What is the significance of advanced metallic materials in modern applications?
Specialized alloys, meticulously engineered for specific performance characteristics, are crucial in contemporary industries. These materials, often exhibiting exceptional strength, durability, or conductivity, find applications spanning from aerospace to electronics. They represent a crucial advancement in material science, enabling innovations across diverse sectors.
The development and application of these sophisticated alloys yield numerous benefits. Enhanced structural integrity leads to lighter, stronger components in vehicles and aircraft, boosting efficiency and reducing fuel consumption. Specialized thermal properties in these alloys enable superior heat dissipation in electronics, preventing overheating and enhancing performance. The evolution of these alloys has been driven by increasing demands for improved performance and efficiency across multiple industries.
This exploration of advanced metallic materials will now delve into specific examples of their application and the scientific principles behind their design.
Metal-Tek
Advanced metal alloys, often referred to as "metal-tek," play a vital role in modern engineering. Their specific properties are crucial for various applications, from aerospace to medical devices.
- Alloy Composition
- Enhanced Strength
- Lightweight Design
- Corrosion Resistance
- Thermal Conductivity
- High Temperatures
- Specific Applications
The diverse properties of these materials stem from careful alloy design, optimizing factors like composition and processing. Enhanced strength, for instance, is achieved by strategically combining different metals. Lightweight design is crucial for aerospace applications, enabling greater efficiency. Corrosion resistance is vital for applications in harsh environments. High-temperature alloys are necessary for engines and turbines. Understanding these properties, and tailored combinations of them, is vital for the development of sophisticated materials. For instance, high-strength, lightweight alloys improve vehicle fuel economy, and alloys with specific thermal conductivity are used in electronic components to prevent overheating.
1. Alloy Composition
Alloy composition is fundamental to the properties and performance of advanced metallic materials, often referred to as "metal-tek." Precise control over the elements present in an alloy directly impacts its strength, ductility, corrosion resistance, and other crucial characteristics. The careful selection and proportioning of constituent metals are key to achieving the desired outcome. For example, specific combinations of metals may exhibit superior strength-to-weight ratios, essential for aerospace applications.
The impact of alloy composition extends beyond fundamental mechanical properties. Consider the development of high-temperature alloys. These require specific compositions to maintain structural integrity and strength at elevated temperatures. Similarly, corrosion resistance in marine environments necessitates alloys with particular compositional balances, thereby extending the lifespan of components. The relationship between composition and final properties is complex; extensive experimentation and modeling are vital to optimize alloys for specific applications. Detailed analysis of microstructures formed during the alloying process further clarifies the connection between composition and properties. Examples in diverse fields demonstrate this critical relationship. High-strength, lightweight alloys are crucial in automotive design for improved fuel efficiency. Medical implants benefit from biocompatible alloys with specific chemical properties.
In summary, alloy composition is a defining factor in the performance and application potential of advanced metallic materials. Understanding the precise relationship between alloy elements and material properties remains a critical aspect of research and development. This knowledge allows engineers to tailor materials for precise requirements, driving innovations in diverse sectors. Ongoing research continually pushes the boundaries of material science and alloy development to create new, even more sophisticated "metal-tek" for novel applications. Challenges persist in developing highly optimized alloys, but the importance of precise composition remains a driving force in this field.
2. Enhanced Strength
Enhanced strength is a defining characteristic of advanced metallic materials, often categorized as "metal-tek." This strength enhancement is not an incidental feature but a meticulously engineered outcome, crucial for specific applications. The pursuit of increased strength is driven by the need for lighter yet more robust components in various industries, particularly aerospace and automotive. A stronger material allows for reduced component size and weight without compromising structural integrity, leading to improved efficiency and performance. This connection is central to the development and application of "metal-tek." For instance, lightweight yet incredibly strong alloys are vital for aircraft construction, allowing for greater payload capacities and fuel efficiency. Similarly, automotive applications benefit from enhanced strength alloys to create safer and more durable vehicles.
