What role does a storage facility play in a modern economy? A warehouse's efficiency is paramount in today's supply chain.
The Italian word "magazzino" translates to "warehouse" or "storage facility" in English. It signifies a structured building or area designed for the storage of goods, materials, or merchandise. Warehouses are essential components of the logistics sector, facilitating the movement and preservation of products from production to consumption. Examples include facilities for storing clothing, food products, electronics, and raw materials. The effectiveness and efficiency of these spaces directly impact the smooth functioning of the supply chain.
Warehouses are crucial to modern economies, supporting diverse sectors, and influencing economies in multiple ways. These facilities act as central hubs in the distribution network. Improved storage capacity and optimized processes translate to reduced logistical costs and minimized disruptions, ultimately benefiting businesses and consumers. Proper inventory management and security measures are integral aspects of warehouse operations, affecting product quality and safety. The historical context of warehousing is also significant, evolving from rudimentary storage systems to highly sophisticated and technologically advanced facilities. Modern technologies, such as automation and tracking systems, are crucial for efficiency in this modern era.
This exploration of warehousing lays the groundwork for a deeper examination of inventory control, distribution networks, and the ongoing development of efficient logistical systems. The design, management, and security of such facilities are essential for maintaining a smoothly functioning global market.
il magazzino
Warehousing, as a critical component of logistics, is essential for efficient product flow. Understanding its key aspects is vital for optimizing supply chains.
- Storage Capacity
- Inventory Management
- Security Measures
- Order Fulfillment
- Transportation Hub
- Technology Integration
Storage capacity dictates the volume of goods a warehouse can handle. Effective inventory management optimizes stock levels, preventing shortages or surpluses. Robust security measures protect stored goods from loss or damage. Order fulfillment efficiency directly impacts customer satisfaction. Warehouses serve as crucial transportation hubs, facilitating movement to and from various destinations. Finally, technology integration automates processes and improves data visibility, maximizing warehouse efficiency. For instance, a warehouse with insufficient capacity may lead to production delays and increased shipping costs. Improved inventory management, using software, can reduce storage costs and boost profitability. Effective security, such as surveillance and access controls, is paramount for protecting valuable goods. An optimized warehouse layout and transportation links ensure swift order fulfillment. Integrating technology, from automated storage systems to real-time tracking, enhances data management and streamlines operations. These interconnected aspects highlight the multifaceted importance of the warehouse in modern supply chains.
1. Storage Capacity
Storage capacity is a fundamental aspect of a warehouse ("il magazzino"). It directly influences the warehouse's operational efficiency and its ability to meet demand. Adequate storage space is crucial for maintaining inventory levels, handling fluctuations in orders, and ensuring timely delivery. Insufficient storage capacity can lead to significant disruptions in the supply chain, impacting profitability and customer satisfaction.
- Impact on Inventory Management
Optimal storage capacity enables effective inventory management. Sufficient space allows for organized storage, preventing overcrowding and damage to goods. This, in turn, facilitates accurate inventory tracking, reducing the risk of stockouts or overstocking. A warehouse with constrained space may necessitate less-than-optimal storage methods, hindering accurate inventory counts and potentially leading to errors. Furthermore, limited capacity can force companies to make difficult choices regarding the prioritization of products.
- Influence on Order Fulfillment
Adequate storage capacity is critical for quick and efficient order fulfillment. Sufficient space allows for the organization of goods in a manner that optimizes retrieval time. This, in turn, enhances order processing speed and reduces delays. A warehouse with limited storage capacity might struggle to accommodate large orders or fulfill demand quickly, leading to customer dissatisfaction and lost business opportunities.
- Relationship with Operational Costs
Storage capacity significantly impacts operational costs. Larger storage facilities, while initially requiring a higher capital investment, can lead to lower long-term costs through increased efficiency. Efficient utilization of space minimizes labor costs associated with handling and retrieving goods. Conversely, a warehouse with limited capacity may necessitate more frequent deliveries or the use of temporary storage solutions, thereby increasing costs and slowing down the process.
