What is the function of a specific fastening device, crucial in certain mechanical applications?
This particular fastening element, often found in machinery and structures, secures components by utilizing a wedge-like shape. It acts as a mechanical key, preventing relative movement between parts. Examples include securing shafts to housings or connecting parts within a complex mechanism. The design typically involves a slotted or tapered shape that fits within a corresponding hole, thereby clamping the parts together securely.
The critical importance of this fastening method lies in its ability to provide reliable and robust mechanical joints. These designs are often selected for their resistance to stress, fatigue, and vibration. Historically, this type of joining method has been employed across a wide range of industries, playing a vital role in ensuring the integrity and functionality of intricate machinery. Such meticulous joinery is crucial for the dependability of various machines, from simple tools to complex industrial equipment.
Transitioning now to a broader exploration of mechanical fastening techniques, this device represents a specific and crucial approach. The precise way this component functions is critical to ensuring the efficacy and safety of machinery.
Cotter
Understanding the fundamental elements of a cotter joint is crucial for appreciating its role in mechanical systems. The cotter, a specific type of fastener, plays a vital part in securing components and maintaining structural integrity. Proper design and selection are essential.
- Fastening
- Securing
- Shafts
- Components
- Wedges
- Tensile strength
- Machine parts
- Load distribution
A cotter's function as a fastening mechanism relies on its wedge shape. This shape, when inserted into a slot, creates a strong, clamping force. Cotter pins secure shafts to housings or other components. The tensile strength of the cotter material is critical, as it must withstand the applied loads. Careful selection ensures the correct load distribution across the joint. By properly understanding and applying the principles of cotter design and selection, mechanical systems can achieve high levels of safety and reliability. For instance, in a crankshaft assembly, cotters hold the connecting rods to the shaft, enabling the engine to transmit power effectively.
1. Fastening
Fastening, in its broadest sense, encompasses techniques used to join or secure components. A critical aspect of fastening relates to the method employed. The cotter joint, a specific fastening method, utilizes a wedge-shaped element (the cotter) to secure components, often shafts to housings. This connection is crucial to the integrity and function of machinery. Without proper fastening, the stability and reliability of equipment are compromised. For example, in a vehicle's drivetrain, cotter pins secure parts that transmit rotational power. Failure of these fasteners can result in catastrophic failure, emphasizing the importance of appropriate fastening techniques.
The significance of proper fastening extends beyond simple mechanical assembly. Precise fastening methods are vital for transferring forces, maintaining alignment, and preventing relative motion between components. These considerations are critical in heavy machinery, aerospace engineering, and even everyday items such as furniture. Accurate fastening ensures consistent performance and longevity. This reliability is paramount in applications where safety and functionality are paramount. A weakened or improperly fastened joint could lead to equipment failure and potential injury. Consequently, understanding the specific fastening technique, including its associated elements like cotter pins, is essential for ensuring structural integrity.
In summary, fastening methods, exemplified by the cotter joint, are fundamental for the reliability and safety of mechanical systems. Careful consideration of fastening methods is crucial, and their application must adhere to the precise standards and tolerances needed for the specific task and material. This understanding extends beyond individual components to encompass the broader system's integrity, and failure to apply appropriate fastening principles can lead to costly consequences and potential risks.
2. Securing
Securing components in mechanical systems is critical for functionality and safety. The cotter joint, a specific securing method, illustrates this principle. Understanding how securing is achieved through a cotter pin provides insights into its role within complex mechanical systems.
- Preventing Relative Motion
Securing, in the context of cotter joints, primarily involves preventing relative movement between connected components. A cotter pin, inserted into a corresponding slot, creates a wedge-like action that resists forces attempting to displace the parts. This is crucial in ensuring consistent operation of machinery and preventing premature wear or failure. Examples include connecting shafts to hubs in rotating machinery or securing parts within structures. The effectiveness of the securing mechanism directly impacts the overall dependability and operational life of the system.
- Resisting Forces and Loads
Cotter pins are designed to resist various forces and loads, maintaining a stable connection under stress. The wedge shape of the cotter provides clamping force that counters pulling, twisting, and bending forces. Correctly sized and placed cotter pins are essential for carrying the intended load. Failure to select and install appropriate cotter pins can lead to component failure or damage. This aspect demonstrates the crucial need for precise engineering calculations and material selection in securing components.
