Installing a bovine-origin component. What are the critical considerations and procedures for a successful implementation?
This refers to the process of integrating a component derived from cattle into a larger system or structure. This could encompass a wide range of applications, from incorporating hides into architectural designs to employing specific biological products in industrial processes. The specific nature of the "component" and the associated technical specifications would significantly influence the implementation procedures.
The importance of meticulous installation procedures is paramount for achieving optimal performance and long-term functionality. Proper installation minimizes the risk of complications, ensuring the integrity of the component's inherent properties, and maximizing its overall contribution to the system. Potential benefits may include enhanced structural support, improved efficiency in production processes, or the creation of novel materials with unique qualities. The historical context of this practice might vary considerably depending on the specific application. In certain agricultural contexts, similar processes for integrating bovine materials have long been practiced. More recent applications might involve integrating advanced biological technologies.
Moving forward, let's delve into the key factors that determine successful installation. Topics to be addressed include selection of appropriate materials, safety protocols during the installation process, and post-installation maintenance procedures.
Bovine Component Installation
Successful bovine component installation hinges on meticulous attention to detail and a comprehensive understanding of relevant procedures. Omission of any key aspect can compromise the integrity and effectiveness of the final outcome.
- Material Selection
- Compatibility Analysis
- Safety Protocols
- Calibration Procedures
- Thorough Documentation
- Quality Control
- Process Optimization
- Environmental Factors
The eight aspects are interconnected. Material selection must consider compatibility with the surrounding system. Calibration procedures ensure accurate integration. Safety protocols prevent accidents and damage. Thorough documentation aids future maintenance and troubleshooting. Quality control, process optimization, and environmental factors are critical in guaranteeing lasting, reliable performance, as seen in large-scale agricultural machinery installations. Precise bovine component integration often demands adherence to stringent standards and protocols, as in bio-medical engineering procedures. Careful consideration of these aspects minimizes risks and maximizes the component's value in its application.
1. Material Selection
Accurate material selection is fundamental to successful bovine component installation. The properties of the chosen material directly impact the integrity, performance, and longevity of the integrated component. Appropriate selection avoids issues like incompatibility, degradation, or structural failure, thereby ensuring the intended functionality and minimizing potential risks.
- Compatibility and Interfacial Interactions
Material compatibility is crucial. Incompatible materials can lead to corrosion, degradation, or weakened structural integrity. Consideration must be given to factors like chemical reactivity, thermal expansion coefficients, and potential for erosion or fracturing. Examples include using a material resistant to the specific chemicals encountered in the surrounding environment or selecting materials with appropriate tensile strength to withstand anticipated stresses. Failing to account for such interactions could result in premature component failure or degradation.
- Mechanical Properties
The mechanical properties of the selected material are critical. Factors like tensile strength, yield strength, and elasticity determine the component's ability to withstand stresses and strains encountered during operation and over its lifespan. Material selection must align with anticipated loading conditions and potential environmental exposures. Selecting an inadequate material might lead to fractures, excessive deformation, or catastrophic failure, potentially causing significant damage or stoppage of operation. This is particularly critical in engineering applications.
- Cost-Effectiveness and Availability
Material selection must consider economic factors. The chosen material should be cost-effective, readily available, and meet quality standards. Balancing cost-effectiveness with performance and durability is essential. Excessive cost without improved performance or durability is counterproductive. This often necessitates a trade-off analysis to select the most suitable material for the specific application and budget.
- Environmental Considerations
Environmental factors play a role in material degradation. Materials should exhibit resistance to corrosion, weathering, or degradation due to moisture, chemicals, or temperature variations. This selection is crucial for long-term reliability and reduces the need for costly maintenance and replacement. Failure to consider these environmental aspects can lead to accelerated deterioration of the component, potentially impacting its operational life.
In conclusion, selecting the right materials is a crucial step in successful bovine component installation. Careful evaluation of compatibility, mechanical properties, cost, and environmental factors ensures the component's optimal function, longevity, and safety. An ill-considered material selection can lead to significant problems, highlighting the importance of thorough analysis and adherence to established standards.
