How does the manipulation of vapor contribute to various fields? A crucial process in diverse industries.
The controlled creation and manipulation of vapora gaseous state of matteris fundamental to numerous processes across diverse sectors. This encompasses the use of heat to convert liquids into vapor, as well as the application of pressure and temperature to alter the properties of the vapor itself. Examples range from the efficient production of steam power to the intricate processes within semiconductor manufacturing. The precision and control over vapor characteristics are key to desirable outcomes in these applications.
The importance of vapor manipulation stems from its role in energy generation, material processing, and technological advancement. Efficient steam engines rely on the expansion of vapor. In modern industries, vapor deposition techniques form the basis for creating intricate microchips and coatings. The precise control afforded by manipulating vapor allows for the production of materials with tailored properties, greatly expanding the possibilities in manufacturing. Moreover, understanding and harnessing vapor's unique properties provide opportunities for sustainable practices and innovative solutions to address contemporary challenges.
Moving forward, we will explore specific applications of vapor manipulation in detail, highlighting the scientific principles underlying these crucial technologies.
Vapor Works
Vapor manipulation underpins diverse processes, from energy production to material science. Understanding its key aspects is crucial for comprehending these applications.
- Energy conversion
- Material deposition
- Precision control
- Chemical reactions
- Thermal management
- Process optimization
- Product enhancement
- Sustainability
These aspects encompass the fundamental mechanisms behind vapor's role in various fields. Energy conversion, for instance, relies on the controlled expansion of heated vapor to drive turbines. Material deposition leverages vapor to create thin films with specific properties. Precision control, achievable through manipulating temperature and pressure, enables the production of complex materials like semiconductors. Further, vapor's role extends to optimizing processes, enhancing product quality, and addressing sustainability concerns within industry by utilizing energy more efficiently. These interlinked elements highlight the pervasiveness and importance of vapor manipulation in contemporary technological advancements.
1. Energy Conversion
Energy conversion relies fundamentally on the controlled transformation of energy from one form to another. A crucial component of this transformation involves the utilization of vapor. Vapor, in its various forms, facilitates energy transfer through processes such as phase changes. The expansion of heated vapor, for instance, powers turbines in various energy generation systems. This principle underlies the operation of steam engines and modern thermal power plants, highlighting the direct connection between vapor and energy conversion.
Consider steam power. The heat from combustion boils water, converting it to steam. This high-pressure steam then drives turbines, which in turn generate mechanical energy, ultimately producing electricity. Similarly, in jet engines, the controlled combustion of fuel creates high-temperature gases, which, as vapor, propel the aircraft. The efficient conversion of thermal energy into mechanical energy, via vapor, directly impacts efficiency and performance in such systems. Furthermore, advanced technologies like vapor-based refrigeration cycles demonstrate how controlled vapor processes can be crucial for manipulating heat in energy systems.
The understanding of vapor's role in energy conversion is paramount for optimizing energy efficiency. Improvements in vapor-based processes directly translate to reduced energy consumption and decreased emissions in various applications. Further research into advanced vapor-based technologies promises innovations in energy conversion techniques, paving the way for more sustainable and efficient energy generation and utilization.
2. Material Deposition
Material deposition, a critical process in numerous industrial sectors, is intrinsically linked to vapor manipulation. This connection arises from the fundamental role vapor plays in transporting and depositing atoms and molecules onto surfaces. Various methods for material deposition, such as chemical vapor deposition (CVD) and physical vapor deposition (PVD), rely on vaporizing materials to create a vapor phase. This vapor phase then facilitates the controlled transfer of material to a substrate, leading to the formation of thin films with tailored properties. The precise control over vapor parameters, including temperature and pressure, is paramount in achieving the desired film characteristics. Crucially, the vapor phase acts as a medium to overcome the inherent limitations of direct material transfer techniques.
