What are the implications of fluctuations in certain semiconductor device characteristics? Understanding these variations is crucial for optimizing performance and reliability.
This phenomenon, often observed in certain types of semiconductor devices, describes the propagation of small, localized changes in device parameters. These changes can arise from variations in manufacturing processes, material properties, or operating conditions. For example, a slight imperfection in the substrate could result in a ripple effect that alters the conductivity of a transistor, potentially affecting its switching speed or power consumption. The impact of these ripples can range from subtle performance degradation to outright device failure, depending on the magnitude and location of the fluctuation.
Understanding and mitigating these fluctuations are paramount in the semiconductor industry. Precise control over manufacturing processes is essential to minimize variations, and advanced analytical techniques are deployed to model and predict the behavior of these ripples. Furthermore, these ripples are crucial in understanding and addressing issues in performance and reliability of semiconductor devices. This knowledge is critical for developing future integrated circuits with improved efficiency and reduced manufacturing costs. Historical context reveals that the development of advanced metrology and simulation techniques has been key to improving the understanding and control of these phenomena.
Moving forward, analyzing this phenomenon is a significant step in developing more reliable and efficient semiconductor devices. Further research in this area is focused on improving both theoretical models and experimental techniques to better characterize and control these micro-scale fluctuations.
CSD Ripple
Understanding CSD ripple is essential for optimizing semiconductor device performance. Accurate modeling and control of these fluctuations are crucial for achieving reliability and efficiency.
- Variations
- Fluctuations
- Propagation
- Characterization
- Control
- Modeling
- Reliability
- Efficiency
CSD ripple, a phenomenon observed in certain semiconductor devices, describes the propagation of small variations in key parameters. These variations arise from diverse sources, from material imperfections to manufacturing inconsistencies. Precise characterization and effective control of these ripples is paramount. Accurate models of the propagation allow for reliable predictions of performance and enable optimization strategies. Improved reliability and increased efficiency are direct consequences of controlling CSD ripple. For example, reducing fluctuations in transistor thresholds can lead to more consistent switching speeds. The insights from analyzing CSD ripple are also critical for the future development of advanced semiconductor devices.
1. Variations
Variations in semiconductor device characteristics are fundamental to the understanding of CSD ripple. These fluctuations, stemming from various sources, directly influence the behavior and performance of these devices. Examining the nature of these variations is crucial for developing effective control strategies and ultimately, reliable and efficient semiconductor technology.
- Material Heterogeneity
Variations in material composition and structure within the semiconductor material itself directly contribute to CSD ripple. Impurities, dislocations, and grain boundaries can create localized variations in electrical conductivity and other crucial parameters. These internal inconsistencies manifest as fluctuations in device characteristics, impacting device performance. For instance, differing dopant concentrations within the semiconductor substrate will lead to non-uniform current flow.
- Manufacturing Process Inconsistencies
Variations in the manufacturing process, such as variations in temperature, pressure, and deposition rates, introduce inconsistencies in the final device structure. Imprecision during fabrication can lead to non-uniform doping profiles, variations in gate oxide thickness, or differences in metallization layer properties. These process variations create inconsistencies that propagate through the device, contributing to CSD ripple. A slight variation in the etching time during the fabrication of the transistor channels, for example, could lead to uneven channel lengths and widths.
- Environmental Fluctuations
External factors like temperature and voltage fluctuations also cause variations in semiconductor device characteristics. These environmental conditions influence the device's internal parameters, leading to CSD ripple. Changes in temperature can affect the mobility of charge carriers, influencing the device's conductivity. Similarly, fluctuating voltages induce changes in the electric fields across the device, impacting its behavior. This emphasizes the sensitivity of the devices to their surrounding environment.
- Design Parameters
Variations in design parameters, from geometry to material choices, can significantly impact the observed CSD ripple. Variations in transistor channel dimensions, contact resistance, or gate oxide thickness can each lead to discernible fluctuations. Precise control and optimization of design parameters are essential to minimize these fluctuations and achieve desired performance.
Ultimately, these various sources of variation are interwoven and often interact to produce complex patterns of CSD ripple. Understanding the interplay between these diverse sources is critical for developing comprehensive strategies to mitigate these effects and ultimately enhance semiconductor device reliability and performance. Effective characterization and modeling of variations are thus crucial to controlling CSD ripple in integrated circuits.
