What causes damage to constrained components, and what implications does this have? A look at the repercussions of compromised restraints.
Compromised restraints, whether in machinery or personal protective equipment, can be the result of various factors. These might include material fatigue from repeated stress, improper installation or maintenance, environmental factors such as corrosion, or direct impact. Examples include a cracked safety harness during a construction fall, a malfunctioning emergency stop mechanism in a factory machine, or a torn fabric strap on a wristwatch. In each instance, the failure of the restraint can lead to serious consequences, ranging from minor inconvenience to severe injury or damage.
The consequences of compromised restraints depend heavily on their specific function and application. In industrial settings, this can lead to equipment malfunctions, production downtime, and potential worker injuries. In personal safety gear, such failures can result in accidents and even fatalities. Historical records demonstrate the critical need for consistently robust and well-maintained restraining systems, across a wide range of industries.
This analysis will explore a range of scenarios where impaired restraints are central to the narrative. This investigation will cover preventative strategies, repair methods, and the implications for safety protocols across multiple sectors.
Broken Restraints
Understanding the multifaceted nature of compromised restraints is crucial for safety and functionality. Proper assessment and attention to detail are essential to prevent issues.
- Material Failure
- Design Flaws
- Improper Use
- Environmental Damage
- Maintenance Neglect
- Impact Forces
- Operational Errors
Material failure, design flaws, and improper use can contribute to compromised restraint systems. Environmental damage, such as corrosion, weakens structures over time. Neglect of maintenance schedules accelerates degradation. Impact forces or sudden pressure can cause immediate breakage. Operational errors during installation or deployment lead to malfunction. In a manufacturing setting, these factors could lead to equipment malfunction, injury, or product defects. Identifying and addressing these elements are critical in preventing potentially harmful or costly incidents. For instance, a frayed seatbelt (compromised restraint) can lead to injury in a vehicle accident; a cracked aircraft component (also a compromised restraint) would present safety risks and could have fatal consequences. Understanding the intricate interplay of these elements improves safety procedures and prevents catastrophic failures.
1. Material Failure
Material failure is a critical factor in compromised restraints, including those often referred to as "broken cuffs." Understanding the mechanisms behind material degradation is essential for preventing failures and ensuring safety, whether in machinery, personal protective equipment, or other applications relying on the integrity of materials.
- Fatigue and Stress Cycling
Repeated application of stress, even below the material's ultimate strength, can lead to microscopic damage accumulating over time. This fatigue process weakens the material, eventually causing fracture or failure. In a mechanical component, this could manifest as a broken gear or fractured axle. For restraints, repeated flexing or tensioning can lead to weakening, and eventual breakage, leading to compromised safety. Examples include a chain link breaking during repeated lifting operations, or a metal strap becoming brittle after prolonged exposure to stress from vibration.
- Corrosion and Degradation
Chemical reactions between materials and the environment can lead to corrosion, weakening and ultimately causing failure. Different environmental factors play a role, from moisture to specific chemicals in industrial settings. Corrosion in restraining systems can compromise their strength and durability, creating a significant safety hazard. For instance, a metal cuff used in a lifting mechanism can corrode, reducing its ability to hold load, leading to failure and risk of injury. Similarly, exposure to harsh chemicals in a work environment could degrade a safety strap or harness.
- Material Defects and Imperfections
Manufacturing flaws or inherent imperfections in the material can cause stress concentration. These imperfections can compromise strength, making the material susceptible to failure at lower stresses than expected. A defect in a metal forging used in a mechanical restraint could lead to premature failure under load. Similarly, a microscopic flaw in a composite material used in personal protective equipment could weaken the fabric or fiber and lead to a potentially disastrous failure.
- Improper Material Selection
Choosing an inappropriate material for a specific application can result in significant risk. If a restraint is subjected to forces beyond the material's capacity, failure is inevitable. For example, using a soft wire for a high-tension cable system could lead to premature breakage and a serious risk of injury. Conversely, using an exceptionally rigid material where flexibility is necessary could cause discomfort and reduced mobility.
In all cases, understanding the factors contributing to material failure is paramount for selecting appropriate materials, implementing robust preventative measures, and establishing stringent maintenance schedules. These strategies directly impact the safety and reliability of systems reliant on the integrity of materials.
