What is the significance of the production processes involved in the creation of certain specialized products?
This specialized manufacturing sector focuses on the creation of specific products, often with unique attributes and design requirements. The manufacturing process encompasses the entire spectrum of production, from material sourcing and component fabrication to final assembly and quality control. This approach ensures a consistent product outcome while also enabling customization where needed. A key aspect of this sector involves intricate design considerations, leading to a high degree of precision and quality in the final product. Many applications demand exceptional durability and reliability, highlighting the demanding nature of these manufacturing procedures. An example includes the production of high-precision components for aerospace or medical equipment. These rigorous processes guarantee quality products tailored to demanding standards.
The importance of this specialized manufacturing lies in its ability to produce goods of superior quality and reliability. This translates to enhanced performance, increased longevity, and reduced maintenance requirements for the end products. Historical context reveals that advances in this field have led to remarkable innovations in various sectors. The rigorous approach has implications for safety, efficiency, and overall product longevity across diverse applications. It fuels advancements in sectors such as medicine, transportation, and aerospace by providing critical, reliable components and systems.
Moving forward, let's explore the detailed processes and potential applications of this specific manufacturing approach in greater depth.
aalco manufacturing
A comprehensive understanding of aalco manufacturing necessitates a detailed examination of its fundamental elements. The process, crucial to product quality and reliability, encompasses meticulous design, stringent standards, and high-precision execution.
- Precision
- Quality control
- Specialized design
- Material selection
- Rigorous testing
- Efficiency
These aspects intertwine to ensure the production of high-quality, reliable products. Precision engineering, for example, is vital in ensuring components fit precisely, as seen in aerospace applications. Quality control measures, like rigorous testing protocols, guarantee product reliability, exemplified in medical device manufacturing. This approach, involving the careful selection of materials and meticulous adherence to standards, is central to delivering durable products suitable for demanding environments. The efficiency of the aalco manufacturing process is often driven by optimized workflows and advanced technologies, crucial for maintaining competitiveness. These aspects, when considered together, result in a seamless and effective manufacturing process, particularly relevant in specialized industries requiring exceptional product quality.
1. Precision
Precision is a fundamental aspect of aalco manufacturing. Accurate dimensions, precise tolerances, and meticulous execution are paramount. This exacting nature is crucial for the reliability, safety, and effectiveness of the final products. It translates into robust performance, lasting durability, and often, intricate functionalities.
- Dimensional Accuracy
Maintaining precise dimensions in components is essential. Deviations, even minute ones, can compromise functionality and overall performance. For instance, in aerospace components, precise measurements ensure proper fit and function within complex systems. This applies to medical devices, where accuracy in part size is critical for safe and effective use. The manufacturing process must meticulously control these dimensions to meet strict standards.
- Tolerances and Specifications
Strict tolerances and adherence to specifications are hallmarks of aalco manufacturing. This entails understanding and precisely meeting designated boundaries for component size and shape. This is vital for interchangeability of parts, for assembly, and for the reliability of complex mechanisms. The use of precise measuring tools and meticulous quality control procedures are essential for maintaining tolerances.
- Material Handling and Control
Precision also extends to material handling. Precise control over materials, their cutting, shaping, and assembly is crucial to achieve desired characteristics and dimensions. This includes careful material selection, minimizing waste, and employing precise cutting techniques to ensure accurate component shapes and sizes. Minimizing variation in the material properties is also critical.
- Quality Control Procedures
Rigorous quality control processes are inherent in aalco manufacturing. This involves regular inspection and testing of components and products against strict standards. Calibration of measuring instruments, trained personnel, and continuous monitoring of the manufacturing process are crucial. Advanced technologies, such as computerized measuring systems, are often incorporated for enhanced precision and efficiency.
In summary, the precision aspect of aalco manufacturing ensures that products meet exacting requirements. This meticulous approach impacts the entire spectrum of production, from material selection to final inspection. The result is a consistent, reliable, and high-quality product, crucial for industries where safety, performance, and durability are paramount. The combination of strict adherence to tolerances, refined processes, and advanced technology underpins the production of exceptional products.
2. Quality Control
Quality control (QC) is integral to aalco manufacturing. It establishes and maintains standards, ensuring product consistency and reliability. Effective QC procedures mitigate risks, minimize defects, and ultimately contribute to the production of high-quality, trustworthy products. This aspect is critical for maintaining a reputation for excellence and reliability within the industry.
