What are the agreed-upon specifications for knots, and why do they matter? Standardized knot designs are critical for consistency and safety in diverse applications.
Defining and documenting knot characteristics allows for the replication of reliable and effective joins. This encompasses details like the type of material used, the specific knotting technique, the desired strength, and the tolerance for variance. Examples include specifications for maritime knots, industrial knots, and climbing knots, ensuring uniform performance under varying conditions. A standardized knot for a particular application, with defined dimensions and load-bearing capacity, is crucial.
The importance of standardized knot specifications lies in their impact on safety and efficiency. Consistency ensures predictable performance, preventing failures that could have serious consequences, from maritime mishaps to industrial accidents. Moreover, pre-defined criteria facilitate training and education, enabling individuals to learn and apply these techniques safely and effectively. Historically, standardized knot knowledge has been vital in areas like navigation, shipbuilding, and exploration, enabling reliable techniques across different geographical locations and time periods.
This now leads us to consider the practical implementation of knot standards within various industries.
Knot Standards
Understanding standardized knot designs is crucial for consistent performance and safety in various fields, from maritime applications to industrial settings. Accurate and consistent knotting techniques are essential for reliable operation and minimize risks.
- Material specification
- Technique definition
- Strength requirements
- Dimensional tolerances
- Load capacity
- Safety factors
- Application contexts
- Testing methodologies
These aspects collectively define a standardized knot. Material specification ensures suitability for the intended use, while technique definition guarantees reproducibility. Strength requirements and load capacity dictate the knot's ability to withstand intended forces, and dimensional tolerances ensure uniformity. Safety factors account for potential variances in material properties or unforeseen stresses. Application contexts narrow the standards to particular uses, like climbing or rigging. Testing methodologies validate compliance with established standards. Properly understood, these aspects contribute to enhanced reliability, reduced failure risk, and improved safety procedures across numerous fields. For example, a standardized climbing knot ensures dependable rope connections, whereas a precise maritime knot minimizes the risk of a vessel's rigging failure.
1. Material Specification
Material specification is a fundamental component of knot standards. The characteristics of the material directly influence the efficacy and safety of the resultant knot. Different materials exhibit varying tensile strengths, elasticity, and resistance to abrasion. A knot's ability to withstand the intended load depends critically on the material's strength properties. For example, a climbing rope constructed from a high-strength, low-stretch polymer will perform better in a knot than one made of a less robust material. Similarly, in maritime applications, the selection of rope made of a material resistant to weathering and saltwater degradation is crucial for long-term reliability.
Furthermore, the material's elasticity and flexibility play a role in the knot's performance. A material with high elasticity might allow a knot to stretch under load, potentially diminishing the overall strength, whereas a material with low elasticity might exhibit brittle behavior during knotting, leading to premature failure. These variations influence the type of knot and the knotting techniques applicable to a given material. Consequently, materials with specific characteristics necessitate the development of tailored knot standards. Conversely, the selection of a particular knot can implicitly dictate certain material properties that are necessary for adequate performance.
In summary, material specification is inextricably linked to knot standards. A proper understanding of material properties is essential for the creation of effective, safe, and durable knots. Failure to account for material characteristics in knot standards can compromise safety and operational reliability in various applications. Thorough consideration of material properties during the design process of a knot is crucial for achieving optimal results.
2. Technique Definition
Accurate technique definition is a cornerstone of knot standards. Precise instructions for constructing a knot are essential for reproducibility and reliability. Variances in knotting technique directly impact the knot's strength, security, and longevity. Consequently, standardizing the techniqueincluding the precise steps, the order of steps, and the tension applicationis paramount. Without standardized procedures, the same knot, seemingly identical, could exhibit substantial differences in strength or durability depending on the individual executing it.