- Ensuring Alignment and Stability
Securing elements also play a role in maintaining precise alignment between parts. The cotter pin, functioning as a restraint, helps keep components aligned. This is vital for proper operation and prevents misalignment, which can lead to increased stress on parts and reduced efficiency. Precise alignment is essential in applications like gears, where even minute misalignment can lead to significant operational issues. The securing action is also critical to maintaining the structural stability of the system.
In essence, the process of securing, exemplified by the cotter joint, emphasizes the need for robust and reliable connections in mechanical systems. Proper securing methods directly influence the system's performance, durability, and safety. The selection and installation of cotter pins, therefore, are critical steps in ensuring the overall integrity of the mechanical assembly.
3. Shafts
Shafts, crucial elements in rotating machinery, often require secure connections. This necessitates specific fastening methods to maintain their integrity and functionality. The connection between shafts and cotter joints is critical; the cotter's role is to prevent relative movement between the shaft and the component it connects to.
- Shaft Alignment and Load Transmission
Precise alignment of shafts is essential for efficient load transmission. Misalignment can lead to increased stress and premature failure. Cotter joints play a vital role in maintaining alignment, preventing unwanted vibrations, and ensuring smooth power transfer. In automotive engines, for instance, shafts connect the crankshaft to the transmission, and cotter pins are used to secure these critical connections, facilitating the smooth transfer of rotational power.
- Preventing Axial Movement
Cotter joints are specifically designed to resist axial movement of the connected components. The wedge action of the cotter pin creates a strong clamping force, preventing the shaft from shifting or disengaging. This is crucial in applications where consistent rotational speed and precise positioning are critical. Imagine a machine tool spindle; precise axial positioning is critical to ensuring accuracy in machining.
- Material Selection and Load Capacity
The material selection for both the shaft and the cotter pin is paramount. The shaft material must have adequate strength to withstand the applied loads, while the cotter pin must possess sufficient tensile strength to resist shearing. Inadequate material selection can lead to joint failure under stress, highlighting the need for careful consideration of mechanical properties and load estimations. This is critical in industrial machinery where high torque is involved.
- Maintenance and Replacement
Cotter joints offer accessibility for maintenance and replacement of components. The design allows for relatively easy disassembly and reassembly, which is vital in industrial settings where regular maintenance is necessary. This feature simplifies inspection and replacement of parts, enhancing the overall serviceability of the connected components. Its important in agricultural equipment, as these require frequent maintenance due to operational conditions.
In summary, the relationship between shafts and cotter joints is essential for maintaining the integrity and functionality of rotating machinery. The cotter joint's ability to prevent relative movement, ensure alignment, and transmit loads effectively highlights its critical role in applications that rely on consistent and reliable rotational power transmission. Proper consideration of material selection, load calculations, and maintenance protocols are essential for safeguarding the reliability of the entire system.
4. Components
Components, as integral parts of a mechanical system, interact directly with fastening mechanisms like cotter joints. Understanding these interactions provides insights into the overall system's performance and reliability. The nature of the components significantly impacts the design choices and functionality of the cotter joint itself.
- Material Properties
The material properties of components directly influence the selection of appropriate cotter pins. Components subjected to high stress require cotter pins with corresponding tensile strength. Compatibility between component materials and the cotter pin material is essential to prevent failure due to dissimilar metal reactions or stress concentrations. For example, in an application involving stainless steel shafts and housings, a stainless steel cotter pin is crucial to maintain corrosion resistance and prevent degradation.
- Shape and Geometry
The shape and geometry of components dictate the design of the cotter joint slot or hole. The slot's dimensions must accommodate the cotter pin without compromising the structural integrity of the component. An overly narrow slot may lead to stress concentrations in the component or prevent the cotter pin from seating properly, thus affecting the joint's security. This necessitates careful consideration of the dimensions of the cotter pin and the corresponding slot or hole.
- Size and Load Capacity
The size and load capacity of components significantly affect the required cotter pin size. Heavier loads necessitate cotter pins with a higher load rating. A cotter pin insufficient for the applied load may fail, jeopardizing the integrity of the component or the entire assembly. Therefore, accurate load analysis and selection of appropriately sized cotter pins are crucial to ensure the mechanical system's longevity and safety.
