What is this essential tool, and how does it impact various fields?
A grinding or pulverizing device, typically a cylindrical stone or a mechanical apparatus, is often used in diverse applications. It can involve preparing pigments, mixing ingredients, or creating a fine powder. Variations exist, from simple hand-cranked models to sophisticated industrial machines. An example includes a mortar and pestle, a common tool in traditional medicine and culinary practices for grinding herbs and spices. Another example is a specialized piece of machinery employed in the ceramic industry for processing clay.
The effectiveness of this device depends on its design and material composition. The grinding action allows for a consistent reduction in particle size, facilitating the desired outcome. In the preparation of ceramics, a machine of this type is crucial for achieving the uniformity needed in various processes. The tool is vital in creating fine textures used in art, food preparation, or industrial production. Historical records show the use of similar tools for centuries in diverse cultures, highlighting their enduring value.
The discussion will now transition to the broader applications of grinding tools within various industries and fields.
A Muller
Understanding the multifaceted nature of a mullera tool for grinding or pulverizingrequires examining its key functions and applications. This exploration highlights crucial aspects for comprehending its role.
- Grinding
- Pulverizing
- Mixing
- Uniformity
- Particle size reduction
- Material preparation
- Industrial use
A muller's function as a grinding tool is essential in achieving a consistent particle size. This is crucial in numerous industries, from ceramics to pharmaceuticals. Mixing ingredients uniformly is critical in creating consistent products, especially in food and cosmetics. Particle size reduction enables substances to be incorporated effectively into formulations or to be better distributed. The preparation of materials for other processes is directly related to the quality of the initial grinding. Examples include pigments for paints, inks, or ceramics; or materials in manufacturing. The industrial applications, including processing minerals and pigments, solidify the tool's importance. A muller's application demonstrates its wide-ranging influence across various sectors.
1. Grinding
Grinding, a fundamental process in numerous applications, is intrinsically linked to the function of a muller. The muller, often a cylindrical stone or mechanical device, is specifically designed for grinding. The process of grinding involves the controlled reduction of material particle size through friction and pressure. This mechanical action is essential in achieving uniformity and consistency in the final product. A muller's effectiveness lies in its ability to exert controlled force and pressure, leading to optimal grinding results. Examples range from the traditional use of a mortar and pestle to grind spices and herbs to the sophisticated machinery used in the ceramic industry for processing clay. In these instances, the controlled grinding facilitated by a muller is crucial for creating a usable product with consistent properties.
The importance of grinding, facilitated by a muller, extends beyond these examples. In the pharmaceutical industry, consistent particle size is critical for the effectiveness and safety of medications. Grinding ensures a uniform distribution of active ingredients within the dosage form. In pigment production, the finely ground particles contribute to the intensity and color consistency of paints and inks. Moreover, the efficiency of a muller-based grinding process influences the overall cost-effectiveness and productivity of operations in various sectors. Optimized grinding, achieved through the appropriate selection and use of a muller, translates directly into improved product quality and reduced production costs.
In conclusion, the connection between grinding and a muller is undeniable. Grinding, a fundamental process involving controlled particle size reduction, is directly enabled by a muller's design and functionality. The resulting uniformity and consistency are critical across numerous industries, from traditional practices to advanced manufacturing. Understanding the intricacies of this relationship empowers informed choices in selecting and utilizing the appropriate grinding tools and techniques to optimize production processes and achieve desired outcomes.
2. Pulverizing
Pulverizing, the act of reducing a substance to a very fine powder, frequently relies on a muller's action. The controlled force exerted by the muller, whether a stone or a mechanical device, facilitates the comminution process. This reduction in particle size is crucial for various applications, enabling effective mixing, uniform dispersion, and enhanced reactivity. The controlled, consistent pressure applied by a muller is vital in pulverizing materials effectively. The selection of the appropriate muller, considering the material's properties and desired outcome, plays a significant role in achieving optimal pulverization results. For example, in the production of pigments, a muller is essential for reducing the size of pigments to achieve the desired color intensity and consistency in paints.