The achievement of enhanced strength in these materials involves a multifaceted approach. Sophisticated alloying techniques play a crucial role. Precise control over the composition and microstructure of the alloying elements results in specific properties, including heightened strength. Advanced manufacturing processes further optimize the material's internal structure, leading to enhanced mechanical properties. The controlled addition of strengthening elements like precipitates or fine dispersions of other materials into the alloy matrix significantly alters the material's microstructure and enhances strength. For example, heat treatments refine the microstructure of specific alloys, improving their strength characteristics. This interplay between alloy design, processing, and structure is critical to achieve the desired level of strength. The understanding and manipulation of these factors are crucial for material engineers in designing components suited for a wide range of industrial applications.
In conclusion, enhanced strength is a core component of "metal-tek" materials. The relationship is not merely incidental but directly driven by the need for improved performance and efficiency in diverse sectors. The precise control over alloy composition, manufacturing processes, and microstructure are essential factors. While challenges remain in developing materials with optimal combinations of strength, lightweight characteristics, and other properties, the pursuit of enhanced strength remains a significant driver in material science, ensuring lighter, stronger, and more reliable components in various industries. The design and use of these advanced materials are heavily dependent on the understanding and application of fundamental metallurgical principles.
3. Lightweight Design
Lightweight design, a critical component of advanced metallic materials (often referred to as "metal-tek"), is driven by the need for improved efficiency and performance across numerous industries. The pursuit of lighter, yet stronger components is central to this concept. Reduced weight directly translates to decreased fuel consumption in vehicles, extended flight times in aircraft, and minimized energy expenditure in various applications. The core connection lies in the ability of advanced alloys to achieve high strength-to-weight ratios.
Real-world examples highlight the importance of this connection. Aircraft manufacturers utilize lightweight alloys to reduce the overall mass of airframes, enabling greater payload capacities and increased range. Automotive engineers employ lightweight designs in vehicles to enhance fuel efficiency and improve acceleration. In medical applications, lightweight yet robust implants minimize the burden on patients. The demand for such materials spans diverse industries, demonstrating the critical role lightweight design plays in "metal-tek." A key factor is the careful selection and manipulation of the alloy composition, achieving high strength without excessive density. This engineering optimization directly impacts the economic viability and performance of the final product. For instance, the use of titanium alloys in aircraft has significantly contributed to increased fuel efficiency and payload capacity. Similarly, aluminum alloys have revolutionized automotive design.
In conclusion, lightweight design is an integral aspect of "metal-tek." The pursuit of high strength-to-weight ratios, achievable through advanced alloy development and manufacturing processes, drives innovations across sectors. The advantages are evident in reduced fuel consumption, improved performance, and enhanced functionality. While challenges remain in achieving the optimal balance between strength and weight, the ongoing research and development in advanced metallic materials ensure that lightweight design remains a critical component for future technological advancements.
4. Corrosion Resistance
Corrosion resistance is a paramount characteristic in advanced metallic materials, often termed "metal-tek." The ability of a material to withstand degradation in corrosive environments directly impacts its lifespan and applicability in various sectors. Understanding and controlling this property is crucial for maintaining structural integrity and functionality, especially in challenging or demanding conditions. This facet explores the significance of corrosion resistance in the context of "metal-tek."
- Alloying Strategies for Enhanced Corrosion Resistance
Materials science approaches frequently involve the strategic addition of alloying elements to enhance corrosion resistance. The presence of specific elements can create a protective surface layer or passivation film, shielding the underlying metal from corrosive agents. This approach is critical in industries like marine engineering, where materials must withstand saltwater environments. Specific alloy compositions, carefully designed, result in materials significantly more resistant to degradation in these conditions. The selection of suitable elements and their precise proportions is a crucial aspect of this process.
- Protective Surface Treatments
Coatings and surface treatments are frequently employed to further bolster the corrosion resistance of "metal-tek." These treatments can range from electroplating to the application of organic or ceramic layers. These layers provide a physical barrier between the metal and the environment, preventing direct contact with corrosive agents. Their effectiveness hinges on the adherence of the coating to the substrate, the composition of the coating material, and environmental conditions. This is prevalent in applications needing superior durability, such as pipelines and external structural elements.