- Inspection and Testing Procedures
Comprehensive inspection and testing protocols are fundamental to QC in aalco manufacturing. This includes visual inspections, dimensional measurements, and functional testing to identify any deviations from established specifications. Examples encompass precise measurements of components, rigorous functionality tests under simulated operating conditions, and verification of material properties against pre-defined parameters. Adherence to these procedures ensures that products meet required standards and minimize failures in the field.
- Statistical Process Control (SPC)
SPC methods monitor manufacturing processes, identify trends, and detect potential deviations from target parameters. This involves collecting data on critical process variables, charting this data, and establishing control limits. By analyzing data, trends in quality can be identified and deviations can be corrected proactively, resulting in consistent product quality. Examples include analyzing variations in raw material characteristics, testing consistency across multiple production runs, or charting the frequency of defects during assembly.
- Root Cause Analysis (RCA)
RCA is crucial for determining the underlying causes of defects or quality issues. By analyzing the factors contributing to deviations, manufacturers can implement corrective actions to eliminate the root cause and prevent future occurrences. This approach delves into the "why" behind defects, examining everything from material inconsistencies to equipment malfunctions or operator error. Using RCA can prevent repeating the same errors, significantly improving long-term product quality.
- Documentation and Record-Keeping
Accurate documentation and meticulous record-keeping are essential components of a robust QC system. Detailed records of inspection results, test data, and corrective actions provide a historical context for quality trends. This enables traceability, allows for informed decision-making regarding process improvements, and serves as a critical reference should issues arise in the future. Detailed records provide the evidence required to demonstrate compliance and justify quality improvements.
These facets of quality control, when seamlessly integrated within aalco manufacturing, establish a framework for consistent product quality, enhanced reliability, and a dependable reputation. By emphasizing these practices, aalco manufacturing fosters a commitment to delivering superior products while reducing risks and optimizing the overall process.
3. Specialized Design
Specialized design is intrinsically linked to aalco manufacturing. The nature of the products produced necessitates tailored designs that meet specific performance requirements and address unique challenges. This specialization demands a deep understanding of the intended application, materials, and manufacturing processes. The design phase is not merely about aesthetics; it's a critical determinant of the product's reliability, efficiency, and cost-effectiveness throughout its lifecycle. A robust design anticipates potential issues, optimizing the entire manufacturing process. For example, in aerospace components, a specialized design might incorporate lightweight materials, enhanced strength, and precision tolerances, directly influencing the manufacturing techniques and equipment needed. This emphasis on tailored design is essential for achieving a consistently high standard in aalco manufacturing.
The importance of specialized design in aalco manufacturing extends beyond simply meeting functional requirements. It proactively anticipates potential manufacturing challenges. By anticipating the need for specific material properties, assembly procedures, and testing methods during the design phase, aalco manufacturers can streamline the production process and minimize issues during actual manufacturing. A well-designed component requires less rework, fewer quality control interventions, and ultimately, a more cost-effective production run. In medical device manufacturing, intricate designs for implantable devices prioritize biocompatibility, sterility, and precise fit, all of which significantly impact the manufacturing process. Consider the detailed design specifications for a micro-surgical instrument, where the intricate design ensures not only functionality but also the necessary precision for its intended use. A deeper understanding of these design intricacies directly impacts the effectiveness and efficiency of aalco manufacturing operations.
In conclusion, specialized design is not a peripheral component of aalco manufacturing but a fundamental driver of its success. Well-conceived designs translate to streamlined production processes, reduced manufacturing costs, and improved product performance. This approach minimizes potential failures, enhances reliability, and positions aalco manufacturing for sustained success in specialized markets demanding precise and high-quality products. By integrating specialized design with a detailed understanding of materials, processes, and anticipated challenges, aalco manufacturing can create highly reliable and effective products, contributing to a stronger industry presence.
4. Material Selection
Material selection plays a critical role in aalco manufacturing. The characteristics of chosen materials directly influence the performance, reliability, and cost-effectiveness of the resultant products. Selecting appropriate materials is not merely a matter of choosing readily available options; it demands a meticulous evaluation of specific properties and suitability for a particular application. The chosen materials must be compatible with the manufacturing processes and meet rigorous quality standards.
- Mechanical Properties
Materials chosen for aalco manufacturing must possess specific mechanical properties, such as strength, stiffness, and ductility. These properties dictate the ability of the components to withstand stresses, maintain their shape, and function reliably. For instance, the selection of a high-strength alloy for an aerospace component ensures durability and resistance to extreme forces. Conversely, a component requiring flexibility may necessitate a different material like certain types of polymers. The choice is driven by the anticipated use and the resultant demands on the component.