- Interfacing Components
The way components interface influences the requirements for cotter pins. Components with complex geometries may require specialized cotter pin designs to achieve secure and reliable connections. Components that experience high vibration or impact may benefit from cotter pins with enhanced resistance to loosening or fatigue. Understanding this interaction is vital in ensuring the stability and proper functioning of the mechanism, especially when components interact in dynamic environments. For example, in a high-speed rotating assembly, choosing cotter pins with appropriate tolerances for vibration is crucial.
In conclusion, components and cotter joints are intrinsically linked. Careful consideration of component materials, shapes, sizes, and load capacities is essential to select and install appropriate cotter pins. This interplay directly impacts the mechanical system's strength, durability, and safety. A flawed connection between components and cotter joints can lead to system failure, highlighting the importance of meticulous engineering design and component selection.
5. Wedges
The concept of wedges is fundamental to understanding the function of cotter joints. Wedge action is a key principle in the design and operation of a cotter joint. Analyzing the characteristics of wedges illuminates the mechanism by which cotter pins achieve their securing function.
- Principle of Wedge Action
A wedge, by its very nature, exerts a force perpendicular to its inclined surface. This force, distributed along the wedge, increases the clamping pressure between the components it secures. This principle is directly applicable to the cotter joint, where the wedge-shaped cotter pin exerts a clamping force that prevents relative movement between the connected parts. The angle of the wedge, and the materials used, affect the clamping force generated.
- Force Multiplication and Load Transfer
Wedges are well-known for their ability to multiply force. The inclined surface of the wedge allows a smaller force applied over a larger distance to be translated into a larger force acting perpendicularly. In a cotter joint, this principle translates into the ability of a relatively small cotter pin to withstand significant loads, effectively transferring the load between connected components. This force multiplication is key to the cotter joint's ability to hold its load.
- Friction and Resistance to Movement
Friction plays a crucial role in the effectiveness of a wedge as a fastener. The wedged shape, combined with frictional forces between the cotter pin and the connected components, creates resistance to relative motion. This resistance is crucial in preventing slippage or loosening under various operating conditions. The material properties of the cotter pin and the components contribute to this frictional resistance. The geometry and the contact areas contribute to the degree of resistance.
- Design Considerations in Cotter Joint Application
The design of the cotter joint necessitates careful consideration of the wedge's geometry. The angle of the wedge significantly impacts the clamping force. The cross-sectional area of the wedge must be appropriate to the anticipated loads. Factors such as material properties and the anticipated operating environment are all variables that influence the optimal wedge design for the cotter joint.
In summary, the wedge is the core element in a cotter joint. Its ability to multiply force, resist movement through friction, and transmit loads between components is directly related to the securing function of the cotter joint. Proper wedge design is integral to ensuring the cotter joint's effectiveness and reliability. The use of wedges in fastening mechanisms is a fundamental principle in mechanical engineering, illustrating how simple geometric shapes can have substantial effects in structural support.
6. Tensile Strength
Tensile strength is a critical material property directly impacting the performance and reliability of a cotter joint. The ability of the cotter pin to withstand pulling forces is paramount to its function. Understanding tensile strength is essential for proper design and application of cotter joints to ensure the joint's integrity under load.
- Defining Tensile Strength
Tensile strength, measured in units like Pascals or pounds per square inch, represents a material's capacity to resist tensile stressa pulling force. For a cotter pin, this translates to its ability to withstand the pulling forces applied across the joint. A higher tensile strength indicates a greater capacity to resist deformation or failure under tension.
- Role in Cotter Joint Function
The cotter pin, acting as a wedge, experiences tensile stress as the load is applied across the joint. The tensile strength of the cotter pin material directly impacts its ability to withstand these forces. An insufficient tensile strength can result in the cotter pin yielding or breaking under load, compromising the joint's integrity. In a critical application, the cotter joint's failure would have significant consequences.
- Selection and Application Considerations
Selecting a cotter pin with an appropriate tensile strength is essential for a safe and reliable joint. Engineers must consider the expected loads on the joint and choose a cotter pin material with a tensile strength that exceeds these anticipated forces. Material selection guides and engineering specifications should be consulted for proper cotter pin selection. Overestimating the load can lead to unnecessarily high cost and potentially unnecessary weight of the cotter pin. Underestimating the load could lead to critical failure.
- Factors Affecting Tensile Strength
Material composition, processing methods, and environmental factors influence tensile strength. Heat treatment, for example, can significantly alter a material's tensile properties. Corrosion, or environmental degradation, can reduce a material's strength over time. Considerations of fatigue and creep, in dynamic environments, become important in certain contexts. This is essential for assessing a material's ability to withstand repeated load cycles.