2. Design Flaws
Design flaws in restraints, often leading to what might be termed "broken cuffs," can stem from various factors. Inadequate consideration of stress concentrations, inappropriate material selection for the intended use, or insufficient safety factors in design calculations all contribute to vulnerabilities. A design flaw inherently compromises the structural integrity of a restraint, making it susceptible to failure under anticipated or unanticipated stresses. This deficiency can have severe consequences, ranging from minor inconveniences to catastrophic failures, highlighting the crucial role of meticulous design in ensuring safety and reliability.
Examples of design flaws leading to compromised restraints are abundant. A poorly designed seatbelt with insufficient anchorage points, leading to a compromised restraint, could result in a passenger being ejected during a collision. Similarly, a safety harness with a weak stitching pattern in the load-bearing straps could result in failure during a fall, with catastrophic consequences. In industrial equipment, a poorly designed lever mechanism, designed with insufficient consideration for stress distribution, might break unexpectedly, causing equipment malfunctions and potential injury. These examples underscore the direct connection between flawed design and compromised restraint systems, emphasizing the need for rigorous design evaluations and testing to identify and address potential vulnerabilities.
Recognizing the significance of design flaws in creating vulnerabilities within restraints necessitates thorough scrutiny of design specifications and rigorous testing protocols. This approach is vital in minimizing the risk of catastrophic failures and ensuring the safety and reliability of systems relying on the integrity of such components. Careful consideration of potential stress points, load-bearing capacity, and the material's properties are critical during the design phase. Detailed simulations and real-world testing procedures should be integrated to identify and correct design flaws before the widespread deployment of potentially dangerous components. Ultimately, a proactive approach focusing on design robustness is crucial in preventing incidents related to broken restraints.
3. Improper Use
Improper use is a significant contributing factor to compromised restraints, often leading to what might be termed "broken cuffs." This category encompasses a wide range of human errors, from neglecting safety protocols to exceeding specified limits. The direct link between misuse and failure is clear: incorrect application or exceeding the intended operating parameters invariably weakens the restraint and renders it vulnerable to failure. This vulnerability can lead to severe consequences, highlighting the paramount importance of proper training and adherence to established procedures.
Numerous real-world examples illustrate the dangers of improper use. A construction worker improperly fastening a safety harness, for instance, may lead to a fall. In industrial settings, operating machinery beyond its designated load capacity can result in equipment failure and potential worker injury. A pilot landing a plane with a malfunctioning safety harness might be compromised. Similar situations exist in various other contexts, from improperly used seatbelts in automobiles to faulty rigging in construction or marine operations. Such cases demonstrate how seemingly minor violations of proper procedure can escalate to critical incidents involving broken restraints and resultant harm. The common denominator in these examples is the failure to adhere to established guidelines.
Understanding the connection between improper use and compromised restraints is critical for improving safety protocols and minimizing risks. Training programs focusing on proper procedures, equipment maintenance, and operational limits are essential. Regular assessments and enforcement of safety standards can help mitigate these issues. Clear communication of usage instructions, alongside readily accessible safety data sheets, are crucial. The resulting understanding can significantly reduce instances of compromised restraints and subsequent incidents. In essence, the prevention of improper use is paramount in minimizing the occurrence of broken restraints and the resulting potential hazards.
4. Environmental Damage
Environmental factors significantly contribute to the degradation and failure of restraints, often leading to compromised integrity and potentially hazardous situations. Exposure to various elements, including moisture, temperature fluctuations, and specific chemicals, can weaken materials and diminish the structural strength of components. This degradation process, while often gradual, can ultimately lead to catastrophic failures. The resulting damage can manifest as fractures, corrosion, or material embrittlement, all of which can lead to compromised restraints, impacting a wide range of applications, from industrial machinery to personal protective equipment. The consequences can range from equipment malfunction to severe injury or even fatality.
Consider a metal cuff used in a lifting mechanism. Prolonged exposure to moisture and salt spray in a marine environment will accelerate the corrosion process, reducing the cuff's load-bearing capacity and increasing the likelihood of premature failure. Similarly, extreme temperature fluctuations in an outdoor environment can cause thermal stress, leading to cracks and fractures in materials, compromising the structural integrity of restraints such as suspension bridges or aircraft parts. Exposure to harsh chemicals, common in industrial settings, can also accelerate corrosion or induce chemical reactions that weaken materials and reduce the strength and durability of restraints. These examples illustrate the critical role environmental conditions play in compromising restraints, and the importance of taking these factors into account during design, manufacturing, and operational phases.