- Impact on Component Life Cycle
Enhanced corrosion resistance directly impacts the lifecycle of components. Reduced degradation translates to longer operational periods, minimizing maintenance requirements and associated costs. This translates into significant economic benefits for industrial applications, particularly in infrastructure projects like bridges or pipelines. The reduced need for replacement or repair extends the lifespan of assets, improving overall efficiency.
- Specific Applications Requiring High Corrosion Resistance
Corrosion resistance is a defining characteristic in diverse applications where materials must endure harsh environments. For instance, in marine environments, specialized alloys must withstand the aggressive nature of saltwater. Similar considerations are necessary in chemical processing plants, where materials must resist exposure to various chemicals. Furthermore, in infrastructure projects like bridges, the longevity of the structures hinges on materials exhibiting exceptional resistance to atmospheric corrosion and environmental stresses. The selection of the appropriate alloy is contingent on the specific corrosive environment and the required performance characteristics.
In summary, corrosion resistance is an integral aspect of "metal-tek" materials. The strategies employedfrom alloying to surface treatmentsdirectly influence the performance and longevity of components in various demanding applications. The selection of appropriate materials depends on understanding the specific corrosive environment and required performance benchmarks. This approach ensures the durability and effectiveness of "metal-tek" across a broad range of industrial applications, impacting critical infrastructure and components in numerous sectors.
5. Thermal Conductivity
Thermal conductivity, a key property of advanced metallic materials, often referred to as "metal-tek," is fundamental to their performance in numerous applications. The ability of a material to efficiently transfer heat directly impacts its suitability for diverse functions. High thermal conductivity allows rapid heat dissipation, preventing overheating, a critical aspect in various technological sectors. Conversely, low thermal conductivity can be advantageous in situations requiring insulation or controlled temperature gradients.
In applications like electronics, high thermal conductivity in "metal-tek" alloys is crucial. Components such as processors generate significant heat during operation. Efficient heat dissipation prevents performance degradation and extends component lifespan. Similarly, in automotive engines, thermal conductivity influences the performance and durability of engine parts. High thermal conductivity alloys ensure effective heat transfer from the engine's core components to the cooling system, preventing overheating and improving overall performance. Specific alloys designed with high thermal conductivity are crucial in heat exchangers, where efficient heat transfer is vital for optimizing energy transfer processes across various industrial applications. The choice of material in these instances critically hinges on thermal conductivity, emphasizing the material's importance in influencing component operation and longevity.
Understanding the interplay between thermal conductivity and material properties in "metal-tek" is crucial for optimizing performance and reliability. The selection of suitable alloys depends on the specific thermal demands of each application. Researchers continue to develop and refine alloys with tailored thermal conductivity, enabling engineers to optimize their designs. While maximizing thermal conductivity is frequently desired, certain applications demand materials with lower conductivity for insulation purposes, underscoring the diverse functional roles this property plays. The implications for advancing technology and industrial efficiency through precise control of this crucial material property are significant.
6. High Temperatures
High-temperature performance is a defining characteristic of advanced metallic materials, often categorized as "metal-tek." The ability of these alloys to maintain structural integrity and desired properties at elevated temperatures is critical in numerous applications. This performance is not incidental but a consequence of meticulously engineered compositions and microstructures. Extreme conditions, such as those encountered in jet engines, turbines, and certain industrial processes, necessitate materials capable of withstanding high temperatures without compromising strength or functionality. These high-temperature alloys enable the operation of critical components under demanding thermal stresses. The understanding and manipulation of these materials are paramount to maximizing performance and operational lifetimes in high-temperature environments.
Real-world examples underscore the importance of high-temperature alloys. Jet engines, operating at extreme temperatures, rely heavily on nickel-based superalloys capable of maintaining strength and resistance to creep deformation at high temperatures. Turbine blades in power plants similarly demand high-temperature alloys to endure continuous high-temperature exposure and maintain mechanical performance. Components in chemical processing plants also require high-temperature resistance to withstand corrosive environments at elevated temperatures. In each case, the performance characteristics of the selected "metal-tek" are directly related to their high-temperature capabilities. The ability to precisely control alloy compositions and processing techniques directly influences the operational temperature limits of these materials. The selection of appropriate "metal-tek" for a given application depends critically on the specific temperature and operational parameters.