2. Fluctuations
Fluctuations are inherent in the manufacturing and operation of semiconductor devices. These variations in key parameters directly influence the phenomenon known as CSD ripple. Understanding the nature and extent of these fluctuations is crucial for predicting and controlling the characteristics of semiconductor devices, ensuring consistent performance and reliability.
- Material Variations
Variations in the composition and structure of semiconductor materials are a primary source of fluctuations. Impurities, grain boundaries, and variations in doping concentrations introduce local inconsistencies in electrical properties. These micro-scale variations can ripple through the device, creating non-uniformities in conductivity, carrier mobility, and other critical parameters. For instance, slight differences in dopant concentration within a transistor's channel result in varying carrier densities along the channel, impacting its switching speed.
- Process Fluctuations
Manufacturing processes, inherently subject to variations in temperature, pressure, and other environmental factors, introduce inconsistencies in the fabricated device structure. Slight variations in deposition rates, etching times, or annealing parameters lead to fluctuations in crucial device dimensions, material thicknesses, and doping levels. These fluctuations accumulate and manifest as CSD ripple in the finished product, affecting performance and reliability. For example, non-uniform gate oxide thickness across a chip can result in varying threshold voltages of transistors, causing inconsistent circuit operation.
- Environmental Variations
Operating conditions, including temperature and voltage, can induce fluctuations in the characteristics of semiconductor devices. Changes in temperature influence carrier mobility and bandgap energies, affecting the device's conductivity and other crucial parameters. Similarly, fluctuations in voltage affect the electric fields within the device, leading to changes in current flow. These environmental variations manifest in the form of CSD ripple. For instance, temperature variations in an operating processor can lead to differing performance characteristics within different areas of the chip.
- Design Variations
Inherent imperfections in design parameters, including variations in device dimensions, layer thicknesses, and geometry, also lead to fluctuations in device characteristics. These imperfections, though often minimal, can significantly impact the overall device performance. For instance, slight variations in transistor channel lengths across a chip lead to diverse switching speeds and impact overall circuit performance. The cumulative impact of these variations is amplified and observable as CSD ripple.
In summary, fluctuations encompass a wide spectrum of factors, from material composition to manufacturing processes and operational conditions. Understanding these diverse sources of fluctuations is essential to effectively control CSD ripple, leading to predictable and reliable semiconductor devices.
3. Propagation
Propagation, in the context of CSD ripple, signifies the spreading or transmission of localized variations in semiconductor device parameters. These variations, often stemming from material or fabrication imperfections, manifest as fluctuations that propagate throughout the device structure. The propagation mechanism is complex, encompassing the influence of various physical phenomena, including charge transport, electrical field distribution, and carrier diffusion. Crucially, the nature and extent of this propagation directly affect the overall performance and reliability of the device. Understanding propagation pathways allows for the identification of critical points within the device where variations are most amplified, enabling targeted mitigation strategies.
The propagation of CSD ripple can be visualized as a chain reaction. A minute imperfection in one region of a semiconductor materiala slight deviation in doping concentration, for instancecan generate an electrical field gradient. This gradient then influences the transport of charge carriers, leading to variations in current density. These variations, in turn, affect the subsequent regions of the device, potentially amplifying the initial disturbance. Consider a MOSFET. A non-uniformity in the gate oxide layer could cause a ripple in the threshold voltage, influencing the current flow throughout the transistor. Predicting the scope of this ripple effect across the device, identifying vulnerable points, and developing countermeasures to limit propagation are key to robust device design. This propagation phenomenon is not merely a theoretical concern; it is a critical factor in understanding and controlling performance variations in real-world integrated circuits.
In essence, understanding propagation within the context of CSD ripple is crucial for effective semiconductor device design. Predicting and controlling the propagation of these variations enables the development of more reliable and efficient integrated circuits. This knowledge empowers engineers to identify and address vulnerabilities in design and fabrication, ultimately leading to increased yield, improved performance, and reduced manufacturing costs. However, the complexity of propagation pathways and the interplay of various factors influencing CSD ripple necessitates continuous research and development of advanced modeling and simulation techniques. This ongoing effort to characterize and control CSD ripple is fundamental to advancing semiconductor technology.