- Effect on Business Growth and Scalability
The ability to scale storage capacity is crucial for business growth and adaptability. A warehouse with limited expansion options may find itself unable to accommodate increasing demand. This can hinder business growth and limit the company's ability to capture market opportunities. Conversely, a warehouse with flexible storage space can easily adapt to changing business requirements, allowing for greater agility and responsiveness to fluctuations in demand.
In summary, storage capacity is a defining characteristic of a successful warehouse. Optimizing this aspect is essential for efficiency, profitability, and the long-term sustainability of operations. By carefully considering storage needs and planning for future expansion, businesses can ensure their warehouses remain vital components of the broader supply chain. This, in turn, optimizes overall business success.
2. Inventory Management
Effective inventory management is intrinsically linked to the success of a warehouse ("il magazzino"). Inventory management systems are not merely administrative tools; they are critical to the operational efficiency and profitability of the storage facility. Proper inventory control minimizes waste, reduces costs, and ensures smooth order fulfillment. A poorly managed inventory can lead to stockouts, overstocking, obsolescence, and increased storage costs. Consequently, accurate inventory tracking and forecasting become essential components in optimizing a warehouse's operation.
Inventory management within a warehouse hinges on several key factors. Accurate record-keeping is paramount. This involves precise tracking of goods entering and leaving the facility, ensuring that inventory levels align with real-time data. Regular stock counts, ideally supported by automated systems, help maintain accuracy and reduce the potential for discrepancies. Forecasting demand is another crucial element. Analysis of sales data, market trends, and seasonal variations allows warehouses to anticipate future needs, optimizing storage allocation and minimizing the risk of shortages or excess stock. Strategic decisions regarding storage space allocation and product placement further enhance efficiency. This involves using the warehouse layout to maximize space utilization and improve the speed of retrieval for various items. Implementing suitable storage methods, from racking systems to appropriate shelving, is crucial for maintaining order and preventing damage to goods. Advanced inventory management software can provide real-time visibility, allowing for better decision-making and more agile responses to changing market conditions. A company managing a retail supply chain, for example, must effectively track inventory levels across different warehouses and distribution centers to ensure timely order fulfillment and avoid stockouts. Companies in the manufacturing sector rely on precise inventory records of raw materials and finished goods to maintain production schedules and avoid costly delays.
In conclusion, robust inventory management is fundamental to the operational success of a warehouse. By accurately tracking inventory, forecasting demand, and optimizing storage strategies, businesses can minimize costs, enhance efficiency, and ensure smooth order fulfillment. A warehouse without effective inventory management will struggle to adapt to market fluctuations, respond to customer demands, and maintain its competitive edge. Understanding and meticulously applying inventory management principles are thus vital to a warehouse's continued success. The successful integration of these principles with warehouse operations ultimately contributes to the streamlined functioning of supply chains as a whole.
3. Security Measures
Security measures are paramount for any warehouse ("il magazzino"). Protecting stored goods from theft, damage, and unauthorized access is not merely a desirable practice; it's a fundamental aspect of operational efficiency and financial well-being. The security of a warehouse directly impacts the reliability and integrity of the broader supply chain. Consequently, robust security protocols are essential to mitigate risks and maintain the value and continuity of operations.
- Physical Security Measures
Physical security encompasses the tangible barriers and deterrents employed to safeguard a warehouse. These measures include robust exterior fencing, controlled access points with security personnel or automated systems, surveillance cameras, and alarm systems. Real-world examples include security patrols, locked gates, and monitored entry points. Effective physical security acts as a first line of defense against theft and vandalism. Compromised physical security leads to substantial losses and operational disruptions. Implementing stringent security measures, such as advanced access control systems, effectively minimizes vulnerabilities.
- Inventory Control and Tracking
Rigorous inventory control systems are inextricably linked to security. Regular stock checks, precise record-keeping, and the utilization of advanced tracking technologies (like RFID tags) provide a clear picture of the inventory present within the warehouse. This aids in quickly detecting discrepancies and theft. Real-world examples include using barcode scanners to track items, software programs designed to monitor stock levels, and implementing inventory management systems that alert authorities about discrepancies. Implementing robust inventory control systems strengthens overall security by minimizing opportunities for theft or misappropriation. An accurate record of inventory makes it easier to identify missing items. Automated tracking systems can provide continuous monitoring of inventory, streamlining security processes and preventing unauthorized movements of stock.
