What are the key characteristics of this advanced aerodynamic design? This innovative approach to vehicle design offers superior performance and efficiency.
This advanced aerodynamic design emphasizes optimized airflow to minimize drag and maximize lift. It incorporates a suite of technologies, including meticulously sculpted body shapes and potentially advanced materials to achieve these goals. Examples include specific designs for automobiles, airplanes, or even high-performance cycling equipment. The focus is on creating a streamlined form that reduces air resistance, leading to improved speed, fuel efficiency, and overall performance.
The importance of this approach lies in its ability to improve performance across a wide range of applications. For automobiles, it leads to higher speeds and better fuel economy. In aviation, it translates to increased range and efficiency, potentially lower operating costs, and reduced environmental impact. The history of aerodynamic design is rich, with continual refinement and innovation driven by the need for greater efficiency and speed in diverse fields. This concept is constantly evolving with advancements in materials science and computational fluid dynamics.
Now that we understand the principles of this sophisticated approach to design, let's explore its specific implementations in different industries.
Feam Aero
Understanding the essential elements of Feam Aero is crucial for comprehending its impact. This approach encompasses a multifaceted design philosophy emphasizing streamlined performance and efficient functionality.
- Aerodynamic Efficiency
- Streamlined Design
- Material Selection
- Performance Optimization
- Computational Modeling
- Reduced Drag
Feam Aero's core aspects interrelate to enhance performance. Aerodynamic efficiency, for example, relies heavily on a streamlined design and optimized material selection. Computational modeling plays a vital role in refining design parameters, allowing for the prediction and simulation of airflow, ultimately resulting in reduced drag. These facets contribute to increased speed and reduced energy consumption across various applications. Cars, aircraft, and cycling equipment are just a few examples of fields where this design principle proves crucial for optimizing performance.
1. Aerodynamic Efficiency
Aerodynamic efficiency is a fundamental component of "feam aero." It dictates the vehicle's ability to navigate through the air with minimal resistance. Optimized aerodynamic design reduces drag, a force opposing motion. This reduction translates directly to improved performance metrics, such as increased speed and fuel efficiency. For example, a streamlined vehicle shape, as exemplified in many racing cars and high-performance aircraft, reduces the air pressure differential between the front and rear surfaces. This reduced drag is directly measurable and demonstrably improves speed and reduces fuel consumption.
The importance of aerodynamic efficiency extends beyond mere performance gains. In various applications, reduced drag contributes to environmental sustainability. By lowering fuel consumption, vehicles with optimized aerodynamic profiles emit fewer pollutants. This is especially critical in the transportation sector, where the environmental impact of vehicles is a growing concern. Furthermore, this principle is not confined to transportation; its application is seen in sports equipment like bicycles and sailing yachts, highlighting the universality of this design concept in improving performance and efficiency across diverse contexts.
In conclusion, aerodynamic efficiency underpins the effectiveness of "feam aero." Its impact on performance, fuel consumption, and environmental sustainability is undeniable. Understanding the relationship between design and airflow is crucial for realizing optimal performance and environmental responsibility in numerous applications.
2. Streamlined Design
Streamlined design is a cornerstone of "feam aero," impacting performance through optimized airflow management. A streamlined shape minimizes resistance, enhancing speed and efficiency. This principle translates across various applications, from vehicles to sports equipment, where aerodynamic advantages are paramount. The following facets delineate how a streamlined shape influences "feam aero" characteristics.
- Reduced Drag Coefficient:
A well-designed streamlined form reduces the drag coefficient a measure of a body's resistance to movement through a fluid (like air). This reduction is achieved by shaping the object to minimize the turbulence and separation of airflow around it. Streamlined aircraft fuselages, for example, demonstrate this principle effectively. Lowering the drag coefficient directly translates to decreased energy expenditure and improved speed in "feam aero" applications.
- Enhanced Lift and Stability:
Streamlining can enhance lift and stability, especially important in applications like aircraft and high-speed vehicles. The shape of a streamlined body affects how air flows around it, creating localized pressure differentials. By manipulating these pressures, aerodynamic forces lift and stabilize the object in flight or motion. This effect is critical for maintaining a desired trajectory and speed in "feam aero" scenarios.
- Minimized Airflow Disturbances:
Streamlined design minimizes air turbulence by smoothly guiding airflow around the object. Sharp edges or abrupt changes in contour create turbulence, increasing drag. A smooth, continuous curve reduces these disturbances, improving efficiency. This characteristic is central to "feam aero," ensuring smooth transitions and minimal energy loss during movement.