2. Compatibility Analysis
Compatibility analysis is an indispensable prerequisite for any bovine component installation. Successful integration depends critically on the seamless interaction between the component and the surrounding system. This analysis identifies potential issues arising from differences in materials, chemical properties, and structural integrity, ensuring a durable and functional outcome. Failure to adequately address compatibility can lead to significant problems, ranging from minor performance degradation to catastrophic failure.
- Material Compatibility
Assessing the chemical and physical compatibility of materials is paramount. Incompatible materials can lead to corrosion, degradation, or weakening of the component or its surroundings. This includes considering the possibility of galvanic corrosion, where dissimilar metals in contact can accelerate deterioration. In bovine component installation, this might involve selecting hides resistant to the environmental conditions of a specific application, or ensuring a biocompatible adhesive for attaching bovine-derived products.
- Structural Compatibility
Analyzing structural compatibility ensures the component aligns with the supporting system. Incompatible dimensions, tolerances, or load-bearing capacities can lead to structural weakness, stresses, or failure. This analysis might involve precise measurements to determine if a bovine hide can withstand a particular tensile force within a specific architectural design. Inconsistencies in material properties can lead to uneven strain distribution, creating stress points prone to fracture.
- Functional Compatibility
Functional compatibility assesses whether the component performs its intended role within the system. Incompatible interactions with other elements can cause unexpected or undesirable behaviors. This could include evaluating how a specific bovine-origin component affects the overall mechanical performance or chemical processes in a system. For example, evaluating how a component derived from bovine collagen affects the structural integrity of a material in a manufacturing process.
- Environmental Compatibility
Evaluating environmental compatibility is vital to predict long-term performance. Exposure to various environmentstemperature fluctuations, humidity levels, or specific chemicalscan impact the component's integrity and effectiveness. This could include evaluating how bovine hide will age and resist degradation in an outdoor environment or how components will perform in high-humidity settings.
Thorough compatibility analysis, encompassing material, structural, functional, and environmental considerations, forms a critical foundation for successful bovine component installation. A failure to conduct rigorous compatibility studies can lead to unforeseen issues, highlighting the need for meticulous planning and detailed analysis to ensure the intended performance and durability of the integrated component.
3. Safety Protocols
Safety protocols are integral to any bovine component installation. They define the procedures and precautions necessary to mitigate risks and prevent accidents during the process. This includes considerations for potential hazards associated with the material itself, handling procedures, and the surrounding environment. The importance of these protocols stems from the potential for injury or damage to personnel, equipment, or the surrounding environment. Failure to adhere to these protocols can result in costly delays, injuries, or even catastrophic system failure.
These protocols are not merely a theoretical construct but a practical necessity. Real-world examples illustrate the criticality of safety measures. Consider a scenario where bovine hide, used as a structural element, is improperly handled. Inadequate safety measures could lead to worker injuries due to slips or falls. Furthermore, improper handling during installation could compromise the structural integrity of the hide, leading to failures later on. Conversely, proper implementation of safety protocols, like using appropriate protective equipment or creating a designated safety zone, mitigates these risks and promotes a safe work environment. This is critical for the continued operational efficiency of installations involving animal-derived products. This includes not only the installation phase but ongoing maintenance and operation as well. The protocols must be adaptable and adaptable to the specific installation and environmental context.
In conclusion, safety protocols are not an add-on to bovine component installations; they are an intrinsic part of the process. Their implementation is paramount for minimizing risks, ensuring worker safety, and safeguarding the integrity of the installation itself. Adherence to established safety protocols translates to a more efficient, sustainable, and secure work environment.
4. Calibration Procedures
Accurate calibration procedures are essential components of bovine component installation. Precise measurements and adjustments are critical to ensuring proper function, safety, and longevity of the installed component. Errors in calibration can lead to compromised performance, potential safety hazards, and ultimately, costly repairs or replacements. The efficacy and reliability of the entire system depend heavily on the precision of these procedures.
