What distinguishes these specialized blades and what makes them crucial tools for specific tasks? These knives, renowned for their exceptional build and functionality, hold a significant place in certain professional and practical circles.
These blades are characterized by their robust construction, often featuring full tangs, bolster designs, and specific blade geometries tailored for tasks like heavy-duty cutting, skinning, or specialized dismantling. Examples include those utilized in butchering or by individuals in the professional trades that demand precision and durability.
The importance of these knives stems from their ability to withstand considerable use and stress. Their enduring quality ensures efficiency and safety in demanding environments. Historical evidence suggests that these tools have been integral in crucial tasks and have served as reliable instruments in various cultures and industries for an extended duration. The focus on superior materials and construction reflects a commitment to longevity and performance.
Let's now delve into the specifics of their design and application, highlighting the key features that make them valuable to users in these specific sectors.
Hogue Knives
Understanding the essential attributes of Hogue knives is crucial for appreciating their purpose and value. These knives are meticulously crafted for specific applications.
- Durability
- Ergonomics
- Blade geometry
- Material strength
- Sharpness retention
- Purpose-driven design
- Professional applications
- Manufacturing precision
These knives' durability, along with their ergonomic designs, make them reliable tools for professionals. Specific blade geometries are crafted to maximize performance in tasks like skinning or butchering. The material strength ensures longevity and resistance to damage. Sharpness retention is crucial for precise cutting. Purpose-driven design and precision manufacturing combine to create instruments tailored for specific tasks. Professional application examples include use in butcher shops and by skinning professionals. High-quality materials and construction lead to significant advantages in various occupations. All these factors contribute to the overall value proposition of Hogue knives, making them a crucial tool in specific professional contexts.
1. Durability
Durability is a defining characteristic of Hogue knives. The inherent strength and resilience of these blades are critical to their effectiveness and longevity in demanding environments. Robust construction, often employing high-carbon steel or other reinforced materials, is a significant factor in achieving this durability. The design features, such as full tangs and bolster reinforcement, are directly related to the tool's ability to withstand repeated use and stresses inherent in professional applications. The ability of the knife to maintain its sharpness over extended periods contributes significantly to this overall resilience. Practical examples include prolonged use in butcher shops, where the knives experience consistent heavy-duty cutting, or in field operations, where the instruments face rigorous handling and varied tasks.
The importance of durability in these knives extends beyond mere longevity. It directly translates to enhanced safety and efficiency in critical tasks. A reliable blade that maintains its integrity under pressure minimizes the risk of accidents or equipment failure, preventing potential injuries. Furthermore, durability ensures the knives maintain consistent performance throughout their lifespan, maximizing productivity and reducing the need for frequent replacements, thereby contributing to cost-effectiveness over the long term. Examples of this can be seen in industrial settings, where downtime can be costly and reduced with reliable instruments, or in field operations where the availability of durable knives means uninterrupted work.
In summary, the durability of Hogue knives is a crucial element in their effectiveness and overall value. The consistent performance and longevity resulting from robust materials and design choices directly contribute to improved safety, efficiency, and cost-effectiveness in professional and practical contexts. Understanding this link between construction, durability, and end-user outcomes is fundamental to appreciating the advantages of these tools in demanding environments.
2. Ergonomics
Ergonomics plays a critical role in the design and effectiveness of Hogue knives. A well-designed ergonomic handle enhances usability, minimizing strain and maximizing control during various tasks. This factor directly affects user experience, safety, and overall performance.
- Grip and Control
The shape and texture of the handle significantly impact grip, particularly during extended use or in challenging conditions. A well-contoured handle provides a secure grip that reduces slippage. This is especially important for tasks requiring precise and controlled cutting, or in environments with potentially moist or slippery surfaces. Specific materials usedincluding variations in rubber or polymer compoundscontribute to this critical aspect. Variations in handle design (e.g., the use of jimping or textured surfaces) also directly influence grip control.