Consider the example of a bowline knot. While the visual appearance might appear uniform, subtle differences in technique can significantly affect its load-bearing capacity. Properly executed, a bowline exhibits high reliability, making it a vital knot in maritime environments. However, improperly formed, the knot could fail under modest stress, posing safety risks. Formalized technique definitions mitigate this risk by providing a clear, consistent blueprint for construction, enabling all practitioners to produce a dependable bowline. This standardization extends to a myriad of knot types, each demanding specific techniques for achieving intended function.
The importance of technique definition extends beyond basic safety considerations. Standardization promotes consistency across different professionals and contexts. This consistency is crucial in high-stakes situations, from climbing expeditions to industrial rigging. Effective technique definitions serve as invaluable training resources, ensuring uniformity in skill development. Clear instructions also facilitate the transfer of knowledge across generations and geographical boundaries, fostering a shared understanding of knotting principles and techniques. Ultimately, accurate technique definition is instrumental in creating a comprehensive framework for knot standards, ensuring that reliable, predictable results are achieved consistently, safeguarding users and maximizing efficiency.
3. Strength Requirements
Strength requirements are integral to knot standards. Predictable and consistent strength is paramount in various applications, from rigging to climbing. Adequate load-bearing capacity is critical to prevent failure and ensure safety. Defining minimum strength criteria is essential for reliability, ensuring that knots can withstand expected loads without compromising structural integrity.
- Load-Bearing Capacity
Determining the maximum load a knot can sustain before failure is fundamental. Different knot types, materials, and application contexts necessitate specific load ratings. For instance, a knot used in a suspension system requires a significantly higher load-bearing capacity than one employed for a decorative purpose. Precise calculations and comprehensive testing protocols are crucial to establish reliable load ratings, factors that are essential components of knot standards.
- Material Properties
The inherent properties of the material directly impact the knot's strength. A knot's strength is inextricably linked to the tensile strength and other mechanical properties of the material used. Different materials exhibit varying degrees of elasticity and flexibility, affecting how the knot handles stresses under load. Knot standards must incorporate material-specific strength data to provide accurate guidelines and ensure the safety of the user.
- Application Factors
The environment and anticipated use significantly influence the necessary strength requirements. Environmental factors, like weathering, abrasion, and exposure to chemicals, can compromise material strength over time. Additionally, the intended load profile also matters. A knot designed for continuous static load requires a different strength rating than one meant for intermittent, dynamic loads. Incorporating these factors into knot standards accounts for real-world conditions and ensures safety.
- Testing Methodologies
Standardized testing methods are vital for validating strength requirements. Rigorous protocols are necessary to gauge the load-bearing capacity of knots, ensuring that stated strength values are accurate representations of actual performance. Consistency in testing methodologies is essential for comparing different knots and materials, and standards should detail the test procedures, equipment, and conditions required for these assessments to maintain accuracy and reliability. These standards are vital for the validity and acceptance of strength claims associated with a knot.
Strength requirements are critical considerations in developing comprehensive knot standards. These detailed aspectsload-bearing capacity, material properties, application factors, and testing methodsensure that knots meet specified criteria, underpinning their safety and reliable performance in various applications. By defining and adhering to robust strength requirements, knot standards ultimately contribute to enhanced safety and efficiency in fields ranging from maritime operations to industrial rigging.
4. Dimensional Tolerances
Dimensional tolerances in knot standards dictate acceptable variations in knot dimensions. These variations are inherent in the manufacturing process and material properties. Precise specifications for knot dimensions are essential because consistent knot geometry ensures consistent load distribution and functionality. Variations in knot size can impact the knot's overall strength, and ultimately influence the safety and reliability of its application. A too-tight or too-loose knot can compromise performance or even lead to failure under load. This is particularly critical in applications requiring repetitive, consistent performance, such as rigging, climbing, and industrial processes.
