How do specialized professionals work on critical infrastructure beneath the waves? A crucial role demands unique skills and equipment.
A specialist trained in welding underwater, this individual employs specialized techniques and equipment to join metals in submerged environments. This often involves working in confined spaces, and at significant depths. The process necessitates precise control of weld parameters, environmental conditions, and the maintenance of proper safety protocols to accomplish reliable, quality welds. Examples include repairing offshore oil rigs, pipelines, or underwater structures in ports. Safety measures are paramount due to the challenging environment.
These professionals are essential for maintaining and repairing critical infrastructure in marine environments. Their expertise ensures the safe and effective operation of deep-sea pipelines, offshore platforms, and other underwater installations. The specialized equipment and training required for this work highlight the complexity and importance of maintaining these critical underwater components. History reveals a gradual evolution from rudimentary to advanced techniques and equipment, showcasing the dedication to safer underwater operations. Successful underwater welding allows for extended operational lifespans of crucial assets and is an example of continuous improvement.
Moving forward, we will explore the specific requirements, training, and equipment used for this demanding field.
Underwater Welder
The profession of underwater welding necessitates specialized skills and equipment for critical infrastructure maintenance. This demanding field requires a deep understanding of various factors to ensure safe and effective operations.
- Specialized Equipment
- Submerged Environment
- Precise Techniques
- Safety Protocols
- Material Properties
- Welding Procedures
The specialized equipment used for underwater welding encompasses specialized welding torches, waterproof power sources, and environmentally sealed controls. The submerged environment necessitates specific techniques to compensate for pressure, visibility, and access challenges. Adherence to stringent safety protocols is paramount for mitigating risks, ensuring worker safety and preventing potential environmental damage. Understanding material properties critical to the chosen welding method enables appropriate selection and quality control. Precise welding procedures are crucial for producing strong, durable welds capable of withstanding underwater pressure. These procedures are validated through rigorous testing and inspections. These aspects, interconnected and crucial, highlight the demanding nature of the field.
1. Specialized Equipment
Effective underwater welding hinges critically on specialized equipment. The unique challenges of the underwater environment necessitate tools designed to operate safely and reliably under pressure and limited visibility. These tools are crucial for the success and safety of underwater welders.
- Welding Torches
Specialized torches are designed to withstand pressure and conduct electricity reliably underwater. These often feature water-resistant housings and specialized electrode configurations suitable for submerged welding processes. Examples include torches designed for specific metals or welding procedures, such as those for arc welding, plasma arc welding, or metal inert gas welding. The correct torch selection significantly impacts weld quality and safety.
- Power Sources
Power sources must provide consistent electrical current under water pressure. This necessitates compact, pressure-resistant units capable of generating the necessary amperage. These units often feature specialized cooling systems and components designed to withstand the marine environment. Such sources might employ specialized voltage regulators to maintain consistent amperage even with changing water conditions.
- Environmental Seals and Controls
Essential for maintaining functionality underwater, environmental seals and controls prevent water ingress into equipment and maintain proper functionality of the welding process. This includes waterproof housings for electrical components, pressure-resistant conduits for gases and cables, and sealing systems for welding wire and shielding gases. These components are crucial for preventing short circuits, breakdowns, and the potential for hazardous conditions.
- Instrumentation and Monitoring Systems
Precise measurements and monitoring of welding parameters are imperative in underwater environments. This necessitates specialized tools that accurately measure variables like amperage, voltage, and depth. The instrumentation and monitoring systems ensure the welds meet specifications, enabling real-time adjustments based on variables like pressure and water temperature, aiding in maintaining weld quality and safety.
The specialized equipment highlighted demonstrates the critical connection between design and performance in underwater welding. Each component plays a role in mitigating risks and enabling safe, reliable operations, directly impacting the overall success of the underwater welder's tasks.