- Personnel Security and Access Control
Securing access to personnel within a warehouse is crucial. Implementing strict employee identification procedures, background checks for personnel, and regular security training for staff are essential. Real-world examples include using identification badges, monitoring access logs, and implementing strict policies regarding unauthorized personnel in the facility. A strong access control system is vital to prevent unauthorized access and internal theft or sabotage. Regular audits of personnel records are essential to ensure compliance with security protocols and protect the integrity of the warehouse.
- Environmental Security Measures
Environmental factors can also pose security risks, such as fire hazards. Proactive measures to prevent fire hazards, such as regular fire safety inspections, proper fire suppression systems, and emergency evacuation procedures, directly impact the protection of the warehouse and its contents. Real-world examples include sprinkler systems, smoke detectors, and controlled storage of flammable materials. Effective fire safety protocols are crucial to prevent significant damage and disruptions to operations.
In summary, a secure warehouse ("il magazzino") requires a multifaceted approach to security. Combining robust physical measures, sophisticated inventory controls, secure personnel access, and proactive environmental safeguards creates a layered defense against various threats. Prioritizing security at every stage ensures a reliable and safe operational environment for the warehouse. Investing in robust security protocols protects not only the goods within the warehouse but also the reputation and financial stability of the organization.
4. Order Fulfillment
Order fulfillment is inextricably linked to the effectiveness of a warehouse ("il magazzino"). The speed, accuracy, and efficiency of order fulfillment directly impact customer satisfaction and a business's profitability. A well-optimized warehouse facilitates swift order processing, minimizing delays and maximizing customer satisfaction. Efficient order fulfillment is a critical aspect of the warehouse's operational success.
- Picking and Packing Processes
Efficient picking and packing procedures are fundamental to order fulfillment within a warehouse. These processes, from locating items to packaging them securely for shipment, directly impact order turnaround times. Well-designed layouts, efficient material handling equipment, and clear procedures contribute to minimizing handling time. For instance, a warehouse employing automated guided vehicles (AGVs) for picking can significantly reduce the time required to fulfill orders compared to a warehouse reliant on manual picking methods. Optimal picking and packing procedures contribute to a high degree of accuracy and minimize the risk of errors in order fulfillment.
- Inventory Management Integration
Effective inventory management directly influences order fulfillment. Real-time visibility into stock levels ensures that orders can be processed without delays due to stockouts. Precise inventory tracking systems allow for accurate order fulfillment, preventing fulfillment issues due to inaccurate inventory records. In addition, precise inventory records make it easier for a warehouse to determine which orders can be fulfilled immediately and which require additional processing or sourcing.
- Transportation and Shipping Integration
Order fulfillment encompasses the entire process from picking and packing to shipping the finished goods. Streamlined communication and coordination between the warehouse and transportation companies are crucial for timely delivery. This includes efficient loading and unloading procedures, proper documentation, and adherence to shipping regulations. For example, a warehouse optimizing its shipping processes by using a courier service with real-time tracking capabilities can provide better delivery estimates to clients and minimize delays due to unforeseen circumstances. Thorough communication and coordination reduce logistical challenges and ensure timely shipment of orders.
- Customer Service and Feedback Loop
Order fulfillment extends beyond the warehouse itself to include customer service. Efficient tracking mechanisms allow customers to monitor their order's status, providing a transparent and positive experience. Effective communication and response mechanisms for resolving any order-related issues contribute to customer satisfaction. Feedback mechanisms allow the warehouse to identify areas for improvement in order fulfillment processes and enhance customer service. In the context of e-commerce businesses, efficient order fulfillment is vital for building and maintaining customer loyalty.
In conclusion, the efficiency of a warehouse ("il magazzino") is closely tied to its ability to fulfill orders effectively. Optimized picking and packing, seamless inventory management, efficient shipping processes, and a strong customer service link are all essential components in the order fulfillment process. By optimizing all these aspects, a warehouse significantly enhances its value to the organization and to its clients.
