What are these ubiquitous small spheres, and why are they so crucial to modern manufacturing?
These small, often translucent, spherical particles are a fundamental component in the production of countless plastic products. They are typically manufactured from polymers, such as polyethylene (PE) or polypropylene (PP), and represent a concentrated form of plastic resin. These tiny beads, often measured in millimeters, are then molded, extruded, or otherwise shaped into the vast array of plastic items we encounter dailyfrom bottles and packaging to toys and automotive parts.
These pellets play a vital role in the global plastic industry. Their standardized size and consistency allow for efficient processing in manufacturing facilities. This consistency, derived from strict manufacturing controls, ensures predictable material properties in the final products. Moreover, the use of pellets is often more economical and resource-efficient than processing raw polymer directly. Historical context reveals a strong correlation between the development of pellet-based plastic manufacturing and the rise of modern plastics industries. The ability to efficiently produce and process plastic in this form has been crucial for the widespread adoption of plastic materials in the 20th and 21st centuries.
To better understand their multifaceted applications and production, let's delve into the process of plastic pellet creation, its global trade, and the environmental considerations that accompany this ubiquitous material.
Plastic Pellets
Plastic pellets, a fundamental component in modern manufacturing, hold immense significance in the plastics industry. Their production, properties, and applications are key considerations.
- Raw materials
- Manufacturing process
- Consistent size
- Versatile shapes
- Economic efficiency
- Recycling potential
- Environmental impact
- Global trade
Plastic pellets, derived from various polymers, undergo precise manufacturing processes. Their uniform size facilitates efficient processing into diverse forms. This efficiency and versatility contribute to the widespread use of plastic in products. The ease of recycling, though debated, holds promise for sustainability. Environmental impact, however, is a growing concern, raising questions about waste management and the broader implications of plastic production. Global trade in plastic pellets is extensive, demonstrating the ubiquitous nature of this material. These interconnected aspects highlight the complexity and significance of plastic pellets in the modern world.
1. Raw Materials
The production of plastic pellets hinges critically on the selection and processing of raw materials. These materials form the foundation of the entire process, influencing the properties, cost, and environmental footprint of the final product. Understanding these components is essential for evaluating the sustainability and efficiency of plastic pellet manufacturing.
- Polymer Sources
A wide spectrum of polymers forms the basis for plastic pellets. These include polyethylene (PE), polypropylene (PP), polystyrene (PS), and many others. The specific polymer choice dictates the eventual characteristics of the pellet and the resulting plastic product. Natural resources like petroleum and natural gas are primary sources for many polymers. Alternative, renewable feedstocks are increasingly investigated as a sustainable response to fossil fuel dependence. The raw materials sourcing process impacts the economic viability of plastic production.
- Additives and Fillers
Pellets often incorporate additives to enhance properties like color, impact resistance, UV stability, or flame retardancy. Fillers, such as minerals or recycled plastic, are also commonly added to reduce costs or improve environmental performance. The selection and quantity of these additives significantly impact the resulting properties of the pellets, and ultimately, the products they are used to manufacture. Careful consideration of these added components is critical for achieving desired properties and for meeting regulatory requirements.
- Processing Techniques
The conversion of raw materials into plastic pellets involves various processing steps. These include polymerization reactions, refining processes, and blending operations. The specific techniques used influence the purity, consistency, and cost-effectiveness of the pellets. Different processing methods result in different pellet qualities and manufacturing costs. Understanding these processing details provides insight into the complexity of the manufacturing cycle.
- Sustainability Considerations
The sourcing and processing of raw materials play a crucial role in the sustainability of plastic pellet production. The environmental impact of extracting fossil fuels, for example, is a major concern. The use of renewable resources, and the efficient use of existing resources are essential for mitigating negative environmental effects. Recycled polymers also serve as a critical raw material, reducing reliance on virgin resources, and lowering the environmental impact of plastic pellet production. The sustainability of raw materials is closely linked to the wider issue of responsible plastic consumption and management.
In summary, the raw materials underpin the entire plastic pellet production process. Selection and processing of these materials directly influence the properties of the resultant pellets. A crucial aspect of sustainable practices involves mindful selection of materials to reduce environmental impact. This highlights the necessity to consider the entire lifecycle of plastics from raw material sourcing to final product disposal.