In conclusion, high-temperature performance is an integral aspect of "metal-tek." The sophisticated compositions and processing techniques employed in the creation of high-temperature alloys are vital for realizing the performance of components operating under extreme conditions. The ongoing advancement of these materials necessitates further research to explore and develop new alloys with even greater temperature tolerances. This pursuit directly impacts the efficiency and reliability of various industrial processes and technologies. Understanding these materials' high-temperature characteristics is vital for selecting appropriate materials for demanding applications and realizing the full potential of advanced manufacturing.
7. Specific Applications
The development and utilization of advanced metallic materials, often referred to as "metal-tek," are intrinsically linked to specific applications. The properties of these materials, meticulously tailored, determine their suitability and performance in diverse sectors. This exploration examines key application areas where "metal-tek" plays a crucial role.
- Aerospace Industry
The aerospace industry relies heavily on "metal-tek" for aircraft construction. Lightweight yet exceptionally strong alloys are vital for reducing weight, improving fuel efficiency, and increasing payload capacity. Advanced titanium and aluminum alloys, examples of "metal-tek," are employed extensively in modern aircraft, demonstrating the crucial relationship between material properties and performance in this sector. The demands for extreme strength and resistance to fatigue under extreme stress conditions are a key driver for research and development in this application area.
- Automotive Engineering
The automotive sector utilizes "metal-tek" alloys for enhanced vehicle performance and safety. Lightweight, high-strength alloys contribute to improved fuel economy, better acceleration, and enhanced handling. Advanced steel alloys, aluminum alloys, and magnesium alloys are commonly incorporated into vehicle components, reducing weight while maintaining structural integrity. This is a major example of how "metal-tek" contributes to advancements in vehicle technology.
- Medical Implants
The medical field leverages "metal-tek" for the creation of implants and prosthetics. Biocompatible alloys are crucial for minimizing the risk of rejection by the human body and for ensuring long-term functionality. Titanium alloys, known for their biocompatibility and strength, are widely used in orthopedic implants, showcasing the critical role of "metal-tek" in advancing medical technology and patient outcomes. This highlights the importance of material science in applications requiring compatibility with biological systems.
- Power Generation
High-temperature alloys are employed in power generation facilities, particularly in turbine blades and other components that operate at extreme temperatures. These specialized alloys must retain strength and resist degradation under significant thermal stress. Nickel-based superalloys, a prime example of "metal-tek," are integral to power plant operations, demonstrating how high-temperature performance is a critical requirement in specific applications.
Across these diverse application areas, "metal-tek" is demonstrably crucial. The careful selection and tailoring of material properties allow engineers to optimize components for specific needs, driving progress in a wide array of industries. The pursuit of novel materials and processing methods continues to advance the capabilities of "metal-tek," leading to enhanced performance and improved application outcomes in both existing and emerging fields. This demonstrates the deep link between materials science, engineering design, and the advancement of technology across various sectors.
Frequently Asked Questions about Advanced Metallic Materials ("Metal-Tek")
This section addresses common inquiries regarding advanced metallic materials, often referred to as "metal-tek." These materials exhibit unique properties crucial in various industrial applications. Clear answers to frequently asked questions are provided below.
Question 1: What are the key characteristics defining "metal-tek"?
Advanced metallic materials, or "metal-tek," are characterized by meticulously engineered compositions that yield exceptional properties such as high strength, lightweight design, corrosion resistance, and specific thermal or high-temperature capabilities. These properties are tailored for specific applications, distinguishing them from standard metals. Key characteristics include precise alloying, sophisticated processing techniques, and advanced microstructure control.
Question 2: How are these materials different from conventional metals?
Conventional metals possess inherent properties; however, "metal-tek" materials are meticulously engineered to optimize specific characteristics. This is achieved through precise alloy design and advanced manufacturing techniques. "Metal-tek" compositions often incorporate rare or specialized elements to enhance desired properties, leading to superior performance compared to their conventional counterparts.
Question 3: What are the primary applications for "metal-tek" materials?
"Metal-tek" finds application in diverse sectors, including aerospace, automotive, medical implants, and power generation. Their enhanced strength-to-weight ratios, corrosion resistance, and high-temperature capabilities make them well-suited for these demanding environments. The specific application dictates the precise material properties required.
