What tools are essential for achieving optimal results in a specific process? This specialized tool, vital for precision and efficiency, is a key factor in success.
A specialized tool, designed for a specific application, is a critical element in achieving desired outcomes. This tool typically possesses unique characteristics, such as a particular shape, size, or material, allowing for precise manipulation of a target material or object. Examples include, but are not limited to, intricate cutting tools for delicate materials or specialized gripping tools for precise assembly. The effectiveness of a particular outcome is often linked to the quality and functionality of these specific instruments.
The importance of such tools lies in their ability to improve the quality, consistency, and speed of a process. Accurate and precise tools are indispensable in various fields, including manufacturing, construction, and scientific research, leading to enhanced productivity and reduced errors. Historical examples demonstrate the pivotal role of these tools in the advancement of technology and civilization, showcasing the ongoing evolution of instruments optimized for specific tasks.
This discussion about specialized tools forms the foundation for a more in-depth exploration into the practical applications, material properties, and manufacturing processes surrounding the development and optimization of such instruments.
Buening Implement
Understanding the characteristics and applications of a "buening implement" is crucial for optimized results. This tool's effectiveness depends on key attributes, influencing its functionality and impact.
- Precision
- Functionality
- Material
- Ergonomics
- Durability
- Specificity
- Efficiency
These aspects, combined, dictate a "buening implement's" success. Precision in design ensures accurate execution. Functionality determines the task it fulfills. Material selection dictates durability and specific use cases. Ergonomics impacts user comfort and control. Durability ensures long lifespan and consistent performance. Specificity addresses specific needs, avoiding unnecessary complexity. Efficiency maximizes productivity in the target process. For example, a finely-tuned surgical instrument exhibits precision, specific functionality, and specialized material. A high-quality implement for a particular agricultural task would emphasize durability, functionality, and efficiency.
1. Precision
Precision is a defining characteristic of a "buening implement." The very nature of such a tool necessitates accuracy in its design and construction. This precision, often achieved through meticulous attention to detail and advanced manufacturing techniques, directly impacts the implement's efficacy. A surgical scalpel, for instance, demands exceptional precision in its blade's sharpness and alignment to ensure precise incisions. A high-precision machine part, critical for intricate machinery, likewise necessitates exacting tolerances. This inherent precision minimizes errors, maximizes efficiency, and ensures optimal outcomes during use.
The importance of precision in tools extends beyond the realm of high-tech applications. A carpenter's measuring tape, used for precise measurements, directly affects the accuracy of a construction project. In agriculture, precision tools, like planters and harvesters, optimize planting density and yield efficiency, reflecting a strong correlation between precision and productivity. Thus, understanding and appreciating the importance of precision in an implement is vital in numerous applications to achieve desired levels of accuracy and effectiveness, and avoid costly errors or inconsistencies.
In conclusion, the connection between precision and a "buening implement" is fundamental. High-precision tools directly translate to enhanced functionality, reduced errors, and optimal performance. This direct link underscores the critical role of precision in a wide spectrum of applications, from the delicate to the substantial.
2. Functionality
The functionality of a "buening implement" is paramount. Its design and construction must directly address a specific need or task. Without precise functionality, the implement fails to deliver intended results and loses its value. Understanding the various facets of this functionality is essential for effective application and optimal outcomes.
- Targeted Application
A "buening implement" is designed for a specific task. A surgical instrument, for example, is optimized for delicate tissue manipulation. An agricultural implement is tailored for cultivating soil or harvesting crops. A manufacturing tool is designed for the precise shaping or joining of materials. The specific function determines its features and construction. Failure to align the design with the intended use limits the implement's effectiveness and compromises the intended outcome.
- Efficiency and Speed
A "buening implement" should maximize the efficiency of a process. High-quality tools reduce the time and effort required to complete a task. For example, modern farming equipment streamlines harvesting, significantly increasing yields and productivity. Similarly, efficient tools in manufacturing reduce production time and increase output. Optimization for speed and efficiency is intrinsically linked to the functionality of the implement.
- Precision and Accuracy
Precision is inherent to functionality. A "buening implement" designed for accuracy in tasks will generally exhibit superior precision in its construction and use. Instruments used in scientific research, like pipettes for precise liquid measurement, are exemplary of this concept. A tool that is not precise fails to deliver consistent and accurate outcomes, impacting the overall effectiveness of the process it supports.
- Durability and Longevity
A "buening implement" must endure regular use. The functionality and longevity of a tool are intrinsically linked. A tool designed for heavy-duty use must be constructed from appropriate materials and have robust engineering to withstand repeated use, preventing wear, tear, and rapid degradation. The long-term viability of a tool is often dependent on its design and ability to endure typical use cycles, directly impacting functionality. Durability contributes to the overall practicality of the implement.
