What is the purpose and impact of a centralized storage system for appliance components?
A centralized repository for appliance parts, organized and readily accessible, streamlines repair processes and ensures a consistent supply of components. This optimized system reduces downtime and enhances customer service. A robust system allows for efficient inventory management, order fulfillment, and streamlined logistics. Examples include a warehouse or online database meticulously cataloging spare parts for washing machines, refrigerators, or other household appliances.
Such a system offers numerous advantages. Reduced repair times translate into increased customer satisfaction and potentially higher profits. Accurate inventory management lowers storage costs and avoids stockouts, which in turn prevents disruptions in the supply chain. A robust and well-maintained centralized part storage system fosters efficiency across the entire appliance maintenance and repair network. This may involve specific technologies such as barcoding, RFID tagging, and integrated software for tracking and managing inventory effectively.
This discussion sets the stage for exploring the specific operational benefits and considerations associated with developing and maintaining a well-functioning system for the parts supply chain for appliances.
acstore
Centralized appliance component storage (acstore) is crucial for efficient repair operations. Effective management of parts ensures minimal downtime and customer satisfaction.
- Inventory management
- Logistics support
- Order fulfillment
- Reduced downtime
- Customer satisfaction
- Cost reduction
- Supply chain optimization
- Part tracking
Efficient inventory management, crucial for an effective acstore, streamlines parts ordering and delivery. Robust logistics support ensures timely delivery to repair centers. Order fulfillment is streamlined through a centralized system, reducing delays. Reduced downtime results in higher productivity and customer satisfaction, which is directly tied to a reliable acstore. Cost reduction is achieved through minimized stockouts and optimized storage. Supply chain optimization ensures consistent part availability, crucial for the entire system. Effective part tracking via technology ensures accurate inventory and efficient distribution. These aspects collectively build a robust acstore that significantly influences the entire appliance repair and supply chain.
1. Inventory Management
Effective inventory management is fundamental to the success of a centralized appliance parts storage system (acstore). Accurate tracking of available components directly impacts repair turnaround times. Insufficient stock of critical parts leads to prolonged customer wait times and lost revenue. Conversely, excessive stock ties up capital and storage space. A well-designed inventory management system within the acstore optimizes stock levels, preventing both shortages and overstocking. Real-world examples demonstrate that accurate forecasting, demand analysis, and agile response systems within an acstore are vital for maintaining a healthy balance of parts. This balanced approach ensures prompt repairs and prevents disruptions in the supply chain.
A robust inventory management system within an acstore demands meticulous data collection and analysis. Tracking historical repair data, seasonal trends, and appliance model-specific part demand is essential. Advanced technologies, such as barcoding, RFID tagging, and inventory management software, enhance accuracy and efficiency. Such tools enable real-time updates on stock levels, facilitating rapid replenishment and preventing potential delays. Further, the system must facilitate easy identification of parts, streamlining the ordering and allocation processes for repair technicians. This efficient system ensures technicians have the necessary parts on hand, reducing repair time and optimizing overall operational efficiency.
In conclusion, a robust inventory management system is not just a component of an acstore; it is the cornerstone. Accurate data, proactive forecasting, and advanced tracking tools are essential for maintaining optimal stock levels, reducing delays, and maximizing overall efficiency within the appliance repair network. Failure to prioritize inventory management within the acstore can significantly impact customer satisfaction, profitability, and the long-term sustainability of the entire operation. Thus, investment in comprehensive inventory management systems is essential for the success of any effective appliance parts storage system.
2. Logistics Support
Effective logistics support is integral to a successful appliance component storage system (acstore). Reliable and efficient movement of parts from the storage facility to repair centers is crucial for minimizing downtime and ensuring timely service. This includes factors like transportation, warehousing, and distribution channels.
- Transportation Efficiency
Optimized transportation methods, whether via trucking, air freight, or other options, directly affect the speed and cost of delivering parts. Route optimization and timely delivery scheduling minimize delays in part replenishment. Real-world examples include utilizing GPS tracking systems and selecting carriers with proven track records. This element is critical in meeting repair deadlines and maintaining a reliable service response, which strengthens the effectiveness of the acstore by ensuring prompt access to needed components.
