What sets this specialized welding apart and why is it crucial in modern fabrication?
High-strength, high-performance welding techniques, often employed in demanding industrial applications, represent a significant advancement in the field. These methodologies leverage specialized equipment and processes, ensuring the creation of exceptionally strong and durable welds. Examples include applications involving critical infrastructure components, aerospace components, and heavy-duty machinery, where reliability and robustness are paramount.
The importance of these welding approaches stems from the need for superior structural integrity. High-quality welds are essential in applications where failure can have significant consequences. This technology contributes to safety, efficiency, and longevity across various industries. The specific processes and materials used, often proprietary and demanding exacting control, directly impact the weld's overall characteristics. This results in a product with enhanced lifespan and resilience.
This detailed discussion will delve into the core principles and applications of these techniques. We will also explore the advanced equipment used in such specialized welding, offering a practical understanding of how it benefits diverse sectors.
Hercules Welding
This specialized welding process is crucial for applications requiring high strength and durability. Understanding its key aspects is essential for appreciating its value.
- High strength
- Precision control
- Advanced materials
- Complex designs
- Robust structures
- Critical infrastructure
These key aspects of Hercules Welding highlight its application in areas demanding exceptional performance. High strength welds are paramount in aerospace components or heavy machinery, demanding precise control over the welding process. Advanced materials like specialized alloys are often utilized, requiring complex designs to accommodate and further enhance the robustness of structures. The use of these techniques is frequently seen in critical infrastructure projects, underscoring the method's significant role in building lasting and reliable structures. For instance, bridges or pipelines often necessitate this high-performance welding, emphasizing the method's significance in modern construction and engineering.
1. High Strength
High strength is a defining characteristic of specialized welding techniques, including those categorized as "Hercules Welding." This attribute is critical for ensuring the structural integrity and durability of components subjected to substantial stress and load. The ability to achieve and maintain high strength directly impacts the longevity and reliability of fabricated structures.
- Material Selection and Properties
The selection of appropriate base materials is fundamental. Welding processes must accommodate the inherent properties of these materials, including their tensile strength, yield strength, and ductility. Specialized alloys or high-strength steels often form the basis for components requiring exceptional strength. This necessitates a profound understanding of material science to optimize weld design and execution.
- Weld Design and Geometry
Appropriate weld design is crucial. Factors such as weld geometry, reinforcement, and the placement of weld beads directly influence the final weld strength. Engineers must consider stress concentrations and potential failure points when creating weld designs. Complex calculations and simulations are often employed to ensure optimal weld geometry.
- Welding Process Parameters
Control over the welding process itself is critical. Factors such as current, voltage, travel speed, and gas flow must be precisely regulated. Inadequate control can lead to welds with diminished strength, potentially compromising safety and longevity. Automated systems and precise monitoring are crucial to maintain consistently high weld strength.
- Post-Weld Heat Treatment (PWHT)
In some cases, post-weld heat treatment (PWHT) is necessary to relieve residual stresses and improve the overall mechanical properties of the weld. PWHT can be employed to further enhance the strength and refine the microstructure of the weld, thereby optimizing its performance under anticipated service conditions. Careful consideration of the process is required to balance desired strength enhancement with potential adverse effects on component dimensional stability.
The multifaceted nature of achieving high strength in "Hercules Welding" underscores the intricate interplay between material science, welding techniques, design principles, and meticulous process control. The inherent need for robust, long-lasting structures demands this rigorous approach, guaranteeing the safety and dependability of critical applications.
2. Precision Control
Precision control is integral to "Hercules Welding." This meticulous approach encompasses precise management of welding parameters to achieve desired weld characteristics. Variations in amperage, voltage, travel speed, and shielding gas flow can significantly impact the resultant weld's properties. Maintaining consistent, controlled parameters is paramount for achieving the high strength and integrity demanded by applications reliant on these welds. Deviations in these critical elements can lead to variations in weld penetration, heat-affected zone formation, and ultimately, compromise the structural integrity of the finished product. Consequently, the precision control aspect fundamentally dictates the quality and reliability of the resulting weld, directly influencing the safe and efficient functioning of the constructed components.