2. Submerged Environment
The submerged environment presents a unique set of challenges for underwater welders. Pressure, limited visibility, and the corrosive nature of seawater significantly impact the welding process. These environmental factors are not merely background conditions but fundamental determinants of safety procedures, equipment design, and welding techniques. The pressure exerted at depth necessitates specialized equipment resistant to crushing forces. For instance, deep-sea pipelines require welds capable of sustaining immense pressure, a factor directly dependent on the specific environmental conditions.
Limited visibility in the water column necessitates careful planning and precise execution. Real-time monitoring and advanced welding techniques such as remotely operated vehicle (ROV) guidance become critical. The corrosive properties of seawater accelerate material degradation, demanding high-quality materials and stringent maintenance schedules for welding equipment and the welding process itself. Rust formation on metal surfaces underwater necessitates meticulous pre-welding preparation and careful control of welding parameters to ensure structural integrity. Examples include the maintenance of submerged oil and gas infrastructure, where water quality and flow can directly affect welding results. Consequently, understanding the specific attributes of the local environment is essential.
In summary, the submerged environment is inextricably linked to the practice of underwater welding. The challenges posed by pressure, visibility, and corrosion necessitate specialized equipment, meticulous planning, and advanced techniques. This understanding forms the foundation for safety protocols, material selection, and the design of effective procedures to ensure the successful completion of underwater welding projects. Failure to account for these factors can compromise the integrity and longevity of underwater structures, highlighting the profound importance of a comprehensive understanding of the submerged environment within the context of underwater welding.
3. Precise Techniques
Precise techniques are fundamental to the success and safety of underwater welding. The unique challenges of the submerged environment demand meticulous control over every aspect of the welding process. Accuracy in welding parameters, material selection, and execution are critical to achieving high-quality, durable welds capable of withstanding pressure and corrosive conditions. This precision is paramount for the structural integrity of underwater infrastructure.
- Weld Parameter Control
Precise control over welding parameters, including amperage, voltage, and welding speed, is essential. Deviations from established protocols can compromise weld strength and integrity. This requires sophisticated instruments for real-time monitoring and precise adjustments. For instance, consistent amperage delivery is vital in maintaining weld quality at considerable depths. Inaccurate settings can lead to incomplete fusion or excessive heat input, potentially weakening the weld. Variations in water temperature, salinity, or pressure further necessitate dynamic adjustments to achieve optimal results.
- Material Selection and Preparation
Choosing the right materials for the submerged environment is crucial. Corrosion resistance, tensile strength, and weldability need meticulous consideration. Substantial pre-welding preparation, including surface cleaning and defect rectification, is often required. Materials must be compatible with the specific chemical composition of the water to mitigate corrosion risks. Improper material selection can contribute to premature failure of underwater structures, emphasizing the importance of precise material choice and preparation. For example, in saltwater environments, specific alloys are essential for preventing galvanic corrosion. This necessitates diligent assessment of the marine environment.
- Joint Design and Positioning
Careful joint design and precise positioning are essential for achieving a strong and reliable weld. Geometric considerations, including angle, overlap, and bevel angles, significantly affect weld quality. Special care is needed for complex geometries and tight spaces. Improper joint design can create stress concentrations, compromising the strength of the weld and the structure. For example, pipe welds require precise beveling and positioning to ensure complete fusion and consistent wall thickness. Techniques used to position the work piece are critical for the overall outcome.
- Inspection and Quality Control
Rigorous inspection and quality control processes are vital to ensuring weld integrity. Employing sophisticated testing and analysis methods, such as radiography and ultrasonic testing, allows for comprehensive verification of weld properties and adherence to standards. This continuous evaluation helps identify potential issues early in the process, minimizing the risk of structural failures. For underwater welding, specific nondestructive testing techniques accounting for pressure and water conditions are vital.
Precise techniques in underwater welding directly translate into the safety and longevity of underwater infrastructure. Each element, from the meticulous control of welding parameters to comprehensive post-weld analysis, collectively contributes to the reliability and durability of structures. These strategies highlight the importance of precision in this specialized field, ensuring the structural integrity of critical assets in demanding underwater environments.