In conclusion, tensile strength is a defining characteristic for the functionality and safety of a cotter joint. Proper assessment and selection of materials with adequate tensile strength are essential for ensuring the structural integrity and preventing failure under anticipated loads. Careful consideration of material properties and environmental effects further refines the engineering judgment needed to apply cotter joints effectively.
7. Machine Parts
Machine parts are the fundamental components that comprise a machine. They interact in specific ways, often requiring secure connections to function correctly. A cotter joint, a particular fastening method, plays a critical role in connecting various machine parts. The design and selection of machine parts directly influence the suitability and effectiveness of a cotter joint. A poorly designed or improperly sized machine part can compromise the strength and reliability of the entire assembly, affecting the machine's performance, lifespan, and even safety.
The connection between machine parts and cotter joints is evident in numerous applications. Consider a connecting rod in an engine. The rod's shape, size, and material properties significantly affect the cotter pin chosen for securing it to the crankshaft. A connecting rod made of a weaker alloy will necessitate a stronger cotter pin to withstand the forces involved in power transmission. Similarly, in a machine tool, the shaft and hub diameters, and the nature of the load they experience determine the necessary cotter pin dimensions and material. A cotter pin insufficiently strong for the applied forces would lead to failure, potentially leading to catastrophic consequences in high-speed machinery. Furthermore, the precision manufacturing of machine parts is critical for a cotter joint to properly engage, maintaining alignment and preventing unwanted movement.
In summary, the function of a cotter joint is inextricably linked to the characteristics of the machine parts it connects. Precise design and selection of machine parts, considering the specific loads and operating conditions, are essential for selecting an appropriate cotter joint. Proper matching of these elements ensures the machine's structural integrity, reliability, and overall performance. A weak link in one machine part can lead to failure of the entire system, highlighting the need for careful design consideration in machine part and cotter joint selection. This understanding directly impacts the safety, efficiency, and cost-effectiveness of the entire machine design.
8. Load Distribution
Load distribution, a critical aspect of mechanical design, significantly influences the performance and longevity of any system. In the context of cotter joints, proper load distribution is paramount for ensuring the joint's integrity and preventing premature failure. An understanding of how load is distributed across the joint is essential for choosing appropriate materials and dimensions for both the components and the cotter pin itself. This exploration will illuminate the crucial relationship between load distribution and cotter joints.
- Impact on Cotter Pin Selection
The way load is distributed across the joint profoundly affects the stress experienced by the cotter pin. Uneven load distribution results in higher stress concentrations in specific areas of the cotter pin, potentially leading to failure at these points. Conversely, uniform load distribution minimizes stress concentrations, enhancing the cotter pin's resistance to failure. An engineer must meticulously consider the anticipated forces and their distribution to select a cotter pin with the necessary strength and dimension to prevent failure. The specific location of applied forces, relative to the geometry of the cotter joint, significantly impacts the stress concentrations and potential points of failure.
- Influence on Component Stress
Load distribution affects the stress levels not only in the cotter pin but also within the connected components. A non-uniform distribution can lead to excessive stress in specific areas of the shaft or housing, potentially resulting in deformation or fracture. Uniform load distribution minimizes these risks, allowing for a more robust and reliable connection. By carefully considering the expected loads and their distribution, designers can ensure a safe and efficient connection. The method of loading (e.g., axial, torsional, or combined) dictates the design criteria for the cotter joint and its components.
- Effect on Joint Integrity
Load distribution directly impacts the overall integrity of the cotter joint. An uneven distribution can cause stress concentrations that weaken the connection, rendering it vulnerable to failure. Conversely, a well-distributed load minimizes these risks, ensuring the joint remains stable and functional. The material properties of the cotter pin and the connected components interact with the load distribution to affect the overall performance. The geometry of the joint, including the cotter pin's angle and the shape of the slot, impacts how the load is transferred and distributed.
In conclusion, load distribution is an integral element in the design and application of cotter joints. Considering the manner in which loads are distributed is crucial for selecting appropriate materials and dimensions, ensuring the integrity of the joint, and preventing potential failure. A comprehensive understanding of load distribution is necessary to create robust and reliable mechanical systems utilizing cotter joints.