5. Transportation Hub
A warehouse ("il magazzino") functions as a critical component of a comprehensive logistics network, often acting as a crucial transportation hub. The efficiency and effectiveness of this transportation aspect significantly impact the warehouse's overall performance. A warehouse's ability to facilitate the smooth movement of goods, from receipt to dispatch, directly correlates to its operational efficiency and profitability. This necessitates strategic location choices, access to diverse transportation modes, and optimized internal infrastructure.
The warehouse's role as a transportation hub is multifaceted. It's a pivotal point where goods are received from various originssuppliers, manufacturersand subsequently prepared for onward transport to distribution centers or directly to customers. Optimized loading and unloading procedures, appropriate storage and handling methods, and efficient transport options (roads, rail, air, sea) are crucial for minimizing transit times and reducing logistical costs. Consider a large-scale retailer. The effectiveness of its warehouse network in coordinating shipments from diverse production sites to various regional distribution centers is essential to maintaining stock levels and fulfilling orders timely. Similarly, a manufacturer using a warehouse as an intermediary between its production facility and client distribution centers relies on efficient transport links to ensure uninterrupted production and delivery schedules.
Understanding the importance of a warehouse as a transportation hub is vital for strategic decision-making. The selection of a suitable location, ideally near major transportation routes or hubs, is crucial for reducing transportation costs and delivery times. The availability of diverse transportation options, such as rail or trucking networks, provides flexibility in responding to fluctuating demand and supply chain disruptions. The ability to streamline internal processes, such as optimized loading docks and efficient handling equipment, further enhances the warehouse's capacity as a seamless transportation nexus. A well-managed transportation hub function within a warehouse is a cornerstone of an efficient supply chain, allowing goods to flow smoothly, reducing delivery times, and minimizing costs, ultimately enhancing the overall profitability of the business.
6. Technology Integration
Technology integration within warehouses ("il magazzino") is no longer a supplementary feature, but a foundational requirement for operational excellence. Technological advancements are reshaping the modern warehouse, transforming its capabilities and efficiency. Implementing appropriate technologies streamlines processes, enhances data management, and optimizes resource allocation. Automated systems, data analytics, and real-time tracking are crucial in navigating complexities in modern supply chains. A warehouse utilizing technology effectively is poised to respond dynamically to fluctuating market demands, reducing operational costs and boosting overall productivity.
Modern warehousing leverages a wide array of technologies to achieve efficiency and accuracy. Automated guided vehicles (AGVs) and robotic systems automate material handling, significantly reducing human error and increasing throughput. Real-time inventory tracking systems, often utilizing Radio Frequency Identification (RFID) tags, provide instantaneous visibility into stock levels, enabling proactive management and minimizing stockouts or overstocking. Data analytics tools provide insights into trends and patterns in order fulfillment, demand forecasting, and supply chain performance, facilitating informed decision-making and strategic planning. Warehouse management systems (WMS) integrate various aspects of warehouse operations, from receiving and storage to picking, packing, and shipping, streamlining workflows and optimizing space utilization. These technologies are not isolated applications; they are deeply intertwined and crucial to achieving a well-functioning and efficient warehouse system. For instance, an automated storage and retrieval system (AS/RS) integrated with a WMS allows for highly efficient and accurate inventory management, minimizing handling errors and improving turnaround times. Similarly, incorporating advanced sensor technologies enables real-time monitoring of environmental conditions, preventing damage to stored goods and optimizing energy consumption.
The strategic integration of technology in warehouses is not merely about automating tasks; it's about fundamentally transforming the nature of warehouse operations. By leveraging technology effectively, warehouses can significantly reduce operational costs, enhance safety, improve accuracy, and adapt to evolving business needs. These advancements equip warehouses to meet the growing demands of modern e-commerce and global supply chains. This transformation, however, comes with challenges. Implementing new technologies often requires significant capital investment and specialized training for personnel. Ensuring compatibility among diverse technologies within the existing infrastructure also presents a practical consideration. Properly understanding the relationship between technology and warehouse operations, and proactively addressing these challenges, is essential for maximizing the benefits of technology integration. The future of warehousing lies in a strong understanding of and commitment to leveraging technology, not merely as a tool but as a driving force for operational excellence.