The importance of pulverizing through a muller's action extends across numerous industries. In the pharmaceutical industry, pulverizing active ingredients to a precise particle size is critical for effective drug absorption and delivery. In the ceramic industry, pulverizing clay and other minerals to a homogenous powder is essential for producing consistent and high-quality products. Agricultural industries rely on pulverizing soil and fertilizers for enhanced nutrient delivery and improved soil structure. The efficiency and precision of pulverization, achieved with a suitable muller, directly impact the quality, efficacy, and cost-effectiveness of these processes. Furthermore, the ability to control the fineness of the powder achieved through pulverizing with a muller greatly impacts the final product's properties and functionality. The final consistency and homogeneity of the powder profoundly affect the performance of the end product.
In summary, pulverizing, using a muller as a critical tool, plays a pivotal role in achieving consistent and fine particle sizes. The controlled nature of the pulverizing process, facilitated by the selection and use of a suitable muller, is essential for achieving optimal results across diverse sectors. The application of a muller underscores the significance of meticulous material preparation for consistent product performance, highlighting the value of proper selection and operation in optimizing the process and minimizing wasted materials. This meticulous control ensures efficient use of materials and enhances the overall effectiveness of the process.
3. Mixing
The connection between mixing and a muller lies in the tool's ability to facilitate uniform dispersion and integration of materials. A muller's function, whether grinding, pulverizing, or both, often precedes mixing. The resultant fine particle size allows for superior integration of ingredients, leading to consistent and homogenous mixtures. This exploration examines the role of a muller in the mixing process.
- Homogenous Material Integration
A muller's role in mixing is crucial for achieving a homogeneous blend. The fine particles produced through grinding or pulverizing ensure that components are evenly distributed. This is particularly important in applications requiring precise ratios and properties, such as pharmaceuticals or paints. Without thorough grinding or pulverizing prior to mixing, materials may not integrate evenly. This results in uneven distribution, impacting product efficacy or aesthetic quality.
- Enhanced Reactivity and Dispersion
The improved dispersion facilitated by a muller's pre-mixing action leads to enhanced reactivity between components. Finely divided particles have a greater surface area for interaction, driving faster and more thorough reactions. This heightened reactivity is essential in chemical processes where precise mixtures are required. In the production of ceramics, for instance, the use of a muller to pulverize raw materials maximizes surface contact, accelerating chemical reactions in the subsequent firing process.
- Consistent Product Properties
A muller contributes to the creation of consistent product properties. The precision in size reduction and subsequent mixing leads to predictable and repeatable results in the final product. This consistency is essential in manufacturing settings where maintaining uniform product quality is critical. For instance, in the production of cosmetics, the homogeneous mixing achieved through the use of a muller ensures consistent product texture and color, satisfying customer expectations.
In conclusion, the process of mixing benefits significantly from the preparatory work of a muller. The tool's ability to ensure uniform particle size directly impacts the final outcome in mixing. The uniformity in blends and the enhanced reactivity resulting from grinding or pulverizing actions achieved through a muller enhance the efficiency and effectiveness of mixing processes in numerous sectors. From pharmaceuticals to ceramics to cosmetics, a muller's role in achieving homogenous mixtures underscores its value in various industries.
4. Uniformity
Uniformity, a critical attribute in numerous processes, is intrinsically linked to the function of a muller. The effectiveness of a muller hinges on its ability to produce a consistent particle size and distribution in the materials it processes. This, in turn, directly influences the uniformity of the final product. The controlled nature of a muller's grinding or pulverizing action is essential for achieving this uniformity. Variations in particle size or distribution lead to inconsistencies in the final product, affecting its properties and performance.
Consider the production of ceramics. Uniform particle size and distribution of raw materials, achieved through meticulous grinding with a muller, are crucial for achieving a consistent ceramic product. Uneven particle sizes can result in variations in density, color, and strength, impacting the quality of the final ceramic piece. Similarly, in the pharmaceutical industry, precise particle size reduction with a muller is vital for maintaining uniform drug dosage and efficacy. Variations in particle size can affect drug absorption and bioavailability, potentially compromising patient treatment. In the production of paints and pigments, uniformity in particle size, achieved by the consistent action of a muller, ensures consistent color intensity and opacity, thereby guaranteeing the desired aesthetic and functional outcomes.