Frequently Asked Questions about Cotter Joints
This section addresses common inquiries regarding cotter joints, a crucial type of fastening mechanism in mechanical engineering. Clear answers to these questions aim to provide a comprehensive understanding of cotter joint principles and applications.
Question 1: What is a cotter joint, and how does it function?
A cotter joint is a mechanical fastening method using a wedge-shaped pin (cotter) inserted into a slot. This wedge action creates clamping pressure, preventing relative movement between connected components, typically shafts and housings. The design leverages the wedge's geometry to resist pulling, twisting, and bending forces, ensuring a secure connection under load.
Question 2: What are the critical considerations when selecting a cotter pin?
Material selection is paramount. The cotter pin must possess sufficient tensile strength to withstand the anticipated loads. The pin's dimensions, including length and cross-sectional area, directly relate to its load-bearing capacity. Proper selection also considers the material properties of the connected components to avoid stress concentrations or compatibility issues. Factors like the operating environment (e.g., corrosion resistance) must also be considered.
Question 3: How is load distribution crucial in cotter joint design?
Uneven load distribution can lead to stress concentrations, potentially compromising the cotter pin or connected components. Uniform load distribution across the joint minimizes these risks, maximizing the joint's strength and longevity. Careful design considerations, such as the geometry of the joint and the placement of the cotter pin, influence load distribution.
Question 4: What are the potential consequences of using an improperly sized or selected cotter pin?
Using an improperly sized or selected cotter pin can result in several issues. Insufficient strength may lead to failure under load, potentially causing catastrophic equipment failure. Inadequate size may lead to improper seating, allowing components to shift and malfunction. Conversely, oversized pins may create excess stress on components or the joint itself.
Question 5: What are the maintenance implications for cotter joints?
Regular inspection and lubrication (when appropriate) are crucial for cotter joints. Regular visual checks for wear, deformation, or loosening are vital. Lubrication can reduce friction, improving the joint's longevity. Understanding the expected operating conditions allows for proactive maintenance schedules.
In summary, cotter joints, when properly designed and applied, offer a dependable and robust fastening solution. Careful consideration of material properties, load distribution, and maintenance protocols is essential for maximizing the safety, reliability, and lifespan of the connected components.
Transitioning to the next section, we'll explore advanced applications and design considerations for cotter joints in various engineering contexts.
Conclusion
This exploration of cotter joints underscores their fundamental role in mechanical engineering. The analysis highlighted the critical interplay of various factors, from material properties and load distribution to the geometry of the joint itself. Key considerations, such as tensile strength, proper sizing, and the prevention of stress concentrations, were emphasized. The examination revealed the importance of meticulous design and selection processes to ensure the reliability and longevity of these connections in diverse applications. Furthermore, the analysis showcased the critical link between the cotter joint and the overall performance and safety of the interconnected machine parts.
The effectiveness of cotter joints hinges on a comprehensive understanding of these interconnected factors. Engineers must carefully evaluate anticipated loads, material properties, and operating conditions to ensure optimal design. By meticulously considering these elements, the potential for catastrophic failure can be significantly reduced. This knowledge empowers engineers to select and implement cotter joints effectively and safely across a broad spectrum of applications, leading to robust and reliable mechanical systems. Continued research and development in advanced materials and fastening techniques will undoubtedly lead to further refinements in cotter joint technology.