- Hand Positioning and Movement
Handle design influences how the hand is positioned and moved while manipulating the knife. Handles promoting a natural, comfortable hand position minimize fatigue during extended use. A knife's ergonomic design accommodates different hand sizes and shapes, ensuring a secure and appropriate fit. The positioning allows for greater precision and control during tasks that demand fine motor skills. The potential for injury through fatigue and strained muscles is mitigated significantly with carefully designed ergonomic features.
- Force Distribution
An ergonomic handle distributes forces exerted on the knife, reducing stress on the user's hand and wrist. Thoughtful design considers how forces are transferred through the handle material and into the hand, minimizing strain and fatigue. This consideration is essential in scenarios involving repeated or heavy use. The structural integrity of the handle ensures these forces are distributed effectively without compromising the blade's structural integrity. Proper force distribution minimizes the risk of hand cramps or injuries.
Ultimately, the ergonomic design of Hogue knives optimizes functionality and user experience. The combination of factors, from grip and control to force distribution, directly contributes to user comfort, safety, and productivity. This attention to detail translates into enhanced performance and reduces the risk of potential injuries or user discomfort during extended operation.
3. Blade Geometry
Blade geometry in Hogue knives is not merely a design element; it's a critical factor influencing performance, functionality, and overall effectiveness. The shape and form of the blade directly impact its cutting ability, efficiency in various tasks, and safety for the user. Understanding these nuances is essential for comprehending the specific applications for which these knives are intended.
- Cutting Edge Profile
The shape of the blade's cutting edgewhether it's a drop point, clip point, or another variationsignificantly impacts its ability to slice, pierce, or chop. Different profiles excel in different types of cutting. A knife designed with a pointed edge might be ideal for intricate cutting tasks, while a knife with a broader, more robust edge might be better suited for heavy-duty chopping. Hogue knives often employ profiles that optimize their performance in particular application areas. Understanding the blade's cutting edge profile provides insight into the knife's intended role.
- Blade Thickness and Curve
Blade thickness and curvature influence the knife's strength, flexibility, and sharpness retention. A thicker blade might offer greater durability but potentially less dexterity, while a thinner blade may be more precise but less resistant to damage. Curve and the shape of the blade, in conjunction with the overall design, are critical to the knife's overall effectiveness in various applications. The balance between strength and precision is a key consideration in this area.
- Blade Angle and Grind
The angle and grind of a knife's blade affect sharpness, cutting efficiency, and the durability of the edge. Different grind types yield different levels of sharpness, sharpness retention, and resistance to damage. The combination of these design elements is essential in achieving a balance between sharpness and longevity. The choice of angle and grind is a direct reflection of the anticipated use of the knife.
- Shape and Size of the Point
The shape and size of the blade's point, when combined with the overall design, directly correlate with the knife's function. A pointed tip excels at piercing, while a blunt tip is better suited for crushing. Hogue knives often use points optimized for their target applications, reflecting a focus on utility and functionality. The relative size of the point also affects how much pressure is required for different cutting tasks.
In conclusion, the blade geometry in Hogue knives is a fundamental aspect of their design, directly influencing their cutting performance, functionality, and suitability for specific tasks. Understanding the distinct features of blade geometry clarifies how these knives are tailored for different applications, allowing users to select the most appropriate tool for a given task.
4. Material Strength
Material strength is paramount in Hogue knives. The efficacy and longevity of these tools are directly correlated to the inherent properties of the materials employed in their construction. High-performance materials contribute significantly to durability and resistance to damage, thereby enhancing the knife's operational lifespan. Choosing appropriate materials is critical for achieving intended functionality, particularly in high-stress environments. For instance, a knife blade destined for repeated, heavy-duty tasks necessitates a material resistant to bending, chipping, and weakening under strain. Materials with high tensile strength and hardness are pivotal in ensuring consistent performance across diverse applications.