4. Safety Protocols
Safety protocols are paramount for underwater welders. The unique hazards of the submerged environment necessitate rigorous adherence to established procedures. These protocols encompass pre-dive preparations, operational techniques, and post-dive contingencies, ensuring the protection of personnel and the prevention of potential environmental damage. Effective protocols directly impact the successful and safe execution of underwater welding tasks.
- Pre-Dive Assessments and Planning
Thorough pre-dive assessments are critical. This involves evaluating environmental conditions, including water depth, currents, visibility, and potential hazards. Careful planning considers equipment functionality, emergency procedures, and the allocation of personnel. Accurate assessment of currents, pressure gradients, and site conditions is crucial. Detailed risk assessments, outlining potential dangers, form the basis of safety planning. For example, a comprehensive pre-dive briefing may include safety guidelines, emergency procedures, and the verification of all equipment before dive operations commence.
- Equipment Integrity and Maintenance
Rigorous maintenance and comprehensive checks of all diving and welding equipment are essential. This includes verifying the integrity of pressure vessels, gas cylinders, and personal protective equipment. Comprehensive inspections, including testing and maintenance documentation, ensure equipment's readiness for use under pressure. For instance, pressure-testing diving gear, verifying the operational status of the submersible, or checking the welding torch's integrity prevent operational failures. Regular inspections and proper maintenance of equipment enhance the overall safety of the operation.
- Dive Procedures and Monitoring
Strict adherence to standardized dive procedures, including decompression schedules and ascent rates, is fundamental. Continuous monitoring of vital signs and location is critical. Monitoring equipment and crew communication systems are paramount. Examples include employing real-time communication systems for constant contact with the crew, establishing safe depth limits, and adhering to decompression protocols after each dive. These procedures mitigate risk and maximize safety.
- Emergency Response Procedures
Detailed emergency response procedures are necessary for handling potential incidents. This includes protocols for decompression illness, equipment failure, or entanglement. Emergency protocols should encompass rescue procedures, communication protocols, and first aid protocols. Examples include having an emergency response team on standby, establishing clear communication channels for immediate response, and familiarizing personnel with first aid protocols for various injuries. Preparedness, through well-defined and practiced emergency procedures, minimizes potential risks.
Effective safety protocols are critical for maintaining the well-being of underwater welding personnel and the protection of the marine environment. They ensure the reliable and efficient completion of underwater welding operations. Failure to adhere to rigorous safety measures can result in potentially severe consequences. This underlines the indispensable role of comprehensive safety protocols in the underwater welding industry.
5. Material Properties
Material properties are fundamental to underwater welding. The selection of materials directly impacts the success and safety of welds in a submerged environment. Resistance to corrosion, tensile strength, and weldability are critical considerations. For example, in deep-sea oil pipelines, materials must withstand immense pressure and corrosive seawater. Choosing a material susceptible to rapid degradation would compromise the pipeline's integrity. Furthermore, certain materials exhibit enhanced corrosion resistance under specific conditions (e.g., elevated salinity or temperature), affecting the suitability of materials for particular marine environments. The understanding and application of material science is not merely an academic exercise; it's crucial for ensuring the structural integrity and long-term viability of underwater structures.
The interplay between material properties and underwater welding conditions is intricate. For instance, stainless steel alloys, known for their corrosion resistance, are frequently employed in underwater structures. However, the specific alloy composition and heat treatment process influence its susceptibility to corrosion pits and cracking under various stress conditions. Weldability also impacts the ability to create strong, continuous bonds underwater. Poor weldability can lead to weak joints, compromising the overall structural strength of the assembled components, especially in demanding deep-sea applications. Therefore, understanding the metallurgical properties of the base material is essential to achieve high-quality, reliable welds in a challenging underwater environment. Furthermore, the understanding of material properties informs pre-welding preparation procedures, optimizing the weld process and enhancing safety by preventing issues like hydrogen embrittlement or stress corrosion cracking.