2. Manufacturing Process
The manufacturing process of plastic pellets is a crucial element in the production chain. It dictates the quality, consistency, and efficiency of the resulting pellets, significantly impacting the properties and applications of the finished plastic products. This process's nuances are critical to understand for both production optimization and environmental considerations.
- Polymer Extrusion
The extrusion process is central. Molten polymer resins, sourced from various feedstocks, are forced through a die, shaping the material into a continuous strand. This strand is then cut into pellets of uniform size and shape, ensuring consistency in the final product. Different extrusion techniques, including variations in temperature control and pressure application, are employed depending on the specific polymer type and desired pellet characteristics. The speed and precision of this step significantly affect the efficiency of the entire production line.
- Granulation and Sizing
Post-extrusion, the continuous strand is often granulated into smaller pieces. Careful sizing and shaping of these pellets are critical. Precise control over pellet dimensions is crucial for efficient downstream processing. This step ensures that pellets are uniform in size and shape, facilitating efficient handling and preventing issues in molding or other manufacturing stages. Variations in pellet size and shape are vital for specific applications.
- Drying and Cooling
The molten polymer, even after extrusion, requires precise temperature control. This is critical to avoid degradation or unintended changes in physical properties. Appropriate cooling and drying procedures are essential for maintaining the integrity of the pellets and preventing moisture absorption. The speed and accuracy of drying and cooling are important factors in maximizing output and maintaining quality.
- Quality Control and Sorting
Rigorous quality control is vital throughout the process to identify any defects or inconsistencies. Automated systems or visual inspections often are used to evaluate pellet size, shape, color, and potential contamination. Sorting separates acceptable from flawed pellets, ensuring a consistent product and maintaining high quality in the end product. These quality control measures safeguard the consistency and reliability of the resulting pellets. Consistent processes translate to consistency in the end product.
The manufacturing process for plastic pellets is complex, and the various stages are tightly interconnected. Control at each step ensures uniform quality and facilitates the efficient production of plastics. Understanding the intricacies of these processes is paramount in optimizing production, minimizing waste, and controlling quality throughout the supply chain.
3. Consistent Size
Uniformity in the size of plastic pellets is fundamental to the efficient operation of downstream manufacturing processes. Precise control over pellet dimensions is crucial for ensuring optimal processing in subsequent stages, from molding and extrusion to injection and blow molding. The consistent size of the pellets dictates the predictable flow, melt characteristics, and ultimately the final properties of the manufactured products.
- Predictable Flow and Melt Properties
Uniform pellet size ensures consistent flow rates during processing. This consistency is paramount for maintaining stable melt temperatures and viscosity. Varied pellet sizes can lead to inconsistent melt flow, potentially causing variations in the final product's properties, including its strength, flexibility, and dimensional accuracy. Predictable melt behavior minimizes defects and allows for precise control in the manufacturing processes.
- Efficient Processing and Reduced Waste
Consistent pellet size allows for more efficient and predictable processing through machinery. Machines designed for a specific pellet size can operate at optimal speed and output, maximizing throughput while minimizing processing time. Uniformity eliminates the need for excessive adjustments, preventing material buildup and reducing the risk of product quality inconsistencies. Inconsistent sizes lead to processing inefficiencies and often result in excess scrap material.
- Improved Product Quality and Consistency
Precise dimensions contribute significantly to the reproducibility and quality of the final plastic product. Variations in pellet sizes can lead to inconsistencies in the plastic's properties across different batches or even within a single batch. A consistent pellet size translates into products with uniform characteristics, meeting quality standards across different products. This reliability reduces costly rework and ensures predictable performance in diverse end-use applications.
- Optimization of Equipment Performance
Consistent pellet size optimizes the performance of downstream machinery. Precisely sized pellets are designed to fit the mechanisms of extruders, injection molding machines, and blow molding systems. Equipment tailored for specific sizes will operate most efficiently, thus increasing the overall output of the production line. Inconsistent pellet size can lead to premature equipment wear and tear or require costly adjustments in manufacturing equipment, thus increasing production costs.