The selection and application of specific materials significantly impact the knife's resistance to wear and tear, a crucial element in professional and practical settings. Consider a butcher's knife: the blade material must withstand the constant force of cutting through tough cuts of meat. Similarly, a knife used in field operations needs to withstand the rigors of demanding environments and various tasks. The choice of materials directly influences the knife's capability to maintain sharpness, hold its edge, and retain its structural integrity throughout its service life. This translates to improved efficiency and safety for the user. The practical implications of understanding material strength extend to the ability to anticipate the knife's performance in specific scenarios, and therefore to properly match the tool to the task.
In summary, material strength is a fundamental aspect of Hogue knives' design and functionality. Understanding the relationship between material properties and operational requirements is critical for maximizing the knife's performance and lifespan. Appropriate material choices are directly linked to durability, edge retention, and safety, making informed decisions about material strength crucial for professionals and practitioners alike. The selection of materials dictates the knife's capability to effectively perform the anticipated tasks, emphasizing the significance of understanding these principles for optimal outcomes.
5. Sharpness Retention
Sharpness retention is a critical aspect of Hogue knives, directly impacting their performance and longevity. Maintaining a keen edge is paramount for effective cutting, whether in professional or practical applications. A dull blade necessitates more force, reduces efficiency, and increases the risk of injury. The ability of a blade to retain its sharpness underscores its overall utility and value.
- Material Composition
The choice of steel significantly influences a knife's ability to retain sharpness. High-carbon steels, often employed in Hogue knives, are known for their hardness and resistance to wear, which contributes to excellent edge retention. Different grades of steel exhibit varying degrees of sharpness retention, impacting the knife's suitability for specific tasks. The microstructure of the steel plays a pivotal role in how effectively it retains an edge.
- Heat Treatment Processes
Precise heat treatment procedures are crucial for achieving the desired hardness and toughness in the steel. This process alters the steel's microstructure to enhance its resistance to deformation during use, thus affecting sharpness retention. Variations in heat treatment can dramatically impact a blade's edge retention characteristics. The particular heat treatment employed directly affects the knife's resilience and its ability to maintain a keen edge during use.
- Blade Geometry and Grind
Blade geometry, including the angle and shape of the cutting edge, greatly impacts sharpness retention. A well-designed grind provides a sharp and durable edge that resists chipping and dulling. The shape of the blade, alongside the grind's precision, optimizes the retention of sharpness. Factors like the blade's thickness and curvature contribute to its overall resilience and the maintenance of a cutting edge.
- Maintenance Practices
Regular maintenance, including proper sharpening techniques and storage practices, is crucial for maintaining a sharp edge. These practices directly influence a blade's ability to retain sharpness for an extended period. Appropriate sharpening tools and techniques can significantly impact the blade's performance. The application of sharpening and cleaning procedures extends the knife's lifespan and maintains optimal cutting performance.
In conclusion, the interplay of material composition, heat treatment, blade geometry, and maintenance practices defines a knife's sharpness retention. Hogue knives, by prioritizing these factors in their design, ensure a high level of performance and longevity. By understanding these elements, users can make informed choices, ensuring the optimal function and durability of their knives. The inherent trade-offs between factors such as blade strength, edge retention, and flexibility need careful consideration when selecting a specific type of knife.
6. Purpose-driven design
Purpose-driven design in Hogue knives is a critical component, influencing the knife's overall utility and performance. The design prioritizes functionality, ensuring optimal performance in specific applications. This approach directly impacts the knife's efficacy, safety, and longevity. The inherent value of Hogue knives is predicated on a careful understanding of specific user needs and the precise tasks the knives will perform. Examples include the specialized designs for butchering, skinning, or general utilityeach tailored for its designated purpose.