In conclusion, selecting suitable materials based on their specific properties is crucial for successful underwater welding. The interplay between material properties, welding techniques, and environmental factors influences the overall performance of underwater structures. This understanding is indispensable for ensuring the safety and longevity of underwater infrastructure. The ability to predict and mitigate potential failures due to material weaknesses is a key aspect of proficient underwater welding. Engineers and technicians specializing in underwater welding must understand these characteristics, ensuring that the welds created not only meet but exceed quality standards, especially given the high-stakes nature of underwater projects.
6. Welding Procedures
Welding procedures are fundamental to the successful and safe execution of underwater welding tasks. They provide a structured framework for the process, encompassing critical steps and techniques to ensure quality welds capable of enduring the demanding submerged environment. These procedures are not merely guidelines but essential components in mitigating the inherent risks associated with underwater welding, including pressure, limited visibility, and corrosion. Adherence to established procedures ensures consistent quality and longevity of underwater infrastructure.
- Pre-Weld Preparation
Thorough pre-weld preparation is crucial. This includes meticulous surface cleaning to remove contaminants and imperfections that can compromise weld integrity. Understanding the specific material properties and characteristics of the base metal is essential. Procedures often include mechanical cleaning methods, chemical treatments, or a combination thereof, optimizing the weld surface for adhesion and ensuring a consistent metallurgical interface. Careful inspection for cracks, pitting, or other defects minimizes the potential for weld failure. For instance, preparation for welding on corroded metal requires additional steps to ensure uniform weld penetration. This step directly affects the weld's strength, ensuring consistent performance under pressure.
- Welding Technique Selection
The choice of welding technique significantly influences the outcome. Different welding processes, such as arc welding, submerged arc welding, or metal inert gas (MIG) welding, present unique characteristics regarding heat input, penetration depth, and the weld quality achievable. The selection considers the base material, welding environment, and desired weld properties. For example, in welding thick sections of pipe, the choice will differ from a thin plate, demanding expertise in identifying the optimal welding procedure. This factor is essential for producing strong and reliable welds capable of handling the immense pressure and stresses encountered in submerged environments.
- Weld Parameter Control
Precise control over welding parameters, including amperage, voltage, and welding speed, is paramount. These parameters are intricately linked to the weld's strength, stability, and corrosion resistance. Techniques for regulating these variables are vital, accounting for environmental pressures and potential temperature variations. For example, adjusting amperage or voltage in response to changes in depth or water temperature ensures consistent welding quality throughout a project. This meticulous control minimizes the risk of incomplete fusion or excessive heat input, factors that can compromise the structural integrity of underwater structures.
- Post-Weld Inspection and Testing
Post-weld inspection and testing are critical. These procedures confirm weld quality and adherence to specifications. Methods may include visual inspections, radiographic testing, and ultrasonic testing. The results inform decisions about acceptance or rework. For instance, radiographic images help identify internal flaws that might not be apparent visually. This verification process ensures the integrity and longevity of underwater structures, mitigating the risk of catastrophic failure.
Welding procedures, therefore, are not just a series of steps but a crucial element in the expertise of an underwater welder. They are central to the success, safety, and longevity of underwater infrastructure. Comprehensive knowledge of these procedures enables welders to adapt to diverse submerged environments, produce high-quality welds, and minimize potential failures. These practices are crucial for the reliable operation of critical underwater assets. In essence, the quality of welding procedures directly impacts the efficacy and longevity of underwater projects.
Frequently Asked Questions
This section addresses common inquiries concerning underwater welding, providing clear and concise answers to key questions about this specialized field. The information presented aims to clarify procedures, equipment, and safety considerations involved in underwater welding operations.
Question 1: What distinguishes underwater welding from conventional welding techniques?