- Chemical Resistance
Materials must resist degradation from exposure to chemicals, solvents, or corrosive environments. In applications involving exposure to harsh chemicals, materials with excellent chemical resistance are essential to maintain structural integrity and prevent material failures over time. Corrosion resistance is crucial for applications in marine environments or industrial settings. The specific chemical properties of the targeted environment determine the necessity and characteristics of the resistant material.
- Thermal Properties
Thermal properties, including thermal conductivity and expansion coefficients, are critical in applications involving temperature variations. Components operating in high-temperature environments require materials with high melting points and low thermal expansion. The selection of a material suitable for high temperature applications significantly affects the overall performance and longevity of the component. The use of specific materials impacts how components respond to temperature changes, influencing the product's operational lifespan.
- Cost and Availability
Material costs and availability also play a vital role in the selection process. An economical material with adequate performance can be a better choice than a superior but more expensive option. Supply chain factors, such as material scarcity or global sourcing, can impact decisions, affecting manufacturing timelines and potentially influencing overall production costs. The balance between material properties, cost-effectiveness, and availability is a key aspect in optimizing manufacturing efficiency.
In summary, material selection in aalco manufacturing demands a comprehensive evaluation of mechanical, chemical, and thermal properties, alongside economic considerations and availability. The suitability and precision of the chosen materials significantly impact the robustness, reliability, and overall performance of the final products. This demonstrates the pivotal role material selection plays in achieving the objectives of aalco manufacturing.
5. Rigorous Testing
Rigorous testing is not merely a step in aalco manufacturing; it's an integral component, crucial for achieving and ensuring product reliability and safety. The connection between rigorous testing and aalco manufacturing is fundamental. Testing procedures, meticulously designed and executed, verify that manufactured components meet stringent performance criteria, thereby guaranteeing functional integrity and safety. A robust testing regimen directly influences the entire production cycle, acting as a quality gate and a safeguard against defects that might emerge later in the product's lifecycle. Without rigorous testing, the risk of defective products entering the market is substantial, leading to potential harm, product liability issues, and reputational damage. This emphasizes the critical importance of a standardized testing procedure for each manufactured component, often with specific and demanding criteria, ensuring the components meet or exceed performance expectations.
Practical examples demonstrate the importance of rigorous testing. In aerospace manufacturing, the testing of critical components like engine parts or landing gear necessitates extreme conditions and sophisticated testing equipment to ensure they withstand intense pressures and vibrations. Similar scenarios exist in medical device manufacturing, where testing rigorously assesses biocompatibility and safety under various conditions. Testing verifies a devices ability to endure its intended lifespan, without compromising its essential qualities and safety. Moreover, this emphasis on testing during the production process has broader implications for industry standards, with manufacturers often having to adhere to strict regulatory requirements for safety certification. The rigorous testing approach not only assures end-user safety but also contributes to establishing a companys reputation for quality and reliability. Beyond the tangible benefits, meticulous testing fosters a culture of quality awareness within the manufacturing process.
In conclusion, the connection between rigorous testing and aalco manufacturing is one of direct causality. Rigorous testing is not a separate entity; it is an integral part of the manufacturing process. By meticulously verifying components against predefined criteria, aalco manufacturing ensures high-quality products that meet or exceed industry standards. This commitment to thorough testing minimizes risks, safeguards user safety, and fosters a culture of quality within the organization. This understanding of rigorous testing's role in aalco manufacturing directly translates to enhanced product reliability, reduced potential liabilities, and a stronger industry reputation. This ensures the production of products ready for the intended application, emphasizing the pivotal role of testing in ensuring product safety and reliability within the framework of aalco manufacturing.
6. Efficiency
Efficiency in aalco manufacturing is paramount. Optimizing processes, minimizing waste, and maximizing output are crucial for profitability and competitiveness within the industry. Efficient operations translate into reduced production costs, higher quality products, and improved responsiveness to market demands. The pursuit of efficiency in aalco manufacturing encompasses multiple interconnected facets, each contributing to overall operational excellence.
- Streamlined Production Processes
Streamlining production processes involves reorganizing workflows to eliminate bottlenecks and redundancies. This involves analyzing existing procedures, identifying areas for improvement, and implementing solutions such as redesigned layouts, optimized material handling, and standardized operating procedures. Examples include the use of automated systems for material transfer, robotic assembly lines for repetitive tasks, and the implementation of lean manufacturing principles to reduce waste and unnecessary steps. Improved efficiency in these processes directly reduces production time and enhances output without sacrificing quality, a critical aspect of aalco manufacturing.