Consider a skinning knife. Its slender blade, often with a pointed tip and a sharpened spine, is specifically designed for cleanly separating hide from flesh. A similar logic applies to a utility knife. Its broader blade and robust construction are ideal for various tasks requiring more substantial cutting force. The design of the knife's handle also reflects this purpose-driven approach. Features like jimping, texture, and specific shapes enhance a secure grip, accommodating varying hand sizes and increasing user control during demanding tasks. This alignment of form and function contributes directly to the knife's overall effectiveness and safety. This tailored approach ensures the knife is appropriately suited to its intended task, enhancing safety and improving efficiency.
In conclusion, a purpose-driven design approach is integral to Hogue knives. The careful consideration of specific tasks translates into optimized performance, enhanced safety, and improved user experience. Understanding this approach underlines the fundamental value proposition of these knives, underscoring their suitability for particular professional and practical applications. By examining the specific design features of each knife, users can ascertain its appropriateness for the specific task and enhance the efficacy of their work. This understanding ensures that the selected tool aligns precisely with the task at hand. The practical significance of this principle is evident in a wide range of sectors, from professional butchery to everyday utility. It's this fundamental alignment of design with purpose that differentiates these knives and underpins their value.
7. Professional applications
Hogue knives frequently find application in professional settings where reliability, durability, and precise performance are paramount. The specific designs and materials utilized in these knives often align with the requirements of various trades and occupations. Understanding these applications highlights the crucial role of Hogue knives in specific professional contexts.
- Butchery and Meat Processing
Hogue knives, particularly those with robust blades and ergonomic handles, are essential tools in butcher shops and meat processing facilities. Their durability and sharp edges allow for efficient and precise cutting of various meats. The specialized blade geometries enable precise trimming, portioning, and deboning. The knives' ability to withstand repeated heavy use is crucial in this demanding environment. The ergonomic design minimizes strain on butchers' hands during extended periods of use, leading to enhanced safety and reduced worker fatigue.
- Skinning and Field Dressing
In industries such as hunting, fishing, and wildlife management, Hogue knives are frequently utilized for skinning, field dressing, and processing game animals. The specific blade profiles, often with pointed tips and durable construction, ensure precise and efficient removal of hides and processing. The knives' ability to retain a sharp edge during repeated use is vital. The durable materials mitigate the impact of tough animal tissues, maintaining the knife's sharpness and structural integrity throughout the process.
- Trades and Manufacturing
Certain trades, such as carpentry, construction, and industrial maintenance, rely on Hogue knives for specific tasks. Their robust blades and sometimes unique handle designs accommodate various cutting needs. The design of the knife may reflect specific requirements like the need for leverage or precision cutting. The durability of the material allows for tasks requiring significant force or repetitive use. These knives are crucial tools for maintaining equipment, preparing materials, and performing specific tasks.
- Law Enforcement and Security
In specific law enforcement and security applications, Hogue knives, depending on the model, may be employed for tactical or utility purposes. The design often prioritizes durability and maneuverability. The specific materials and construction features prioritize resilience during potential high-impact situations. These knives can have a variety of applications from general-purpose cutting to specialized tasks, and often incorporate features that enhance performance in specific scenarios.
These examples illustrate the broad range of professional applications for Hogue knives. The connection between the knives' design features and the particular demands of each profession underscores the importance of tailored design. The reliable and durable nature of Hogue knives, combined with their specific design features, makes them valuable tools in various professional environments, enhancing performance, safety, and efficiency in diverse fields. This highlights the importance of matching the knife to the specific task.
8. Manufacturing Precision
Manufacturing precision is fundamental to the quality and dependability of Hogue knives. Exceptional attention to detail in every stage of production ensures the final product meets exacting standards of performance, durability, and safety. This meticulous approach guarantees the knife's ability to withstand rigorous use, maintaining its sharpness and functionality for extended periods. The commitment to precision in manufacturing directly correlates with the user's experience and the overall value proposition of the product.
- Material Selection and Control
Precise selection and control of materials are critical. The choice of steel grade, its hardness, and its carbon content directly impact the knife's edge retention, durability, and resistance to wear. Variations in these properties, even subtle ones, can significantly affect the knife's performance in different use cases. Rigorous material testing ensures the chosen materials consistently meet predefined standards. This meticulous process safeguards against inconsistencies or defects, upholding a high level of quality across all manufactured knives.