Understanding the impact of environmental damage on restraints is crucial for preventative measures. Proper material selection, protective coatings, and regular maintenance schedules can help mitigate the effects of environmental degradation. Moreover, implementing appropriate environmental monitoring systems can alert personnel to potentially hazardous conditions and allow for proactive intervention to reduce the risk of failure. This knowledge directly translates to improved safety standards and decreased risk of equipment failure in critical applications, leading to a safer and more reliable operational environment. By incorporating environmental factors into the design and maintenance protocols, the likelihood of compromised restraints, and the potential for catastrophic consequences can be significantly minimized.
5. Maintenance Neglect
Neglect of maintenance procedures directly contributes to the deterioration of restraints, leading to failures. Regular inspections, lubrication, and component replacements are vital to prevent gradual weakening and eventual breakage. Failure to address these elements creates a cascade of risk, increasing the likelihood of what can be termed "broken restraints." The consequences can range from minor inconveniences to significant injuries or fatalities, depending on the application and severity of the neglect.
Real-world examples demonstrate the devastating effects of maintenance neglect. A critical component in an aircraft's landing gear, left unmaintained, can experience progressive fatigue. This, over time, may lead to fracture during operation, with potentially catastrophic consequences. In industrial machinery, neglected lubrication can cause friction and wear. This rapid deterioration weakens crucial components, leading to sudden breakdowns and potential injury. Similarly, inadequate inspection of safety harnesses and ropes in construction or mountaineering can mask structural damage, leading to failures under load, resulting in serious harm. In each instance, neglected maintenance exposes personnel and equipment to unforeseen risks associated with compromised restraints. Proactive maintenance protocols directly reduce the likelihood of these potentially severe incidents.
Understanding the causal link between maintenance neglect and "broken restraints" highlights a crucial responsibility for safety professionals and operators. Establishing and enforcing comprehensive maintenance schedules, coupled with rigorous inspections, is essential. Training personnel on proper maintenance procedures minimizes errors. This knowledge, combined with regular testing and replacements of worn parts, can prevent catastrophic failures. Ultimately, proactive maintenance stands as a critical defense against the consequences of neglected maintenance, preventing potential harm and maximizing the operational lifespan of critical equipment and systems. By addressing maintenance neglect head-on, the frequency of "broken restraints" can be significantly reduced.
6. Impact Forces
Impact forces represent a significant threat to the integrity of restraints, potentially leading to "broken cuffs." Understanding the mechanisms by which these forces exert their damaging effect is crucial for minimizing the risk of associated injuries and equipment failures. This exploration examines the various aspects of impact forces in relation to compromised restraints.
- Magnitude and Direction of Force
The severity of damage from an impact force hinges directly on its magnitude and direction. A high-velocity impact will exert significantly more force than a low-velocity one. Moreover, the angle at which the force is applied impacts the stress distribution across the restraint, potentially concentrating stress in specific areas, rendering them more susceptible to failure. For example, a direct hit to a safety harness will have a different impact than a glancing blow. Understanding these parameters is key to anticipating the potential failure points.
- Duration of Impact
The duration of the impact also plays a significant role. A short, sharp impact might cause localized damage, while a longer-lasting impact can lead to widespread material degradation or fatigue. This extended impact can generate substantial stress within the restraint, exceeding the material's capacity, thus increasing the chance of breakage. Examples include a whiplash-style impact versus a more sustained crushing force.
- Material Properties of the Restraint
The inherent material properties of the restraint significantly influence its response to impact forces. A brittle material is far more susceptible to fracture than a ductile one. The elasticity and tensile strength of the material determine its ability to absorb and distribute the impact forces. Consequently, selecting appropriate materials for the intended application is paramount to safety.
- Point of Impact
The location of the impact on the restraint is critical. A localized impact can cause concentrated stress, leading to failure at that precise point. Conversely, a more distributed impact can cause damage along a wider area. Understanding the stress distribution within the restraint, particularly at critical load points, is essential for risk assessment. For example, a direct impact on a rivet in a safety harness might cause that rivet to fail, leading to a complete breakdown of the restraint.
In conclusion, impact forces are a complex interplay of magnitude, duration, material properties, and the location of impact. Failure to consider these factors can result in compromised restraints. Thorough analysis of potential impact scenarios and the use of appropriate materials and designs can mitigate the risk of "broken cuffs" and subsequent injuries or damage.
7. Operational Errors
Operational errors represent a significant contributing factor to compromised restraint systems, often leading to failures. These errors, encompassing a spectrum of human actions or inactions, can result in inadequately secured or improperly utilized restraints, ultimately leading to instances of what may be termed "broken cuffs." Understanding the various facets of operational errors is crucial for improving safety protocols and minimizing the risk of injury.