Consider a maritime application, where a standardized knot in a mooring system must maintain consistent strength across various deployment scenarios. Slight variations in the dimensions of the knot's constrictions can affect its ability to resist the force of the waves or currents. Likewise, in climbing, a precise loop size in a locking knot is crucial for proper engagement of the rope and protection of the climber. Variations in this dimension can reduce the knot's effectiveness in holding or release the rope, presenting serious safety hazards. Similarly, in industrial settings, standardized tolerances in the construction of a lifting knot ensure uniform load distribution, preventing catastrophic failures and preserving equipment integrity. Uniformity in dimensions allows for predictable outcomes, enhancing the reliability and safety inherent in these applications.
Accurate dimensional tolerances are crucial elements of comprehensive knot standards. Precise specifications ensure consistent knot performance across various deployments. These tolerances are not merely theoretical; they translate directly into practical implications for safety and efficiency in diverse applications. Defining and adhering to dimensional tolerances is essential to guarantee the dependable performance and prevent failures that could lead to accidents or damage. This highlights the importance of rigorous testing protocols and consistent quality control measures in producing reliable knots, which are vital components of robust safety standards within those industries.
5. Load Capacity
Load capacity represents a critical aspect of knot standards, directly influencing the safety and reliability of a knot in various applications. A knot's ability to withstand a specified load is paramount. Insufficient load capacity can lead to catastrophic failure, jeopardizing individuals and equipment. Conversely, exceeding the established load capacity can compromise the integrity of the knot, potentially resulting in a sudden and dangerous release of stress or tension. Consequently, accurate determination and documentation of a knot's load capacity are essential elements within knot standards. This necessitates rigorous testing and meticulous analysis of material properties, knot configurations, and environmental factors.
The practical significance of understanding load capacity within knot standards is multifaceted. In maritime applications, a compromised mooring knot could lead to vessel damage or even loss. In climbing, a failing climbing knot can result in a fall with potentially severe consequences. Industrial rigging relies heavily on knots with defined load capacities to ensure the safe lifting and handling of heavy objects. Accurate load capacity data enables engineers and technicians to select the appropriate knot for a given application, mitigating risks and maximizing safety. Without a clear understanding of load capacity, the reliability and safety of various operational procedures become compromised, highlighting the fundamental importance of this parameter within knot standards.
In conclusion, load capacity is not merely a theoretical concept; it is a critical component of knot standards. Accurate and thorough assessment of load capacity, grounded in rigorous testing and a comprehensive understanding of materials and application contexts, safeguards individuals and equipment. Ignoring load capacity in the design and implementation of knot standards compromises safety and opens the door to potentially catastrophic consequences. This reinforces the necessity of robust and precisely defined knot standards that incorporate load capacity as a primary consideration.
6. Safety Factors
Safety factors are crucial components of knot standards. They acknowledge the inherent uncertainties and potential deviations from ideal conditions in real-world applications. A safety factor, often expressed as a multiplier, accounts for variances in material strength, environmental influences, and unpredictable loads. In essence, it provides a margin of safety, ensuring a knot can withstand forces exceeding the anticipated operational loads. A knot standard without a defined safety factor lacks a crucial element of reliability and fails to address the inherent unpredictability of practical application. Failure to incorporate safety factors compromises the entire safety framework, potentially leading to catastrophic consequences.
The incorporation of safety factors into knot standards is predicated on real-world examples. A climbing rope, subjected to dynamic forces and potential abrasion, demands a significantly higher safety factor compared to a static rigging rope. Similarly, a knot used in a marine setting needs to account for fluctuating water currents and potential debris impact, warranting a higher safety margin than a knot in a controlled factory environment. Precisely defined safety factors ensure that the knot remains functional and secure under diverse operational conditions, mitigating the risks of failure. The practical significance of understanding these safety factors in knot standards is critical for ensuring the safety and integrity of personnel and equipment. Safety factors are not merely mathematical calculations; they represent a crucial safeguard in preventing failures, accidents, and potentially life-threatening situations.