- Dimensional Accuracy
Ensuring dimensional accuracy in bovine component installation is crucial. Inaccurate measurements can lead to misalignment, improper fit, and potentially compromised structural integrity. For example, a precisely calibrated bovine hide panel in a building's facade ensures structural soundness, preventing instability or leaks. Conversely, miscalibration might lead to weak joints, jeopardizing the structure's overall stability.
- Force and Load Calibration
Calibration of forces and loads is critical in applications involving bovine components subject to mechanical stress. Precise calibration of the load-bearing capacity of the component, such as a bovine ligament in an artificial joint replacement, ensures structural integrity and prevents catastrophic failure under load. Inadequate calibration can lead to premature breakage or deformation, negatively impacting the device's efficacy.
- Environmental Parameter Calibration
Calibration of environmental parameters, like temperature and humidity, is vital when incorporating bovine-derived components into systems sensitive to these factors. Precise calibration ensures consistent operation and prevents degradation or performance issues. For example, instruments calibrated to monitor temperature ensure the structural integrity of a bovine hide awning during extreme weather conditions. Inaccurate calibration could result in the hide's deterioration, leading to premature failure and safety risks.
- Mechanical Performance Calibration
Calibration of mechanical performance, such as tensile strength or elasticity of a bovine tendon used in a bio-mechanical device, is critical to anticipate the stresses it will withstand. Proper calibration ensures these components can meet expected performance standards. Incorrect calibration might result in premature failure or reduced operational capacity, impacting overall system reliability.
In summary, calibration procedures are integral to every stage of bovine component installation, from ensuring structural integrity to maintaining the component's intended function. Precise calibration is not just a technical requirement; it's a critical factor contributing to the safe, efficient, and reliable operation of systems incorporating bovine components.
5. Thorough Documentation
Thorough documentation is inextricably linked to the success of bovine component installations. Comprehensive documentation serves as a crucial reference for all phases of the installation process, from initial planning to ongoing maintenance. It acts as a repository of crucial information, ensuring consistency, facilitating troubleshooting, and enabling future modifications or expansions. Precise and detailed records are essential for maintaining the integrity and reliability of the installation, minimizing potential complications and reducing the likelihood of errors in the process. Effective documentation safeguards against ambiguities and clarifies procedures, ultimately fostering a more efficient and sustainable operation.
The practical significance of meticulous documentation is evident in various contexts. Consider a large-scale agricultural project involving the installation of bovine-derived structural elements in a livestock facility. Detailed documentation, including blueprints, material specifications, installation protocols, and calibration records, would be essential. In the event of a subsequent issue, this record could quickly guide maintenance teams, enabling the identification of the exact cause and facilitating appropriate remedial action. Similarly, in a biomedical research setting, documentation of bovine component integration into a device or system is paramount for reproducibility, allowing researchers to precisely replicate procedures and facilitating knowledge transfer across research groups. A clear, detailed documentation trail minimizes ambiguity and allows for consistent and verifiable data collection and analysis. This demonstrably contributes to the scientific validity of the research process. In both agricultural and biomedical contexts, efficient documentation contributes to overall project success, avoiding costly delays and ensuring effective performance.
In conclusion, thorough documentation is an indispensable component of any bovine component installation. It empowers effective management, facilitates issue resolution, enhances reproducibility, and promotes long-term sustainability. The ability to consult accurate, detailed records throughout the life cycle of an installation significantly improves its efficiency and cost-effectiveness, while enhancing the reliability of the entire process. Without thorough documentation, the installation is vulnerable to errors, delays, and future complications, making clear records a cornerstone of successful project execution.
6. Quality Control
Quality control (QC) is inextricably linked to successful bovine component installation (bov install). Rigorous QC procedures, implemented throughout the installation process, directly impact the integrity, safety, and long-term performance of the integrated component. These procedures encompass every stage, from material selection and handling to final testing and verification. QC ensures the component meets predetermined standards and specifications, preventing potential failures and ensuring reliability. The application of robust QC protocols reduces the likelihood of costly repairs, replacements, or project delays.
