What is the function of a specialized cutting instrument, and how does it impact various industries?
A specialized cutting tool, often employed in industrial settings, is designed for precise and efficient material separation. Its design incorporates specific features, such as blade geometry and material composition, which contribute to its effectiveness. This tool can be used for a wide range of tasks, from intricate shaping of complex materials to straightforward cutting of uniform shapes. Examples include specialized blades for intricate fabrics, precise metal cutting, or even very specific tasks in the food industry, such as certain types of meat processing.
This type of cutting tool offers numerous benefits. Efficiency gains often translate to cost reductions in production processes. Precision contributes to high-quality finished products. Safety features in the design can reduce operator risk. The use of specialized tools in industry has led to increased productivity and improved product quality. Historical context reveals an evolution from simpler, less-precise tools to modern, highly-specialized implements. This evolution reflects advancements in materials science, engineering, and manufacturing processes.
The following sections will explore specific instances and variations of this specialized cutting technology in more detail, examining their application and impact in diverse sectors.
Lise Cutter
Understanding the characteristics of a lise cuttera specialized cutting toolis crucial for appreciating its impact in various industrial applications. Its specific design features and functionality determine its effectiveness.
- Precision
- Efficiency
- Material compatibility
- Blade geometry
- Safety features
- Versatility
- Industrial applications
Precision and efficiency are paramount in a lise cutter. Material compatibility ensures optimal performance and avoids damage. Blade geometry directly affects the tool's ability to cut various materials. Safety features mitigate risks for operators. Versatility enables its use in diverse applications. Industrial applications range from food processing to metal fabrication, illustrating the tool's importance in specific industries. These aspects collectively define the effectiveness and suitability of the lise cutter in diverse industrial settings.
1. Precision
Precision is fundamental to the effectiveness of a specialized cutting tool. The design and construction of a lise cutter, a tool often used in industrial contexts, must prioritize precise blade geometry and material selection. Achieving precise cuts minimizes waste, improves product quality, and enhances efficiency in manufacturing processes. Variations in blade sharpness and angle directly correlate to the quality of the finished product. A slight deviation from the intended angle can result in inconsistent cuts, leading to material waste and rework. Accurate measurement of materials, ensuring proper alignment, and adherence to exacting tolerances are prerequisites for precise cutting.
Consider a scenario in a metal fabrication facility. Precise cuts are critical for creating intricate components, such as those used in machinery or automotive parts. Small discrepancies in blade accuracy can lead to malfunctions and costly repairs. In the food industry, precise cutting ensures consistent portion sizes and reduces food waste, optimizing both productivity and profitability. The pharmaceutical industry also relies heavily on precise cutting for consistent dosage amounts in pills and tablets. These diverse examples demonstrate how precision is not just a desirable feature but a necessity for many industrial applications and processes involving lise cutter tools.
In conclusion, precision in the design and operation of a lise cutter is essential for optimal performance and efficiency across diverse industries. Understanding the connection between precise measurements, precise cuts, and resultant product quality is fundamental to success in these sectors. Without a commitment to precision, the very function of the specialized tool is compromised. Consequently, operational efficiency and cost-effectiveness are significantly impacted. A holistic approach that values meticulous measurements and a focus on detailed design is crucial in maintaining consistent product quality and preventing costly operational errors.
2. Efficiency
Efficiency, a critical component of any specialized cutting tool, is directly tied to the performance of a lise cutter. Optimized efficiency translates to reduced production time, minimized material waste, and ultimately, increased profitability. A lise cutter's design, including blade geometry, material composition, and operational mechanisms, significantly influences its efficiency. Consideration for material propertiesthe lise cutter's ability to cut efficiently without compromising qualityis integral. Improved efficiency allows for the streamlined handling of higher volumes, a crucial factor in many manufacturing processes. Efficiency in a lise cutter is not merely a desired attribute; it's essential for productivity and cost-effectiveness.
Real-world examples demonstrate the practical significance of this connection. In food processing, a lise cutter designed for optimal efficiency ensures rapid and consistent portioning, minimizing waste and increasing output. Similarly, in the textile industry, efficient cutting tools like a lise cutter contribute to faster material preparation and reduced fabric scrap. In metal fabrication, an efficient lise cutter leads to faster part production, minimizing delays and ensuring timely delivery. The impact extends beyond immediate production, affecting supply chain logistics and overall market competitiveness. Effective use of a lise cutter directly correlates to a streamlined production process, leading to substantial cost reductions.