Numerous real-world applications exemplify this critical relationship. The semiconductor industry, for instance, heavily utilizes CVD and PVD to create complex integrated circuits. These techniques allow for the precise deposition of layers of silicon, silicon dioxide, and other materials onto silicon wafers. Similarly, the production of optical coatings for lenses and mirrors relies on vapor deposition methods. These coatings, deposited via vapor, enhance light transmission and reduce reflection, vital in optical instruments and displays. Furthermore, vapor deposition enables the creation of protective coatings on various metal components, enhancing corrosion resistance and longevity. The resulting materials exhibit superior performance in diverse applications, highlighting the crucial role of vapor-based deposition methods.
In summary, material deposition, achieved through vapor manipulation, represents a critical enabling technology in numerous industries. The precise control over vapor parameters allows for the creation of materials with tailored properties, directly impacting performance and application suitability. Understanding the underlying principles of vapor-based deposition is essential for continued innovation and advancement in fields such as electronics, optics, and materials science. However, challenges such as maintaining consistent deposition rates and controlling film uniformity remain areas for ongoing research and development efforts.
3. Precision Control
Precise control over vapor parameters is fundamental to "vapor works." The ability to manipulate temperature, pressure, and other variables during vaporization and deposition processes is essential for achieving desired outcomes. This meticulous control impacts material properties, performance, and the efficacy of various applications, from energy conversion to advanced manufacturing.
- Temperature Regulation
Precise temperature control during vaporization directly influences the quality and characteristics of the resultant vapor. Maintaining specific temperatures is critical for achieving the correct molecular state and avoiding unwanted byproducts. For instance, in semiconductor manufacturing, precise temperature control during CVD ensures that the correct types and thicknesses of layers are deposited onto wafers, impacting the functionality of the final chip. Similarly, in materials science, controlling temperature during vapor deposition is crucial for optimizing the structural organization and properties of the created materials, potentially leading to enhanced performance in various applications.
- Pressure Management
Controlling pressure during vaporization and deposition processes is equally vital. Varying pressure can significantly influence the nucleation and growth rates of deposited materials. Adjusting pressure allows for tailoring film thickness and uniformity, crucial for applications in optics and electronics. In thermal spray processes, precise pressure control dictates the rate and uniformity of the sprayed material, affecting its adherence and final properties, thus affecting the quality of parts manufactured.
- Composition Control
Precise control over the chemical composition of vapor is crucial for tailoring the properties of the resultant material. In many vapor-based processes, precise control is achieved by carefully adjusting the ratios of different reactants to produce the desired chemical composition. For instance, in chemical vapor deposition (CVD), the chemical composition of the gas phase directly impacts the crystal structure, morphology, and other properties of the film deposited. The ability to precisely control vapor composition in advanced manufacturing is critical for producing films with specific functionalities, including high temperature resistance and optical properties.
- Growth Rate Control
Precise control over the rate of vapor deposition is vital for creating consistent and uniform material layers. Varying growth rates can significantly impact the quality of the final product. In applications requiring specific thicknesses and uniform properties, meticulous control over the growth rate is essential for reproducibility and reliability. Adjusting growth parameters like temperature and pressure can also control the rate of vapor deposition, further enhancing uniformity and final properties. This control is particularly crucial in microelectronics fabrication, where precise layer-by-layer growth is essential for integrated circuits.
In conclusion, precision control in "vapor works" is more than just a technical detail; it's a cornerstone for success. Mastering temperature, pressure, composition, and growth rates allows for the tailoring of materials with highly specific properties, ultimately enabling advanced manufacturing and innovative technologies across diverse sectors. This control is paramount in ensuring reproducibility, reliability, and the optimization of vapor-based processes.
4. Chemical Reactions
Chemical reactions are integral to many vapor-based processes. The manipulation of vapor often involves transformations at a molecular level, where chemical reactions dictate the composition and properties of the resulting vapor and subsequently deposited materials. Understanding these reactions is crucial for optimizing and controlling various facets of vapor manipulation.