The importance of QC in bov install is evident in diverse applications. In agricultural settings, QC processes ensure structural integrity of bovine-derived materials used in livestock housing. Defective materials or poorly installed components can lead to costly repairs, compromised animal well-being, and even structural collapses. Likewise, in biomedical engineering, QC procedures are indispensable for ensuring the biocompatibility and functionality of bovine-derived components in implants or prosthetics. Failing to adhere to stringent QC protocols can have severe consequences for patient safety and treatment effectiveness. In architectural applications utilizing bovine hides, meticulous QC ensures the material's durability and resistance to environmental factors like weathering, guaranteeing the longevity of the finished structure. The avoidance of defects at every stage translates to a more efficient, safer, and sustainable operation. Failure to implement robust quality control standards can have significant implications in each scenario.
In summary, quality control is not a secondary consideration but a fundamental aspect of bovine component installation. Its integration throughout the entire installation process is critical to ensure the integrity, safety, and reliable performance of the final product. Strict adherence to QC protocols mitigates risks, enhances the longevity of the installed component, and ultimately contributes to the success of the overall project. By prioritizing QC, stakeholders can avoid costly errors, prevent potential safety hazards, and ensure the long-term reliability of the integration.
7. Process Optimization
Optimizing processes related to bovine component installation (bov install) is crucial for achieving efficiency, cost-effectiveness, and safety. Improved processes reduce waste, minimize errors, and enhance the overall reliability of the installation. Effective optimization leverages knowledge of the specific installation parameters to create streamlined workflows and mitigate risks, maximizing the value derived from the component.
- Material Handling and Storage
Efficient handling and storage of bovine components are critical. Improper storage can lead to deterioration or damage, impacting the component's integrity and requiring costly replacements. Optimized handling procedures, such as using specialized equipment for delicate components, and implementing controlled storage environments (temperature, humidity, and light control), minimize deterioration and maximize material longevity. This careful handling directly correlates with the quality and effectiveness of the final installation.
- Installation Sequencing and Timing
Strategic sequencing of installation steps significantly impacts the overall process. Optimizing the order of operations, considering dependencies between steps, and defining precise timing reduce errors, minimize downtime, and expedite the installation process. This approach minimizes the risks of incompatibility issues between components and ensures the final structure meets its design specifications. For instance, carefully staged and controlled installation sequencing prevents mechanical stress on adjacent structures.
- Personnel Training and Skill Development
Trained and skilled personnel are paramount. Comprehensive training programs focused on the specific installation techniques and safety protocols related to bovine components are essential. Proficient personnel, familiar with the procedures and potential hazards, minimize errors and ensure the installation process adheres to the established standards. This not only improves safety but also minimizes delays and associated costs arising from errors or rework. A well-trained workforce ensures a consistent, high-quality installation.
- Quality Assurance and Control Protocols
Integrated quality assurance (QA) and control (QC) protocols are essential to optimization. Implementing standardized testing methods at each stage of the installation process, for example, verifying the structural integrity or ensuring compliance with biocompatibility standards, guarantees high quality. Effective QC protocols lead to the detection and correction of errors before they impact the final installation, reducing rework and improving the overall quality of the final product. These systems minimize risks related to subpar quality and ensure cost-effective completion.
Optimizing the processes involved in bovine component installation leads to not only more efficient workflows but also a higher quality final product. By focusing on material handling, installation sequencing, personnel training, and quality control protocols, organizations can significantly reduce costs, improve safety, and enhance the long-term reliability of their bovine component installations.
8. Environmental Factors
Environmental factors exert significant influence on bovine component installations. Considerations encompassing temperature fluctuations, humidity levels, and exposure to specific chemicals or microorganisms are critical to ensuring the long-term integrity and performance of the integrated component. Ignoring these environmental aspects can lead to premature degradation, compromised functionality, and potential safety risks. Effective management of environmental conditions is therefore integral to the success of any bovine component installation.
- Temperature Fluctuations
Variations in temperature can induce stress and strain within the component, potentially leading to dimensional changes, cracks, or other structural failures. This is particularly critical in installations exposed to extreme temperatures or rapid temperature changes. For example, a bovine-derived structural element in an outdoor environment might experience significant degradation due to repeated freezing and thawing cycles. Conversely, controlled temperature environments can extend the life of a component by minimizing these stresses.