Underwater welding differs significantly from conventional techniques due to the unique challenges of the submerged environment. These include pressure variations, limited visibility, and the corrosive nature of seawater. Specialized equipment, including pressure-resistant welding torches, waterproof power sources, and sealed controls, is essential. Precise control of welding parameters is also critical to compensate for these environmental factors. Procedures for pre-welding preparation, dive planning, and post-weld inspection are significantly more complex and rigorously enforced to mitigate risks. The complexity of this field mandates expertise in both welding and underwater operations.
Question 2: What safety precautions are specific to underwater welding?
Safety protocols in underwater welding extend beyond those of conventional welding. Rigorous pre-dive assessments, including environmental evaluations and equipment checks, are mandatory. Strict adherence to established dive procedures, including decompression schedules and emergency response plans, is critical. The use of specialized safety equipment like dive suits, breathing apparatus, and emergency signaling devices is mandatory. Real-time monitoring of divers and equipment is crucial, requiring communication systems and safety procedures specific to the underwater environment. Specialized training for handling underwater emergencies is also essential.
Question 3: What specialized equipment is required for underwater welding?
Underwater welding necessitates specialized equipment capable of operating under pressure and water. This includes pressure-resistant welding torches, compact and reliable power sources that can function underwater, and equipment designed to maintain the integrity of the welding process in the water column. Environmental seals and controls, ensuring the water-tightness of all components, are crucial. Monitoring systems, for parameters like voltage, amperage, and depth, are integrated into the design to enable adjustments during operation. Welding cables and wires must be resistant to corrosion, providing reliable conductivity despite the harsh environment.
Question 4: What are the challenges of working underwater?
The primary challenges in underwater welding are the limitations imposed by the aquatic environment. Pressure increases significantly with depth, demanding specialized equipment and techniques. Limited visibility necessitates precision in welding, often relying on specialized tools or guidance systems. The corrosive nature of seawater accelerates material degradation, demanding corrosion-resistant materials and meticulous pre-welding preparation. Equipment functionality and reliability are crucial to avoid failure in these challenging conditions. Furthermore, logistical aspects such as dive planning, communication, and emergency response are essential considerations within this field.
Question 5: What is the importance of pre-weld preparation in underwater welding?
Pre-weld preparation is critical in underwater welding to mitigate corrosion and ensure weld quality. Cleaning the base metal to remove contaminants and imperfections is essential. Material selection needs careful consideration, selecting materials that resist corrosion under the prevailing environmental conditions. Pre-weld preparation protocols also involve rigorous assessment of existing welds and the identification of any defects to optimize procedures and mitigate risks. This ensures the weld meets the required specifications, particularly regarding strength, corrosion resistance, and structural integrity in the long term.
In summary, underwater welding is a specialized field requiring meticulous planning, specialized equipment, and rigorous adherence to safety protocols. This specialized knowledge is essential for the success and safety of underwater welding operations.
Moving forward, we will delve deeper into the specific training and certification requirements for underwater welding professionals.
Conclusion
This exploration of underwater welding highlights the intricate interplay of specialized equipment, precise techniques, and rigorous safety protocols. The unique challenges of the submerged environment necessitate tailored approaches to material selection, welding procedures, and operational logistics. Critical factors such as pressure, limited visibility, and corrosion resistance significantly impact the design of equipment, selection of materials, and execution of welding procedures. The comprehensive understanding of these variables, coupled with adherence to strict safety protocols, underpins the success and safety of underwater welding operations. The demands of underwater welding extend beyond conventional welding, requiring expertise in both welding methodologies and the intricacies of the aquatic environment.
The future of underwater welding likely lies in further advancements in robotic systems and remotely operated vehicles (ROVs). Automated welding systems may become more prevalent, streamlining the process and reducing the exposure of human welders to hazardous conditions. Simultaneously, there is a growing need for skilled professionals capable of operating and maintaining this complex technology. The continued development and refinement of underwater welding techniques and procedures are vital for the continued operation and maintenance of critical infrastructure in the marine environment. This specialized expertise is crucial for the safety and integrity of underwater structures for years to come.