- Warehouse Management
Efficient warehouse management within the acstore is essential. Inventory control systems, including proper storage methods and procedures, are key for preventing damage and ensuring quick retrieval of parts. Examples include employing sophisticated storage shelving to accommodate various part sizes and types. Proper warehouse management ensures parts remain accessible and in optimal condition. This contributes significantly to the acstore's ability to fulfill repair requests promptly, avoiding delays and inventory issues.
- Distribution Network Design
Strategic distribution network planning is vital. Locating warehouses strategically to reduce transit times, particularly in areas with high repair demand, is critical. Examples include using proximity analysis for distribution points to ensure repair centers are within a reasonable radius of storage facilities. This optimized network design ensures parts reach the appropriate service centers rapidly, fostering quick turnaround times for repairs.
- Supply Chain Visibility
Maintaining transparency and real-time visibility throughout the supply chain allows for efficient tracking of parts, from initial procurement to final delivery. Examples include leveraging technology for monitoring and tracking parts in transit. This visibility facilitates rapid response to potential supply chain disruptions. Improved supply chain visibility enhances the reliability of the acstore, ensuring that required components reach the point of repair promptly, enabling more efficient and predictable workflow.
In summary, logistics support forms a crucial element of a successful acstore. Effective planning and management across transportation, warehousing, distribution networks, and supply chain visibility contribute to minimizing delays and optimizing the overall appliance repair process. By streamlining these processes, the acstore ensures timely part availability, which in turn enhances operational efficiency, customer satisfaction, and overall profitability.
3. Order fulfillment
Order fulfillment, a critical component of a robust appliance parts storage system (acstore), directly impacts the efficiency and effectiveness of the entire repair process. Prompt and accurate fulfillment of orders for appliance components ensures timely repairs, minimizing customer inconvenience and maximizing operational efficiency. A seamless order fulfillment system within the acstore reduces repair delays by ensuring rapid access to the necessary parts.
The connection between order fulfillment and acstore is fundamental. A well-structured acstore, equipped with accurate inventory tracking and efficient logistics, enables swift fulfillment. Conversely, inadequacies in order fulfillment procedures within the acstore can lead to significant delays in repairs. Stockouts of crucial parts can cause prolonged downtime and frustration for customers, negatively impacting customer satisfaction and repair center productivity. Real-world examples illustrate that a reliable acstore, supported by a sophisticated order fulfillment system, fosters smooth repair operations. Delays in procuring parts from an inadequately managed acstore result in extended repair times, lost revenue opportunities, and reduced customer loyalty. Effective order fulfillment is crucial for the acstore to function as a centralized hub for parts, ensuring a seamless flow of components from storage to repair technicians.
In summary, order fulfillment is not simply a process within the acstore; it is an integral part of the system's overall performance. A well-functioning order fulfillment system directly contributes to the efficiency, profitability, and customer satisfaction associated with the entire appliance repair process. Challenges in this area, such as inaccurate inventory management or inefficient logistical processes, can lead to significant disruptions in the acstore's functionality. Therefore, investing in optimized order fulfillment procedures within the acstore is critical for maintaining a high level of service, and ultimately, success in the appliance repair industry.
4. Reduced Downtime
Minimizing downtime is a primary objective in appliance repair operations. A well-managed centralized appliance component storage system (acstore) plays a critical role in achieving this. Reduced downtime directly translates to increased productivity, higher customer satisfaction, and enhanced profitability.
- Rapid Part Availability
A well-stocked and organized acstore ensures prompt access to necessary components. This minimizes delays in procuring parts, enabling quicker diagnosis and repair. Quick part retrieval directly reduces the time a unit remains out of service. Efficient warehousing and inventory management within the acstore are critical for ensuring the required parts are readily available when needed.