In summary, consistent size in plastic pellets is integral to the entire production process. The uniform dimensions contribute directly to predictable processing, optimized equipment performance, improved product quality, and reduced waste. Maintaining this consistency throughout the supply chain from raw materials to finished product is critical for achieving efficiency and reliability in the plastic manufacturing industry.
4. Versatile Shapes
The ability to mold plastic pellets into diverse shapes is a key driver of the versatility and widespread application of plastics. This inherent adaptability stems from the inherent malleability of polymers when heated, allowing for a wide range of designs and configurations. The shaping of plastic pellets isn't a separate process but an integral part of the manufacturing process itself. Early stages of pellet production often involve shaping the molten polymer into a continuous strand, which is then cut and sized into pellets. Subsequent processing steps further define the form of the final product.
The versatility of shapes, in turn, leads to the production of a vast array of products. Consider the intricate designs of toys, the seamless curves of automotive parts, or the precise geometry of medical implants. These varied shapes directly reflect the adaptability of the original plastic pellets. The shapes are not arbitrary; they are meticulously designed to meet specific functional requirements. The contours of containers, for instance, impact their capacity and resilience. The complex geometry of a car's body panels reflects both aesthetic appeal and engineering considerations for strength and aerodynamics. Even seemingly simple shapes, like the uniform cylindrical form of a plastic water bottle, are carefully optimized for function and efficiency. The variety underscores the profound impact of pellet shaping on the final products and their practical applications.
Understanding the connection between versatile shapes and plastic pellets is critical for both product design and manufacturing processes. Precise control over the shaping process is essential to meet the specifications of various end-products. This understanding also illuminates the material's adaptability, enabling the creation of customized forms to fulfill particular needs. Further, the knowledge of how shape affects material properties is crucial for optimizing designs for strength, flexibility, and longevity. Moreover, understanding this connection can aid in the design of more efficient manufacturing processes. This understanding, ultimately, drives the ability to tailor plastic solutions for a multitude of applications.
5. Economic Efficiency
Economic efficiency in plastic pellet production is a crucial factor driving the industry's viability and competitiveness. Cost-effectiveness at every stage, from raw material acquisition to final product distribution, significantly impacts the overall market price and consumer accessibility. Optimizing resource utilization, minimizing waste, and streamlining production processes all contribute to this efficiency. Efficient production methods translate directly into lower manufacturing costs, enabling competitive pricing for plastic products and wider consumer adoption.
Several factors contribute to economic efficiency in the plastic pellet industry. Minimizing raw material costs through strategic sourcing and negotiations is critical. Efficient processing techniques, including optimized extrusion parameters and minimized energy consumption, directly reduce production costs. Waste reduction, by ensuring accurate sizing and minimal scrap generation, lowers material expenditures and maximizes the utilization of raw resources. Furthermore, leveraging economies of scale by producing larger quantities of pellets enhances efficiency and lowers costs per unit. This leads to competitive pricing in the plastic market. Real-world examples include manufacturing plants adopting advanced automation to reduce labor costs while maintaining high output. Another instance is companies switching to renewable energy sources to lower production energy expenses, a positive example of sustainable practices intertwined with economic efficiency.
Understanding the connection between economic efficiency and plastic pellets is vital for both industry participants and policymakers. Optimized production processes translate to lower prices for end-users, increasing accessibility to plastic goods. Understanding cost structures and efficient operational strategies helps manufacturers maintain profitability and compete effectively in a global market. The demand for sustainable solutions encourages manufacturers to explore cost-effective strategies that minimize environmental impact. Conversely, inefficient production methods can lead to higher prices, potentially reducing consumer demand and impacting overall market competitiveness. This underscores the importance of embracing innovation and responsible production practices for long-term economic sustainability in the plastic pellet industry.
6. Recycling Potential
The recycling potential of plastic pellets is a complex issue, directly tied to the inherent characteristics of the polymers from which they are derived. The recyclability of plastic pellets isn't an inherent property but depends on several factors, including the type of polymer, the processing conditions, and the presence of contaminants. The diverse range of polymers used in pellet production significantly affects the potential for successful recycling. Not all plastics are easily recycled, and this complexity necessitates careful consideration of materials composition during pellet manufacturing.