In conclusion, efficiency is not merely a desirable trait in a lise cutter but a defining characteristic. Maximizing the efficiency of the tool directly impacts productivity, reduces operational costs, and enhances the overall profitability of an operation. Understanding the interplay between design, material properties, and operational procedures is vital to ensure a lise cutter consistently achieves its intended purpose: optimized material separation. Any optimization in this area directly contributes to the overall efficiency and competitiveness of the process.
3. Material Compatibility
Material compatibility is a critical consideration when selecting and employing a lise cutter. The effectiveness and safety of the cutting process are directly influenced by the suitability of the tool's design and construction to the specific material being processed. Mismatched materials can lead to premature blade wear, inefficient cuts, or even safety hazards.
- Blade Material Selection
The material comprising the blade of a lise cutter must possess properties suitable for the intended material. For instance, a blade made of hardened steel might be optimal for cutting metals but unsuitable for delicate fabrics. The choice of blade material must align with the material's hardness, toughness, and potential for chemical reactions with the cutting tool. A poor choice in blade material can result in rapid dulling and reduced performance or even damage to the material being cut.
- Material Hardness and Structure
The hardness and structural integrity of the material being cut influence the required blade characteristics. Harder materials necessitate blades with increased strength and resilience to resist deformation during the cutting process. Conversely, softer materials may allow for the use of less robust blades. Understanding the material's inherent characteristics allows for proper selection of the optimal lise cutter design to achieve efficient and safe cutting.
- Chemical Compatibility
Chemical interactions between the blade and the material can significantly impact performance. Certain materials may cause corrosion or dulling of the blade, leading to premature tool failure or reduced cutting precision. Selecting a lise cutter and materials compatible in their chemical makeup is crucial to minimize these issues and maximize tool lifespan.
- Cutting Properties and Tool Efficiency
Compatibility factors impact the cutting properties of a lise cutter. For instance, a blade designed for specific material types might not produce optimal cuts when used for another. This leads to inefficiencies, higher energy consumption, and potentially increased costs. The right tool ensures clean cuts, reduced waste, and efficient material processing.
Ultimately, material compatibility in the context of a lise cutter is pivotal for achieving efficient, safe, and cost-effective cutting operations. Carefully considering the specific properties of both the cutting tool and the material being processed allows manufacturers to maximize the tool's lifespan and ensure consistently high-quality results in various industrial applications.
4. Blade Geometry
Blade geometry plays a critical role in the performance of a lise cutter. The shape, angle, and dimensions of the blade directly impact the cutting process, influencing efficiency, precision, and the overall effectiveness of the tool. Understanding the nuances of blade geometry is essential for maximizing the lise cutter's capabilities across various materials and applications.
- Blade Profile and Cutting Edge
The profile of the bladeits shape along its lengthand the precise angle of the cutting edge determine the material's interaction with the blade. Different profiles are suited to diverse materials. For instance, a curved blade might be ideal for intricate curves, while a straight blade might be more effective for straight cuts. The sharpness and angle of the cutting edge directly influence the ease and smoothness of the cutting action. A sharp, precise edge minimizes friction and maximizes material separation, minimizing the risk of chipping or tearing.
- Blade Thickness and Material Composition
Blade thickness significantly affects the tool's ability to withstand pressure during cutting. Thicker blades provide greater strength and durability but may increase the resistance to cutting softer materials. The material composition of the blade is equally important. Different materials exhibit varying hardness, resistance to wear, and corrosion resistance, directly influencing the blade's lifespan and effectiveness across diverse materials. A high-carbon steel blade, for example, might be suitable for cutting metals, while a softer material might be preferable for fabrics or certain food products.
- Blade Angle and Cutting Force
The blade's angle of attackthe angle at which the blade encounters the materialdirectly impacts the cutting force required and the resulting quality of the cut. A carefully calibrated angle minimizes the force needed while maximizing the efficiency of the cut. Misaligned angles can lead to uneven cuts, increased friction, and potential damage to both the material and the blade. Optimization of this angle is paramount for achieving efficient and precise cutting operations.
- Blade Length and Width
The length and width of the blade affect the amount of material that can be cut in a single pass. Longer blades might be more efficient for extended cutting tasks, while narrower blades offer more precise control over intricate details. The balance between length and width must align with the specific material, task, and desired output. For instance, long, narrow blades can be ideal for fine detail work, while short, wide blades are more suitable for bulk material removal.
In summary, the interplay of blade profile, thickness, angle, and dimensions in a lise cutter directly influences its performance. Optimizing these geometric elements ensures precise, efficient, and safe cutting operations across various materials and applications. A comprehensive understanding of blade geometry allows manufacturers to design and utilize lise cutters tailored to specific tasks, maximizing both efficiency and output.