Question 4: What are the costs and challenges associated with using "metal-tek"?
The sophisticated manufacturing processes and specialized alloy compositions employed in "metal-tek" materials often lead to higher production costs compared to conventional metals. Material research and development, necessary for tailoring desired properties, also contribute to the expense. Challenges include achieving precise control over the composition, microstructures, and processing of these alloys.
Question 5: What is the future outlook for "metal-tek" development?
Ongoing research focuses on expanding the range of "metal-tek" materials to meet increasingly demanding performance requirements in various sectors. This includes advancements in alloy design, manufacturing techniques, and processing methods to improve properties like strength, durability, and sustainability. Future developments likely encompass wider application ranges and cost reductions in production.
In summary, "metal-tek" materials represent a significant advancement in material science, offering specialized properties for demanding applications. The benefits often come at a cost, requiring ongoing research and development to achieve the desired balance of performance and cost-effectiveness. Further exploration of these materials' potential is an important element of future innovation.
This concludes the FAQ section. The following section will explore the technical aspects of "metal-tek" material science in greater detail.
Conclusion
This exploration of advanced metallic materials, often categorized as "metal-tek," has highlighted the profound impact these engineered alloys have on modern industry. Key characteristics, including enhanced strength, lightweight design, corrosion resistance, and tailored thermal conductivity, have been examined in detail. The precise control over alloy composition and manufacturing processes is crucial for achieving the desired properties. The exploration has revealed a complex interplay between material science, engineering design, and application, showcasing the vital role "metal-tek" plays in various sectors. From aerospace to automotive, medical implants to power generation, the strategic