- Material Optimization:
While primarily a shape-based concern, the choice of materials is directly connected to streamlined design. Lightweight materials, or materials with specific characteristics facilitating smooth airflow, can augment the streamlining effect. Applications like bicycles highlight this connection: lightweight, aerodynamically-suited frames contribute to performance gains aligned with "feam aero" principles.
In conclusion, streamlined design is intrinsically linked to "feam aero" by its ability to optimize airflow around an object. The facets outlined above reduced drag, enhanced lift, minimized turbulence, and strategic material selection contribute to the core efficiency and performance advantages embedded in this design philosophy. The benefits of a streamlined approach manifest in improvements in speed, fuel efficiency, and stability in diverse applications.
3. Material Selection
Material selection is a critical component of "feam aero" design. The properties of materials directly influence an object's aerodynamic performance. Choosing materials with low density, high strength, and specific stiffness characteristics is crucial for minimizing weight while maintaining structural integrity. This optimization is paramount for reducing drag and maximizing speed and efficiency in various applications.
Consider an aircraft wing. The material used significantly affects its aerodynamic characteristics. A lightweight yet strong composite material, for instance, allows the wing to achieve greater lift with less weight, enhancing fuel efficiency and range. Conversely, a heavier material would necessitate a larger wing surface area for the same lift, compromising performance. Similarly, in automotive design, the choice between aluminum alloys, carbon fiber composites, or high-strength steel significantly impacts fuel economy, acceleration, and overall performance, reflecting a direct connection between material properties and the "feam aero" principle. In high-performance bicycles, lightweight but stiff materials like carbon fiber are employed to reduce the overall weight of the frame without compromising structural integrity. This translates to superior handling, reduced energy expenditure, and enhanced speed. Such selections directly contribute to the performance gains underpinning the "feam aero" concept.
The optimal material selection for "feam aero" designs depends on the specific application and performance requirements. Careful consideration of factors like density, stiffness, and thermal properties is essential. Moreover, material selection must consider cost-effectiveness, availability, and maintainability throughout the design and production process. This multifaceted approach ensures practicality and efficiency in the application of "feam aero" across diverse fields. Understanding these relationships provides a crucial framework for designing objects that not only meet performance requirements but also achieve optimal efficiency and functionality, which are central tenets of the "feam aero" philosophy.
4. Performance Optimization
Performance optimization is inextricably linked to "feam aero." It represents the systematic process of enhancing the efficiency and effectiveness of a design, leveraging the principles of "feam aero" to achieve superior results. The crucial connection lies in the direct correlation between optimized aerodynamic design and enhanced performance. Improved aerodynamics reduce drag, thereby increasing speed and lowering energy consumption. This reduction in drag results in a more efficient system, leading to gains in output and reduced resource expenditure.
Consider a racing car. Optimized aerodynamic components, including spoilers, diffusers, and underbody tunnels, are meticulously designed to minimize air resistance. This translates directly to increased speed and acceleration, essential aspects of performance optimization. Similarly, in aircraft design, efficient wing shapes and optimized control surfaces reduce drag, allowing for higher altitudes, longer ranges, and greater payloads. These tangible examples highlight how optimized aerodynamics drive improved performance by efficiently managing forces acting on a system. The precise integration of these elements underscores the critical role of performance optimization within the "feam aero" paradigm.
Understanding the interplay between "feam aero" and performance optimization has significant practical implications. For engineers and designers, it dictates a methodical approach to developing high-performing systems. By rigorously considering aerodynamic principles during the design phase, significant improvements in performance parameters are achievable. Optimization demands meticulous analysis of airflow patterns and the selection of materials with aerodynamic properties. This systematic approach allows designers to predict and mitigate drag, leading to increased speeds and enhanced operational efficiency. Ultimately, this understanding translates into tangible benefits, particularly in sectors demanding peak performance, like automotive racing, aviation, and high-performance sports equipment. Efficient implementation of these concepts is essential to improving designs and maintaining a competitive edge.
5. Computational Modeling
Computational modeling plays a critical role in "feam aero" design. Advanced computational tools simulate airflow and other aerodynamic phenomena, enabling engineers to predict performance characteristics and optimize designs before physical prototypes are built. This approach significantly reduces development time and cost while enhancing design efficacy. The meticulous analysis of airflow patterns and forces facilitates innovative solutions for achieving peak aerodynamic efficiency.
- Aerodynamic Force Prediction
Computational modeling accurately predicts aerodynamic forces acting on a body. Sophisticated software utilizes mathematical equations to model fluid dynamics, enabling the assessment of lift, drag, and moment coefficients. This allows engineers to understand how different design features impact these forces, enabling the iterative refinement of designs to minimize drag, optimize lift, and maintain stability at various velocities and angles of attack. Examples of this include simulating the airflow over aircraft wings or the airflow around car bodies to optimize performance.