- Reactant Interactions
Chemical reactions in vapor systems typically involve interactions between different reactants in the gaseous phase. The specific nature of these interactions, including their kinetics and thermodynamics, significantly influence the final product characteristics. Examples include the reactions occurring during chemical vapor deposition (CVD), where gaseous precursors react to form solid films. The reaction kinetics in CVD processes directly affect the growth rate and uniformity of the deposited layers.
- Vapor-Phase Transformations
Chemical reactions often lead to vapor-phase transformations. Reactants can combine or decompose, resulting in the formation of new chemical species in the vapor phase. These transformations play a pivotal role in determining the composition and properties of the resulting materials. For instance, in some vapor-based processes, a mixture of precursor gases undergoes chemical reactions, leading to the formation of a specific vapor composition, which then condenses into a desired material. These controlled reactions are essential in tailoring the properties of the final product.
- Catalysis and Kinetics
Catalysts frequently play a crucial role in vapor-based reactions, influencing reaction rates and selectivity. Optimizing reaction kinetics is vital for controlling vapor characteristics. In industrial systems, careful selection and design of catalysts are critical for efficient vapor production and desired product outcomes. The understanding of reaction kinetics in vapor processes allows for predictive modeling and process optimization.
- Control over Product Composition
Controlling the composition of vapor through targeted chemical reactions allows for the precise tailoring of materials produced. Understanding reaction mechanisms enables scientists and engineers to manipulate factors like temperature and pressure to influence the product's composition. For instance, varying the reactants or reaction conditions can lead to the formation of materials with specific compositions, impacting properties such as conductivity or hardness. This controlled manipulation directly facilitates the creation of tailored materials for diverse applications.
In summary, chemical reactions within vapor-based systems are not merely secondary considerations; they are fundamental to controlling and optimizing these processes. The precise manipulation of chemical reactions within vapor systems enables the creation of materials with specific properties for various applications. Further research in this area will lead to more sophisticated and efficient vapor manipulation techniques, ultimately impacting numerous industrial sectors.
5. Thermal Management
Thermal management is inextricably linked to "vapor works," as controlling temperature is paramount in virtually all vapor-based processes. Precise temperature regulation dictates the behavior of vapor, influencing its properties, enabling efficient conversion of energy, and ensuring the successful production of desired materials. Maintaining optimal thermal conditions across these processes is crucial for safety, performance, and cost-effectiveness.
- Heat Transfer in Vapor Systems
Vapor systems inherently involve heat transfer. The conversion of liquid to vapor, for example, necessitates significant heat input. Conversely, condensation, a critical part of many vapor-based cycles, involves releasing heat. Understanding and optimizing heat transfer within these systems are essential for maximizing efficiency and minimizing energy losses. Effective thermal management strategies must account for conduction, convection, and radiation processes occurring within the vapor and surrounding components.
- Temperature Control for Vapor Properties
Temperature directly affects vapor pressure, density, and thermal conductivity. These properties, in turn, influence the efficacy of various vapor-based applications. For instance, in power generation, elevated temperatures increase steam pressure, improving turbine performance. Conversely, precise temperature control during thin-film deposition (e.g., CVD) ensures the creation of films with desired properties by controlling the kinetics of condensation. Deviations from optimal temperatures can result in undesirable consequences, such as material defects or system failure.
- Maintaining System Integrity and Safety
Extreme temperatures associated with some vapor processes can cause significant material stresses, leading to component failure or even safety hazards. Proper thermal management systems, involving insulation, cooling mechanisms, and temperature sensors, mitigate these risks. Controlling temperature limits the potential for thermal shock and degradation of equipment, ensuring safe and reliable operation. Safety considerations are paramount in high-temperature or high-pressure vapor systems.
- Efficiency Optimization through Thermal Management
Thermal management strategies directly impact the overall efficiency of vapor-based processes. Minimizing energy loss due to excessive heat dissipation and ensuring consistent thermal conditions result in enhanced performance. For instance, efficient insulation reduces heat loss, reducing energy consumption and operating costs. Optimization techniques for thermal management are crucial for maximizing energy yield in power generation and reducing operational costs in diverse industrial processes.