- Inadequate Training and Procedures
Insufficient or ineffective training programs can result in personnel lacking the necessary knowledge and skills to properly utilize restraints. This lack of proficiency can lead to misapplication, improper tightening, or failure to adhere to safety protocols. Examples include improper knot tying in a rigging system, incorrect harness adjustments during a climbing operation, or failure to check equipment before use. Such deficiencies increase the risk of compromised restraints and associated accidents.
- Exceeding Design Limits
Operating a system beyond its intended capacity or exceeding specified load limits places undue stress on restraints. This can lead to premature failure, even under seemingly normal operating conditions. Real-world examples include overloading a lifting mechanism beyond its rated capacity, resulting in a broken sling, or a vehicle exceeding the load limit imposed on the seatbelt system. Such errors directly compromise the structural integrity and can result in catastrophic failure.
- Equipment Misuse and Neglect
Improper handling, neglect, or intentional misuse of restraints can compromise their effectiveness. This includes damage from improper storage, exposure to harmful environments, or deliberate modifications, all of which reduce the strength or structural integrity of the restraining device. Examples include using a frayed or damaged safety harness, storing restraints in corrosive environments, or tampering with locking mechanisms. Such actions directly contribute to a potential for broken cuffs and incident-related injuries.
- Inadequate Supervision and Monitoring
Insufficient oversight and monitoring of personnel during operations can allow for errors that go uncorrected, thereby increasing the risk of compromised restraints. Absence of clear supervision protocols or the lack of a trained supervisor on-site during critical activities can lead to unmitigated issues. For example, a construction crew undertaking tasks requiring robust fall protection without appropriate supervision may not adequately inspect or maintain their safety harnesses, and consequently, potentially lead to failures.
In summary, operational errors are multifaceted and encompass a range of human and procedural failures. Preventing these errors through robust training programs, clear operating procedures, and rigorous safety checks is paramount in minimizing the risk of compromised restraints, a critical factor in preventing significant workplace accidents and injuries. Failure to recognize the direct link between operational errors and "broken cuffs" can lead to potentially devastating consequences.
Frequently Asked Questions
This section addresses common inquiries regarding compromised restraints, emphasizing the importance of understanding the factors contributing to such issues. Understanding these factors is crucial for maintaining safety and avoiding potential harm.
Question 1: What are the primary causes of compromised restraints?
Compromised restraints result from a confluence of factors, including material fatigue, corrosion, design flaws, improper use, environmental damage, and maintenance neglect. Repeated stress cycles, exposure to corrosive substances, inadequate design specifications, operator error, environmental conditions, and skipped maintenance routines all contribute to reduced strength and potential failure.
Question 2: How does material fatigue contribute to restraint failure?
Material fatigue arises from repeated stress cycles. Even stresses below the material's ultimate strength can cause microscopic damage that accumulates over time. This leads to progressive weakening, eventually resulting in fracture or failure. Regular inspections and preventative maintenance are crucial in mitigating this risk.
Question 3: What are the implications of using restraints beyond their design limits?
Exceeding design limits imposes excessive stress on the restraint system. This can lead to premature failure and subsequent injuries or equipment damage. Understanding and adhering to specified load capacities and operating parameters is essential for safety.
Question 4: How does environmental exposure affect the integrity of restraints?
Environmental factors, including moisture, temperature fluctuations, and corrosive chemicals, can significantly degrade the performance of restraints. This degradation weakens materials, impacting the strength and reliability of the restraining system. Proper material selection, protective coatings, and regular inspections are essential in environments with these hazards.
Question 5: What is the importance of regular maintenance for restraint systems?
Regular maintenance, encompassing inspections, lubrication, and component replacements, is critical for preventing deterioration and ensuring the continued effectiveness of restraints. Neglecting maintenance accelerates weakening, thereby increasing the risk of failure and associated risks. Established maintenance schedules are vital for safety and reliability.
Understanding the causes and implications of compromised restraints is paramount for mitigating potential safety risks. Adhering to safety protocols, utilizing appropriate materials, and maintaining equipment are vital for preventing failures and ensuring safe operations. Consistently rigorous safety standards are necessary to prevent incidents and to foster a culture of safety.
Next, we'll explore specific preventative measures that can strengthen systems and minimize the risk of compromised restraints.