- Flow Visualization and Analysis
Computational models visually depict airflow patterns around an object. This visualization allows for the identification of areas with high turbulence, drag, or other aerodynamic inefficiencies. Detailed examination of these flow patterns allows engineers to make targeted design adjustments, such as modifying surface shapes or adding aerodynamic elements, to enhance the efficiency of the design. This can be applied to the design of complex structures like airplane wings or high-speed train carriages to ensure streamlined airflow and optimized performance.
- Optimization of Design Parameters
Computational simulations permit the iterative optimization of various design parameters. Engineers can manipulate variables like shape, size, and material properties within the simulation environment. This process allows them to explore a wide range of options and identify the optimal configuration for desired aerodynamic performance. This iterative design process is crucial for achieving peak performance, minimizing weight, and maximizing efficiency, key characteristics of "feam aero." For example, the design of a Formula 1 car utilizes computational modeling to refine the shape of the car body and optimize the design of its aerodynamic elements.
- Predictive Analysis for Various Scenarios
Sophisticated computational models accurately predict performance across a range of conditions. This includes varying speeds, altitudes, angles of attack, and other operational parameters. Engineers can effectively simulate and analyze performance under diverse conditions, ensuring the design performs optimally across the entire operational envelope. This allows for robust design solutions that remain consistent and effective in a broader range of situations. This is particularly important in aircraft design, where the aircraft must operate in various atmospheric conditions and at different speeds and altitudes.
In conclusion, computational modeling is integral to "feam aero" design. By enabling the prediction of aerodynamic forces, the visualization of airflow, the optimization of design parameters, and the analysis across diverse scenarios, computational tools significantly accelerate the design process and lead to highly optimized and effective designs. This approach is vital for achieving the desired level of aerodynamic efficiency inherent in "feam aero" principles.
6. Reduced Drag
Reduced drag is a central tenet of "feam aero." Minimizing the resistance encountered by an object moving through a fluid (like air) is paramount to achieving superior performance and efficiency in diverse applications. This principle underpins the design philosophy of "feam aero" and plays a crucial role in optimizing speed, fuel efficiency, and overall performance characteristics.
- Streamlined Form Factor
A primary method of reducing drag involves creating a streamlined form. This shape minimizes turbulence by guiding airflow smoothly around the object. Examples range from the teardrop-shaped profile of a racing car to the smooth, aerodynamic contours of an airplane wing. The streamlined form factor directly reduces the surface area exposed to the oncoming airflow, minimizing friction and the creation of eddies that generate drag. The reduction in drag leads to increased speed and decreased energy consumption in applications involving movement through air.
- Optimized Surface Finish
The surface finish of an object significantly impacts its drag. A smooth, polished surface minimizes friction between the object and the airflow, thereby reducing the drag component. Advanced materials and techniques like specialized coatings are used to achieve exceptionally smooth surfaces in high-performance applications. A reduction in surface roughness and imperfections directly decreases the drag forces affecting the object, maximizing its performance and efficiency in motion through air.
- Minimized Turbulence
Minimizing turbulence in the airflow around an object is vital for reducing drag. Turbulence occurs when airflow becomes chaotic and unsteady. This creates eddies and vortices that increase the resistance to motion. "Feam aero" designs often incorporate specific elements, like spoilers or diffusers, to manage the flow and prevent the formation of these turbulent zones. These strategies directly decrease the overall drag experienced by the object, allowing for improved efficiency and speed through a controlled, smooth airflow.
- Material Selection for Density and Strength
Optimal material selection is essential for minimizing drag. Materials with low density but high strength allow for the creation of lightweight yet sturdy structures. Such materials reduce the overall weight of the object and minimize the drag force stemming from inertia. Examples include the use of advanced composite materials in aircraft and high-performance bicycles to achieve both lightness and structural strength, which are key considerations within the "feam aero" paradigm. The result is a more efficient object, leading to a reduction in energy expenditure and heightened performance.
In essence, the reduction of drag through meticulous design and selection of optimal materials is central to "feam aero." The core principles described contribute to a substantial improvement in performance and efficiency across diverse applications. By minimizing air resistance, "feam aero" designs allow for faster speeds, increased range, and reduced energy consumption, all contributing to improved performance outcomes and a focus on efficiency.
Frequently Asked Questions (FAQs) about "Feam Aero"
This section addresses common inquiries regarding "Feam Aero," clarifying key aspects and dispelling potential misconceptions. The following questions and answers provide a comprehensive overview of this design philosophy.
Question 1: What is "Feam Aero," and what are its core principles?