In conclusion, thermal management is not a peripheral consideration but a fundamental aspect of "vapor works." Effective temperature control and heat management are crucial for optimizing efficiency, ensuring safety, maintaining system integrity, and producing the desired properties in vapor-based processes. Advancements in thermal management directly translate to advancements in vapor-based technologies, potentially driving innovation across a wide range of industries.
6. Process Optimization
Process optimization is an integral component of "vapor works," encompassing a systematic approach to improving efficiency and yield in vapor-based processes. Optimization strategies address various factors, from energy consumption to material utilization. Effective optimization hinges on a deep understanding of the thermodynamic principles governing vapor-phase transformations and the subsequent material properties. Optimizing these processes is crucial for enhancing performance, reducing costs, and minimizing environmental impact.
Real-world examples illustrate the practical significance of optimization. In semiconductor manufacturing, optimizing chemical vapor deposition (CVD) processes ensures consistent film thickness and quality, reducing defects and maximizing yield. Similarly, in energy production, optimizing steam turbine cycles minimizes energy losses, enhancing overall efficiency. These examples demonstrate how process optimization in "vapor works" translates to tangible improvements in product quality, cost reduction, and resource utilization. The development of process models and simulations plays a critical role in this optimization, enabling predictive analysis and iterative adjustments to optimize parameters like temperature, pressure, and reactant flow rates. Sophisticated control systems and data analytics are vital in implementing these optimized procedures.
Optimizing "vapor works" processes necessitates a multifaceted approach, considering factors ranging from raw material selection and process parameters to waste management strategies. Identifying bottlenecks, pinpointing areas for improvement, and implementing solutions requires a detailed understanding of the system's behavior and interactions. This understanding, combined with advanced modeling and simulation techniques, leads to more efficient and sustainable vapor-based processes. Furthermore, improved process optimization reduces operational costs, minimizing waste, and enhances the overall sustainability of industrial systems.
7. Product Enhancement
Product enhancement, a key driver of innovation, is deeply intertwined with "vapor works." The controlled manipulation of vapor allows for the creation of materials with specific properties that, in turn, enhance the functionality and performance of diverse products. The application of vapor deposition techniques, for example, leads to the creation of advanced materials exhibiting superior characteristics, thereby enhancing product attributes like durability, conductivity, or optical clarity. This enhancement is not merely cosmetic; it significantly affects product efficacy and end-user experience.
Consider the semiconductor industry. Vapor deposition techniques, such as chemical vapor deposition (CVD), are essential for creating integrated circuits. The precise control over vapor parameters enables the precise layering of materials, leading to enhanced conductivity and minimized defects in the final product. This, in turn, results in faster processors and more energy-efficient devices. Similarly, in the production of optical lenses, vapor deposition methods create coatings that enhance light transmission and minimize reflections, significantly improving image quality and resolution in various applications, from cameras to telescopes. In these instances, "vapor works" directly contributes to the enhancement of product performance.
Understanding the intricate connection between "vapor works" and product enhancement is critical for innovation and advancement in numerous sectors. It underscores the importance of refined control over vapor characteristics in achieving superior material properties and thus, enhancing product performance. The sophisticated interplay between vapor manipulation and product properties is crucial in developing high-performance components for aerospace, electronics, and other technological domains. Challenges in this area include ensuring consistent deposition rates and managing the complexity of chemical reactions within vapor systems. Overcoming these challenges leads to the creation of enhanced products with optimized performance. Ultimately, this deeper understanding empowers the development and production of technologically advanced products that satisfy ever-increasing market demands.