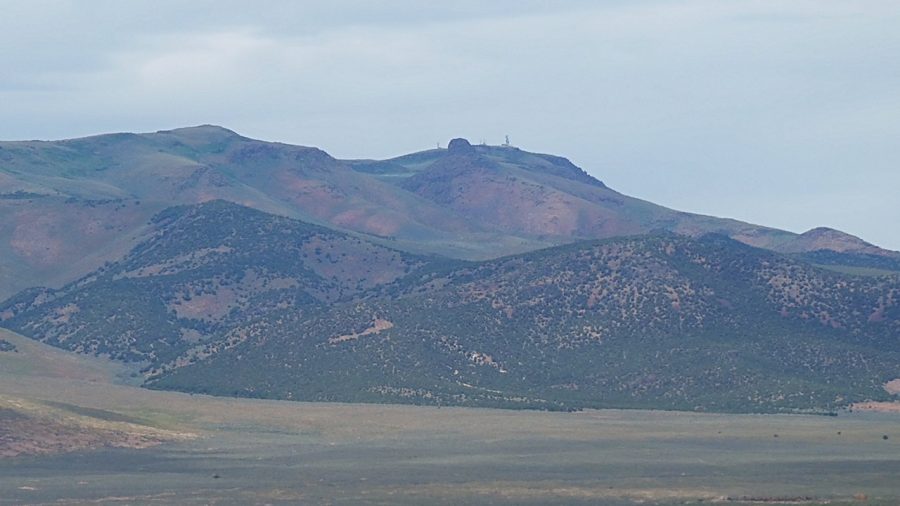
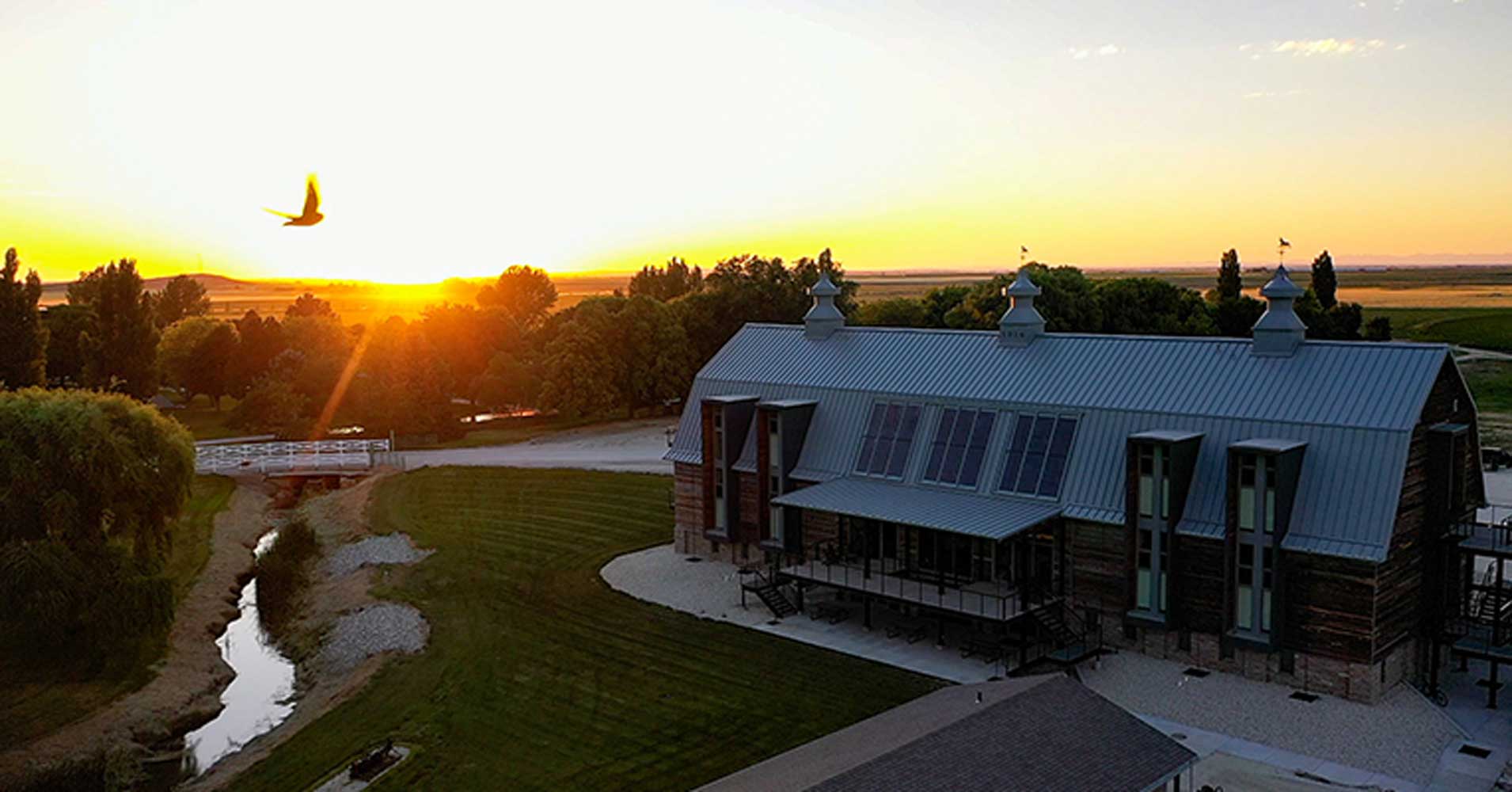