- Optimized Resource Utilization
Maximizing the utilization of available resources, including raw materials, energy, and labor, is essential for operational efficiency. This involves meticulous inventory management to prevent stockouts and minimize waste, energy-efficient machinery to reduce operational costs, and training and development programs to improve employee skills and productivity. Examples range from using digital tools for precise material ordering to implementing energy-saving technologies in production equipment. Optimal resource management in aalco manufacturing ensures sustainable operations and cost control.
- Minimized Waste and Scrap Reduction
Minimizing waste and reducing scrap generation directly impacts efficiency in aalco manufacturing. This includes employing techniques like waste reduction and recycling programs to maximize the usage of resources. Reducing defects during the manufacturing process through improved quality control mechanisms, implementing preventative maintenance schedules, and optimizing material selection are also important. These practices minimize the need for rework and scrap disposal, improving efficiency and resource allocation within the entire production process.
- Leveraging Technology and Automation
Leveraging technology and automation is a key driver of efficiency in modern aalco manufacturing. This includes adopting digital manufacturing technologies, computer-aided design (CAD), and advanced control systems to automate processes, gather data, and analyze performance. Examples include automated material handling systems, robotic arms for intricate assembly tasks, and the use of sensors to monitor and adjust machinery performance in real time. Automation in aalco manufacturing leads to higher output, reduced error rates, and improved overall production efficiency.
In conclusion, achieving efficiency in aalco manufacturing is a multifaceted endeavor demanding optimization across various facets. By prioritizing streamlined processes, optimized resource allocation, reduced waste, and technological advancements, aalco manufacturers can enhance their competitiveness, reduce costs, and improve overall operational performance. This focus on efficiency fosters the creation of high-quality products while simultaneously ensuring sustainability and profitability within the industry.
Frequently Asked Questions (FAQs) about Specialized Manufacturing
This section addresses common inquiries regarding specialized manufacturing, particularly those relating to processes, quality standards, and industry trends. These questions are designed to provide clarity and accurate information.
Question 1: What distinguishes specialized manufacturing from general manufacturing?
Specialized manufacturing focuses on the production of specific, often complex, products requiring tailored design, materials, and processes. This contrasts with general manufacturing, which may encompass a wider range of products and processes. Key distinctions include the use of specialized equipment, highly trained personnel, and stringent quality control measures to meet precise specifications. The product types and manufacturing techniques often differ significantly.
Question 2: What are the key quality control measures employed in specialized manufacturing?
Quality control in specialized manufacturing incorporates rigorous inspection and testing procedures, ensuring products adhere to exacting specifications. This typically includes visual inspections, dimensional measurements, functional tests, and advanced techniques like statistical process control (SPC) to monitor process variations. Root cause analysis helps pinpoint and rectify issues, maintaining consistent quality.
Question 3: How does material selection impact the overall manufacturing process?
Material selection is critical. The chosen material's properties, including strength, durability, and compatibility with the manufacturing process, directly affect product quality, cost, and ultimately, the overall manufacturing efficiency. Specialized manufacturers carefully evaluate numerous factors, including chemical resistance, thermal stability, and cost-effectiveness, in the selection process.
Question 4: What role does technology play in modern specialized manufacturing?
Modern specialized manufacturing increasingly relies on advanced technologies like automation, computer-aided design (CAD), and sophisticated quality control systems. These technologies enhance efficiency, precision, and quality by automating repetitive tasks, optimizing processes, and providing real-time data analysis. Data-driven decision-making is becoming crucial to maintain a competitive edge.
Question 5: What are the common challenges faced in specialized manufacturing?
Specialized manufacturing faces unique challenges, including the high cost of specialized equipment, the need for highly skilled labor, sourcing unique or exotic materials, and stringent regulatory compliance. Finding skilled personnel and ensuring the supply chain for materials are often critical concerns. Meeting tight deadlines and ensuring product consistency within complex and specialized processes also present significant hurdles.
In summary, specialized manufacturing thrives on precision, quality, and a deep understanding of the specific product and application. Careful selection of materials, rigorous testing, and efficient processes are integral to achieving the desired output. Understanding these factors allows for a clearer comprehension of the intricacies involved in this specialized field.
Moving forward, let's explore specific applications of specialized manufacturing technologies and their impact on various industries.