8. Sustainability
The connection between sustainability and vapor-based processes is multifaceted, encompassing resource efficiency, waste reduction, and the minimization of environmental impact. Sustainable practices are increasingly crucial within vapor works due to the inherent energy demands and potential environmental consequences of certain processes. Minimizing the use of non-renewable resources, reducing hazardous emissions, and adopting environmentally friendly materials are crucial elements in this context. For instance, optimizing chemical vapor deposition (CVD) processes can significantly decrease the consumption of high-energy resources while ensuring high-quality product output. This optimization considers the life cycle of materials, encompassing their production, usage, and eventual disposal or recycling. This is crucial for environmentally responsible manufacturing.
A key example illustrating this connection is the shift towards alternative energy sources in industrial vapor generation. Utilizing renewable energy sources, such as solar or wind power, for heating and vapor production in applications like power generation directly reduces reliance on fossil fuels. This transition mitigates carbon emissions, contributing to a lower environmental footprint. Furthermore, the use of recycled materials and waste products in vapor-based processes, like thin-film deposition, has significant implications for sustainability. This approach reduces the demand for raw materials, minimizing environmental impacts related to resource extraction. Moreover, carefully designing vapor-based processes to minimize hazardous waste products is crucial. The adoption of closed-loop systems, where byproducts are recycled or reused, demonstrates this commitment to environmental responsibility. The broader implications are far-reaching, as improvements in vapor-based processes often lead to more energy-efficient and environmentally friendly products. These products ultimately offer a more sustainable solution across various sectors.
In conclusion, sustainability is no longer a secondary consideration but a crucial component of "vapor works." By adopting principles of resource efficiency, waste reduction, and environmentally friendly materials, the sector can minimize its environmental impact and contribute to a more sustainable future. Challenges include developing more energy-efficient vaporization methods and optimizing waste-management strategies for various vapor-based manufacturing processes. Continued innovation and research in this area are essential to realize the full potential of vapor-based technologies while upholding responsible environmental practices. Ultimately, sustainable "vapor works" fosters a circular economy, where resources are utilized effectively and waste is minimized throughout the entire product life cycle.
Frequently Asked Questions
This section addresses common inquiries regarding vapor-based processes, providing concise and informative answers to promote a better understanding of these essential technologies.
Question 1: What are the key applications of vapor-based processes?
Vapor manipulation underpins a diverse array of applications, including energy generation (e.g., steam power plants), material science (e.g., thin-film deposition for semiconductors), and chemical processing. The controlled manipulation of vapor enables the precise tailoring of materials, driving advancements in diverse sectors.
Question 2: What are the fundamental principles behind vapor-based processes?
Vapor-based processes rely on the principles of thermodynamics, particularly phase transitions. Key factors include temperature control, pressure management, and understanding the chemical reactions involved. Efficient vaporization, controlled transport, and subsequent condensation or deposition are essential for desired outcomes.
Question 3: How does temperature influence vapor-based processes?
Temperature significantly affects vapor properties like pressure, density, and thermal conductivity. Precise temperature control is critical for the efficient operation of various systems. Elevated temperatures often promote vaporization, while controlled cooling facilitates condensation and deposition. Maintaining optimal temperature gradients ensures desired product characteristics and system integrity.
Question 4: What are the environmental considerations in vapor-based processes?
Environmental sustainability is increasingly important in vapor-based processes. Minimizing emissions, optimizing energy use, and adopting environmentally friendly materials and processes are key considerations. Efforts to reduce hazardous waste and utilize renewable energy sources are crucial for environmental responsibility.
Question 5: What are the potential challenges in implementing vapor-based processes?
Challenges in implementing vapor-based processes often include precise control over various parameters like temperature, pressure, and reactant flow rates. Ensuring consistent and uniform deposition or condensation, managing potential hazardous byproducts, and maintaining system integrity are also critical considerations.
In summary, vapor-based processes are essential for a wide range of applications, underpinned by fundamental thermodynamic principles. Efficient and sustainable operation requires careful consideration of temperature control, environmental impacts, and process optimization strategies. Addressing the challenges associated with these processes enables continued innovation and wider application in various sectors.
Moving forward, we will explore specific examples of vapor-based technologies and their applications in greater depth.