Ultimately, the functionality of a "buening implement" is judged not only by its ability to perform a specific task but also by its overall effectiveness, precision, and endurance during typical use. A well-designed and functional implement reduces errors, optimizes efficiency, and ensures longevity in its application across diverse sectors.
3. Material
Material selection is critical for a "buening implement." The inherent properties of the material directly influence the tool's performance, durability, and overall effectiveness. Choosing the appropriate material is paramount for optimizing the tool's functionality and longevity, thus impacting the precision, safety, and efficiency of the intended application.
- Strength and Durability
The material's ability to withstand stress and repeated use is essential. High-impact applications, such as in industrial settings, demand materials with superior strength and toughness. Conversely, applications requiring fine manipulation might prioritize materials with a balance of strength and flexibility. Examples include high-carbon steel for cutting tools and titanium alloys for surgical instruments, reflecting the direct correlation between material properties and implement functionality. Selecting materials that can withstand expected stress and environmental factors is crucial for sustained performance.
- Hardness and Resistance to Wear
The material's hardness and resistance to wear significantly impact its lifespan. Tools subjected to high friction or abrasive environments, such as those in construction or machining, must be crafted from materials with high hardness and wear resistance. Materials like tungsten carbide or high-grade steel excel in these scenarios, ensuring the tool remains effective over extended use cycles. A lack of hardness can lead to premature wear and reduced performance.
- Chemical Resistance
The resistance of the material to chemical degradation or corrosion in specific environments is crucial for long-term use. Tools used in chemical laboratories or certain industrial settings must be composed of materials resistant to corrosive substances. Stainless steel, for example, is commonly used due to its chemical resistance in diverse applications. Failure to consider chemical resistance can result in premature tool failure and compromise the implement's utility.
- Thermal Properties
Certain applications require materials with specific thermal properties. High-temperature environments or precision instruments need materials that maintain shape and integrity under heat. High-temperature alloys and specific ceramics demonstrate thermal stability, which is important for maintaining accuracy in high-heat settings, such as manufacturing processes. Materials with poor thermal properties can lead to warping or deformation, impacting the implement's precision and utility.
Ultimately, the choice of material directly impacts a "buening implement's" functionality, durability, safety, and overall effectiveness. Careful consideration of these material properties during the design phase is essential for maximizing the tool's operational lifespan and achieving optimal results across a range of applications.
4. Ergonomics
Ergonomics plays a crucial role in the design and effectiveness of a "buening implement." A well-designed implement considers the physical interaction between the user and the tool. This encompasses factors like the tool's size, weight, shape, and the hand grip. Optimizing these elements enhances user comfort and reduces the risk of fatigue or injury during prolonged use. A well-designed ergonomic handle on a gardening tool, for example, allows for comfortable and efficient operation. Conversely, an awkwardly shaped tool leads to strain, reducing productivity and potentially causing injuries. The human-tool interface should be optimized for maximum performance and minimal risk.
Practical considerations for implementing ergonomic principles in tool design involve a thorough understanding of anthropometric data, encompassing the diversity of human body shapes and sizes. Testing the grip and balance of a prototype with a diverse range of users is essential. Tools optimized for different hand sizes and grip styles are more inclusive and result in better performance, minimizing fatigue, and reducing the possibility of repetitive strain injuries. Ergonomically designed tools in construction, manufacturing, and medical procedures minimize risks and enhance efficiency. Consideration of the interplay between user and tool is therefore critical in developing effective and safe implements. This involves understanding how the hand, wrist, and forearm interact with the tool, and subsequently, how these interactions can affect the body over time.
In conclusion, ergonomic principles are indispensable in "buening implement" design. Optimizing the tool's interaction with the user promotes safety, comfort, efficiency, and long-term productivity. Careful attention to anthropometric data, user feedback, and comprehensive testing are crucial for the creation of tools that benefit both the user and the overall efficiency of a task. Ignoring these principles can lead to avoidable discomfort, injury, and reduced productivity.
5. Durability
The durability of a "buening implement" is a critical factor determining its overall value and utility. A tool's ability to withstand repeated use, environmental stresses, and expected wear and tear is directly linked to its long-term effectiveness and economic viability. This inherent resilience influences operational efficiency, safety, and the ultimate return on investment for any user.
- Material Selection and Construction
The choice of material is paramount in ensuring durability. Materials with inherent strength and resistance to wear and tear are preferred. For instance, a high-carbon steel blade for a knife will be more durable than a softer metal. Robust construction techniques, ensuring proper welding, fasteners, or joining processes, are equally crucial. Proper material selection and construction methods enhance a tool's resistance to damage from impacts, abrasion, or corrosion, thereby extending its lifespan and preventing costly replacements.