Successful recycling of plastic pellets relies on maintaining material purity. Contamination during processing can significantly reduce the quality of recycled material. Moreover, the varied types of plastic within a batch affect the sorting process, which in turn impacts the ultimate recycling success rate. The market for recycled plastics is often segmented by polymer type, affecting the demand for specific types of recycled pellets. This necessitates efficient sorting and processing techniques to ensure that recycled pellets meet the standards required for different applications. Real-world examples demonstrate the importance of stringent quality control. Facilities struggling with mixed plastic batches often find it difficult to convert recycled pellets into useful products due to the inherent variations and contamination in the source material. Conversely, facilities that employ precise sorting and processing techniques can obtain more consistent and higher-quality recycled pellets, leading to more viable applications. The ability to recycle specific types of pellets is tied to the presence of suitable processing infrastructure and market demand for the recycled material.
Understanding the recycling potential of plastic pellets is crucial for responsible plastic management. This knowledge aids in optimizing production processes to enhance material recyclability, enabling the development of more sustainable plastics solutions. The need for effective sorting, processing, and quality control measures during plastic pellet recycling is paramount to ensuring a viable market for recycled materials. This also encourages manufacturers to incorporate recyclable materials into their product designs, contributing to a circular economy. Challenges persist, including the lack of standardized recycling processes and inconsistent quality control across different facilities. Continued research and innovation are critical for overcoming these challenges and maximizing the recycling potential of plastic pellets. The efficient processing of recycled pellets is critical for a broader adoption of recycled plastics.
7. Environmental Impact
The environmental impact of plastic pellets is multifaceted and significant, extending far beyond the manufacturing process itself. The production of these pellets, often reliant on fossil fuels, contributes to greenhouse gas emissions. The sheer volume of plastic produced globally, with a substantial portion destined for single-use products, directly impacts waste management systems. This material's persistence in the environment, and the difficulties inherent in its decomposition, presents a crucial concern, impacting ecosystems, wildlife, and human health. The ubiquitous nature of plastic pellets underscores their importance in evaluating the environmental footprint of the entire plastic lifecycle.
The extraction of raw materials for plastic production, a vital stage in the pellet creation, often involves environmental degradation. The mining for minerals used in additives or fillers can lead to habitat destruction, soil erosion, and water pollution. The energy intensive processes of refining polymers and manufacturing pellets contribute substantial amounts of carbon emissions into the atmosphere. Furthermore, the inherent persistence of plastic, even in fragmented pellet form, contributes to plastic pollution. Microplastic fragments originating from the breakdown of these pellets have been found in vast stretches of oceans, harming marine life and potentially entering the food chain. The sheer quantity of plastic pellets used globally highlights the critical importance of sustainable production and management practices in mitigating these adverse environmental impacts.
Understanding the environmental impact of plastic pellets is crucial for developing more sustainable solutions. This necessitates evaluating the entire lifecycle of these materials, from resource extraction to final disposal. Manufacturers and policymakers must explore alternative materials, promote the use of recycled content, and implement responsible waste management strategies. The transition to a circular economy model, where plastic is reused and recycled, is essential to minimize the environmental footprint of plastic pellets. Real-world examples, such as companies actively implementing sustainable practices in their production lines, show that significant strides can be made to reduce pollution and promote environmental responsibility. This understanding is vital to ensure the long-term sustainability of the plastics industry and the well-being of the planet.
8. Global Trade
The global trade of plastic pellets is a complex and significant aspect of the plastics industry. The movement of these materials across international borders is driven by a multitude of factors, including production capacity, market demand, and economic considerations. Understanding this global trade is crucial for comprehending the intricacies of the plastic industry and its environmental impact. Fluctuations in global trade can influence prices, availability, and the overall market dynamics of plastic pellets.