Frequently Asked Questions about Warehousing (il magazzino)
This section addresses common inquiries regarding warehousing, providing clear and concise answers to help understand the critical role of storage facilities in modern logistics.
Question 1: What are the key functions of a warehouse?
Warehouses are central to the logistics process, encompassing receiving, storing, and shipping goods. Key functions include receiving and inspecting incoming shipments, storing goods safely and efficiently, organizing inventory, picking and packing orders for dispatch, and preparing goods for transportation. A warehouse also plays a role in managing inventory levels, fulfilling customer orders, and ensuring timely delivery.
Question 2: How does technology impact warehouse operations?
Technology significantly influences warehouse performance. Automated systems like AGVs and AS/RS improve efficiency by automating material handling and storage. Real-time inventory tracking, utilizing RFID and barcodes, enhances accuracy and allows for proactive management. Warehouse management systems (WMS) integrate various processes, streamlining workflows and optimizing space utilization. Data analytics tools further refine operations by identifying trends and patterns.
Question 3: What are the essential security considerations in a warehouse?
Warehouse security is crucial for protecting stored goods. Robust security measures include controlled access points, surveillance systems, and alarm systems. Proper inventory management systems, including regular stock counts, are vital for detecting and preventing theft. Secure storage areas, adequate lighting, and adherence to safety regulations contribute to a secure operational environment.
Question 4: What are the different types of warehouses?
Warehouses can be categorized by function, size, and location. Examples include distribution centers focused on rapid order fulfillment, cold storage facilities for temperature-sensitive goods, and specialized warehouses catering to particular industries. Determining the appropriate type of warehouse depends on the specific storage needs and logistical requirements of the business.
Question 5: How is a warehouse's location chosen?
Warehouse location decisions are critical. Considerations include proximity to transportation networks (roads, rail, ports), access to labor, proximity to customers, and local regulations. Ideally, a strategic location minimizes transportation costs and ensures efficient order fulfillment. Cost-benefit analyses and assessments of infrastructure availability are often used to determine the best location.
Understanding the different functions, technological advancements, security measures, types, and location selection strategies associated with warehousing provides a comprehensive overview of these vital logistics facilities. Effective warehouse operations are integral to the smooth functioning of modern supply chains, enabling businesses to efficiently and reliably fulfill customer demands.
The subsequent section will delve deeper into the specifics of warehouse design and management, exploring advanced concepts and best practices.
Conclusion
This exploration of "il magazzino," or warehousing, has illuminated the multifaceted importance of these facilities within modern supply chains. Key aspects examined include storage capacity, inventory management, security protocols, order fulfillment processes, transportation integration, and the crucial role of technological advancements. The analysis underscored the significant impact of each element on overall efficiency, cost-effectiveness, and the ability to meet evolving customer demands. Warehousing is not simply a storage space; it's a dynamic hub that directly affects the smooth flow of goods from origin to consumer.
The future of warehousing hinges on the continued evolution and implementation of sophisticated technologies. The integration of automation, data analytics, and real-time tracking systems will be essential for optimization and adaptability in increasingly complex logistical landscapes. Moreover, the proactive management of security, both physical and informational, will be paramount to safeguarding assets and maintaining trust in the supply chain. The careful consideration of these factors will be essential for ensuring the continued smooth operation and profitability of warehousing in the years ahead, ultimately benefiting both businesses and consumers.