- Minimized Search Time
The efficient organization of the acstore significantly reduces the time repair technicians spend locating specific parts. This organized structure streamlines the repair process, allowing technicians to spend less time searching and more time performing repairs. An optimized system, such as one incorporating barcode scanning or RFID technology, further enhances speed and efficiency. The reduction in search time directly correlates to a decrease in overall downtime.
- Preventive Measures against Stockouts
Proactive inventory management within the acstore helps avoid stockouts of critical components. This proactive approach minimizes the risk of repair delays due to a lack of necessary parts. Real-time inventory tracking allows for timely reordering, reducing the likelihood of shortages. The acstore acts as a buffer against unexpected demand fluctuations, ensuring reliable availability of parts and minimizing downtime due to stockouts.
- Optimized Repair Processes
A streamlined acstore allows for well-defined workflows and standardized procedures in accessing and utilizing parts. This consistency reduces variations and minimizes errors. Well-defined workflows ensure smooth and predictable access, reducing the potential for delays during the repair process. A comprehensive acstore system can integrate into a broader repair management system, fostering further optimization and minimizing downtime.
In conclusion, an effective acstore directly contributes to reduced downtime in appliance repair. By optimizing part availability, minimizing search time, preventing stockouts, and enhancing repair processes, the acstore significantly improves the operational efficiency and overall profitability of the repair network. The efficient management of parts directly translates into reduced customer wait times, greater technician productivity, and ultimately, a more successful and profitable appliance repair business.
5. Customer Satisfaction
Customer satisfaction is intrinsically linked to the performance of a centralized appliance component storage system (acstore). A well-managed acstore contributes to faster repairs, minimizing inconvenience for customers. Efficient component availability directly influences customer perception of service quality. Conversely, delays or unavailability of parts due to inadequacies within the acstore create negative experiences and erode satisfaction.
Real-world examples highlight this connection. A repair service with a readily accessible acstore, providing technicians with necessary components promptly, generally experiences higher customer satisfaction ratings. Conversely, a service hampered by frequent stockouts or logistical issues within the acstore often faces customer complaints about extended repair durations and inadequate service. This demonstrates the direct correlation between acstore effectiveness and customer contentment. Maintaining a comprehensive inventory, efficient logistics, and speedy order fulfillment procedures within the acstore directly contribute to positive customer experiences. This, in turn, cultivates loyalty and positive word-of-mouth referrals, crucial for the long-term success of any appliance repair business.
Understanding this connection is vital for businesses seeking to optimize appliance repair operations. Strategies to enhance customer satisfaction through acstore management include investing in advanced inventory management systems, prioritizing efficient logistics networks, and ensuring timely order fulfillment processes. A responsive acstore, equipped with readily available components and optimized workflows, results in pleased customers, fostering repeat business and a strong reputation. Conversely, neglecting acstore maintenance and optimization can lead to a decline in customer satisfaction, impacting the overall success and profitability of the business. This underlines the importance of prioritizing acstore efficiency for sustained customer satisfaction and business growth within the appliance repair sector.
6. Cost reduction
Cost reduction within a centralized appliance component storage system (acstore) is a crucial objective, directly impacting the profitability and sustainability of appliance repair operations. Optimizing processes within the acstore can lead to significant savings across various operational areas. Minimizing waste, streamlining workflows, and enhancing efficiency are key strategies for achieving cost reduction within this framework.
- Reduced Inventory Holding Costs
Maintaining optimal inventory levels within the acstore minimizes holding costs. Efficient demand forecasting and inventory management systems help prevent excessive stock accumulation, thereby reducing storage space requirements, insurance premiums, and the risk of obsolescence. Examples include implementing just-in-time inventory strategies and utilizing software for real-time inventory tracking. These measures directly lower the overall financial burden associated with maintaining an acstore.
- Minimized Stockouts and Backorders
Effective inventory management in the acstore reduces the frequency and impact of stockouts. This minimizes the costs associated with lost sales, rushed orders, and potential damage to customer relationships. Accurate forecasting, timely reordering, and proactive measures to anticipate potential demand fluctuations contribute to a more stable inventory, resulting in cost savings. Example scenarios include a decrease in emergency procurement costs and avoiding expedited shipping charges.