4. Characterization
Characterization plays a critical role in understanding and mitigating CSD ripple. Precise characterization of semiconductor devices is essential to identify, quantify, and model fluctuations in device parameters. This process is vital for predicting the behavior of CSD ripple under various operating conditions and for developing effective mitigation strategies. Without thorough characterization, predicting and controlling CSD ripple remains challenging.
- Material Analysis
Analyzing the material properties of the semiconductor substrate and other components is foundational to understanding the sources of CSD ripple. Techniques like electron microscopy, X-ray diffraction, and spectroscopic methods provide detailed information on material composition, defects, and structural variations. Identifying and quantifying these factors allows engineers to correlate material variations with the observed CSD ripple patterns. For instance, the presence of specific impurities in the silicon substrate can be directly linked to variations in transistor threshold voltages, a critical component of CSD ripple.
- Device Fabrication Process Analysis
Thorough examination of the fabrication process is crucial. Understanding variations in deposition rates, etching times, and other process parameters is vital. This process analysis can reveal the extent to which manufacturing imperfections contribute to CSD ripple. For example, if variations in gate oxide thickness are consistently measured, this indicates a potential source of CSD ripple and allows for process optimization.
- Electrical Parameter Measurement
Precise measurement of electrical parameters such as current-voltage characteristics, capacitance-voltage characteristics, and threshold voltages is essential. These measurements enable the identification and quantification of CSD ripple effects in specific device configurations. Data from these measurements are vital for building predictive models of the ripple propagation and for quantifying its impact on device operation. Careful calibration and repeatability are vital to obtaining accurate data, enabling the analysis of the ripple effect under various operating conditions.
- Statistical Modeling and Data Analysis
Statistical methods are vital to analyze the collected data and identify patterns in the fluctuations associated with CSD ripple. Techniques like statistical process control, correlation analysis, and regression modeling help isolate the influence of various factors on the device characteristics. By analyzing variations statistically, engineers can determine the relative significance of each contributing factor to CSD ripple and develop suitable mitigation strategies. For example, clustering algorithms might reveal distinct categories of devices exhibiting differing characteristics of CSD ripple.
In essence, characterization is a multifaceted endeavor that requires expertise in material science, device fabrication, and electrical measurement. The process is not just about measuring the presence of CSD ripple, but also about understanding its root causes. These insights, gleaned through rigorous characterization, are crucial for developing strategies to reduce CSD ripple, ultimately leading to more reliable and efficient semiconductor devices. This detailed understanding allows engineers to predict device behavior under varying conditions and ensures robust performance over time, contributing to a deeper understanding of the complexities involved in controlling fluctuations in semiconductor device parameters.
5. Control
Controlling CSD ripple is paramount to achieving reliable and predictable performance in semiconductor devices. Control encompasses the strategies and methodologies employed to minimize fluctuations in device characteristics, ultimately stemming from various sources such as material variations, manufacturing inconsistencies, and environmental changes. Effective control strategies directly address the root causes of these fluctuations, ensuring consistent performance across devices and mitigating the impact of CSD ripple on device reliability and yield. The goal is to create a more uniform and predictable response within the semiconductor, reducing the effects of variability.
Control strategies manifest in several key areas. Precise control over manufacturing processes is critical. Optimizing deposition techniques, refining doping profiles, and carefully controlling temperature and pressure during fabrication reduce the range of variability inherent in the manufacturing process. Material selection plays a vital role, as the homogeneity and purity of the materials directly correlate with reduced fluctuations. Design considerations are equally crucial, as effective design minimizes sensitivity to variations. Advanced design tools and simulation techniques aid in identifying and mitigating potential sources of ripple before manufacturing. Advanced metrology provides precise measurements during fabrication, enabling timely adjustments and process optimization. These control measures are not isolated interventions; they are integrated elements of a comprehensive approach to semiconductor fabrication and design. Real-world examples include the use of advanced metrology tools to monitor wafer thickness during deposition, enabling precise adjustments and reducing variability in the subsequent devices, thereby minimizing CSD ripple.