Conclusion
This exploration of "vapor works" has illuminated the fundamental role of vapor manipulation across diverse sectors. The controlled alteration of vapor properties, encompassing temperature, pressure, and chemical composition, facilitates critical processes from energy conversion to material deposition. Key insights highlight the intricate interplay between thermodynamic principles, chemical reactions, and thermal management in optimizing vapor-based technologies. The multifaceted nature of "vapor works" demonstrates its pervasive influence on product enhancement, process optimization, and sustainability initiatives across industries, from energy production to advanced manufacturing.
The future of "vapor works" hinges on continued innovation in process optimization and sustainable practices. Addressing challenges like ensuring consistent deposition rates, reducing environmental impact, and developing more efficient thermal management strategies are crucial. Advancements in modeling and simulation, combined with the strategic implementation of automation, will likely drive significant progress in "vapor works" across various sectors. Further research and development in this area promise to deliver increasingly sophisticated and reliable technologies, contributing to broader technological advancements and a more sustainable future.

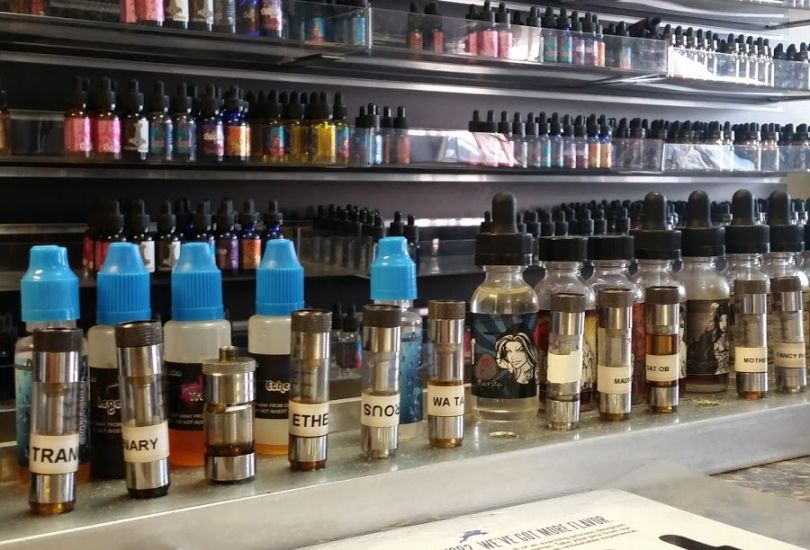
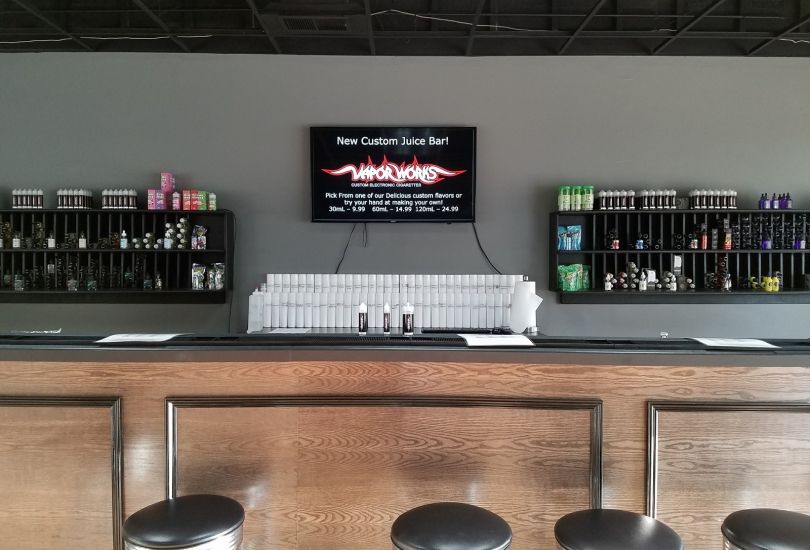