In summary, safety factors are not optional additions to knot standards; they are integral components, reflecting the fundamental importance of acknowledging uncertainty and variability in practical applications. A comprehensive knot standard must account for the inherent variations that arise in the field. Without these factors, knot standards risk becoming theoretical ideals, detached from the real-world realities where knots are put into use. Thorough consideration of safety factors, rigorously applied through testing and analysis, elevates knot standards from mere specifications to practical safeguards. This robust approach guarantees a significant contribution to safety and reliability in a multitude of fields.
7. Application Contexts
Application contexts are critical to knot standards. A knot's suitability and effectiveness are directly tied to the specific environment and task for which it is intended. Understanding these contexts is paramount for creating standards that ensure safety and reliability in diverse applications.
- Maritime Applications
In maritime settings, knots are vital for mooring, rigging, and sailing. Knot standards in this context must address the unique stresses and environmental factors at sea. These include fluctuating water currents, potential impacts from waves, and the corrosive effects of saltwater. Consequently, knots used for mooring must possess exceptional load-bearing capacity and resistance to prolonged exposure to harsh conditions. Standards for these knots must incorporate rigorous testing procedures to simulate the dynamic forces encountered at sea.
- Industrial Applications
Industrial environments often require specific knot standards that cater to the unique demands of heavy lifting, rigging, and equipment maintenance. Load-bearing capacities need to be far more substantial compared to other applications. Factors such as abrasion resistance, and resistance to specific chemicals or temperatures must also be taken into account. Industrial knot standards are crucial in preventing accidents and ensuring the continued operation of equipment.
- Climbing Applications
Knot standards for climbing emphasize dynamic load conditions, and resistance to abrasion and stretching. Knots used in climbing must ensure precise and reliable engagement of the rope, preventing slippage and ensuring the security of the climber. These knots must be designed to withstand the dynamic forces associated with climbing and the potential for impacts or unexpected movements. Rigorous testing in simulated climbing scenarios is vital in this context.
- General Purpose Knots
While knots are frequently adapted to specific applications, general-purpose knots find use in various scenarios. Standards for these knots must consider broad applicability without compromising strength. General-purpose knots are frequently employed in everyday situations. For instance, the requirements of a general-purpose knot differ significantly from the demanding requirements of a climbing knot. This often necessitates different safety factors, testing procedures, and materials.
Application contexts, therefore, are not mere descriptive labels but essential parameters for formulating effective knot standards. Tailoring standards to specific contexts ensures the knots meet the unique operational and environmental demands of their designated tasks. These contexts demand different criteria for assessment, from load capacity and environmental resilience to the specific mechanical characteristics of the material. By acknowledging the varied demands of each application, knot standards can achieve optimal safety and reliability across a broad spectrum of uses. A comprehensive approach to knot standards hinges on careful consideration of these application contexts.
8. Testing Methodologies
Testing methodologies are integral to knot standards, acting as the empirical foundation upon which safety and reliability assessments are based. Accurate and consistent testing procedures are critical for ensuring that stated properties align with real-world performance. Without rigorous testing, knot standards become theoretical constructs, lacking the empirical validation necessary to ensure practical safety. Testing methodologies serve to confirm the load-bearing capacity, durability, and overall efficacy of various knot types under different conditions.
Testing methodologies encompass a range of procedures, from controlled laboratory experiments to simulations of real-world conditions. These procedures must be clearly defined and documented, allowing for reproducibility and comparability. Standardized test protocols are vital for ensuring that results are reliable and can be used to compare different knot designs or materials. Crucially, these protocols must incorporate factors specific to the intended use of the knot. For example, a knot used in a mooring system demands testing protocols that simulate the dynamic stresses from waves and currents, while a climbing knot requires testing that reflects the dynamic loads during ascent and descent. Failure to account for these application-specific variables compromises the validity and utility of the testing results.