The practical significance of controlling CSD ripple is multifaceted. Reduced variability translates to higher yields in semiconductor manufacturing. More uniform device performance leads to improved circuit reliability and efficiency. Control strategies enable the creation of more predictable and consistent electronic systems. The impact extends beyond specific applications. Improved control over CSD ripple contributes to the ongoing advancement of semiconductor technology, enabling the development of more sophisticated and powerful integrated circuits, impacting everything from computing power to communication systems. However, challenges remain. Complicated interactions among various factors make comprehensive control a continuous pursuit. Advanced modeling and simulation techniques are vital for predicting and analyzing the ripple propagation paths and vulnerabilities. Continuous refinement of control methods and monitoring techniques is crucial to further optimizing semiconductor device manufacturing and design.
6. Modeling
Modeling plays a critical role in understanding and managing CSD ripple. Accurate models of semiconductor devices, encompassing their physical structure, material properties, and fabrication processes, are essential for predicting and mitigating the impact of CSD ripple. These models provide a framework for simulating device behavior under various conditions, enabling the identification of potential sources of variability and the evaluation of mitigation strategies. Simulations can reveal how material imperfections or fabrication inconsistencies propagate through the device, leading to fluctuations in key parameters like threshold voltage or current density. This predictive capability is crucial for optimizing design and manufacturing processes to minimize CSD ripple and ensure consistent performance across a wide range of operating conditions.
The complexity of CSD ripple necessitates advanced modeling techniques. Sophisticated simulations often involve computational fluid dynamics, electromagnetism, and statistical methods to accurately capture the interplay of different physical phenomena. These models can incorporate the statistical nature of manufacturing variations, allowing for the prediction of the probability distribution of device characteristics. Real-world examples include the use of finite element analysis to simulate the electric field distribution within a transistor, aiding in the identification of regions susceptible to CSD ripple. Similarly, Monte Carlo simulations can model the impact of random fluctuations in material properties on device performance. By accurately predicting device behavior under diverse conditions, these models enable more informed design decisions and optimization strategies to minimize CSD ripple, resulting in more dependable semiconductor components.
Accurate modeling is crucial for achieving reliable and efficient semiconductor devices. The ability to predict and understand the propagation of CSD ripple empowers engineers to proactively address potential issues and optimize design parameters. This predictive capability significantly reduces costly trial-and-error approaches in fabrication and design. By integrating detailed models into the design and manufacturing process, manufacturers can enhance the reliability and reproducibility of semiconductor components. Addressing the complexities of CSD ripple, through the development and refinement of accurate modeling techniques, is vital for future advancements in the semiconductor industry. Challenges remain in accurately capturing the complete interplay of physical mechanisms that contribute to CSD ripple, necessitating further research and development. Addressing these challenges will lead to more robust models and more dependable semiconductor products.
7. Reliability
Reliability, in the context of semiconductor devices, signifies the ability of a device to perform its intended function consistently under specified conditions over a given period. CSD ripple, characterized by fluctuations in device parameters, directly impacts this reliability. Understanding this connection is crucial for developing robust and predictable semiconductor technology. Variations in device behavior, stemming from CSD ripple, can lead to inconsistent performance and ultimately, system failure.
- Yield and Manufacturing Efficiency
Consistent device behavior, minimized by controlling CSD ripple, directly translates to higher manufacturing yields. Reduced variability in device parameters enables more predictable performance during production, increasing the proportion of functioning units and consequently, reducing costs. Fluctuations associated with CSD ripple can cause a significant portion of manufactured devices to fail testing, thereby diminishing yield rates. Consistent performance, achieved by minimizing CSD ripple, is thus essential for efficient production.
- Long-Term Stability and Performance Degradation
CSD ripple, if left uncontrolled, can accelerate performance degradation over time. Minor fluctuations in critical parameters, such as threshold voltage, can accumulate and lead to diminished device functionality. This gradual decline impacts the lifespan of the device and ultimately leads to failures that are less easily detected during initial testing. Controlling CSD ripple thus contributes to extending the operational lifespan of semiconductor devices. By reducing the inherent variability, the overall performance of a device will be more consistent and reliable in the long term.
- System Reliability and Predictability
The reliability of complex systems often hinges on the consistent performance of individual components, including semiconductor devices. CSD ripple-induced fluctuations in device parameters can propagate throughout the system, potentially causing unpredictable and cascading failures. Ensuring consistency and minimizing variations through controlling CSD ripple is essential for a system's overall reliability. Predictability in the system's response to various operating conditions is therefore dependent on dependable device characteristics, free of the fluctuations associated with uncontrolled CSD ripple.