Conclusion
This exploration of compromised restraints, often referred to as "broken cuffs," highlights the multifaceted nature of safety failures. The investigation underscored the critical interplay of material degradation, design flaws, improper use, environmental damage, and maintenance neglect. Each factor contributes independently and synergistically to the weakening and ultimate failure of restraint systems. The analysis revealed that failures are not isolated incidents but rather the result of a complex interplay of vulnerabilities. Understanding these interconnected factors is crucial for mitigating risks and preventing catastrophic consequences, across a spectrum of applications from industrial machinery to personal protective equipment.
The pervasive nature of compromised restraints demands a comprehensive and proactive approach to safety. A robust strategy necessitates rigorous material selection, meticulous design, comprehensive training, adherence to stringent maintenance schedules, and ongoing environmental monitoring. Failure to address these factors inevitably increases the likelihood of catastrophic failures. Safety protocols must evolve beyond reactive measures to embrace proactive strategies, focusing on the inherent vulnerabilities in restraints and the interconnectedness of operational elements. The consequences of ignoring these critical aspects are severe, demanding a commitment to preventative measures, diligent maintenance, and robust safety standards for a secure and reliable operational environment.

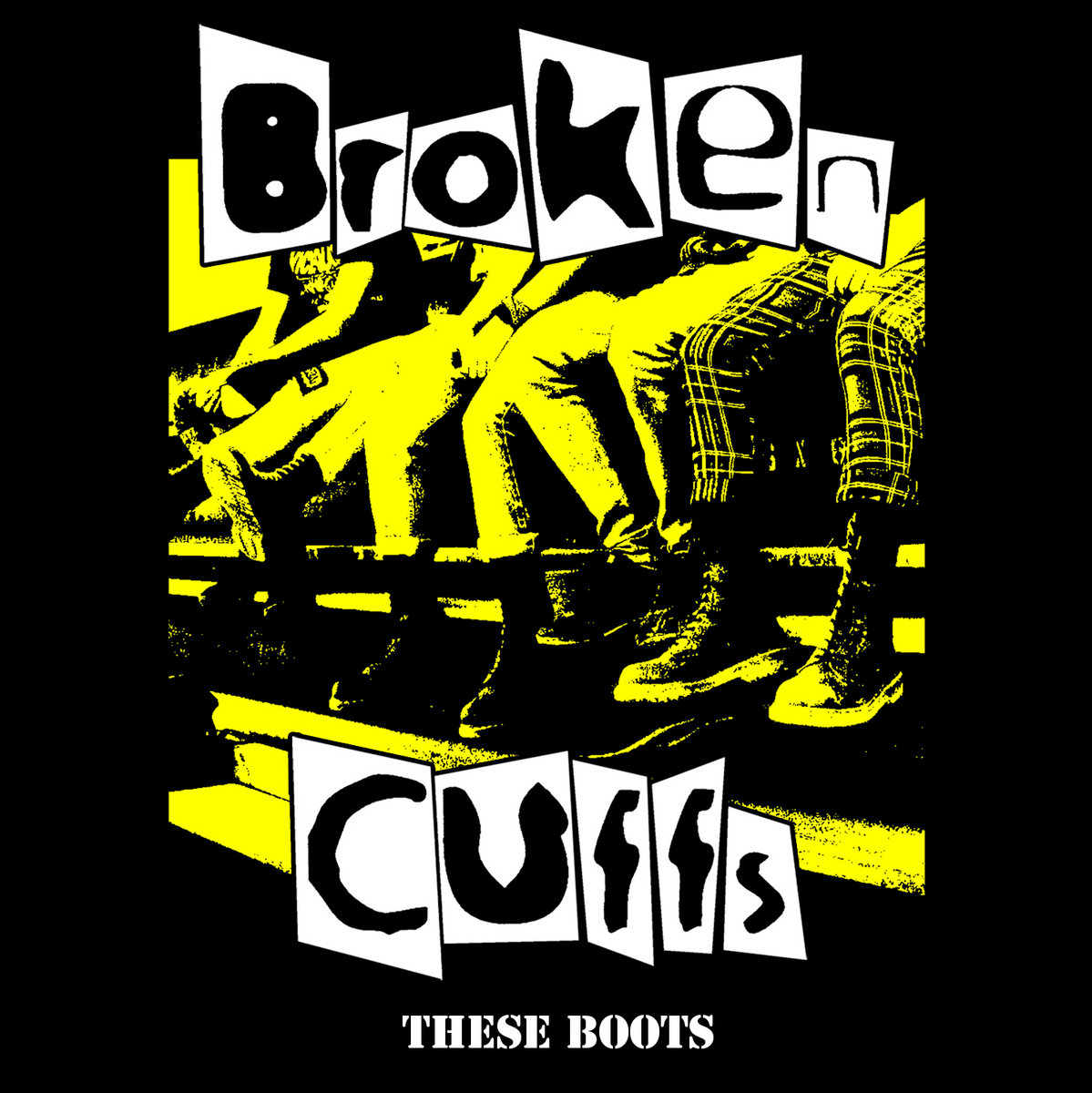
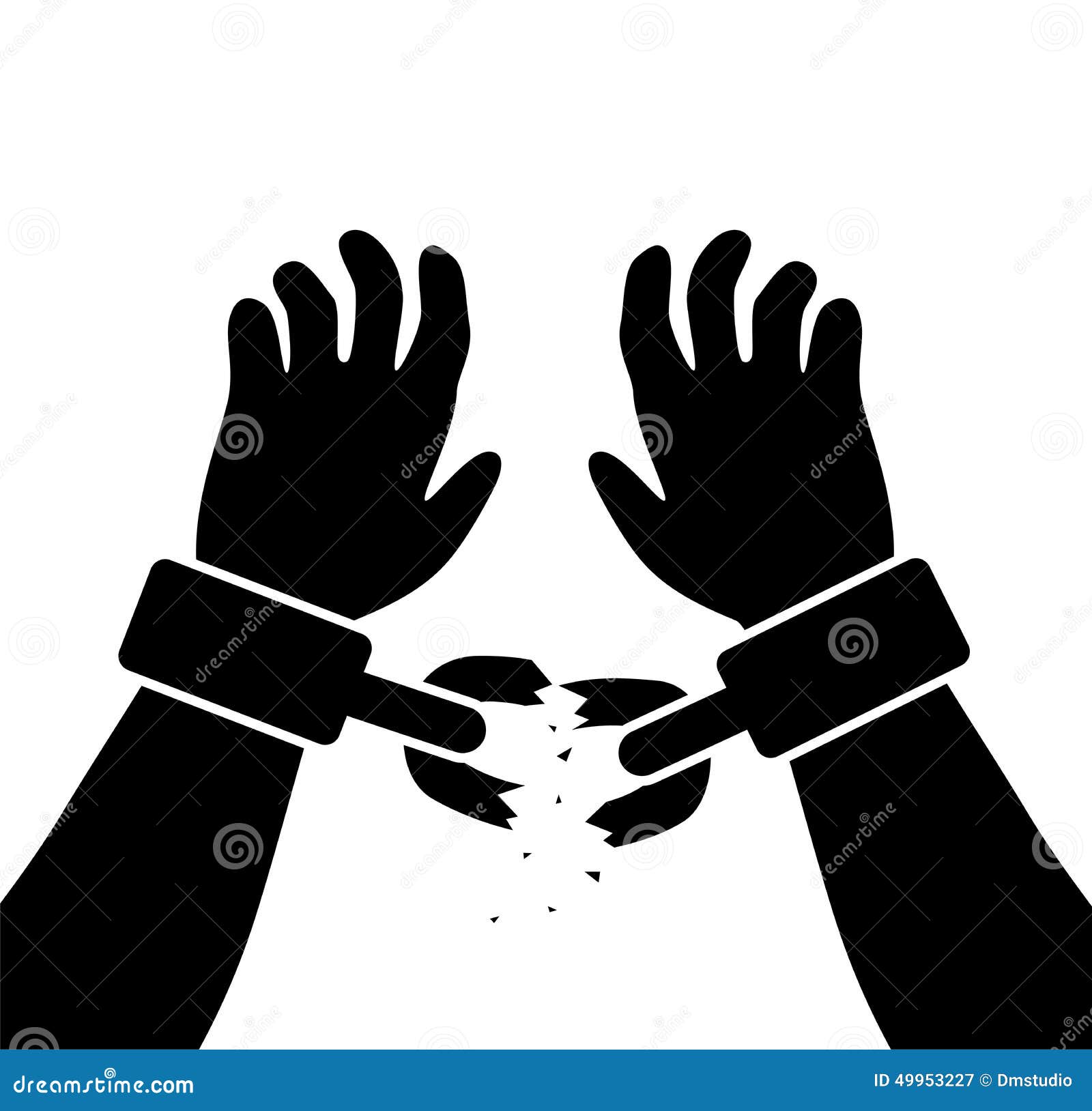