- Humidity Levels
Elevated humidity can foster microbial growth or accelerate corrosion processes, leading to degradation of the component and its surrounding materials. Examples include bovine hides used in architectural applications, where moisture can induce mold or mildew, compromising the integrity of the structure. Conversely, proper humidity control can maintain the structural integrity and aesthetic appeal of such installations.
- Exposure to Chemicals
Specific chemicals in the surrounding environment can induce corrosion or degradation of bovine materials. For instance, the presence of certain acids or alkalis can negatively affect bovine hides used in construction, leading to faster deterioration. Proper material selection and protective coatings can help mitigate these risks. Identifying and addressing potential chemical exposure is vital to extending the life and functionality of any bovine component installation.
- Microorganism Exposure
Exposure to microorganisms can accelerate deterioration of the component. Certain bacteria or fungi can break down the material, reducing its strength and impacting its ability to perform its designated function. For example, bovine-derived biomaterials used in medical implants need rigorous sterilization to prevent infection and premature degradation from microbial growth. Prevention strategies and appropriate handling are necessary to mitigate the risks associated with exposure to microorganisms in any bovine installation.
Careful consideration of environmental factors during the design, installation, and ongoing maintenance of bovine component installations is crucial. Addressing temperature variations, humidity control, chemical exposure, and microbial presence can substantially extend the life span and reliability of these installations, ensuring their optimal performance within diverse applications.
Frequently Asked Questions about Bovine Component Installation
This section addresses common inquiries regarding the installation of bovine-derived components. These questions cover crucial aspects of the process, from material selection to environmental considerations.
Question 1: What are the key considerations when selecting materials for a bovine component installation?
Material selection prioritizes compatibility, structural integrity, and cost-effectiveness. The chosen material must be chemically compatible with the surrounding environment and possess adequate mechanical properties to withstand anticipated stresses. Cost-effectiveness and availability are also important factors, balancing practicality with desired performance.
Question 2: How do safety protocols safeguard installations incorporating bovine components?
Robust safety protocols are essential to mitigate risks throughout the installation process. These protocols cover handling procedures for the bovine component, personal protective equipment, and established emergency procedures. Adherence to safety protocols minimizes potential harm to personnel, equipment, and the environment.
Question 3: What environmental factors influence bovine component installations?
Environmental factors such as temperature fluctuations, humidity levels, and exposure to chemicals directly impact the long-term integrity of the installation. Material selection and installation techniques should consider these factors to ensure the component's continued performance and avoid premature degradation.
Question 4: How crucial is meticulous documentation in bovine component installation?
Thorough documentation is critical for successful installation. Comprehensive records allow for easy troubleshooting, facilitate future maintenance, and provide a historical record of the installation process. Precise documentation ensures consistent execution of procedures and simplifies the identification of potential issues.
Question 5: What role does calibration play in the process?
Accurate calibration is vital for precise measurements and adjustments. Calibration ensures accurate integration of the bovine component into the overall system. This process covers dimensional accuracy, load capacity, and environmental parameters, ensuring safe and reliable performance throughout the component's operational lifespan.
Understanding these key factors ensures successful bovine component installations, prioritizing safety, reliability, and long-term performance.
Moving forward, let's explore specific case studies of bovine component installations in various industries.
Conclusion
Bovine component installation (bov install) necessitates a multifaceted approach encompassing meticulous material selection, rigorous safety protocols, precise calibration procedures, and comprehensive documentation. Optimizing installation processes, alongside careful consideration of environmental factors and quality control measures, are paramount for achieving successful integration and long-term reliability. The successful implementation of bov install hinges on the seamless interaction between the component and the surrounding system, minimizing risks associated with incompatibility and maximizing the component's functional contribution. Thorough understanding of the material properties, environmental conditions, and potential hazards is essential to ensure both safety and optimal performance throughout the installation's lifespan.