"Feam Aero" encompasses a comprehensive design approach emphasizing aerodynamic efficiency. Core principles include streamlined form factors, optimized material selection, and meticulous consideration of airflow dynamics to minimize drag and maximize performance. This results in increased speed, enhanced fuel efficiency, and reduced energy consumption across various applications.
Question 2: How does "Feam Aero" influence performance in different industries?
The impact of "Feam Aero" is evident in sectors demanding peak efficiency, including automotive design (higher speeds and fuel economy), aerospace (increased range and payload capacity), and sporting equipment (enhanced performance and reduced fatigue). In each, the focus is on optimizing performance through aerodynamic principles.
Question 3: What role does material selection play in achieving "Feam Aero" design goals?
Material choice directly impacts performance. Lightweight materials with high strength are preferred to reduce weight without compromising structural integrity. This directly contributes to minimizing drag, thereby increasing efficiency and performance.
Question 4: How do computational models contribute to "Feam Aero" design?
Computational fluid dynamics (CFD) simulations are essential for "Feam Aero" design. These models allow engineers to virtually analyze airflow around designs, identify drag-inducing characteristics, and optimize design features before physical prototypes are produced. This iterative process ensures maximum performance and efficiency.
Question 5: What are the environmental benefits associated with "Feam Aero" principles?
Improved fuel efficiency, a hallmark of "Feam Aero" designs, leads to reduced greenhouse gas emissions. This contributes to a more sustainable approach across industries reliant on energy consumption, reflecting the design philosophy's broader ecological implications.