- Cost Reduction and Increased Market Viability
Reliable devices are essential for reducing the overall cost of developing and deploying products. Implementing strategies to mitigate CSD ripple minimizes the need for extensive post-production testing and troubleshooting, reducing the overall cost of production and increasing the device's viability in the market. The reduced rates of defects and failures that result from effective mitigation strategies lead to higher manufacturing yields. This, in turn, ensures a more robust supply chain, contributes to a more profitable business model, and expands the devices' market potential.
In conclusion, controlling CSD ripple is critical for enhancing reliability in semiconductor devices. Robust methodologies to minimize and manage fluctuations contribute to improved manufacturing efficiency, extended lifespan, more predictable system behavior, and ultimately, reduced costs. These aspects all stem from the direct link between consistent device performance and a reliable, stable technological platform.
8. Efficiency
Efficiency in semiconductor devices is intrinsically linked to the phenomenon of CSD ripple. Fluctuations in device characteristics, stemming from CSD ripple, directly impact energy consumption and operational speed. Minimizing these fluctuations is crucial for maximizing efficiency. A device exhibiting consistent performance under varying conditions consumes less energy and operates at a higher speed, thus increasing overall efficiency. Conversely, uncontrolled CSD ripple can lead to significant energy waste, diminished processing speed, and reduced overall device efficiency.
Consider a microprocessor. Variations in transistor characteristics, a manifestation of CSD ripple, can lead to discrepancies in switching times and power consumption across different transistors within the chip. These inconsistencies can result in uneven energy demands, thus reducing the overall efficiency of the microprocessor. Similarly, in memory circuits, fluctuations in the charge storage capacity of memory cells due to CSD ripple directly impact read and write speeds and the energy required for these operations, ultimately impacting the overall efficiency of the memory system. These real-world examples highlight the practical significance of understanding the relationship between efficiency and CSD ripple. Strategies to mitigate CSD ripple are thus crucial for improving the energy efficiency of electronic devices and for designing more powerful, yet more energy-conscious, systems.
In essence, a deep understanding of CSD ripple is essential for optimizing semiconductor device efficiency. Minimizing these fluctuations through improved design, fabrication, and materials science allows for the creation of high-performance, energy-efficient components. This, in turn, has significant implications for the broader technological landscape, enabling advancements in diverse fields from computing and communication to energy conservation. However, challenges remain. The complex interplay of numerous factors contributing to CSD ripple continues to demand advanced modeling, simulation, and optimization techniques to ensure the development of truly efficient semiconductor devices. The pursuit of higher efficiency, in the context of CSD ripple, necessitates a multifaceted approach encompassing materials science, fabrication processes, and advanced device design.
Frequently Asked Questions about CSD Ripple
This section addresses common questions and concerns regarding CSD ripple, a phenomenon impacting semiconductor device characteristics. These questions provide a clear and concise overview of this complex topic.
Question 1: What is CSD ripple, and why is it important?
CSD ripple describes fluctuations in key parameters of certain semiconductor devices. These fluctuations arise from variations in material properties, manufacturing processes, and environmental conditions. Understanding and controlling CSD ripple is crucial for ensuring reliable and predictable device performance, optimizing energy consumption, and maximizing manufacturing yields. Uncontrolled CSD ripple can lead to performance degradation, reduced reliability, and increased manufacturing costs.
Question 2: What are the primary sources of CSD ripple?
Several factors contribute to CSD ripple. Material variations, including impurities, structural defects, and non-uniform doping, introduce inconsistencies in device behavior. Manufacturing process variations, such as inconsistencies in deposition rates, etching times, or temperature control, also contribute significantly. Furthermore, environmental fluctuations, including changes in temperature and voltage, induce changes in device parameters, thus contributing to CSD ripple.
Question 3: How does CSD ripple affect device reliability?
Uncontrolled CSD ripple can manifest as inconsistent performance and reduced reliability in semiconductor devices. Fluctuations in crucial parameters like threshold voltage and current density lead to variations in device behavior, resulting in lower yields during manufacturing and increased failures during device operation. This impacts long-term stability and can accelerate performance degradation. The variability in performance characteristics reduces overall system reliability.