- Manufacturing Processes and Quality Control
The methods employed in manufacturing significantly influence a tool's durability. Rigorous quality control measures, encompassing careful inspection at various stages of production, help identify and mitigate potential flaws. Modern manufacturing processes, employing advanced machinery and techniques, contribute to the consistent production of durable implements. A robust manufacturing process, including precise tolerances and careful adherence to standards, is vital to minimizing defects and ensuring the tool's ability to endure demanding use cases.
- Impact Resistance and Toughness
The ability of the material to resist damage from impacts is a critical factor. This is often measured through standardized impact tests. Tools exposed to frequent impacts, such as those in construction or industrial settings, necessitate materials with superior toughness and impact resistance. Tools that readily fracture or deform under impact are not durable and necessitate replacing sooner.
- Environmental Resistance
Durability extends to a tool's ability to endure the environment in which it is employed. Exposure to corrosive agents, extreme temperatures, or other environmental hazards can significantly affect a tool's lifespan. Proper surface treatments and protective coatings can substantially improve environmental resistance, preventing rust, degradation, or other detrimental effects. Tools designed for outdoor or harsh industrial settings require materials and surface treatments explicitly chosen to minimize damage from environmental elements.
In summary, durability in a "buening implement" is not a singular attribute but a multifaceted characteristic resulting from the interaction of material properties, manufacturing processes, and the environment in which the implement operates. Prioritizing durability during the design and production phases leads to more cost-effective and efficient tools in the long run. A durable tool reduces maintenance requirements, minimizes downtime, and ultimately improves the return on investment for the user.
6. Specificity
A "buening implement's" efficacy is intrinsically linked to its specificity. This characteristic ensures the tool directly addresses a particular task or need, maximizing efficiency and minimizing wasted effort. The degree of specialization dictates the implement's suitability for specific applications, influencing its effectiveness and overall performance.
- Targeted Application
A "buening implement" is designed for a precise purpose. A surgeon's scalpel, for example, is specifically designed for delicate tissue manipulation, whereas a carpenter's saw is designed for cutting wood. This tailored functionality avoids unnecessary complexity and ensures optimal performance within the targeted application. Broad-spectrum tools often lack the precision and efficiency of specialized ones, potentially compromising the outcome. The fundamental design principle of specialization in a "buening implement" centers around addressing a particular need with the utmost precision and efficiency.
- Minimized Redundancy
Specificity eliminates redundant features. A highly specialized implement focuses exclusively on the required functions, eschewing unnecessary components. This streamlined design enhances efficiency, reduces weight, and frequently lowers production costs. For example, a specialized tool for a singular assembly process avoids incorporating features unsuitable for other tasks, thus leading to a more focused and effective design. This minimized redundancy improves performance and lowers production costs.
- Enhanced Performance and Accuracy
Specialized tools often exhibit superior performance and accuracy. The focused design typically results in higher precision, contributing to improved results in targeted applications. A high-precision machining tool designed for intricate work will likely surpass a generalized tool in accuracy and speed. The increased focus on a specific task, often observed in specialized tools, leads to superior outcomes. This heightened precision and accuracy directly enhance the overall value of a "buening implement" for its intended function.
- Reduced Training Requirements
The specificity of the "buening implement" simplifies the learning curve for users. With a clear and singular function, training is often more streamlined and quicker, minimizing the time required for personnel to master the tool's usage. This reduced training time reflects a significant benefit, accelerating productivity in environments where efficiency is paramount. A tool with a single, defined function requires less extensive training to master, which translates to faster productivity gains.
Ultimately, specificity is a key aspect of an effective "buening implement." This characteristic ensures the tool addresses a specific need, enhancing its functionality, precision, and performance within its designated role. Tools explicitly designed for particular tasks lead to optimal outcomes and efficient processes, maximizing returns and minimizing wasted resources. This inherent specificity underscores the crucial role of careful design and functional focus in the development of high-performance implements.
7. Efficiency
Efficiency, in the context of a "buening implement," signifies the optimized use of resources to achieve a specific task with minimal waste. This encompasses both time and material, ultimately impacting productivity and output. A highly efficient implement minimizes wasted motion, energy, and materials, leading to a more productive process.
- Reduced Cycle Time
An efficient "buening implement" minimizes the time required to complete a task. This reduction can be achieved through streamlined design, optimized material selection, and precise construction methods. For example, a modern agricultural harvester, designed for optimal field coverage and crop separation, significantly reduces the time needed to harvest a given area compared to older models. Reduced cycle time directly impacts overall productivity and output, demonstrating a strong correlation between efficiency and the speed of task completion.