In summary, "Feam Aero" is a comprehensive design philosophy focused on optimized aerodynamic performance. Its principles result in significant improvements across various applications, with the added benefit of reduced environmental impact. This strategic approach underscores the importance of streamlined designs for enhanced efficiency in the modern world.
This concludes the FAQ section. Further information and specific case studies regarding "Feam Aero" applications can be found in the subsequent sections.
Conclusion
The exploration of "feam aero" reveals a multifaceted design philosophy focused on optimizing aerodynamic performance. Key elements include streamlined form factors, meticulous material selection, and sophisticated computational modeling techniques. These aspects collectively contribute to reduced drag, enhanced efficiency, and improved performance across diverse applications, from automotive and aerospace engineering to sporting equipment design. The systematic approach to aerodynamic optimization allows for the prediction and mitigation of air resistance, resulting in significant gains in speed, fuel efficiency, and environmental sustainability.
The future of design will likely continue to rely on advanced aerodynamic principles like those encapsulated in "feam aero." Continuous advancements in materials science and computational modeling will further refine these techniques. Understanding and applying these principles will remain critical for achieving peak performance and efficiency, particularly in high-demand sectors where fuel conservation and optimized functionality are paramount. The integration of "feam aero" principles promises to shape future technologies, offering solutions for a more sustainable and efficient world.

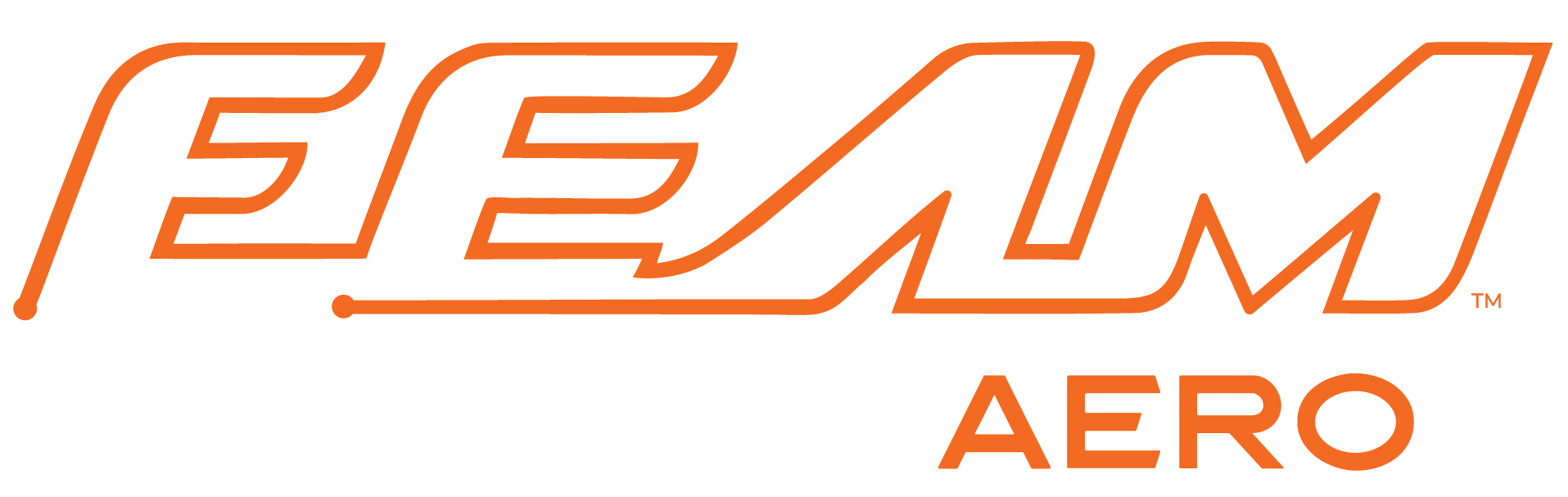
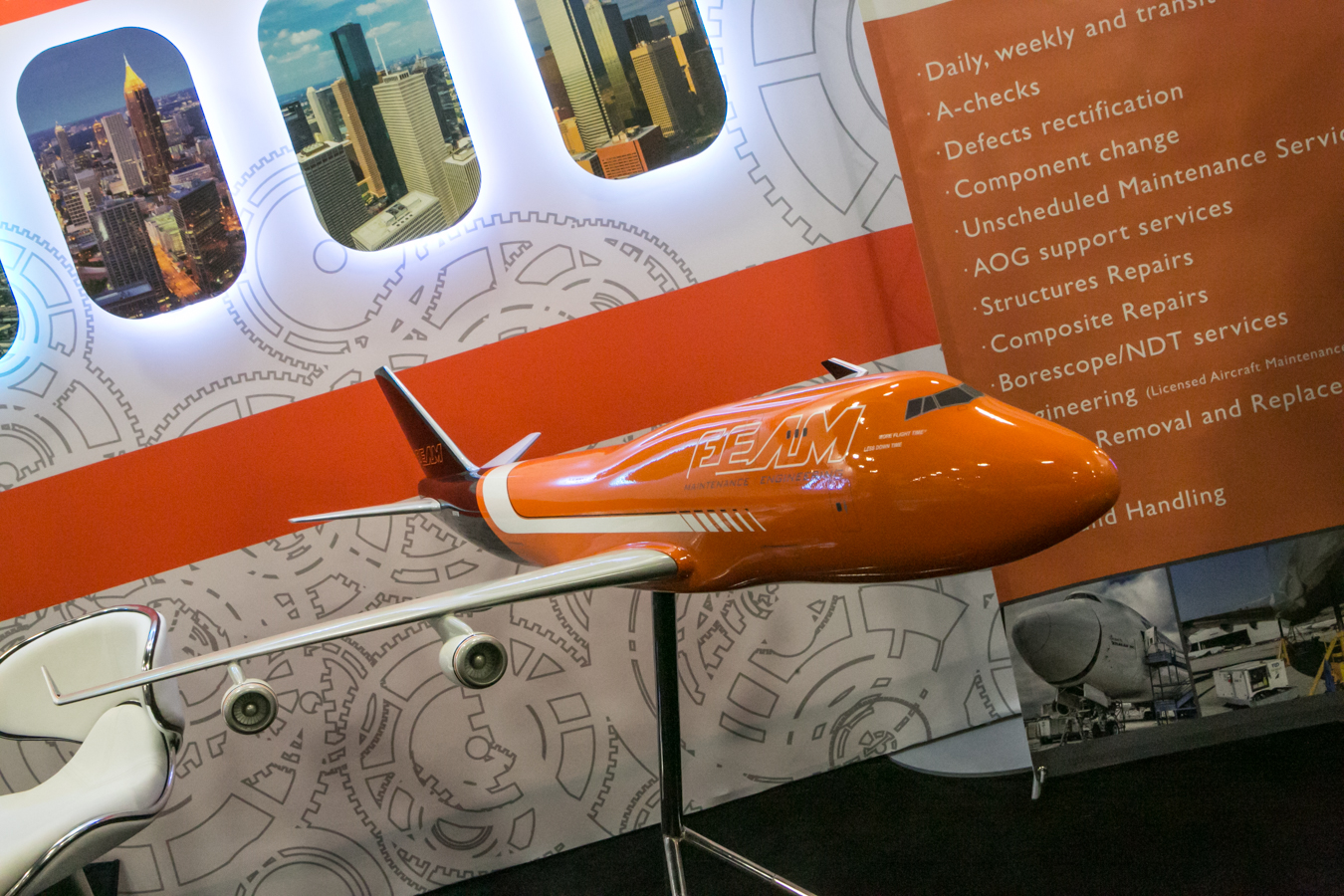