Question 4: What are common strategies for mitigating CSD ripple?
Mitigation strategies focus on minimizing the sources of variability. Advanced control techniques in manufacturing processes, precise material selection and characterization, improved design optimization, and rigorous testing protocols help reduce fluctuations. Advanced modeling and simulation techniques also allow for early identification and mitigation of potential CSD ripple-related issues. These approaches are vital for optimizing device performance and ensuring reliability.
Question 5: What is the future outlook for managing CSD ripple?
Continued research and development in materials science, fabrication techniques, and advanced modeling methods are crucial for further managing CSD ripple. Improving process control and developing more robust device designs are key components in achieving consistent performance across varied operating conditions. The drive toward higher-performance, energy-efficient devices necessitates continued investigation and control of CSD ripple effects.
In summary, CSD ripple is a significant factor in semiconductor device performance and reliability. Addressing the underlying causes and implementing robust mitigation strategies are essential for realizing the full potential of semiconductor technology. Continued research and innovation in this area are crucial for future advancements in the field.
Next, we will delve into specific case studies demonstrating the impact of CSD ripple in various applications.
Conclusion
This exploration of CSD ripple highlights the multifaceted nature of fluctuations in semiconductor device characteristics. The phenomenon arises from a complex interplay of material variations, manufacturing inconsistencies, and environmental factors. Key findings underscore the importance of precise material characterization, meticulous fabrication control, and advanced modeling techniques in minimizing CSD ripple's detrimental effects. The analysis revealed that uncontrolled fluctuations can lead to significant performance degradation, reduced reliability, and increased manufacturing costs. The propagation of these localized variations throughout the device structure necessitates a comprehensive understanding of their influence on critical parameters like threshold voltage and current density.
Addressing CSD ripple is not merely a technical challenge; it is a crucial step in advancing semiconductor technology. The pursuit of higher-performance, energy-efficient devices hinges on mitigating CSD ripple's impact. Further research focused on developing innovative materials, optimizing fabrication processes, and refining simulation tools is essential. This ongoing effort promises to yield more reliable and predictable semiconductor components, driving advancements in various technological domains. Improved control over CSD ripple is essential for the continued development of advanced integrated circuits, enabling faster processing speeds, greater energy efficiency, and enhanced system reliability.
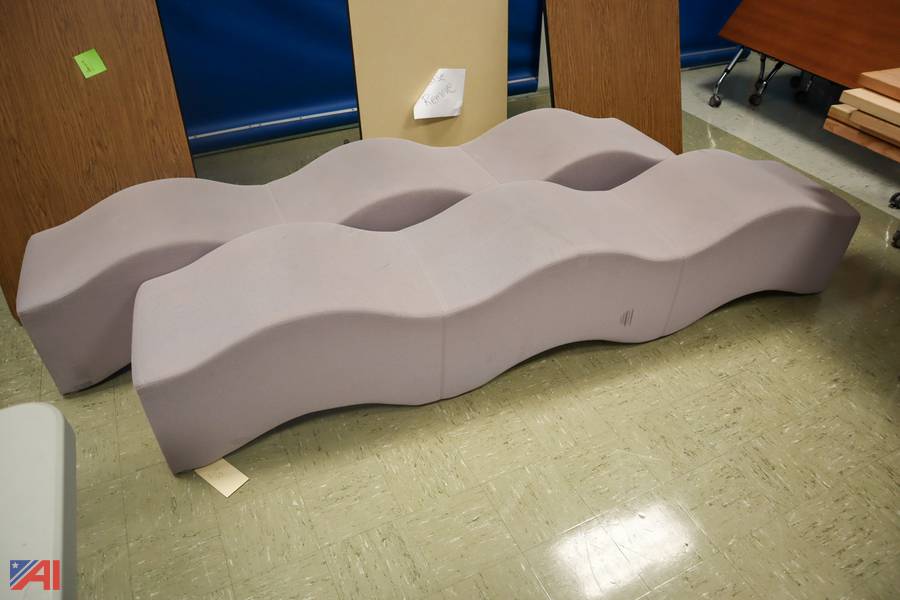