The practical significance of these testing methodologies is profound. In maritime operations, accurate load capacity assessments for mooring knots are crucial to preventing ship damage. In industrial environments, the proper testing of lifting knots ensures the safe handling of heavy loads, preventing accidents and equipment failures. In climbing, reliable testing methods for knots ensure the safety of climbers, avoiding falls and injuries. Comprehensive testing ensures that knots meet safety standards, thereby minimizing risks and enhancing the safety of individuals and equipment in a multitude of applications. Without these standardized and rigorous methodologies, the entire concept of knot standards becomes fundamentally compromised, and the claimed safety factors lose their grounding in reality. This underscores the importance of incorporating robust and reproducible testing methodologies as a fundamental element of sound knot standards.
Frequently Asked Questions about Knot Standards
This section addresses common inquiries regarding knot standards. Clear definitions and consistent application of these standards are critical for safety and reliability across various industries.
Question 1: What are knot standards, and why are they important?
Knot standards define consistent specifications for knots, encompassing material types, construction techniques, strength requirements, and dimensional tolerances. These standards ensure predictable performance, minimizing risks and promoting safety in applications ranging from maritime operations to industrial rigging and climbing. Standardized procedures facilitate training, enhance reliability, and reduce potential hazards.
Question 2: How are knot standards developed?
Knot standards are developed through a collaborative process. Experts from various relevant fields contribute their knowledge and experience, considering factors like material properties, environmental conditions, and intended uses. Rigorous testing methodologies and analysis form the foundation for establishing these standards. Organizations dedicated to safety and quality often publish and maintain these standards.
Question 3: What factors influence knot strength?
Knot strength depends on multiple factors. Material properties, such as tensile strength and elasticity, directly impact the knot's ability to withstand forces. The specific knot type and construction method significantly influence its load-bearing capacity. Environmental factors, including exposure to moisture, chemicals, or abrasion, affect the long-term strength and durability of the knot. Safety factors are built into standards to account for real-world variability.
Question 4: How do knot standards ensure safety?
Knot standards establish minimum strength requirements and testing procedures, ensuring a predictable level of safety. By specifying techniques, tolerances, and materials, these standards mitigate risks associated with variations in knot construction. This consistency in knot performance helps prevent failures that could lead to accidents or equipment damage. Proper application of these standards plays a crucial role in safety.
Question 5: Are knot standards static?
Knot standards are not static. They are continuously reviewed and updated in response to new materials, advancements in testing technology, and evolving best practices in various applications. This dynamic approach ensures that standards remain current and reflect the ever-changing demands of industries relying on secure knotting.
Understanding knot standards is essential for safe and reliable operation across numerous sectors. These standards promote consistency, enhance reliability, and ultimately contribute to a safer working environment.
Next, we will delve into the practical implementation of knot standards within different industries.
Conclusion
This exploration of knot standards reveals a multifaceted system crucial for safety and reliability across diverse fields. Key components, including material specifications, construction techniques, strength requirements, and dimensional tolerances, are meticulously defined to ensure consistent performance. Application contexts, ranging from maritime operations to industrial rigging and climbing, dictate the specific parameters within these standards. Rigorous testing methodologies are essential to validate the practical application of these standards, ensuring predictable outcomes under various operational conditions. Furthermore, safety factors are incorporated to account for real-world uncertainties and potential variations, emphasizing the proactive approach to risk mitigation inherent in knot standards. A comprehensive understanding of these elements is vital to maximize safety and efficiency, while minimizing the risk of catastrophic failures.
In conclusion, knot standards are not simply sets of specifications but represent a critical safety net in numerous fields. Adherence to these standards is not merely a procedural requirement; it embodies a commitment to safety and operational efficiency. The continued refinement and application of knot standards are essential for ensuring the continued security of personnel and equipment in a variety of settings. Adherence to and diligent application of these standards safeguard against unforeseen challenges and contribute to the overall safety paradigm. Sustained commitment to maintaining and enhancing knot standards ensures their continued effectiveness in a constantly evolving landscape of operational requirements.