The principle of uniformity, driven by a muller's consistent action, is fundamental to achieving predictable and consistent outcomes in various sectors. Maintaining uniformity in material properties directly translates to reliable and consistent product performance. Understanding the intricate relationship between a muller's design, operating parameters, and the resulting uniformity is essential for optimization of processes and enhancement of product quality. Careful selection and operation of a muller, as well as consideration of the specific material being processed, directly impact the level of uniformity achieved and ultimately, the quality of the end product.
5. Particle Size Reduction
Particle size reduction is a fundamental process in numerous industrial and scientific applications. A key instrument in this process is the muller, a device designed for the controlled grinding or pulverizing of materials. The intimate connection between particle size reduction and the muller lies in the device's ability to effectively manipulate material properties.
- Mechanism of Action
The muller's mechanism of action involves applying controlled pressure and friction to a material. This mechanical action breaks down larger particles into smaller ones, leading to a reduction in average particle size. The specific design of the muller, whether a simple mortar and pestle or a complex industrial machine, influences the efficiency and degree of particle size reduction achievable. The type of material being processed also dictates the appropriate muller design and operating parameters.
- Impact on Material Properties
Reducing particle size significantly alters material properties. A smaller particle size often increases the surface area of the material, which impacts reactivity, solubility, and dispersibility. Increased surface area facilitates interactions with other substances, leading to faster reactions or more efficient mixing in subsequent processes. In applications like pigment production, a finely ground powder allows for greater color intensity and uniformity in the final product. In pharmaceuticals, reduced particle size enhances drug absorption and bioavailability.
- Control and Efficiency
The degree of particle size reduction and its uniformity are controllable factors in a muller-based process. Sophisticated designs and operating parameters allow for precise control over the grinding or pulverizing action. This precise control is pivotal for consistent quality in the final product and minimizes material waste, making the process cost-effective. Accurate measurement of particle size, before and after processing with a muller, allows for process optimization.
- Applications Across Industries
Particle size reduction through muller-based methods is essential across various industries. Ceramics, paints, pharmaceuticals, and food products all benefit from controlled particle size reductions. The specific application and design of the muller are adapted to the unique needs of each sector. This adaptable nature underscores the versatility and significance of the muller in various industrial contexts.
In conclusion, particle size reduction, expertly facilitated by a muller, is a crucial process with far-reaching implications across numerous industries. The ability to precisely control this process, coupled with its impact on material properties, showcases the muller's vital role in modern manufacturing and scientific endeavors.
6. Material Preparation
Material preparation, a crucial preliminary step in numerous industrial processes, directly impacts the effectiveness and efficiency of subsequent operations. A muller plays a significant role in this preparation, particularly concerning the reduction and modification of particle size and the creation of homogeneous mixtures. This exploration examines the key aspects of material preparation facilitated by a muller.
- Particle Size Reduction
A muller's primary function in material preparation is the reduction of particle size. This process, whether grinding or pulverizing, is critical for achieving desired properties in the final product. For instance, in ceramic production, the initial grinding of raw materials with a muller ensures consistent particle size, crucial for achieving uniform density and color in the finished product. Similarly, in the pharmaceutical industry, reducing active ingredients to specific particle sizes enables efficient drug absorption and delivery.
- Material Homogenization
Material homogenization is another essential aspect of preparation where a muller plays a critical role. The controlled grinding or pulverizing action of a muller ensures that various components are evenly distributed throughout the material. This uniformity is vital in ensuring consistent product properties, crucial in industries like paints and coatings where uniform color and texture are essential. The consistent mixing action of a muller ensures a homogenous blend of pigments, providing a consistent final product.
- Surface Area Modification
Modifying the surface area of materials is often a crucial part of material preparation. A muller, by reducing particle size, dramatically increases the surface area of the processed material. This increased surface area significantly impacts subsequent processes, such as chemical reactions, adsorption, or coating. For instance, in catalyst production, a muller is used to create finely divided powders with a large surface area. This enables better contact between the catalyst and reactants, improving catalytic activity.
- Material Mixing and Blending
A muller is frequently used in the mixing and blending of materials. The controlled grinding or pulverizing action facilitates thorough mixing of disparate components. This controlled mixing of ingredients is vital for achieving uniform dispersions in various products. In the food industry, for example, the mixing of ingredients through a muller ensures uniform distribution and consistent product texture.