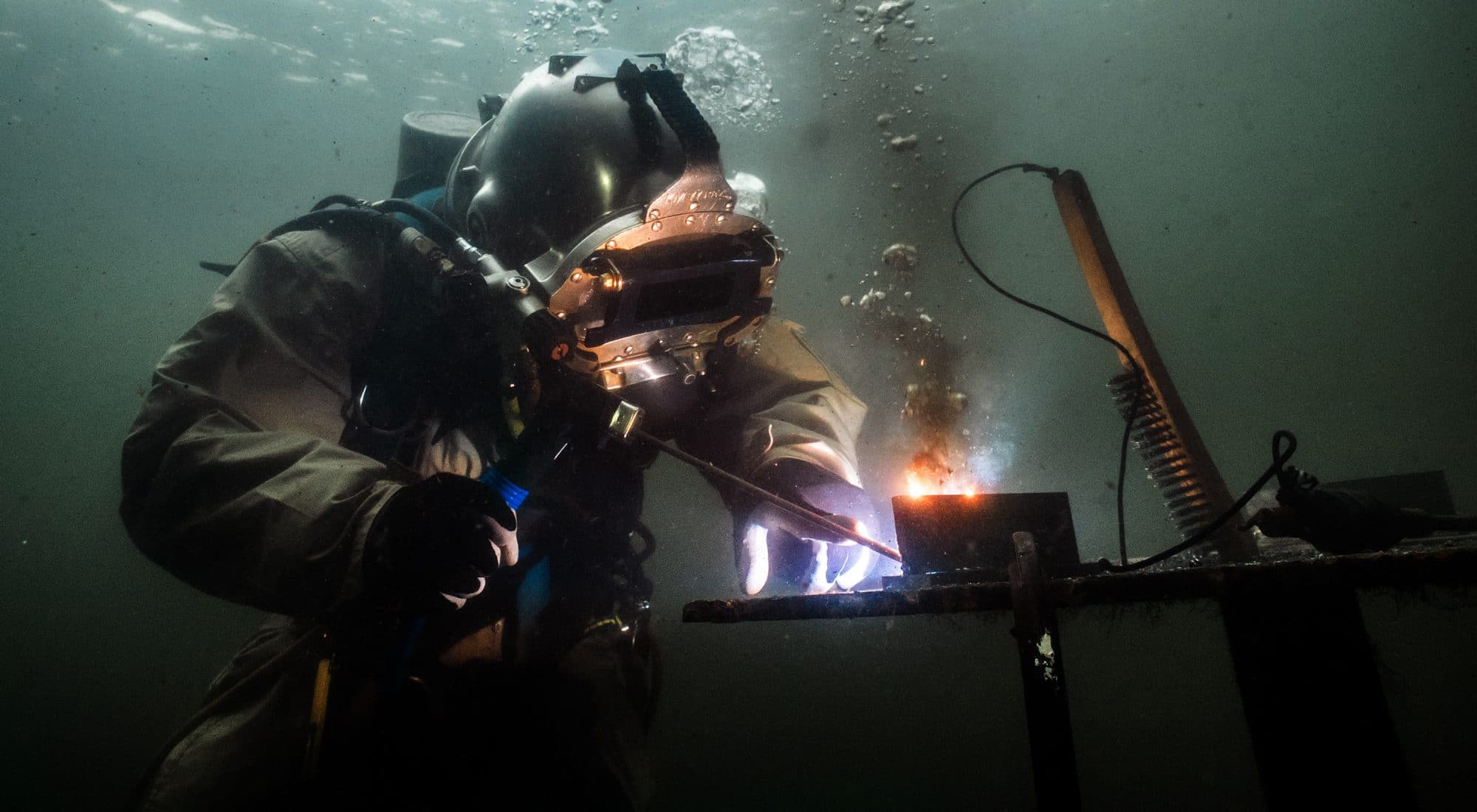