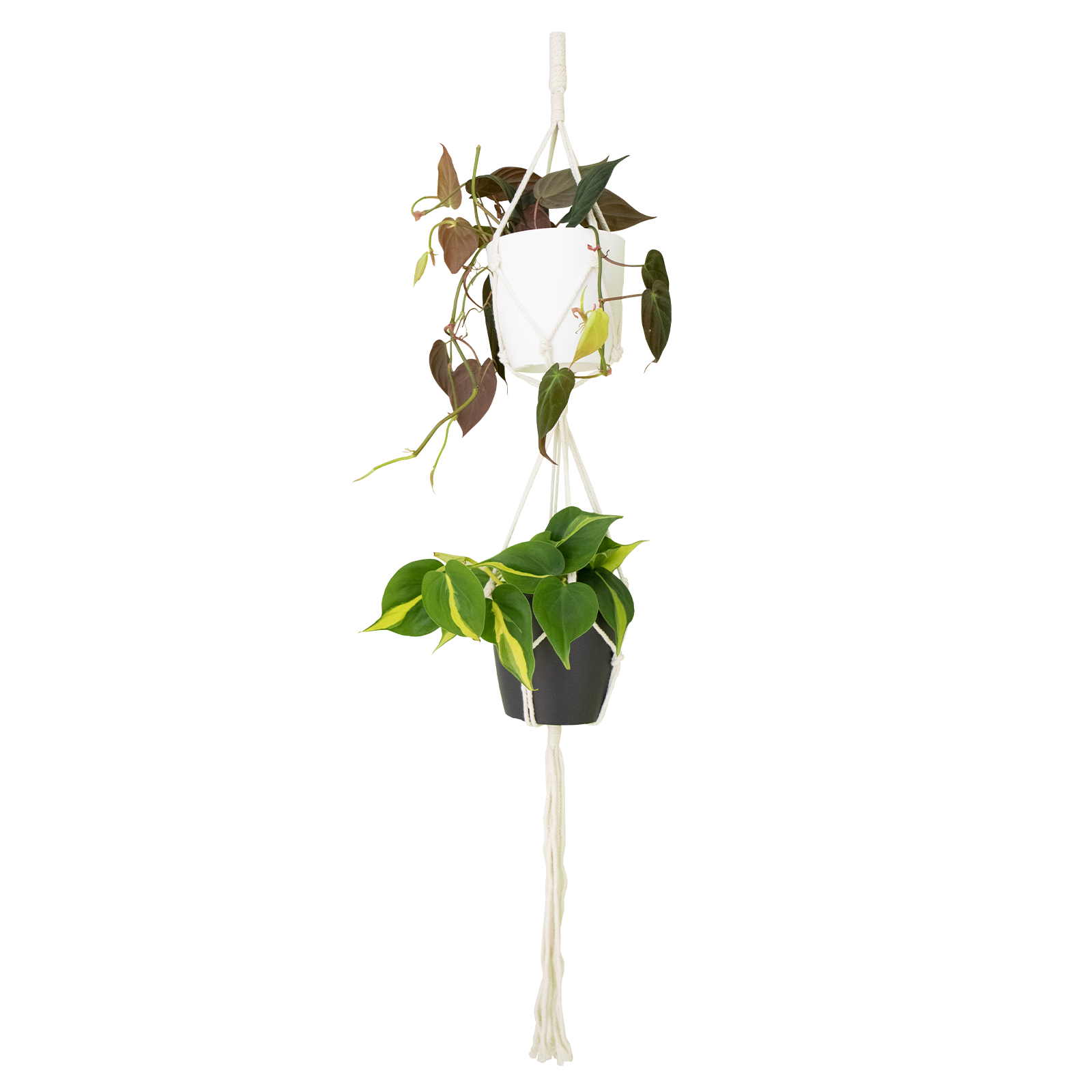