Real-world examples highlight the importance of precision. In aerospace construction, for instance, welds in aircraft fuselages or engine components must adhere to stringent tolerances for structural soundness and performance. Slight variations in welding parameters can significantly impact the fatigue life of the component or even compromise airworthiness. Similarly, in the energy sector, precisely controlled welds in pipelines are critical to ensure the integrity and durability of the infrastructure, preventing costly leaks and safety hazards. The precise control over the welding process in these high-stakes applications directly translates to enhanced reliability and safety. The avoidance of inconsistencies is vital to prevent potentially catastrophic structural failures.
Understanding the pivotal role of precision control in "Hercules Welding" is crucial for engineers and technicians. It underscores the necessity of sophisticated equipment calibrated to precise tolerances and skilled operators trained to maintain consistent parameters. This precision-focused approach minimizes variations, which is essential for producing high-quality, dependable welds. The meticulous execution, therefore, contributes to the overall safety and long-term reliability of the structures or components on which it is applied. Failure to adequately prioritize precise control can have considerable repercussions across diverse industries, ranging from infrastructure to manufacturing.
3. Advanced Materials
The selection of materials is fundamental to achieving the strength and durability demanded by "Hercules Welding." Advanced materials, often engineered alloys with tailored properties, are frequently employed. These materials possess enhanced tensile strength, fatigue resistance, and corrosion resistance, critical factors for applications demanding extended service life and reliable operation. The choice of material is inextricably linked to the successful implementation of the welding process and its subsequent long-term performance. A deep understanding of material behavior under various stress conditions is essential for optimal weld design and execution.
Specific examples illustrate the critical role of advanced materials. In aerospace applications, high-strength alloys, carefully selected for their resistance to extreme temperatures and stresses, are vital. Likewise, in the construction of bridges and high-rise buildings, specialized steels exhibiting superior weldability and high yield strength are crucial for structural integrity. The selection of suitable materials is not merely about maximizing strength but also about optimizing ductility and impact resistance, ensuring the structural components can withstand unforeseen loads and environmental conditions. Corrosion resistance is another significant factor, particularly in marine environments or harsh industrial settings.
The use of advanced materials in "Hercules Welding" requires a multifaceted approach encompassing material science, welding techniques, and engineering design principles. Understanding the interplay between these elements is essential for optimal weld performance. Careful consideration must be given to factors such as grain structure, heat treatment, and the specific alloying elements within the materials. This ensures the resulting welds meet the precise requirements for the application. The selection of advanced materials represents a critical step in ensuring the reliability, safety, and longevity of structures and components where "Hercules Welding" is employed. This understanding has significant practical implications for design engineers, constructors, and safety personnel. Material selection directly impacts safety margins, maintenance schedules, and overall operational costs.
4. Complex Designs
Complex designs are intrinsically linked to specialized welding techniques like those categorized as "Hercules Welding." The intricate geometries and demanding tolerances found in advanced structures necessitate precise welding processes capable of achieving high strength and structural integrity. These designs often incorporate numerous components, requiring meticulous weld planning and execution to ensure the integrity of the final assembly. This connection emphasizes the crucial role of advanced welding in accommodating and reinforcing intricate structural elements.
- Multi-faceted Assemblies
Many complex designs consist of multiple, interconnected components. These components may have varying geometries and require intricate welds to create strong, seamless connections. Think of aerospace structures where various wings, fuselage sections, and engine components need to be meticulously integrated. The need for precise alignment, weld penetration, and consistent weld quality throughout the diverse assembly is paramount.