Several factors contribute to the extensive global trade in plastic pellets. Nations with robust manufacturing capabilities often export pellets to regions with higher demand but potentially limited domestic production. Market demand, influenced by consumer trends, industrial growth, and economic conditions, drives the flow of pellets between nations. Economic incentives, such as lower labor costs or favorable tax policies in certain regions, can also attract the production and subsequent export of plastic pellets. The global trade landscape is dynamic, influenced by geopolitical events, trade agreements, and environmental regulations, which can affect pricing and availability. Real-world examples include countries specializing in specific types of plastic production, exporting pellets to other nations for use in various downstream applications. Additionally, the presence of large-scale manufacturing hubs often dictates trade routes and influences the quantity of pellets traded internationally.
The understanding of global trade in plastic pellets is vital for several reasons. It highlights the interconnected nature of global industries, demonstrating how production in one region can directly impact markets and consumption patterns in others. This understanding is important for policymakers in managing resource allocation and environmental policies. Companies involved in the production and distribution of plastic pellets must carefully monitor and adapt to these international trade fluctuations to maintain profitability and market share. For instance, understanding the global supply chain allows companies to anticipate price changes and respond appropriately, ensuring sustainability and profitability. Finally, this knowledge is crucial for comprehending the broader impact of plastic consumption, waste management, and environmental policies, as the global trade network directly influences the flow of plastic materials and products across the world.
Frequently Asked Questions About Plastic Pellets
This section addresses common inquiries regarding plastic pellets, encompassing their production, use, and environmental impact. Accurate information is presented to promote informed understanding.
Question 1: What are plastic pellets, and what are they used for?
Plastic pellets are small, often translucent spheres composed of polymers like polyethylene or polypropylene. They represent a concentrated form of plastic resin. These pellets serve as the fundamental building blocks for a wide array of plastic products, from packaging and bottles to toys and automotive parts. The consistent size and form allow for efficient processing into diverse shapes and sizes required by various manufacturing processes.
Question 2: What are the primary raw materials used in plastic pellet production?
Common raw materials include petroleum and natural gas, which are used to create many polymers. Alternative, renewable feedstocks are increasingly investigated as a sustainable solution. Additives and fillers, like minerals or recycled plastics, are also frequently incorporated to enhance specific properties or reduce costs.
Question 3: How does the manufacturing process for plastic pellets work?
The process typically involves extrusion, where molten polymer is forced through a die to form a continuous strand. This strand is then granulated and sized into uniform pellets. Critical steps include drying and cooling to maintain pellet integrity and quality control to ensure uniformity.
Question 4: What are the environmental concerns related to plastic pellets?
The production process can contribute to greenhouse gas emissions, and the vast quantities of plastic pellets used globally contribute to plastic pollution. The persistence of plastics, and resulting microplastics, in the environment poses risks to ecosystems and wildlife. Efficient recycling and sustainable production practices are crucial to mitigate these impacts.
Question 5: Are there sustainable alternatives to traditional plastic pellets?
Efforts to develop sustainable alternatives to traditional plastic pellets are ongoing. These include bio-based polymers derived from renewable resources and innovative recycling technologies. Continuous research aims to reduce reliance on fossil fuels and minimize environmental impacts associated with plastic production.
Understanding the lifecycle of plastic pellets, from raw material sourcing to end-product disposal, is key to addressing associated environmental concerns. This includes effective waste management, promotion of responsible plastic consumption, and continuous development of sustainable alternatives.
Further exploration of individual production steps, material composition, and market dynamics would provide a more thorough understanding.
Conclusion
Plastic pellets are a fundamental component in modern manufacturing, facilitating the production of a vast array of plastic products. The process, from raw material sourcing to the finished product, involves complex steps with diverse environmental implications. Key aspects explored include the importance of consistent pellet size for efficient downstream processing, the versatility of shapes achievable with pellets, the economic considerations driving production, and the crucial role of recycling potential in mitigating environmental impact. The global trade network for plastic pellets further underscores the interconnectedness of global markets and production chains. Furthermore, the significant environmental impact of plastic pellet production, from resource extraction to plastic pollution, requires careful consideration and sustainable solutions.