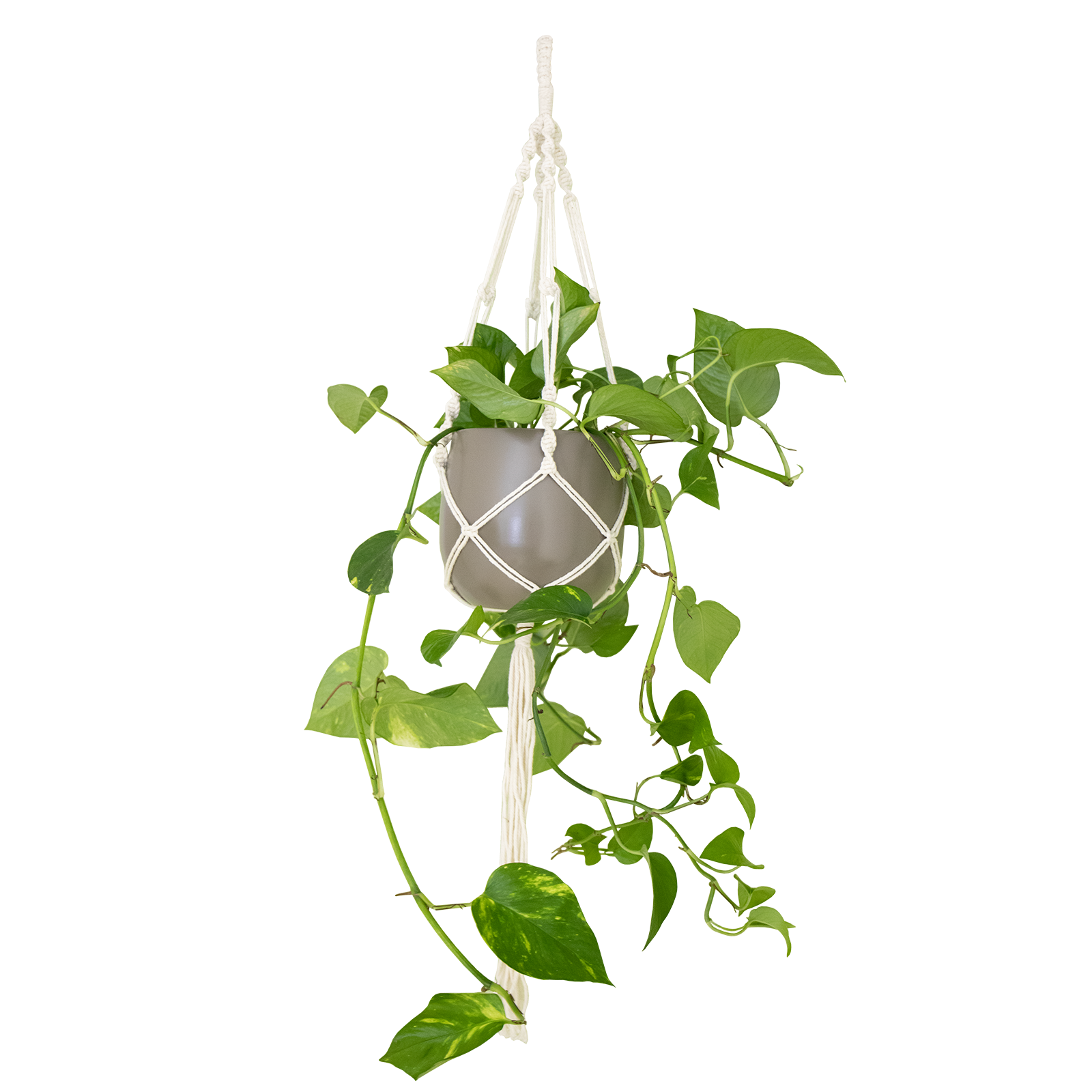