In conclusion, material preparation is inextricably linked to the effectiveness and efficiency of a muller. The controlled particle size reduction, homogenization, surface area modification, and mixing facilitated by a muller are essential for a wide range of applications. By understanding these facets, one gains a deeper appreciation for the multifaceted role of a muller in preparing materials for downstream processing.
7. Industrial use
A muller's significance extends beyond rudimentary applications. Industrial use of this tool reveals its profound impact on various manufacturing processes. The effectiveness of a muller in these applications hinges on its ability to precisely control particle size reduction, homogeneity, and material properties.
- Ceramic Production
In the ceramic industry, a muller plays a critical role in preparing raw materials. The controlled grinding action ensures uniform particle size and distribution of clay and other minerals. This uniformity is essential for creating consistent products with desired properties, including density, color, and strength. Consistent particle size reduction also optimizes subsequent steps in the ceramic production process, such as shaping and firing.
- Pigment Manufacturing
Pigment manufacturing heavily relies on a muller's ability to finely grind pigments, achieving consistent particle size and dispersion. This process is crucial in producing uniform color intensity and opacity in paints, inks, and other coatings. The controlled grinding action ensures consistent quality and minimizes variability in the final product.
- Pharmaceutical Production
The pharmaceutical industry utilizes a muller for the precise pulverization of active pharmaceutical ingredients (APIs). This process ensures consistent particle size, which is critical for maintaining the efficacy and safety of medications. Fine particle size also facilitates optimal drug dissolution and absorption, contributing to enhanced treatment outcomes. The consistent nature of a muller's action is essential in maintaining quality control and ensuring the reliability of pharmaceutical products.
- Mineral Processing
A muller's application extends to mineral processing where it is instrumental in reducing the particle size of ores and minerals. This process, crucial in extracting valuable components, enhances the efficiency of downstream operations, such as separation and refining. Controlled grinding and pulverization are essential to extract valuable components cost-effectively.
Across these diverse industrial applications, a muller's ability to precisely manipulate material properties is a key factor in the overall efficiency of the process. The consistency in particle size reduction and material distribution is directly related to the quality of the final product and the economic viability of the manufacturing process. A muller's fundamental role underscores its enduring importance in contemporary industrial practices.
Frequently Asked Questions About a Muller
This section addresses common queries about a muller, a crucial tool in various industrial and scientific applications. These questions and answers provide a clear understanding of its functionality and significance.
Question 1: What is a muller, and what are its primary functions?
A muller is a device used for grinding or pulverizing materials. Its primary functions include reducing particle size, creating homogeneous mixtures, and preparing materials for further processing. The specific design and operation of a muller adapt to the required particle size reduction and desired final product properties.
Question 2: What are the key applications of a muller across various industries?
A muller finds application in diverse sectors. In ceramics, it ensures uniform particle size of clay and other minerals. In pigment manufacturing, it produces consistent pigment dispersions in paints and coatings. The pharmaceutical industry uses it for precise pulverization of active ingredients. Mineral processing also utilizes a muller for reducing ore particle size. Each industry tailors its use to the specific material and desired outcome.
Question 3: How does a muller contribute to the uniformity of a final product?
The consistent action of a muller leads to uniform particle size and distribution of materials. This uniformity is crucial for producing consistent product properties, such as color, texture, or density. Variations in particle size directly impact the final product's characteristics.
Question 4: What factors influence the selection of a suitable muller for a specific application?
The selection of an appropriate muller depends on the material being processed and the desired particle size reduction. Factors like material hardness, desired particle size, and the scale of production influence the choice between different types and sizes of mullers. Safety considerations are also important.
Question 5: What are the advantages of using a muller-based material preparation process?
A muller-based process offers advantages like controlled particle size reduction, improved material homogeneity, and enhanced reactivity of components. These benefits translate to consistent product quality, optimized processes, and reduced material waste in various industrial settings. Increased efficiency and cost-effectiveness often result from the controlled nature of the process.
In summary, a muller stands as a versatile and essential tool in material preparation and processing. Its ability to precisely control particle size and homogeneity highlights its critical role in diverse industries.
The next section will delve into the specific types of mullers used for different applications.
