "ran carthon." These may include equipment malfunctions, material handling errors, human error, safety hazards, environmental issues, and potential cost overruns. A thorough assessment of these factors is imperative to mitigate risks and plan for contingencies.
Question 5: How can organizations ensure the effective implementation of "ran carthon"?
Effective implementation of "ran carthon" requires careful planning, thorough training of personnel, adherence to established safety protocols, consistent monitoring of key metrics, and continuous evaluation for process improvement. Clear documentation and communication across all stages of the process are vital.
In summary, understanding "ran carthon" necessitates a clear definition and comprehensive context. Key aspects include operational stages, potential benefits, associated risks, and crucial implementation strategies. Detailed descriptions and specific operational parameters are essential for a complete understanding of this process.
The following sections will provide further detail on the broader topic, exploring the practical application of "ran carthon" within specific contexts.
Conclusion
The exploration of "ran carthon" reveals a complex process deeply intertwined with various operational facets. Key aspects include detailed procedural steps, effective material handling protocols, stringent quality control measures, efficient resource utilization, meticulous safety protocols, environmental considerations, and astute cost analysis. A comprehensive understanding of these elements is essential for optimized performance. The process's efficacy depends crucially on clear communication, consistent implementation, and continuous evaluation for improvement.
Ultimately, "ran carthon," when meticulously executed, can contribute significantly to improved productivity, reduced costs, enhanced safety, and minimized environmental impact. Further research and practical application in relevant contexts are crucial to fully realizing its potential. Careful documentation, meticulous tracking, and a commitment to process improvement are essential to achieving desired outcomes. Failure to account for these factors can lead to operational inefficiencies, safety hazards, and potential environmental damage. A commitment to rigorous evaluation and adaptation is paramount for optimal long-term performance.
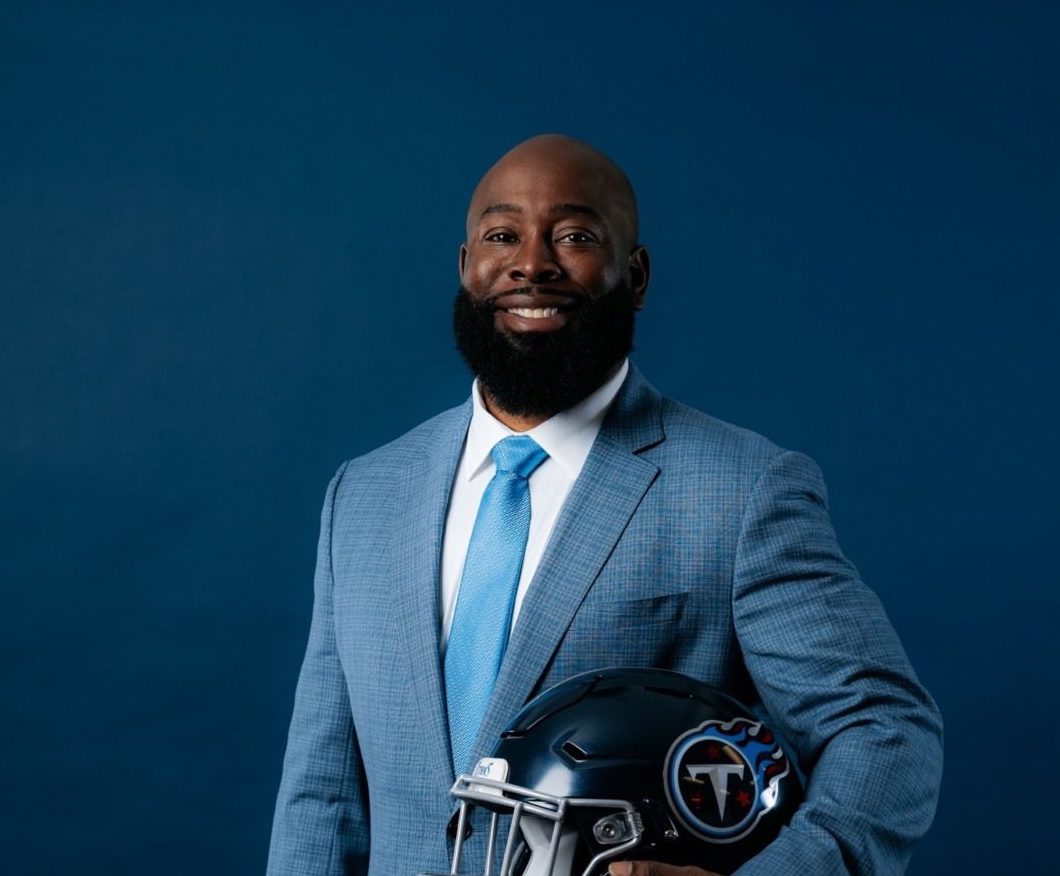
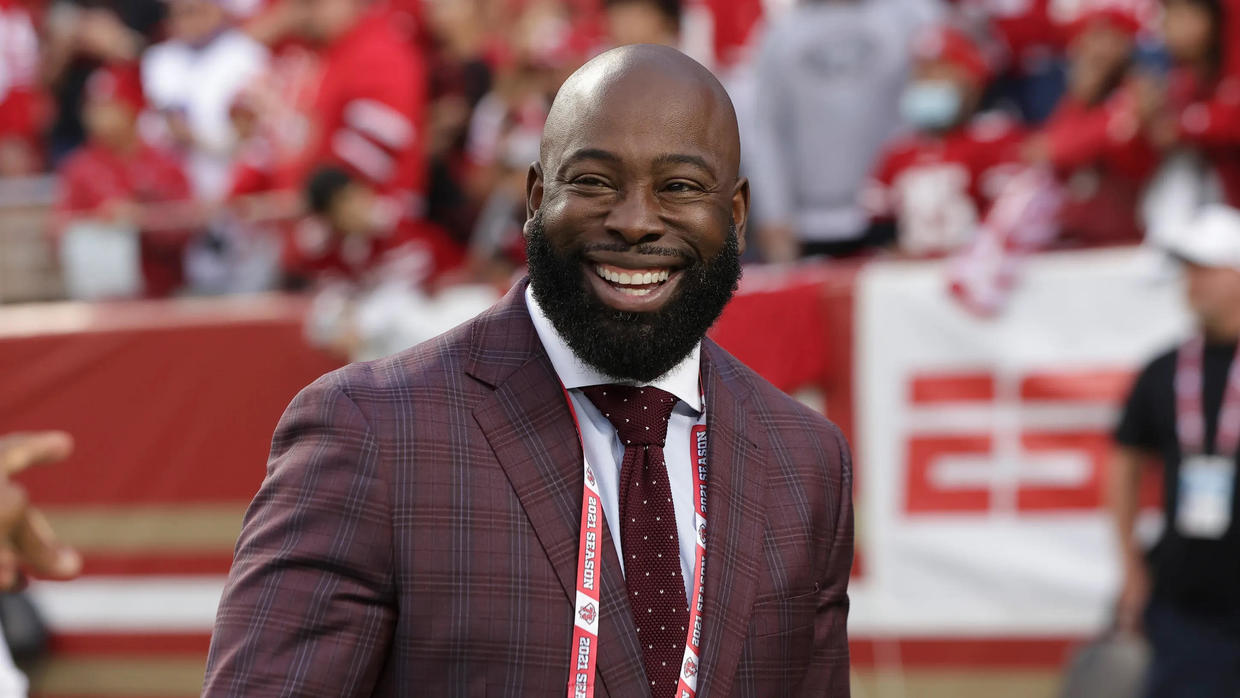