5. Safety Features
Safety features are integral components of a lise cutter, not merely add-ons. Their presence directly influences the safety of operators and the longevity of the tool itself. Proper design and implementation of safety features are crucial to prevent accidents, mitigate risks, and ensure the safe operation of cutting equipment. The design considerations for safety features in lise cutters should account for potential hazards associated with the cutting process, such as blade slippage, material ejection, and operator exposure to moving parts. Adequate protection against these hazards is essential for preventing injuries and maintaining a safe working environment.
Real-world examples demonstrate the practical significance of safety features. In metal fabrication, a lise cutter with a robust blade guard can prevent serious hand injuries from accidental contact with the sharp cutting edge. In food processing, safety interlocks that automatically shut off the machine when the guard is removed are crucial to prevent injuries from unexpected contact with moving parts. In the textile industry, the use of appropriately designed and well-maintained safety devices, like those designed for preventing entanglement and pinching hazards, are crucial to prevent injuries to personnel during operation. Properly integrated safety measures are essential for minimizing the risks involved in utilizing lise cutters, protecting workers, and contributing to the overall safety culture within industries utilizing this type of equipment.
In conclusion, safety features in lise cutters are not merely optional add-ons; they are essential components of a safe and effective tool. Comprehensive safety features are designed to mitigate risks associated with the operation of cutting equipment. Implementing and prioritizing safety in the design and operation of lise cutters safeguards personnel from potential injuries and ensures the long-term functionality of the tool. A proactive approach to safety fosters a safe work environment and reduces the likelihood of costly accidents. Proactive safety measures in cutting equipment directly correlate with improved productivity and a positive impact on overall operational efficiency.
6. Versatility
Versatility in a lise cutter refers to the tool's adaptability to various materials, tasks, and applications within diverse industries. The ability to switch between different materials or cutting configurations without significant modifications is critical for cost-effectiveness and operational efficiency. This adaptability is crucial for maximizing the tool's utility and minimizing downtime during production cycles.
- Material Adaptability
Lise cutters excel in versatility by being adaptable to different materials. This adaptability extends to varying thicknesses, densities, and compositions. The tool's design, specifically the blade material and geometry, allows for the efficient cutting of diverse substances. For example, a lise cutter equipped with a specific blade can smoothly cut through leather, but the same cutter with a different blade can be used for precise cuts in metal. This material adaptability is a key factor in its widespread industrial applications.
- Cutting Configuration Flexibility
The versatility of a lise cutter extends beyond material adaptability to encompass various cutting configurations. Its design often allows for adjustments to blade angles, cutting speeds, and cutting depths. This flexibility enables precision cuts for intricate designs and streamlined processing of bulk materials. Examples include adjustments in cutting angles to accommodate specific curves or varying material thicknesses. This adaptability ensures efficient use in diverse production processes, enabling rapid shifts in production demands.
- Application Specificity
The versatility of a lise cutter isn't just about the materials it can cut; it's also about the tasks it can perform. Specific modifications and attachments allow for the execution of specialized tasks, from intricate shaping to the creation of consistent product portions. Tools with these attachments are well-suited for complex operations, such as cutting parts in the automotive industry or creating precisely measured pieces in the food processing industry. This application-specific adaptability maximizes the tool's value for various operations.
- Maintenance and Upkeep Ease
The versatile design of a lise cutter sometimes translates into ease of maintenance and upkeep. Standard designs allow for simple blade changes, allowing for quicker transitions between different materials and tasks, limiting downtime. This simplicity in maintenance procedures contributes to reduced operational costs and increased productivity. This is especially beneficial for industrial settings needing rapid adjustments to production processes. The design often prioritizes straightforward blade replacement, reducing the time and expertise needed for upkeep.
In summary, the versatility of a lise cutter is a crucial factor contributing to its widespread use across industries. Its ability to adapt to diverse materials, cutting configurations, and specific applications makes it a valuable asset in various production environments. This adaptability translates to reduced costs, higher output, and enhanced efficiency, highlighting its critical role in modern production processes.
7. Industrial Applications
The lise cutter, a specialized cutting tool, finds significant application in diverse industrial sectors. Its effectiveness stems from a combination of precision, efficiency, and adaptability, all of which are crucial for optimized production. This section explores key industrial applications where lise cutters demonstrate their value.
- Food Processing
Lise cutters are indispensable in food processing for tasks requiring precise portioning and consistent product size. They're used for meat slicing, vegetable dicing, and intricate shaping of prepared foods, enhancing efficiency and reducing waste. The consistency this tool provides is critical for maintaining quality control and meeting consumer expectations. For instance, in poultry processing plants, lise cutters can quickly and accurately portion chicken pieces for various product lines, improving output and minimizing labor costs.