The future of plastic pellets hinges on the adoption of sustainable practices throughout the entire lifecycle. This necessitates a shift towards resource efficiency, reducing reliance on fossil fuels, and prioritizing responsible waste management. Ongoing research and development in bio-based polymers and advanced recycling techniques are crucial for mitigating the environmental footprint of plastic pellets and ensuring a more sustainable future. The global community must acknowledge the critical role of plastic pellets in modern life and collaborate to develop solutions that address their environmental impact without sacrificing their economic and industrial utility. This requires collective action from manufacturers, policymakers, and consumers to create a circular economy and move away from a linear, take-make-dispose model.


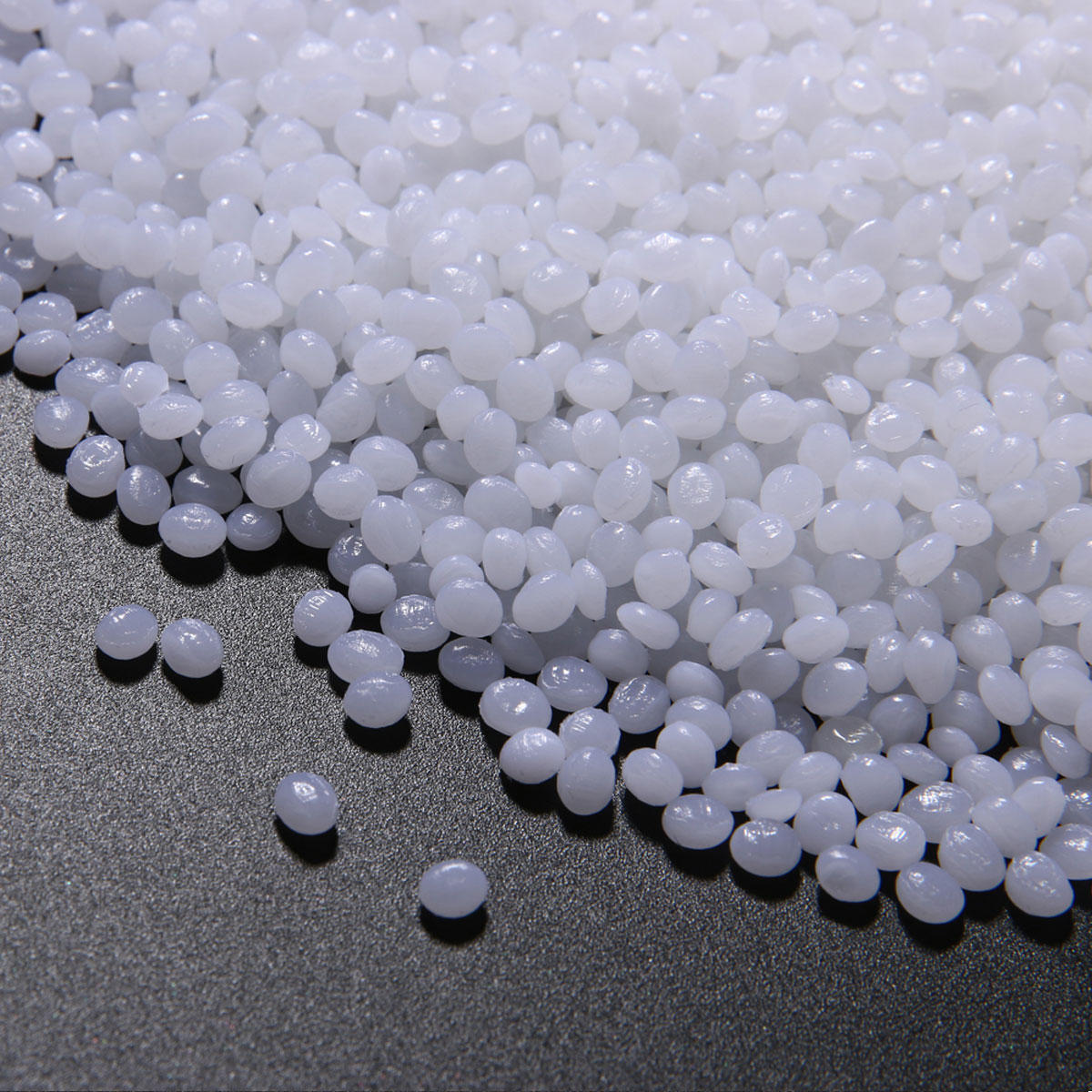