application of these advanced alloys directly impacts efficiency, performance, and safety. The discussion has underscored the critical link between material properties and the functionality of components operating under demanding conditions.
The future trajectory of "metal-tek" research and development promises further innovation and optimization. Continued exploration into novel alloy compositions, enhanced manufacturing processes, and refined processing techniques will undoubtedly lead to even more sophisticated and versatile materials. This evolution will likely drive breakthroughs in various sectors, leading to lighter, stronger, more efficient, and safer products. Understanding and manipulating the intricate relationships between material properties and application demands will remain paramount in the continuing development and utilization of these advanced metallic materials. The significance of "metal-tek" in shaping future technological advancements is undeniable.
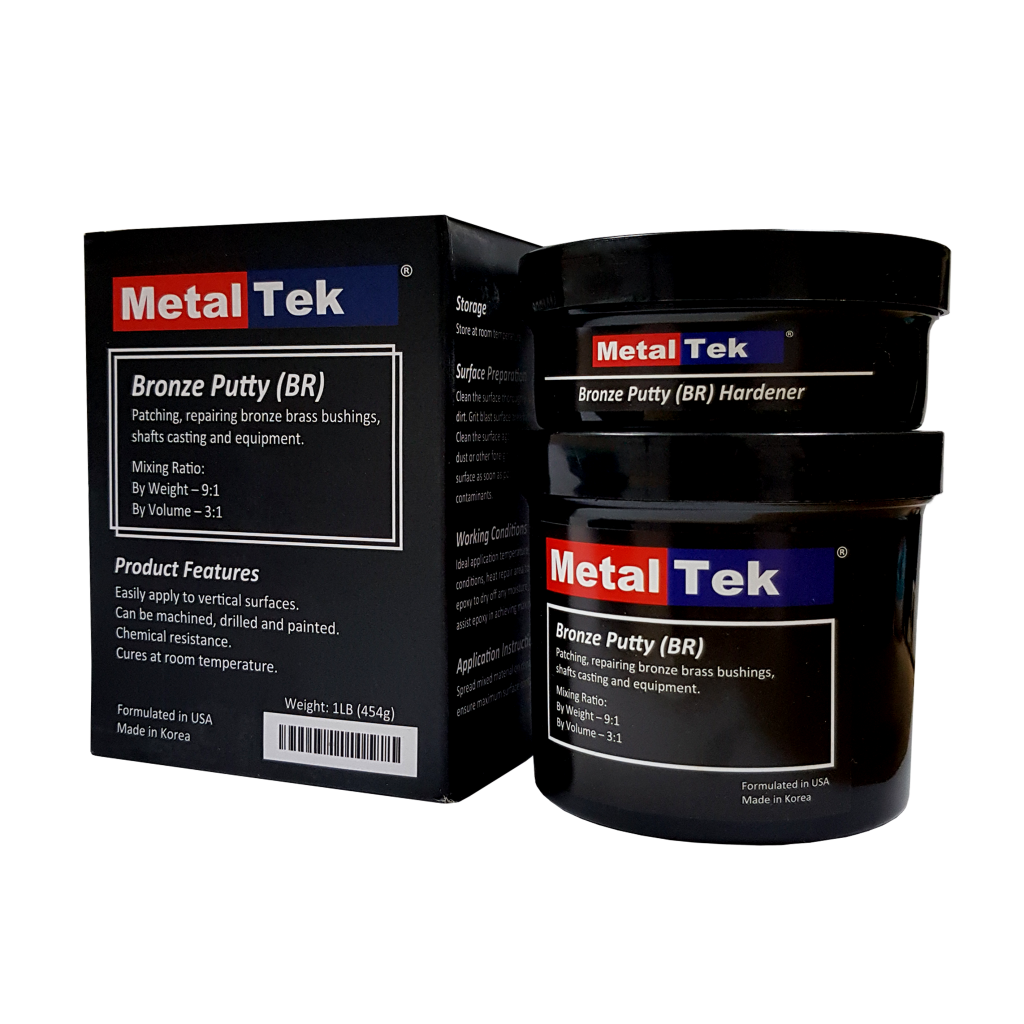
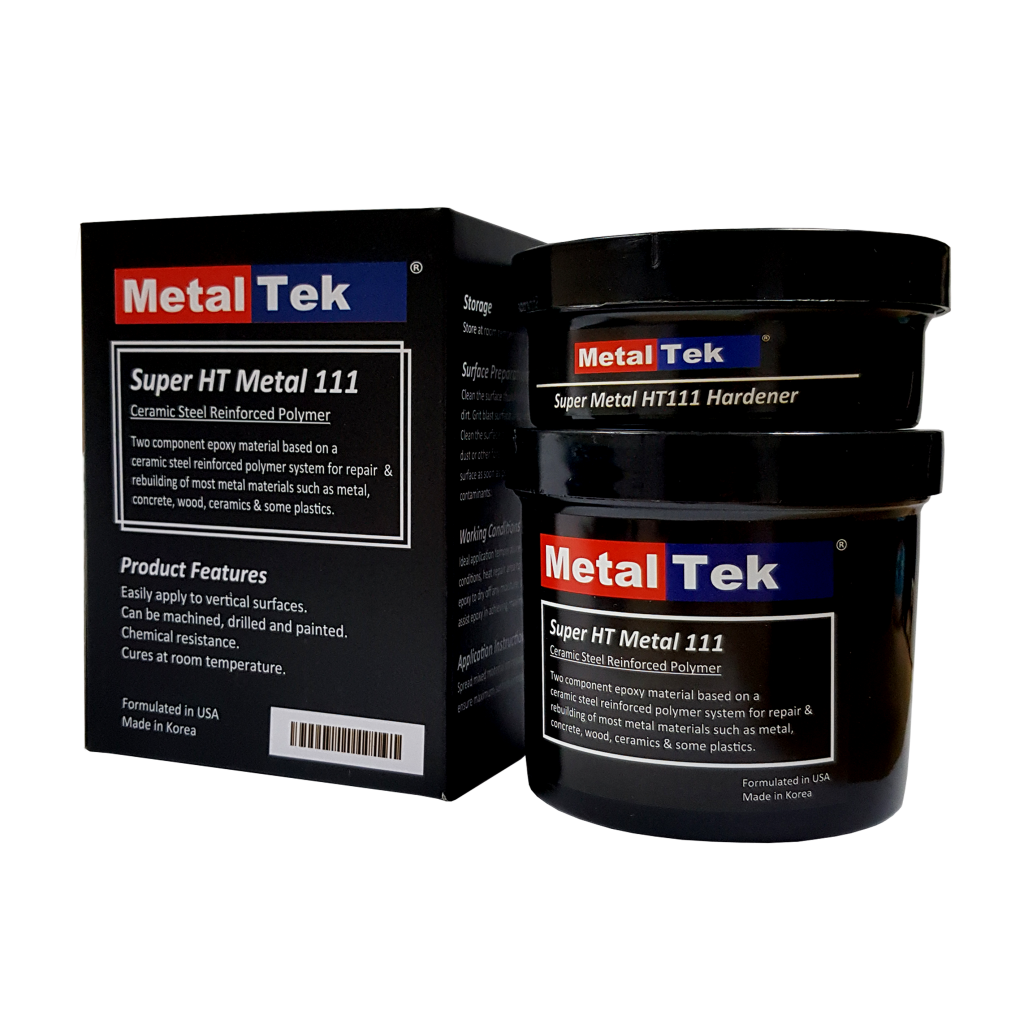
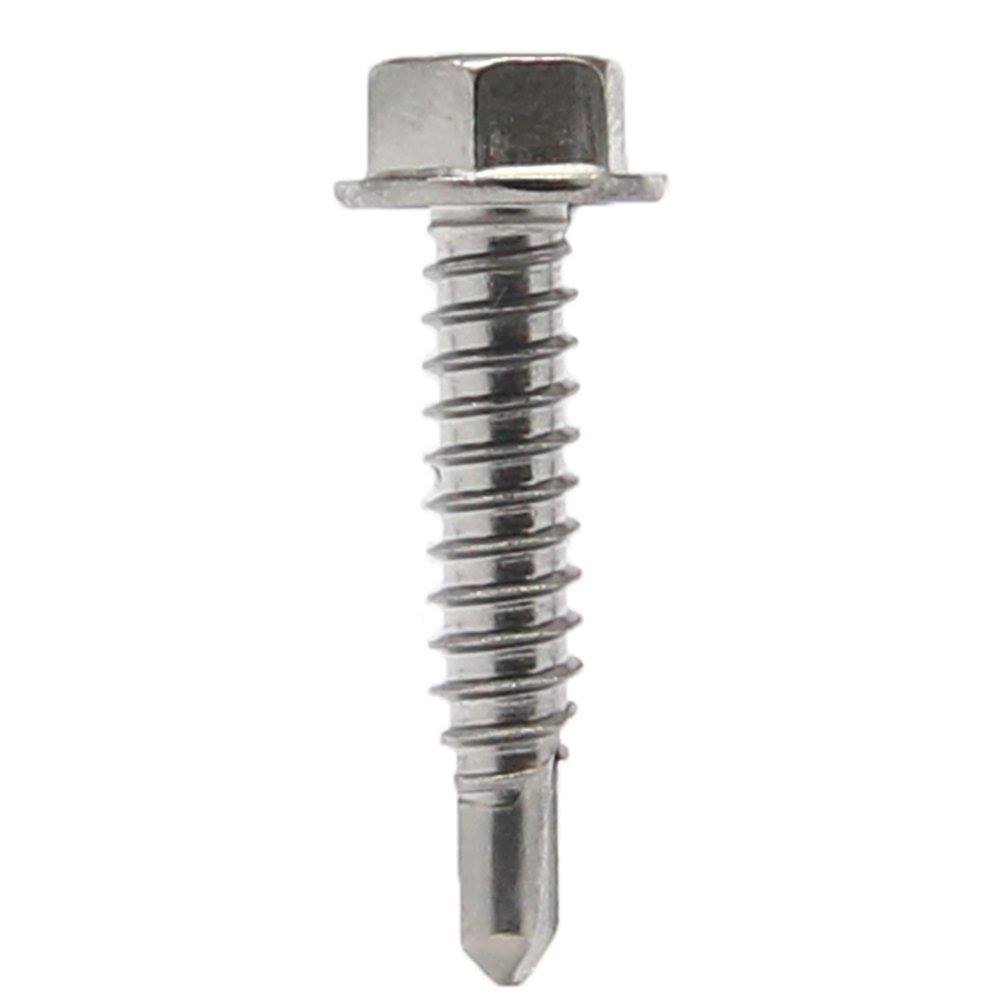