- Lowered Repair Turnaround Times
A well-organized acstore facilitates rapid part retrieval, consequently reducing repair turnaround times. This translates into lower labor costs per repair, as technicians spend less time searching for components. A streamlined process, leveraging technology like barcodes or RFID tags, reduces the time spent locating and verifying parts. This directly correlates to savings through more efficient use of technician time. Furthermore, reduced downtime for appliances awaiting repairs translates into reduced lost revenue.
- Optimized Procurement and Logistics
Streamlined procurement and logistics within the acstore lead to potential cost reductions. Negotiating favorable contracts with suppliers for consistent component delivery can result in lower material costs. Effective routing and transportation strategies minimize transportation expenses and delays. Optimizing these logistical aspects reduces the overall cost of procuring and distributing components within the acstore.
In summary, cost reduction in an acstore is not an isolated objective but a multifaceted outcome achievable through careful optimization of various operational aspects. Minimizing holding costs, preventing stockouts, accelerating repair times, and optimizing procurement directly contribute to a more financially viable and efficient appliance repair operation. Therefore, continuous refinement of the acstore processes remains a critical aspect of long-term financial success in this sector.
7. Supply Chain Optimization
A robust and efficient supply chain is indispensable for the optimal functioning of a centralized appliance component storage system (acstore). Optimization of this chain directly impacts the acstore's ability to provide timely and reliable access to parts. A streamlined flow of components, from procurement to delivery to repair centers, is paramount. Interruptions, delays, or bottlenecks in this process directly affect the acstore's performance and profitability.
Effective supply chain optimization within the acstore context requires meticulous planning and execution. Forecasting demand accurately for various appliance models and parts is critical. This necessitates analyzing historical repair data, anticipated seasonal variations, and potential market trends. Accurate forecasting allows for proactive procurement strategies, preventing stockouts and ensuring a consistent supply of necessary components. Efficient partnerships with suppliers are also crucial. These partnerships should guarantee reliable delivery schedules and competitive pricing, thereby minimizing procurement costs. Real-world examples include utilizing advanced analytics to predict future demand for specific refrigerator compressor models, enabling timely procurement and preventing stock shortages. Further, a well-designed supply chain maps the flow of parts throughout the process, from supplier to repair center, ensuring every step contributes to timely delivery. Efficient logistics management further enhances supply chain optimization by utilizing the most cost-effective and efficient transportation methods, considering factors like distance and volume. Optimized warehousing and inventory control systems within the acstore reduce storage costs and ensure easy access to parts. This ensures repair technicians can access required components swiftly, minimizing downtime and enhancing efficiency.
In summary, supply chain optimization is an essential component of a successful acstore. A well-optimized system facilitates the consistent flow of appliance parts, reducing downtime and costs. This involves accurate forecasting, strategic supplier relationships, and efficient logistics management. By understanding and implementing these strategies, businesses can enhance their acstore's operational efficiency and ultimately achieve higher levels of customer satisfaction and profitability. Failures in supply chain optimization within an acstore lead to inefficiencies, shortages, and costly delays, impacting both the repair process and the business's bottom line. This highlights the critical relationship between supply chain optimization and the success of a robust centralized appliance parts storage system.
8. Part Tracking
Effective part tracking is inextricably linked to the success of a centralized appliance component storage system (acstore). Precise identification and location of components are critical for efficient repair operations. Accurate tracking within the acstore ensures parts are readily available when needed, minimizing downtime and maximizing productivity. Without robust part tracking, the acstore becomes a disorganized collection of components, hindering repair efficiency and negatively impacting customer satisfaction. The ability to quickly and reliably locate specific parts is paramount to minimizing the time technicians spend searching. This directly translates into reduced repair times and greater cost-effectiveness.