- Intricate Geometries
Complex designs often incorporate curved surfaces, sharp angles, and intricate shapes. Achieving high-quality welds in these geometries requires advanced welding techniques and tools. Precise control over heat input, weld bead placement, and the mitigation of distortion are critical in order to retain the structural integrity and aesthetic appeal of these components. Examples can be seen in high-pressure vessels, pipelines, or intricate custom-designed machinery.
- Precise Tolerances and Alignment
Complex designs are frequently characterized by precise tolerances, requiring exacting alignment between parts before and during welding. Errors in alignment or tolerance variations can compromise the structural integrity and functionality of the finished product. Techniques like laser alignment or specialized jigs are employed to ensure that pieces are assembled accurately and ready for welding. This alignment requirement is crucial for achieving both the aesthetic goals and the strength goals of the structure, underscoring the necessity for precise control in "Hercules Welding".
- Material Complexity
Complex designs frequently incorporate diverse materials with different properties. This may include different metals, composites, or coatings. Welding these diverse materials requires expertise to prevent weld failures or material incompatibility. Maintaining consistency in strength and avoiding stress concentration points through the weld is vital. Appropriate welding processes and material preparation techniques must be employed to accommodate these diverse material characteristics.
In summary, the relationship between complex designs and "Hercules Welding" underscores the need for sophisticated techniques and skilled professionals. These techniques, while demanding, are essential for creating structures that are both aesthetically pleasing and functionally robust. The intricate nature of the designs necessitates a deep understanding of material properties, welding processes, and precision in execution, ultimately contributing to the integrity and reliability of the final product.
5. Robust Structures
Robust structures rely on the integrity of their constituent components, including welds. "Hercules Welding" techniques are essential for achieving this robustness. The strength and durability of a structure are directly correlated with the quality of its welds. Failures in welds compromise the structure's ability to withstand intended loads and stresses, leading to potential safety hazards and costly repairs. High-quality welds are critical to prevent catastrophic failure in critical applications.
Real-world examples demonstrate this connection. In bridge construction, welds in supporting beams and girders must be exceptionally strong to maintain structural integrity under heavy traffic and environmental pressures. Likewise, in the aerospace industry, welds in aircraft components play a vital role in the aircraft's ability to withstand the forces of flight. Imperfect welds in these applications can have serious safety implications. Precise control over the welding process is paramount for ensuring the structure can perform its function reliably over time. Furthermore, in heavy machinery, robust welds are essential for the longevity and safe operation of critical components, preventing breakdowns and failures. Robust structures, dependent on high-quality welds, are imperative for reliable performance and safety.
Understanding the relationship between robust structures and "Hercules Welding" is critical for engineers and designers. It dictates the selection of appropriate materials, welding procedures, and quality control measures. This knowledge ensures structures can withstand anticipated loads and environmental factors. The use of advanced materials, precise weld geometry, and meticulous quality checks are all essential components in creating a robust structure capable of withstanding the rigors of its intended application. Without this attention to detail, the potential for structural failure and associated risks significantly increases. This knowledge forms the bedrock of safe and durable construction practices across numerous industries.
6. Critical Infrastructure
Critical infrastructure, encompassing essential services like power grids, transportation networks, and water systems, relies heavily on the integrity of its components. These systems are often subjected to substantial stress and require exceptional durability. "Hercules Welding" techniques become vital in ensuring the longevity and reliability of such infrastructure. Precise, high-strength welds are essential to withstand the stresses inherent in these applications, preventing catastrophic failures with potentially wide-ranging consequences.
Real-world examples demonstrate the crucial role of advanced welding in critical infrastructure. Consider pipelines transporting oil and gas; robust welds are essential to prevent leaks and explosions. Failures in these welds can have severe environmental consequences and pose significant risks to human safety. Similarly, in power generation facilities, welds in pressure vessels and turbines must meet stringent standards to guarantee uninterrupted power supply. The intricate systems within these facilities demand high-quality welds to withstand immense pressure and temperature fluctuations. Furthermore, bridges and other transportation systems, experiencing constant load and movement, depend on highly reliable welds to ensure structural integrity. Failures can result in loss of life and costly repairs. The quality and precision of welding directly influence the dependability and longevity of critical infrastructure, underscoring the profound importance of this technology.