- Textile Manufacturing
In textile production, lise cutters are vital for precise fabric cutting. Complex patterns, intricate designs, and even large-scale cutting operations benefit from the accuracy and speed these tools offer. This precision minimizes fabric waste and maximizes the yield from raw materials, contributing to cost savings and sustainability. For example, cutting intricate designs for fashion garments or producing uniform widths for industrial textiles relies heavily on the precision of these specialized cutters.
- Metal Fabrication
Lise cutters excel in metal fabrication by ensuring precise cuts for components in various industries, including automotive, aerospace, and machinery. The precision afforded by these tools is critical for creating intricate parts and maintaining tight tolerances. This is particularly important for parts requiring precise measurements or intricate geometries, where deviations can lead to malfunctions and increased production costs. For example, cutting sheet metal into specific shapes for vehicle chassis parts demands high accuracy and precision provided by lise cutters.
- Packaging Industry
Lise cutters play a role in the packaging industry for the precise cutting of materials for boxes, wrappers, and labels. Consistency in dimensions and accuracy in cuts are vital for proper fitment and to avoid waste. This precision is essential in automating packaging lines, allowing for higher production rates and minimizing material loss. For instance, in carton production, consistent cutting ensures optimal packaging for products, reducing wasted material and maintaining product integrity.
Lise cutters, through their diverse applications, demonstrate a pivotal role in enhancing efficiency and precision in numerous industrial sectors. The ability to precisely cut diverse materials underpins their widespread adoption across various industrial settings, contributing to cost savings, increased output, and higher product quality. The multifaceted utility of lise cutters reflects their substantial impact on operational effectiveness and cost efficiency across several key industries.
Frequently Asked Questions about Lise Cutters
This section addresses common questions and concerns regarding lise cutters, a specialized cutting tool with applications in various industries. The information provided aims to clarify key aspects of their functionality, usage, and impact.
Question 1: What are the primary applications of lise cutters?
Lise cutters are utilized across diverse industries, notably in food processing (for precise portioning), textile manufacturing (for intricate fabric cutting), metal fabrication (for precise metal parts), and packaging (for consistent material cutting). Their versatility allows for adaptation to various materials and tasks.
Question 2: What factors influence the performance of a lise cutter?
Blade geometry, including profile, thickness, and angle, significantly impacts cutting efficiency and precision. Material compatibility between the blade material and the workpiece is crucial to prevent damage, premature blade wear, and inconsistent cuts. Operator skill and adherence to safety protocols also contribute significantly to the tool's effective and safe use.
Question 3: How does material compatibility affect lise cutter performance?
Mismatched material properties between the lise cutter blade and the workpiece can lead to poor cuts, accelerated blade wear, and potential damage to the workpiece. For example, a blade designed for metal might be unsuitable for fabric. Proper selection of blade material, considering the material's hardness, structure, and chemical properties, is essential for optimal performance.
Question 4: What safety measures are important when using lise cutters?
Implementing proper safety protocols, including the use of protective gear and adherence to manufacturer guidelines, is crucial. Ensuring the lise cutter's mechanical integrity and regular maintenance are critical. Adequate blade guarding and operator training are essential for mitigating potential risks and preventing accidents.
Question 5: How can lise cutter efficiency be improved?
Optimizing blade geometry, selecting appropriate blade materials, and maintaining the tool in optimal condition are crucial steps. The operator's proficiency in using the cutter, adherence to operational procedures, and maintaining a clean workspace also influence efficiency. Regular sharpening and replacement of blades as needed also contribute to long-term efficiency.
In conclusion, lise cutters offer diverse applications within various industrial sectors. Their effectiveness depends on careful consideration of material compatibility, safety protocols, and operational procedures. Optimizing the use of these specialized tools contributes significantly to enhanced productivity and product quality. Understanding these factors ensures safe and efficient operations using lise cutters.
The next section will explore case studies showcasing the practical implementation of lise cutters in specific industries.
Conclusion
This article explored the multifaceted nature of lise cutters, a specialized cutting tool with critical applications across various industries. Key aspects examined included precision and efficiency in material separation, emphasizing the importance of blade geometry and material compatibility for optimal performance. The exploration underscored the necessity of safety features, highlighting the crucial role of preventative measures in minimizing risks and maximizing operational safety. Further, the article showcased the versatility of the tool across diverse applications, from food processing to metal fabrication, showcasing its adaptability to specific material types and complex cutting tasks. The significance of lise cutters in improving efficiency, reducing waste, and ensuring precision in industrial settings was a central theme. The analysis of practical applications and frequently asked questions provided a comprehensive understanding of the tool's impact.