- Blade Geometry and Grind Precision
Exacting tolerances in blade geometry and the grind are vital. The precise angles, curves, and thickness of the blade significantly influence sharpness, balance, and overall performance. Variations in these aspects, even minute ones, can compromise a knife's cutting ability or lead to uneven wear. Advanced tools and techniques, combined with strict quality control measures, maintain uniformity in blade shapes, ensuring consistent performance.
- Handle Construction and Fit
Precise machining and assembly of the handle are essential. The handle's form and its fit with the blade affect grip, ergonomics, and overall balance. Maintaining precise tolerances ensures a secure grip, even in challenging conditions. This crucial attention to detail mitigates potential slippage and user discomfort. The meticulous joining of the handle components to the blade tang ensures structural integrity.
- Quality Control Measures
Comprehensive quality control checkpoints are implemented throughout the manufacturing process. Each stage involves rigorous inspection to identify and rectify any deviations from established specifications. This proactive approach helps maintain high standards, guaranteeing the consistency of quality and preventing defects from reaching the consumer. Testing under simulated stress conditions, for example, helps ascertain the resilience and functionality of the completed knife.
In summary, manufacturing precision in Hogue knives translates to a superior product. The rigorous attention to detail in material selection, blade geometry, handle fit, and quality control contributes to durability, performance, and overall value. These factors directly affect the knife's ability to function as a reliable and effective tool, thereby satisfying the needs of professional users. This unwavering commitment to precision underpins Hogue's reputation for producing high-quality, dependable knives.
Hogue Knives FAQs
This section addresses common questions about Hogue knives, providing clear and concise answers to promote understanding and informed decision-making.
Question 1: What types of steel are commonly used in Hogue knives?
Hogue knives frequently utilize high-carbon stainless steels known for their strength, durability, and edge retention. Specific grades vary depending on the intended use and application of the knife. These materials are selected for their ability to withstand heavy use and maintain sharpness.
Question 2: How do Hogue knives compare in terms of durability to other brands?
Hogue knives are renowned for their robust construction and durable materials. This translates to a high level of resistance to wear and tear, often exceeding that of comparable knives in certain applications. However, comparative durability can depend on specific steel types and construction details in each brand.
Question 3: Are Hogue knives suitable for professional use?
Yes, many Hogue knife models are designed for professional applications, incorporating features like robust blades, ergonomic handles, and durable materials. Their suitability depends on the specific task and the professional context. Careful consideration of the blade geometry and materials is essential when selecting a knife for a professional role.
Question 4: What maintenance is required to keep Hogue knives in optimal condition?
Regular sharpening and proper cleaning are essential for maintaining a Hogue knife's sharpness and longevity. Following the manufacturer's instructions for sharpening and storage is recommended. The method of sharpening is critical to sustaining a functional cutting edge. Proper care can extend the life of a Hogue knife significantly.
Question 5: How do ergonomic designs in Hogue knives enhance user experience?
Ergonomic designs in Hogue knives prioritize user comfort and control. Features such as textured handles and contoured grips reduce hand fatigue, minimizing the risk of injury during extended use. These designs also enhance precision and control in demanding tasks, making the knives more efficient.
These frequently asked questions offer a comprehensive overview of Hogue knives and their various attributes, highlighting essential considerations for both professional and casual users. Understanding these details can assist in selecting the appropriate Hogue knife for specific tasks and applications.
Next, let's delve deeper into the specific types of Hogue knives and their associated applications.
Conclusion
Hogue knives exhibit a distinct design philosophy prioritizing durability, functionality, and precision. This focus on material strength, coupled with ergonomic handle designs and specific blade geometries, results in tools exceptionally suited to demanding tasks. The knives' performance in professional settings, such as butcher shops, hunting, and various trades, underscores their efficacy in specific applications. Manufacturing precision contributes significantly to the long-term reliability and consistent performance of these knives. Thorough understanding of the knife's material properties, blade geometry, and intended use significantly impacts optimal performance and user safety. The commitment to sharpness retention further enhances functionality across a wide spectrum of professional and practical applications.