Real-world examples underscore the importance of part tracking within an acstore. Consider a scenario where a repair technician requires a specific component for a washing machine. If the acstore lacks a robust tracking system, the technician might spend considerable time searching through an unorganized inventory. This delay leads to increased labor costs and dissatisfaction among customers. In contrast, a well-implemented part tracking system, potentially utilizing barcodes, RFID tags, or sophisticated software, allows for immediate identification and retrieval of the necessary part. This streamlined process dramatically reduces repair time and improves operational efficiency. Beyond these practical benefits, accurate part tracking facilitates better inventory management, allowing for proactive ordering and preventing stock shortages. Furthermore, detailed tracking data provides valuable insights into repair patterns, enabling the acstore to better anticipate demand and optimize stocking strategies.
In conclusion, part tracking is not merely an ancillary feature of an acstore; it's a foundational element. An efficient and accurate tracking system is essential for maintaining a well-organized acstore, enabling faster repair times, minimizing costs, and improving overall customer satisfaction. The ability to pinpoint specific components rapidly within the acstore directly contributes to the system's effectiveness. Implementing a robust part tracking system is crucial for the long-term success and profitability of any appliance repair operation, thereby highlighting the fundamental role of tracking in a functional acstore system.
Frequently Asked Questions about Centralized Appliance Component Storage (acstore)
This section addresses common inquiries regarding centralized appliance component storage systems. Understanding these answers clarifies the benefits, functionality, and practical applications of an acstore.
Question 1: What are the key benefits of implementing an acstore system?
Implementing a centralized appliance component storage system (acstore) offers several advantages. These include reduced repair times due to readily available parts, minimized downtime for appliances awaiting repairs, increased technician productivity, improved customer satisfaction, and potentially lower operational costs through optimized inventory management.
Question 2: What technologies support an effective acstore?
Several technologies enhance the effectiveness of an acstore. These include barcode scanning, RFID (radio-frequency identification) tagging, and sophisticated inventory management software. These technologies facilitate precise tracking of parts, real-time inventory updates, and automated ordering processes, ultimately improving the efficiency of the entire system.
Question 3: How does an acstore impact customer satisfaction?
A well-functioning acstore contributes directly to enhanced customer satisfaction. Faster repair turnaround times, fewer stockouts of critical parts, and reliable access to components directly result in a more positive customer experience. This leads to increased customer loyalty and positive brand perception.
Question 4: What are the potential costs associated with setting up an acstore?
Implementing an acstore system involves several potential costs. These include the initial investment in storage facilities, inventory management software, technology upgrades (e.g., barcode scanners), staff training, and potential logistical costs associated with the centralized distribution network. However, these costs often translate into reduced long-term operational costs due to increased efficiency.
Question 5: How does an acstore contribute to supply chain efficiency?
An optimized acstore contributes to a more robust and responsive supply chain. By centralizing component storage, businesses gain greater control over inventory levels and distribution. This, in turn, allows for more accurate forecasting, reduced lead times for part procurement, and minimized disruptions to the overall supply chain.
Understanding these FAQs provides a clearer picture of the multifaceted benefits and considerations associated with implementing a centralized appliance component storage system.
The following section will explore the specific operational procedures and best practices for managing an acstore.
Conclusion
This exploration of centralized appliance component storage (acstore) highlights its crucial role in optimizing appliance repair operations. Key aspects discussed include the benefits of efficient inventory management, optimized logistics, streamlined order fulfillment, and the reduction of downtime. The analysis underscores the direct correlation between a well-managed acstore and enhanced customer satisfaction, reduced operational costs, and improved overall supply chain efficiency. The importance of robust part tracking systems in supporting timely repairs and maintaining accurate inventory levels has also been emphasized. Furthermore, the strategic advantages of a centralized system in optimizing procurement processes and minimizing stockouts were examined.
The implementation of a meticulously designed and maintained acstore system offers substantial advantages for appliance repair businesses. While initial setup costs may exist, the long-term benefits, in terms of efficiency gains and enhanced profitability, can be considerable. Continuous optimization of the acstore system, incorporating feedback from repair operations and adapting to evolving customer needs, is essential for sustained success in the competitive appliance repair market. A thoughtfully constructed and well-maintained acstore not only ensures quick and efficient repairs but also serves as a cornerstone of a resilient and adaptable supply chain for the modern appliance industry.