Conclusion
This exploration of aalco manufacturing underscores the critical role of precision, quality control, specialized design, meticulous material selection, rigorous testing, and operational efficiency. These elements intertwine to create products of exceptional reliability and performance. The focus on these key aspects highlights the demanding nature of the industry and the importance of consistent adherence to stringent standards. The analysis reveals that aalco manufacturing is not simply a process; it is a commitment to excellence. The intricacies of design, materials, and testing methodologies contribute directly to product durability, safety, and functionality. These aspects are particularly crucial in specialized industries requiring robust and reliable components.
The future of aalco manufacturing likely involves continued technological advancements, further refining processes, and intensifying the focus on sustainability. Innovation in materials science, automation, and data analytics will likely drive further efficiencies and improvements in product quality. The consistent pursuit of these advancements will be crucial in maintaining aalco manufacturing's position as a key contributor to industries that rely on dependable and high-performing products. This sector's commitment to meticulous processes and a high standard of quality will likely continue to shape its trajectory for years to come.
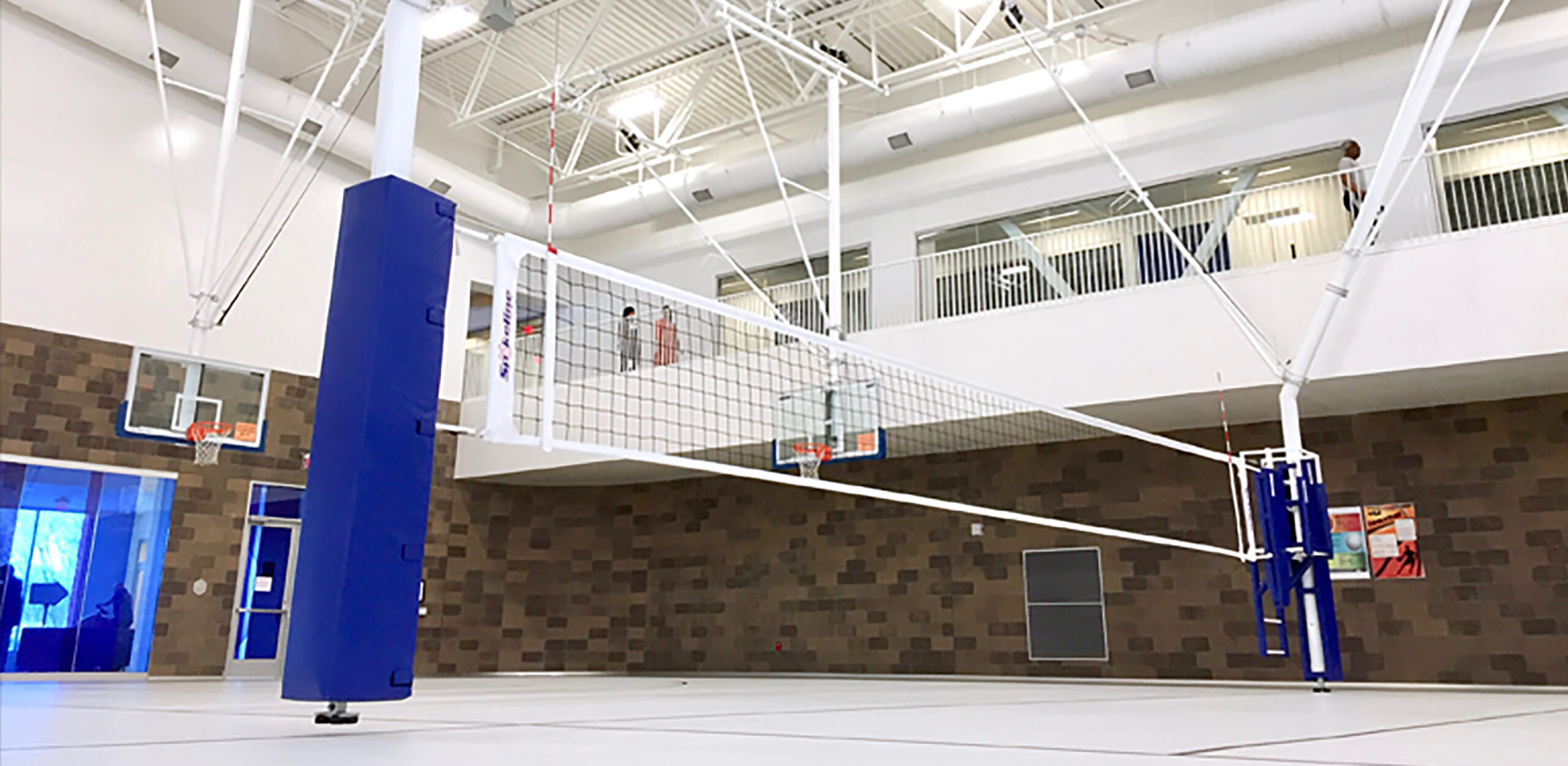
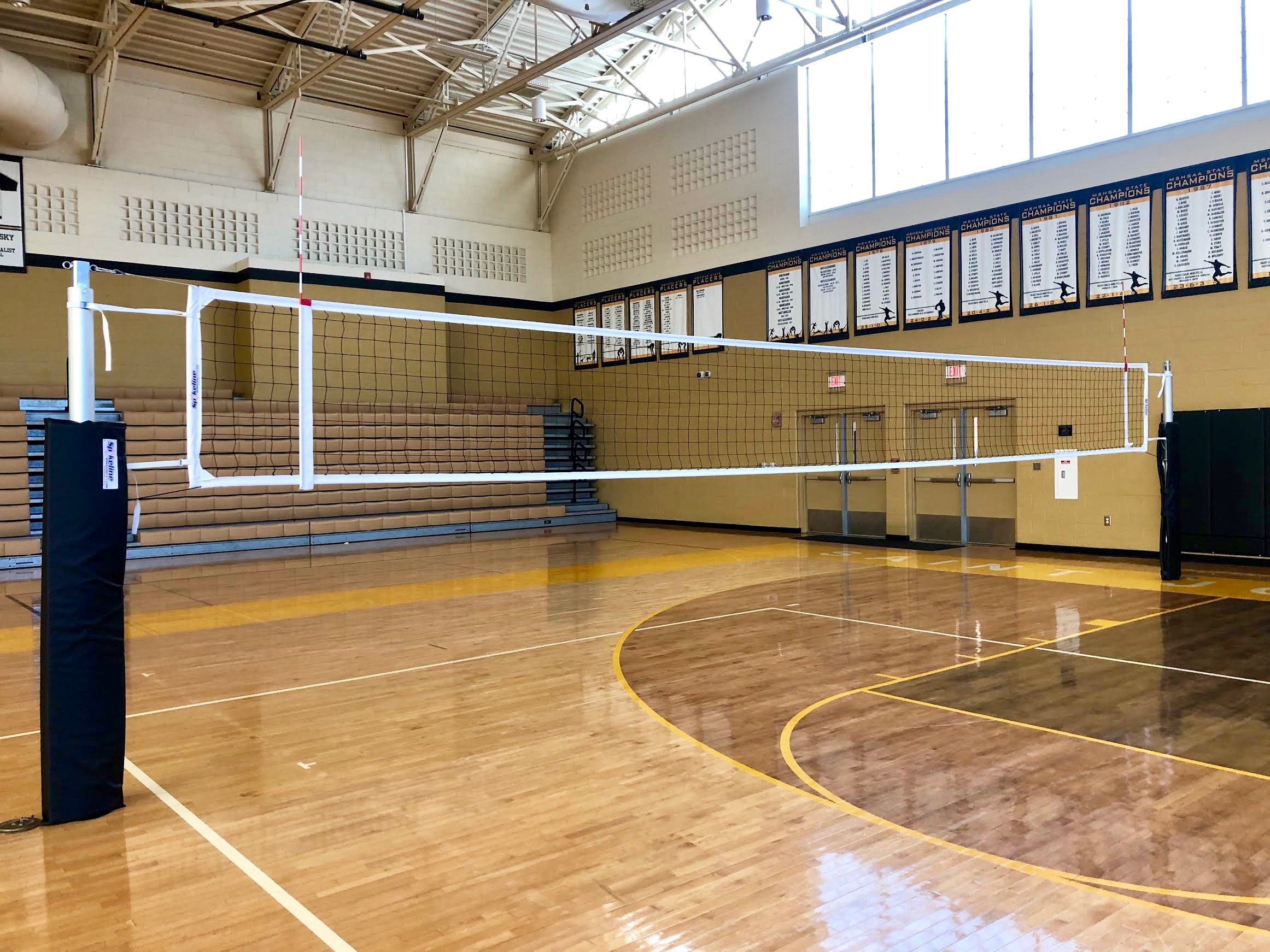