Understanding the interplay between critical infrastructure and "Hercules Welding" is crucial for engineers and maintenance personnel. It necessitates a deep understanding of material science, welding procedures, and stringent quality control measures. Accurate assessment of the potential stresses and operational parameters is essential to guarantee the longevity of critical infrastructure components. Proper design considerations, including weld geometry and material selection, directly affect the system's overall safety and reliability. This specialized knowledge ensures the sustained function of crucial services, safeguarding public well-being and the economic stability of a nation. The significance of maintaining a high standard of "Hercules Welding" within critical infrastructure extends beyond mere technical expertise; it encompasses societal well-being and economic resilience.
Frequently Asked Questions about Hercules Welding
This section addresses common inquiries surrounding Hercules Welding, providing concise and informative answers. These responses aim to clarify key aspects of this specialized welding process.
Question 1: What distinguishes Hercules Welding from other welding techniques?
Hercules Welding typically focuses on applications requiring exceptionally high strength and durability. Distinguishing features often include the use of specialized alloys, intricate weld designs, and meticulous control over welding parameters. This specialized approach necessitates precise equipment and skilled personnel to ensure consistent high-quality welds suitable for demanding environments.
Question 2: What are the key applications for Hercules Welding?
Hercules Welding finds application in sectors demanding robust structures, including aerospace components, heavy machinery, critical infrastructure (like pipelines and bridges), and high-pressure vessels. Its specific use depends on the need for exceptionally strong and durable welds capable of withstanding substantial stress and load.
Question 3: What materials are commonly employed in Hercules Welding?
The choice of materials in Hercules Welding hinges on the specific application's requirements. Often, high-strength alloys, specialized steels, and advanced composites are utilized. The selection considers the material's ability to maintain integrity during the welding process and its long-term resistance to environmental factors and operational stresses.
Question 4: What are the critical considerations for quality control in Hercules Welding?
Rigorous quality control is paramount in Hercules Welding. This includes precise control over welding parameters (current, voltage, speed), careful examination of weld beads, and often, post-weld heat treatment (PWHT). Maintaining strict tolerances and adherence to industry standards are fundamental aspects of the quality control process, ensuring reliable performance of the finished product.
Question 5: What are the training requirements for professionals in Hercules Welding?
Specialized training is necessary for personnel performing Hercules Welding. Comprehensive training programs cover the specific welding techniques, equipment operation, material properties, and quality control procedures. Certifications and ongoing professional development are often crucial for staying current with advancements in this field. Understanding material compatibility and the specific application's demands is essential for professionals.
The precision, stringent control, and focus on high-strength, long-term performance define Hercules Welding. These factors dictate the high standards and intensive training required for successful execution. Understanding these nuances is crucial for maintaining the reliability of structures relying on this technique. This understanding ensures the safe operation and longevity of critical infrastructure.
This concludes the FAQ section. The following sections will explore the detailed aspects of Hercules Welding equipment, process specifics, and best practices. This includes safety considerations for professionals involved.
Conclusion
This exploration of "Hercules Welding" has highlighted the critical role of this specialized welding technique in constructing robust and durable structures. Key aspects discussed include the demanding need for high strength, precise control, the use of advanced materials, the intricacies of complex designs, and the vital contribution to critical infrastructure. The significance of meticulous quality control throughout the process, from material selection to post-weld treatments, was emphasized. The analysis revealed that "Hercules Welding" is not simply a method but a complex system requiring significant expertise and advanced technology to ensure optimal performance and long-term reliability.
The future of "Hercules Welding" hinges on continued advancements in materials science, welding processes, and quality control methodologies. Maintaining a high standard of execution is not only crucial for safety but also for optimizing the efficiency and lifespan of structures in diverse sectors. Ongoing research and development in this field are essential to address the evolving demands of modern construction and engineering. The meticulous execution of these welding principles will remain a fundamental element of safe and reliable infrastructure design for years to come.