The exploration of Hogue knives reveals a commitment to crafting tools designed for enduring performance. The combination of meticulous manufacturing, specific material choices, and ergonomic designs contributes to the knives' lasting value proposition. Appreciating these crucial design elements empowers users to select knives optimally suited to specific tasks, thereby improving efficiency and safety in professional and practical contexts. The enduring quality and functionality of Hogue knives stand as a testament to the importance of careful consideration in tool design and application.
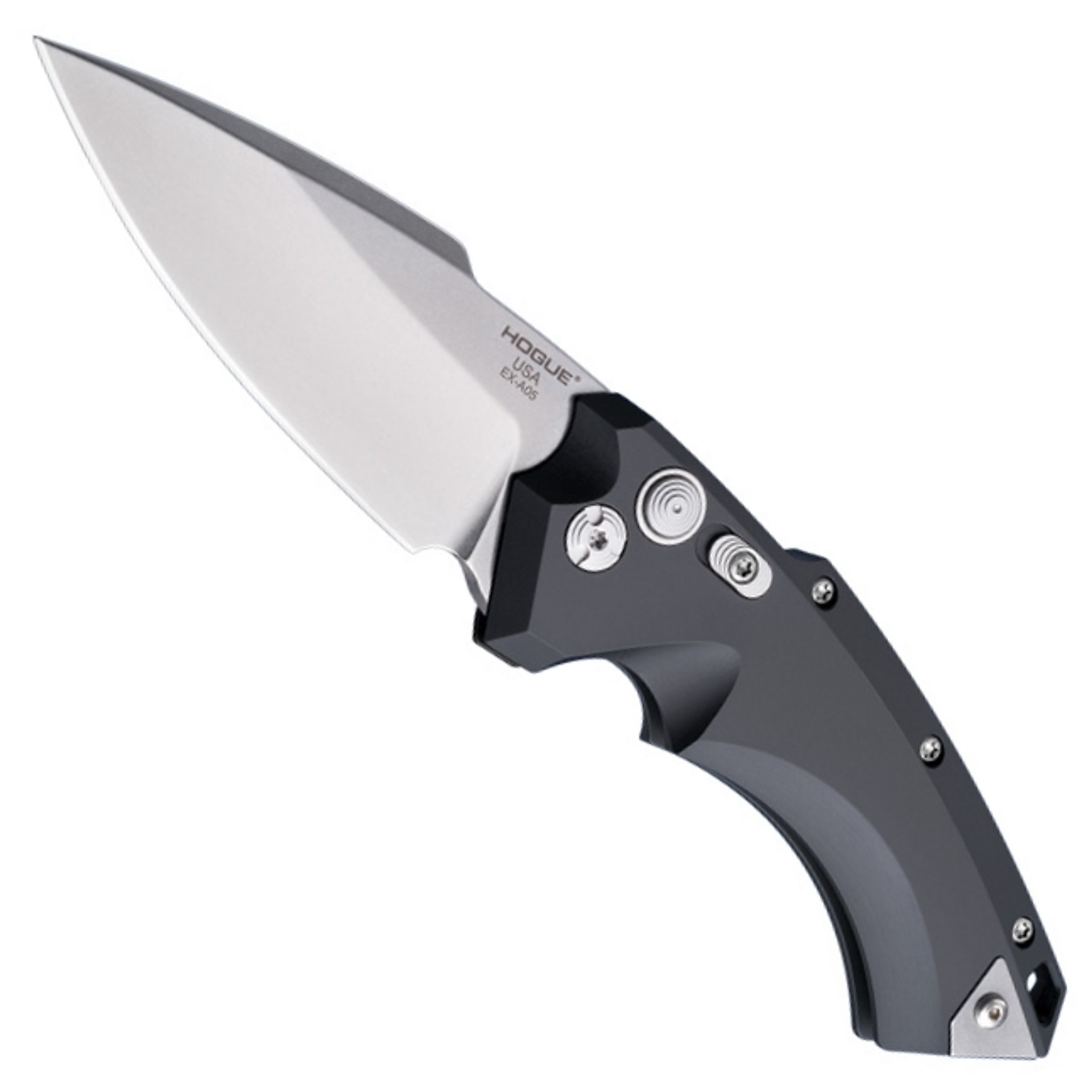

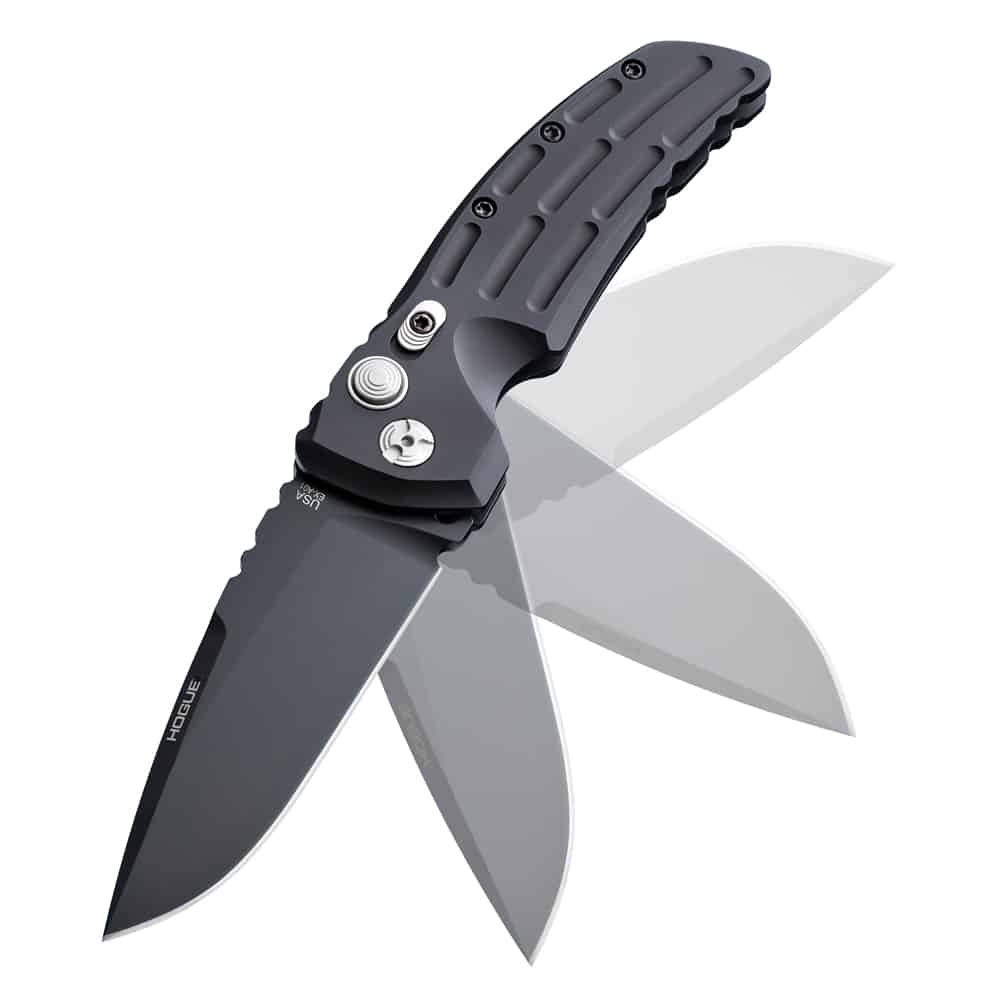