The implications of lise cutter technology extend beyond immediate productivity gains. The tool's ability to streamline processes and elevate precision in manufacturing settings has significant long-term implications for cost reduction and product quality. Further development and innovation in lise cutter design and application will likely continue to impact various sectors. Manufacturers and operators should prioritize understanding the technical intricacies of these specialized tools to achieve optimal results. Continued research and development within this area promise to drive further advancements in material separation technologies.
![Lise Cutter Detailed Biography with [ Photos Videos ]](https://alchetron.com/cdn/lise-cutter-bea44f97-d31b-40fb-b925-6c1e72ad556-resize-750.jpeg)
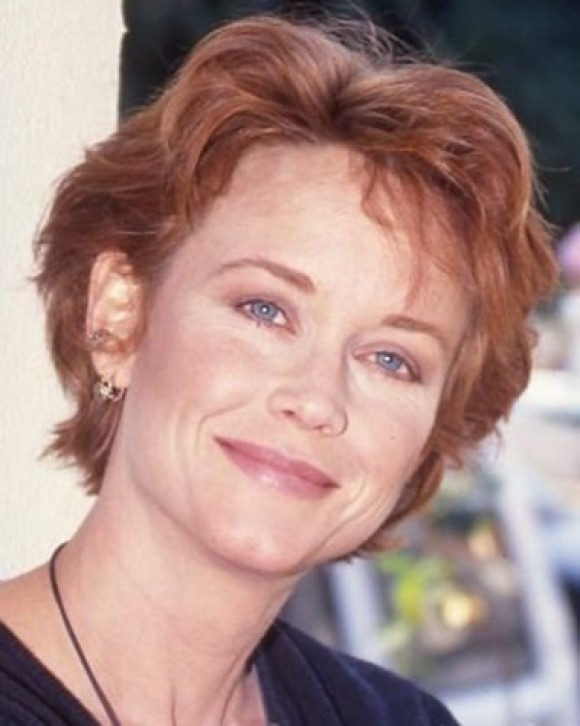
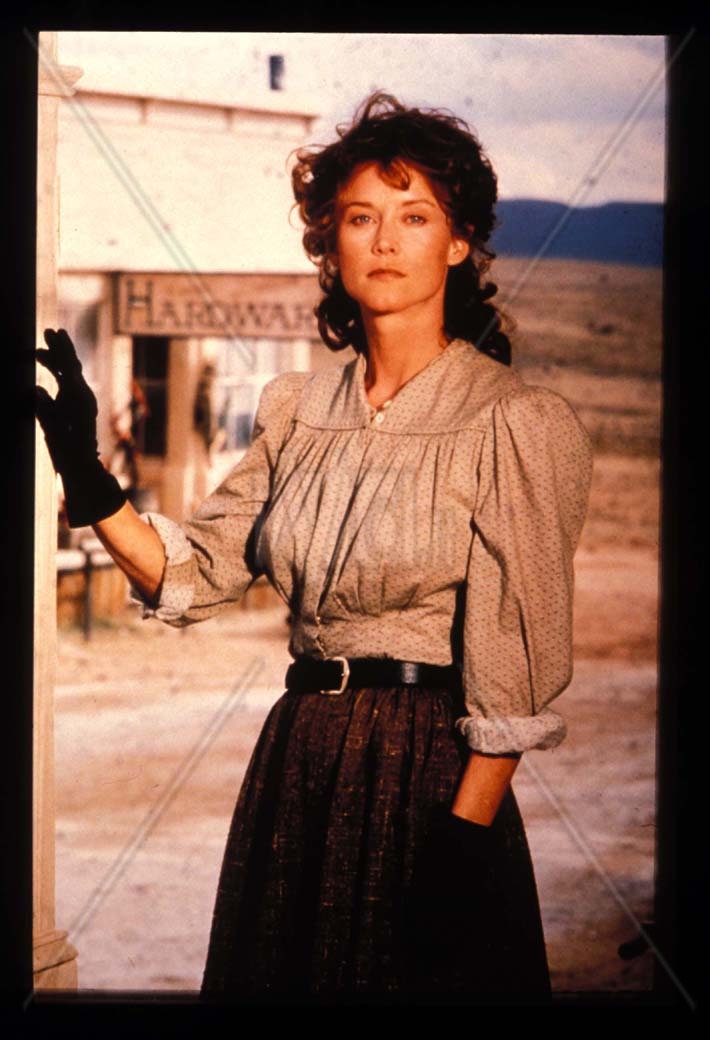