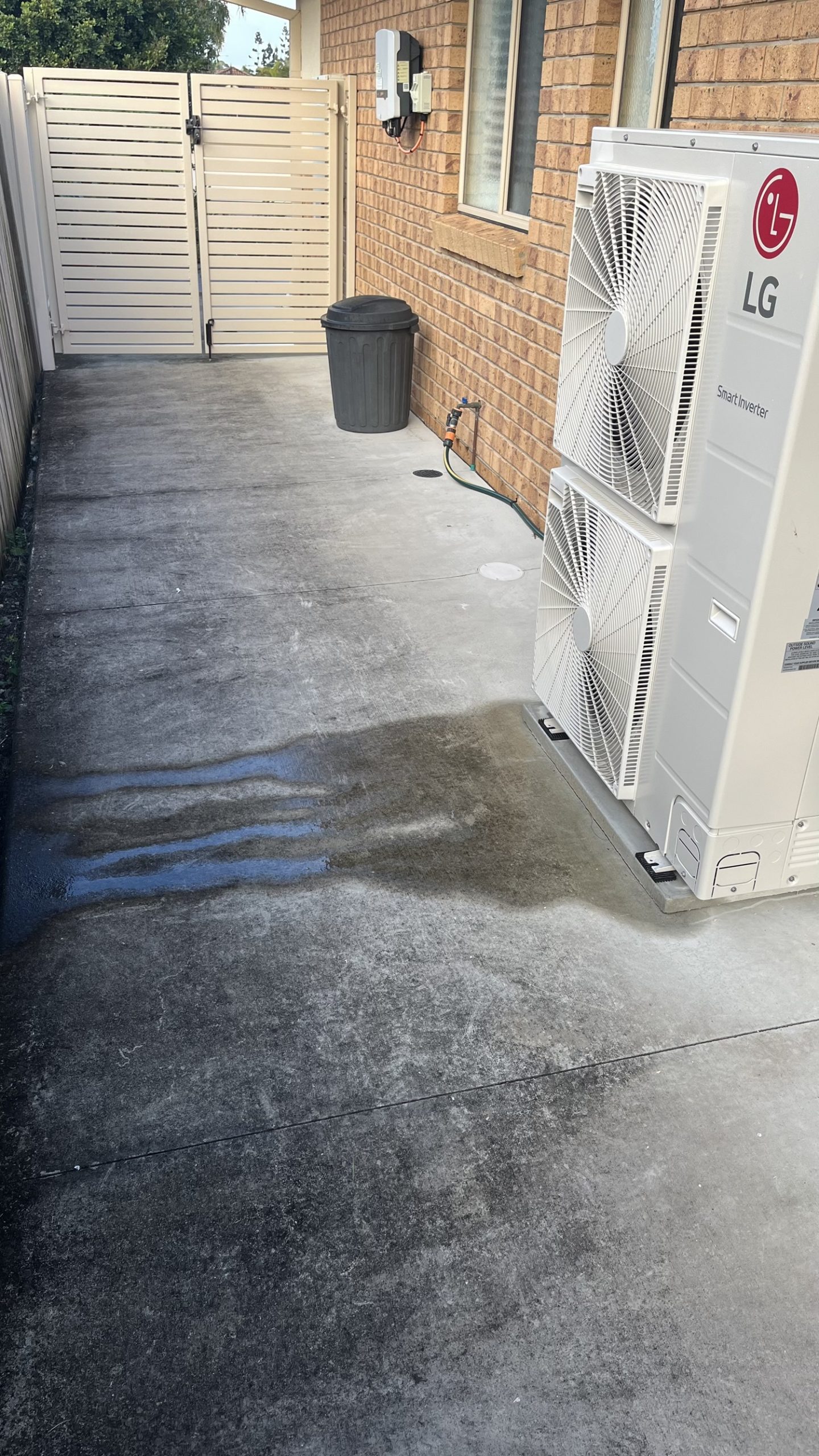