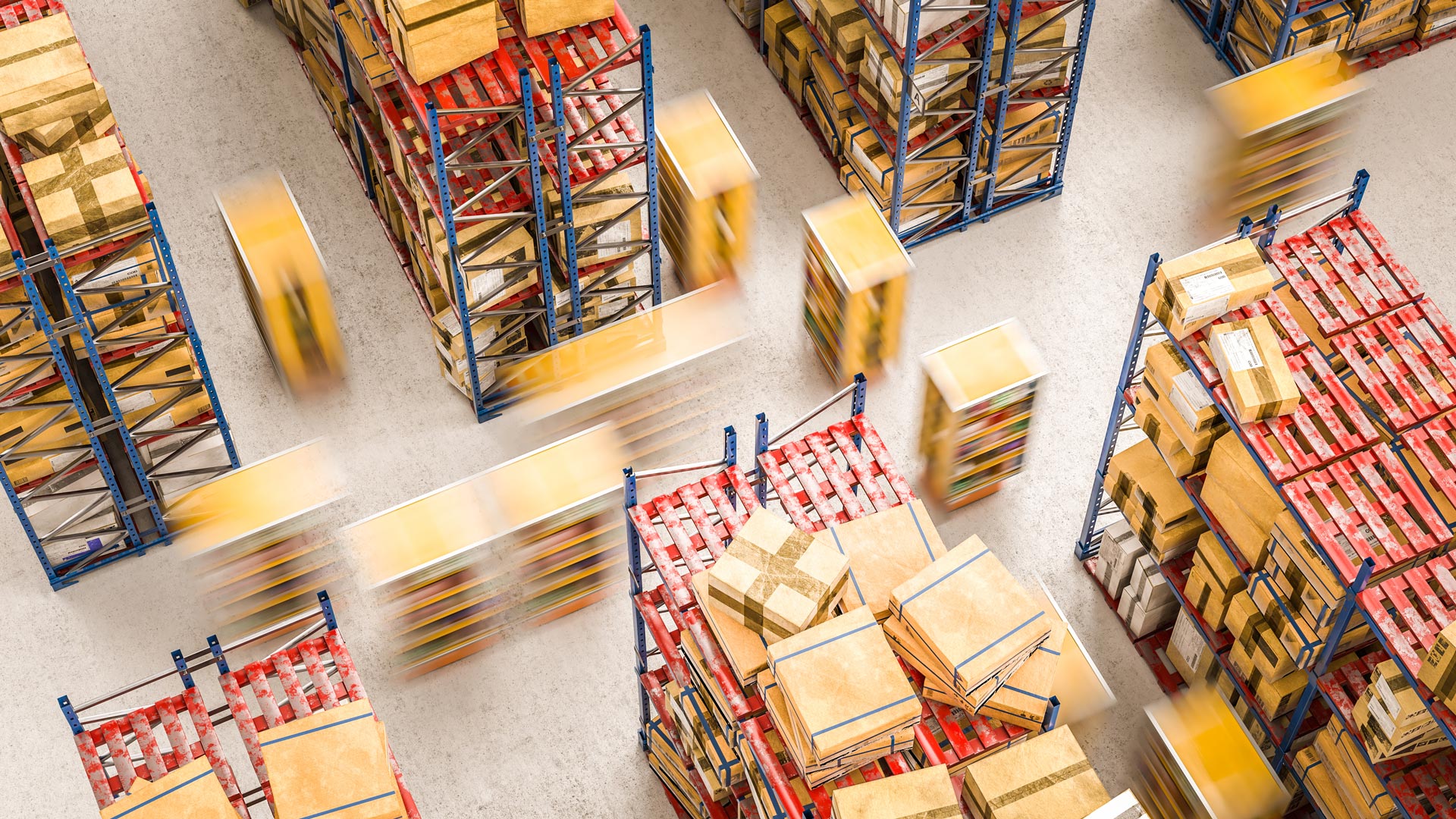
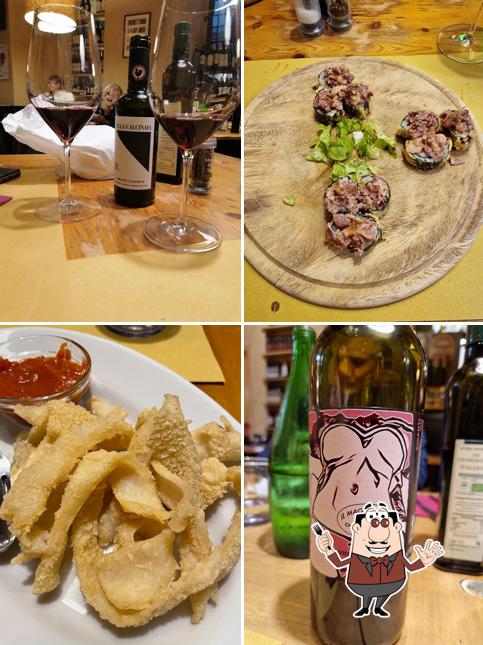