The discussed aspects underscore the importance of a holistic approach to bov install, extending beyond the physical act of integration. Careful planning, adherence to established standards, and proactive risk mitigation are critical for long-term success. Future advancements in this field will likely focus on further optimizing installation procedures, incorporating novel materials with enhanced properties, and developing predictive models to anticipate and mitigate potential challenges. Continued research and development in these areas will be crucial for ensuring the safety, efficiency, and broader applicability of bovine components in diverse industrial and technological contexts.
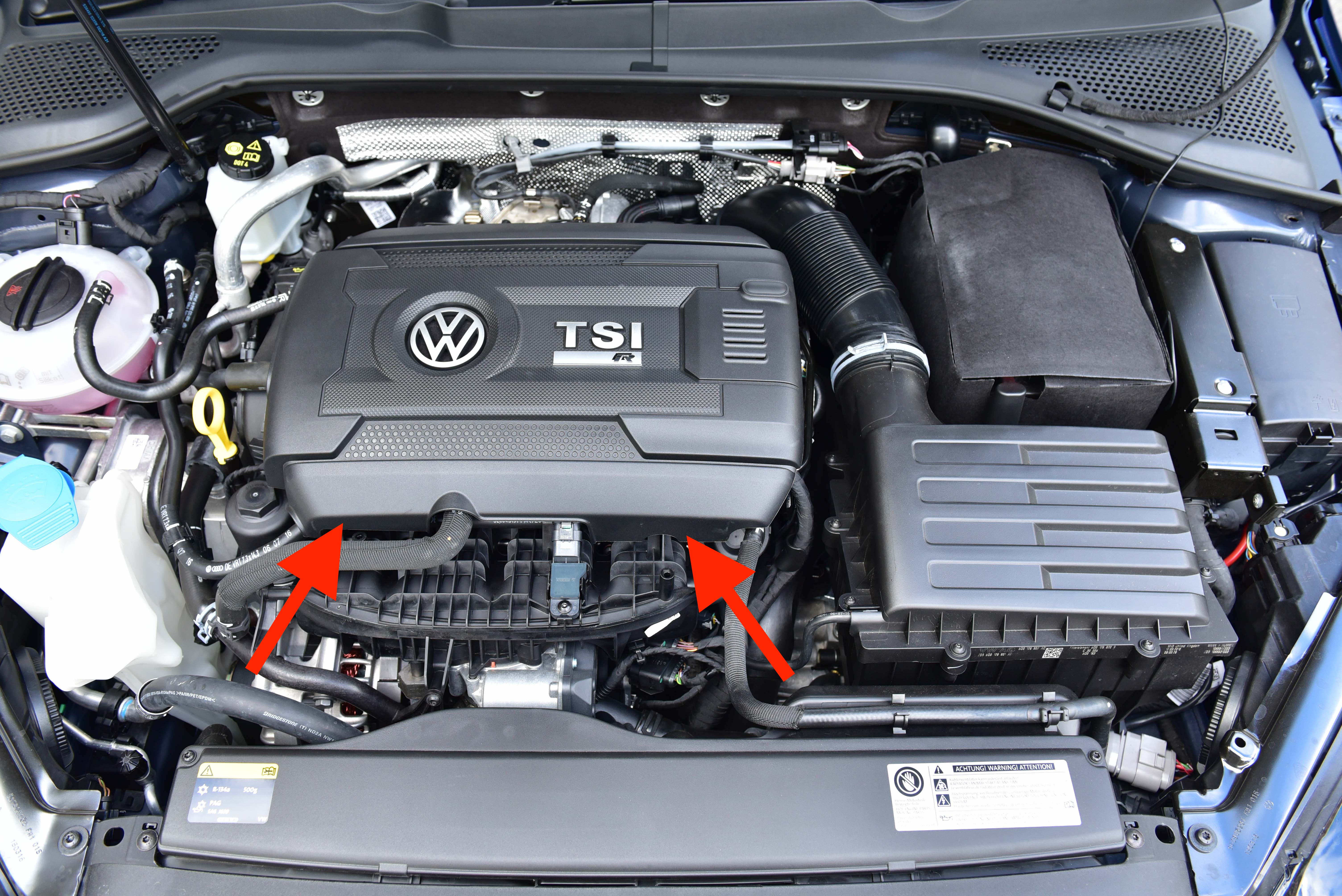

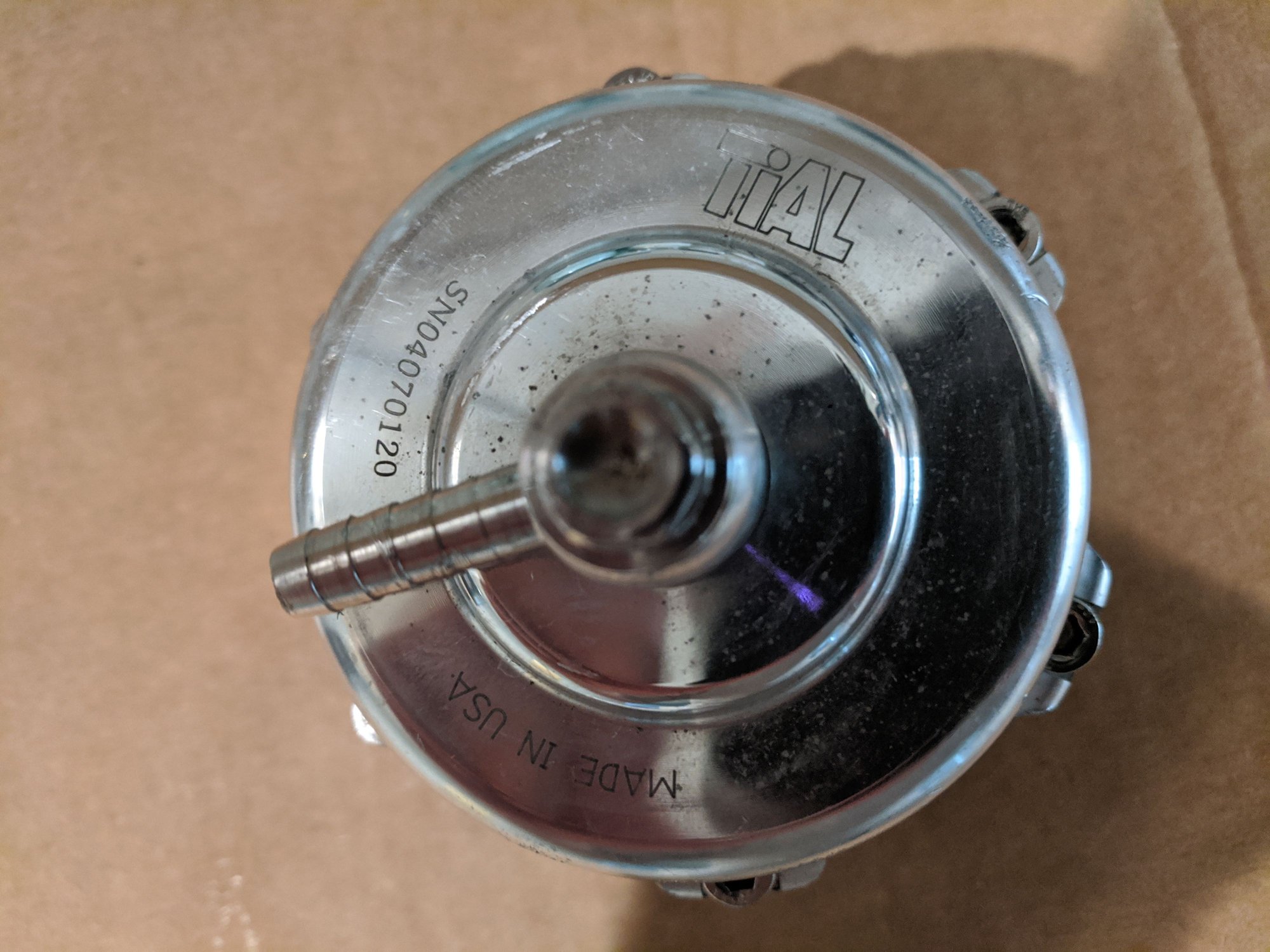