Conclusion
This exploration of a muller reveals its multifaceted role in various industries. From its fundamental function in particle size reduction to its contribution to material homogenization, the muller demonstrates remarkable versatility. The article highlights the crucial link between a muller's consistent action and the achievement of uniform material properties. Key applications span diverse sectors, including ceramics, pigments, pharmaceuticals, and mineral processing, underscoring the tool's enduring relevance in modern manufacturing. The controlled nature of the process, from initial material preparation to final product output, underscores the muller's importance in optimizing efficiency and minimizing waste. This analysis emphasizes the profound impact of precise particle size reduction, achieved through a muller, on the quality and consistency of final products across a wide array of applications.
The historical and contemporary utility of the muller signifies its enduring importance. Its continued presence in various industrial processes speaks volumes about its effectiveness and adaptability. The ongoing evolution of muller technology and its integration into automated systems promises further enhancements in efficiency and precision. A comprehensive understanding of the muller, its operation, and its impact remains crucial for continued innovation and optimization within relevant industries.
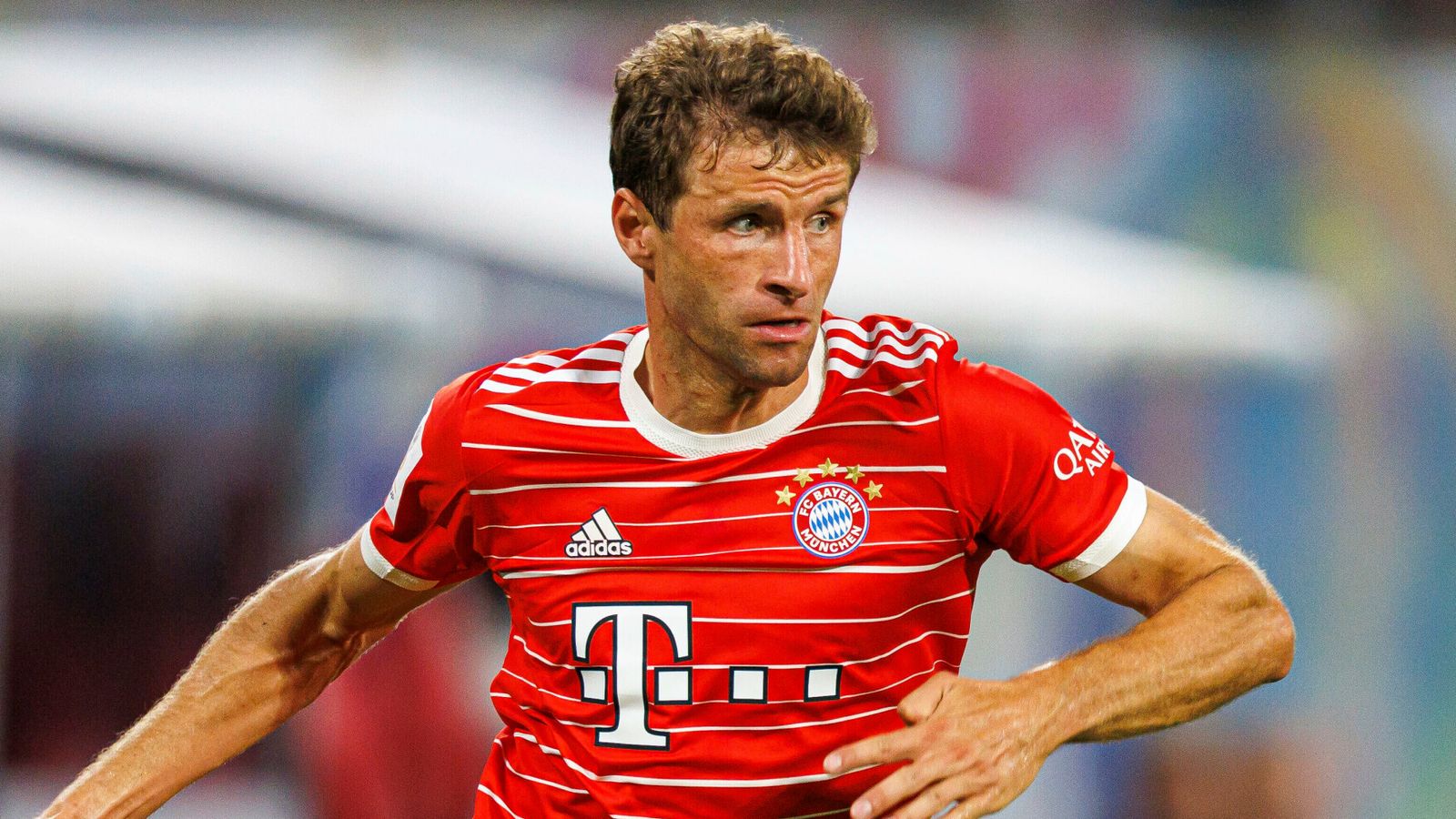

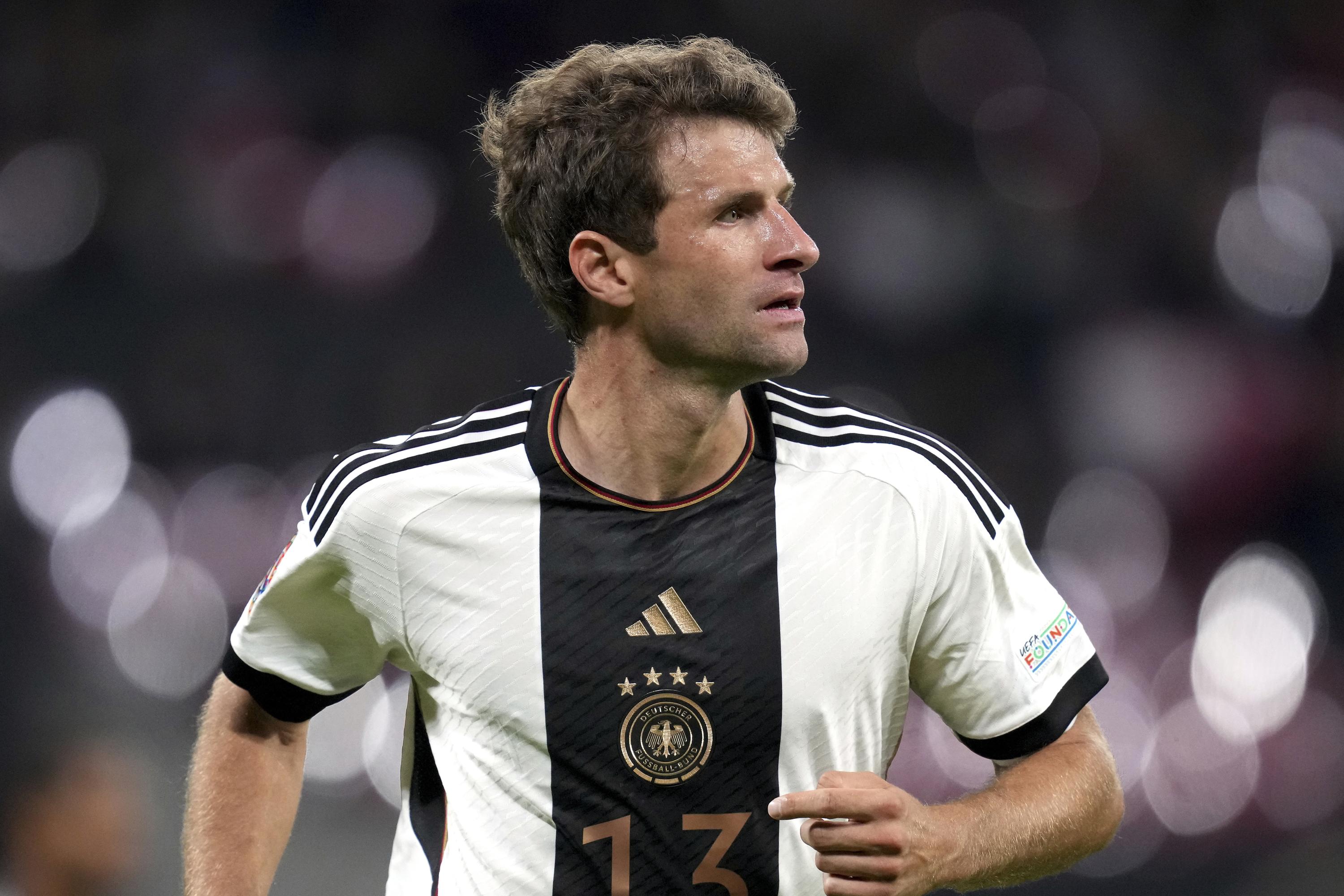