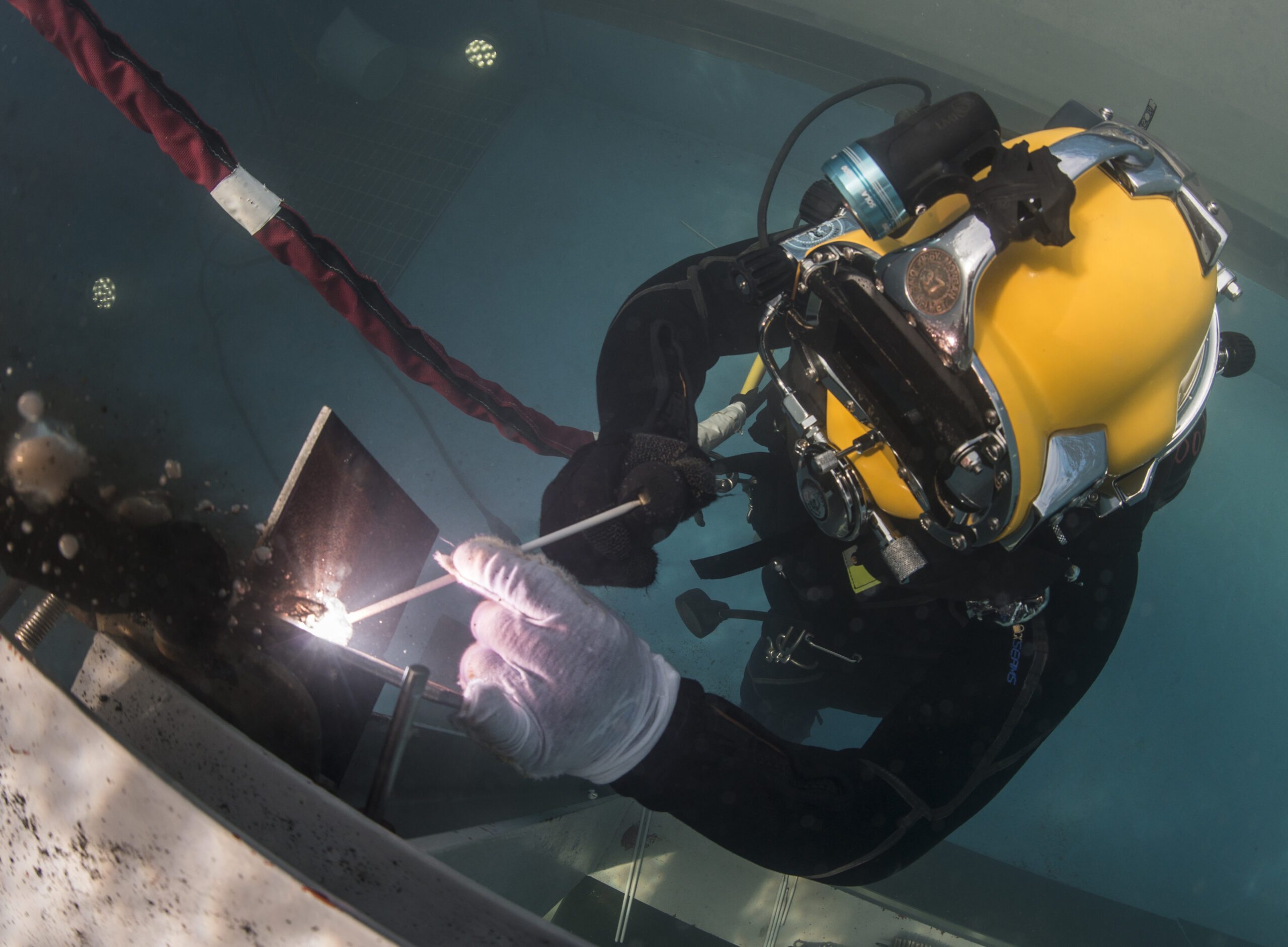