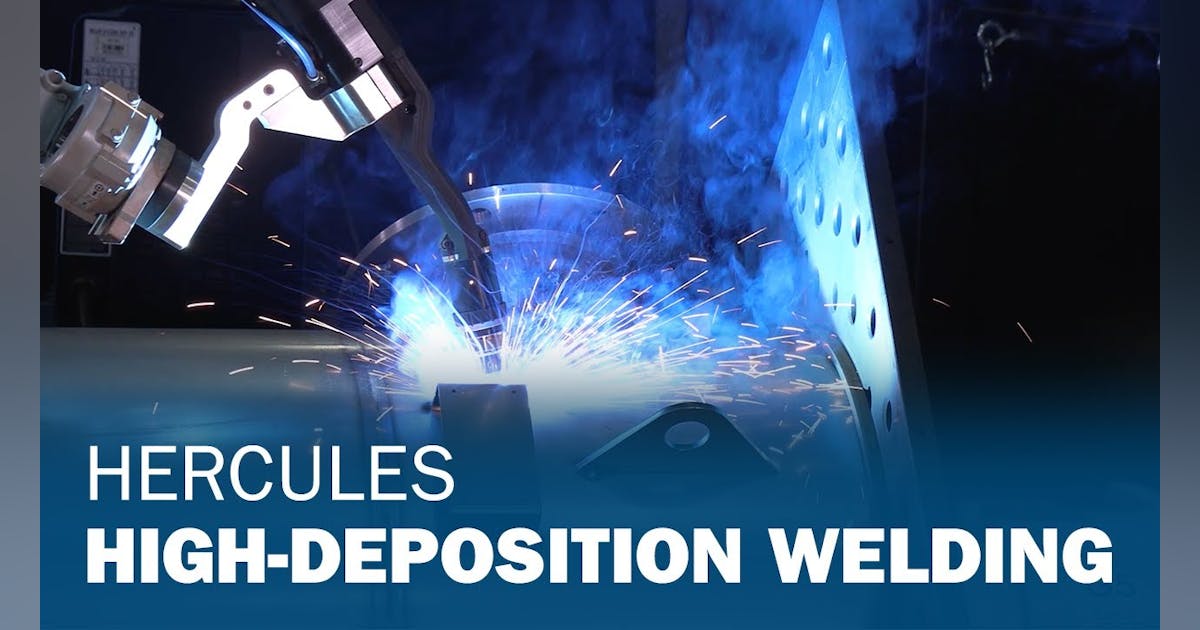
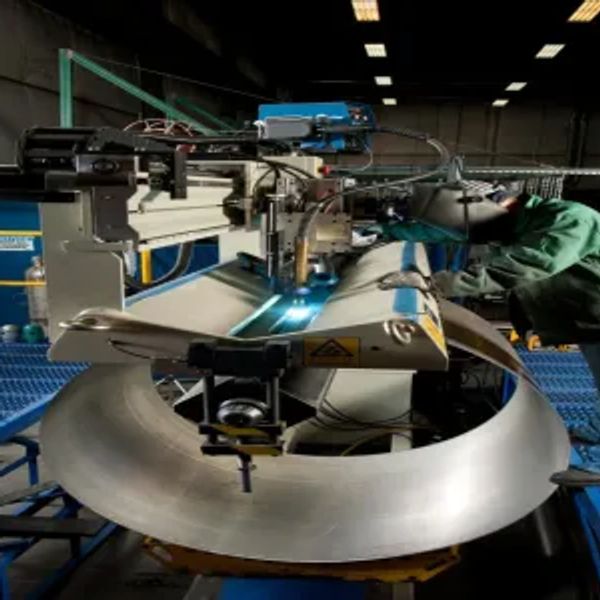