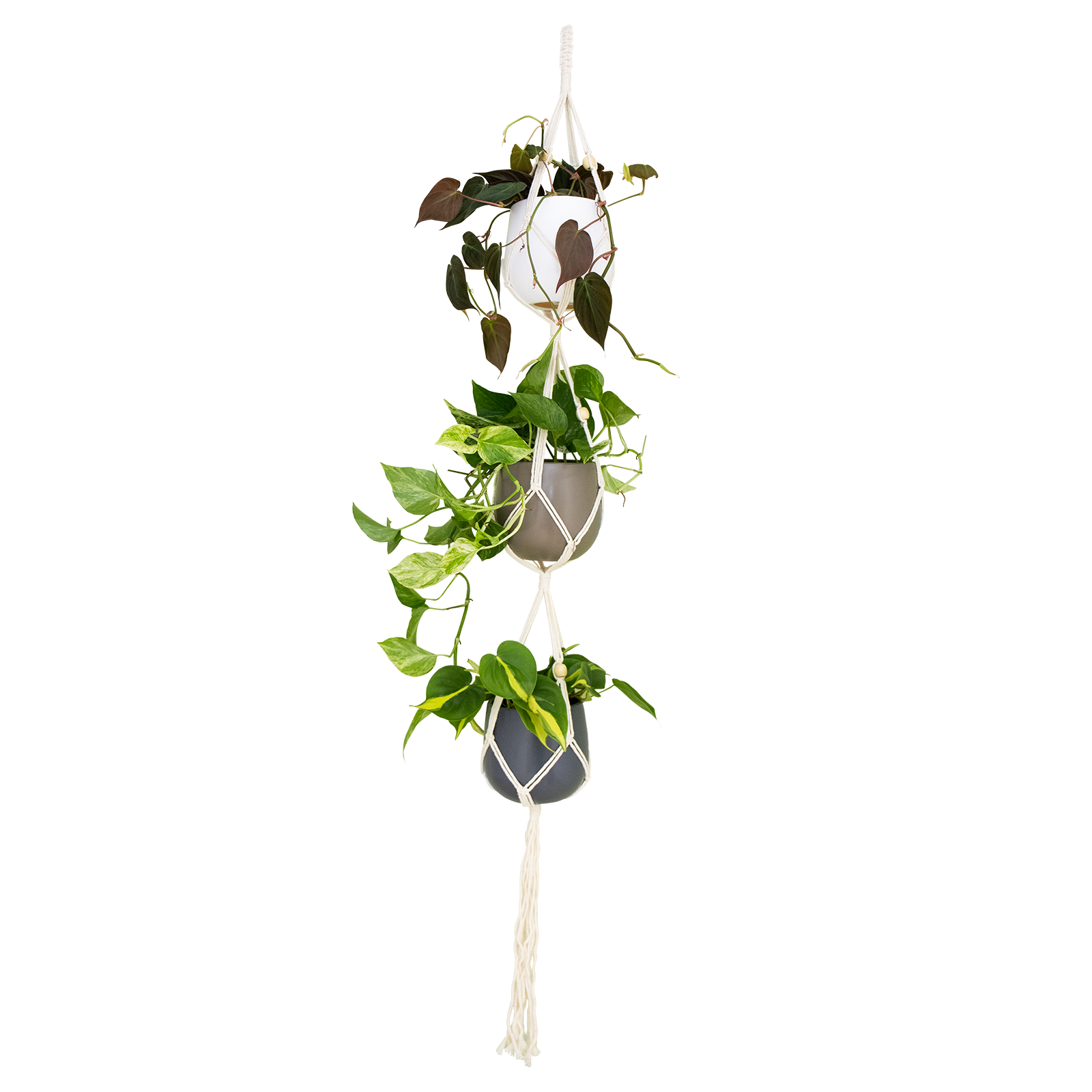