- Minimized Material Waste
Efficiency in a tool extends to minimizing material waste during operation. A well-designed implement, by design, reduces material loss through controlled processes, precise cutting, or controlled application. A cutting tool with a sharp, precisely calibrated edge, for instance, will minimize material loss and maximize the use of the raw material. Optimizing resource use is a key component of efficient implement design.
- Increased Output and Productivity
Efficient "buening implements" directly translate to increased output and productivity. By reducing the time and material wasted, the overall output of a production process is boosted. In manufacturing, an efficient machine tool will produce more parts in a given time frame, significantly increasing overall productivity. This boost in productivity, directly connected to efficient tool design, illustrates the positive correlation between efficient tools and enhanced output.
- Improved Precision and Accuracy
Efficiency in tool design often leads to improved precision and accuracy. Tools that are well-designed and efficiently manufactured tend to operate with greater precision, decreasing errors and increasing output quality. A precision-machined part, for example, will exhibit greater accuracy in fit and function compared to a less precise counterpart. This enhanced precision contributes to improved product quality and reduced waste.
In conclusion, efficiency in a "buening implement" is not merely a desirable trait but an essential aspect of its effectiveness. Improved efficiency translates to reduced costs, increased productivity, and enhanced overall output. The correlation between efficient tools and positive outcomes underscores the critical importance of optimizing design, materials, and construction methods to maximize the value and impact of these implements.
Frequently Asked Questions about "Buening Implement"
This section addresses common inquiries regarding "buening implements." Clear and concise answers are provided to foster a thorough understanding of these specialized tools.
Question 1: What is a "buening implement," and what is its purpose?
A "buening implement" is a specialized tool designed for a specific task or process. Its purpose is to perform that task efficiently and effectively, often with a high degree of precision. The tool's design, materials, and construction are tailored to meet the precise requirements of the intended application.
Question 2: What factors influence the selection of materials for a "buening implement"?
The selection of materials for a "buening implement" is crucial. Considerations include strength, durability, resistance to wear, and compatibility with the intended environment (e.g., chemical resistance, heat resistance). Material properties directly impact the tool's longevity, performance, and safety.
Question 3: How does the design of a "buening implement" affect its performance?
A "buening implement's" design is directly correlated to its effectiveness. Aspects like ergonomic design, precision engineering, and consideration of the specific task directly affect the tool's ease of use, accuracy, and efficiency. A poorly designed tool will likely be ineffective or even dangerous.
Question 4: What are the benefits of using a specialized "buening implement" over a general-purpose tool?
Specialized tools often deliver higher levels of precision, accuracy, and efficiency compared to general-purpose tools. Their design focuses on a particular application, minimizing unnecessary features and maximizing performance in the specific task. This specialized approach often translates into reduced errors, faster completion times, and enhanced overall productivity.
Question 5: How can the durability of a "buening implement" be assessed and improved?
Durability is assessed through rigorous testing under anticipated operating conditions. This involves evaluating factors like resistance to wear, corrosion, and impact damage. Improving durability often involves selecting high-quality materials, employing advanced manufacturing techniques, and optimizing the tool's design for robustness. Quality control measures at each stage of production contribute to the overall durability of the implement.
In summary, the characteristics of a "buening implement"including material selection, design, functionality, specificity, and durabilitydetermine its effectiveness and the quality of the outcome. By focusing on the precise needs of the application, these specialized tools yield improved results and increased efficiency. They contribute to various fields by streamlining tasks, enhancing accuracy, and reducing potential errors.
This concludes the FAQ section. The following section will delve deeper into the practical applications and uses of "buening implements" across diverse sectors.
Conclusion
This exploration of "buening implements" highlights the critical role of specialized tools in diverse applications. Key attributes, such as precision, functionality, material properties, ergonomics, durability, specificity, and efficiency, all contribute to a tool's effectiveness. The careful consideration of these elements during design and manufacturing is paramount for optimized performance and long-term value. The discussion underscores the substantial impact of well-designed "buening implements" on productivity, accuracy, and safety across various sectors.
The evolution of "buening implements" reflects advancements in technology and engineering. Continuous innovation in material science, manufacturing processes, and ergonomic design will drive further improvements in tool performance. Understanding the intricacies of specialized tools is vital for maximizing efficiency and minimizing risk in today's demanding environments. Furthermore, a deep comprehension of the crucial elements in "buening implement" design and application can foster the development of more effective and resilient tools for future generations.
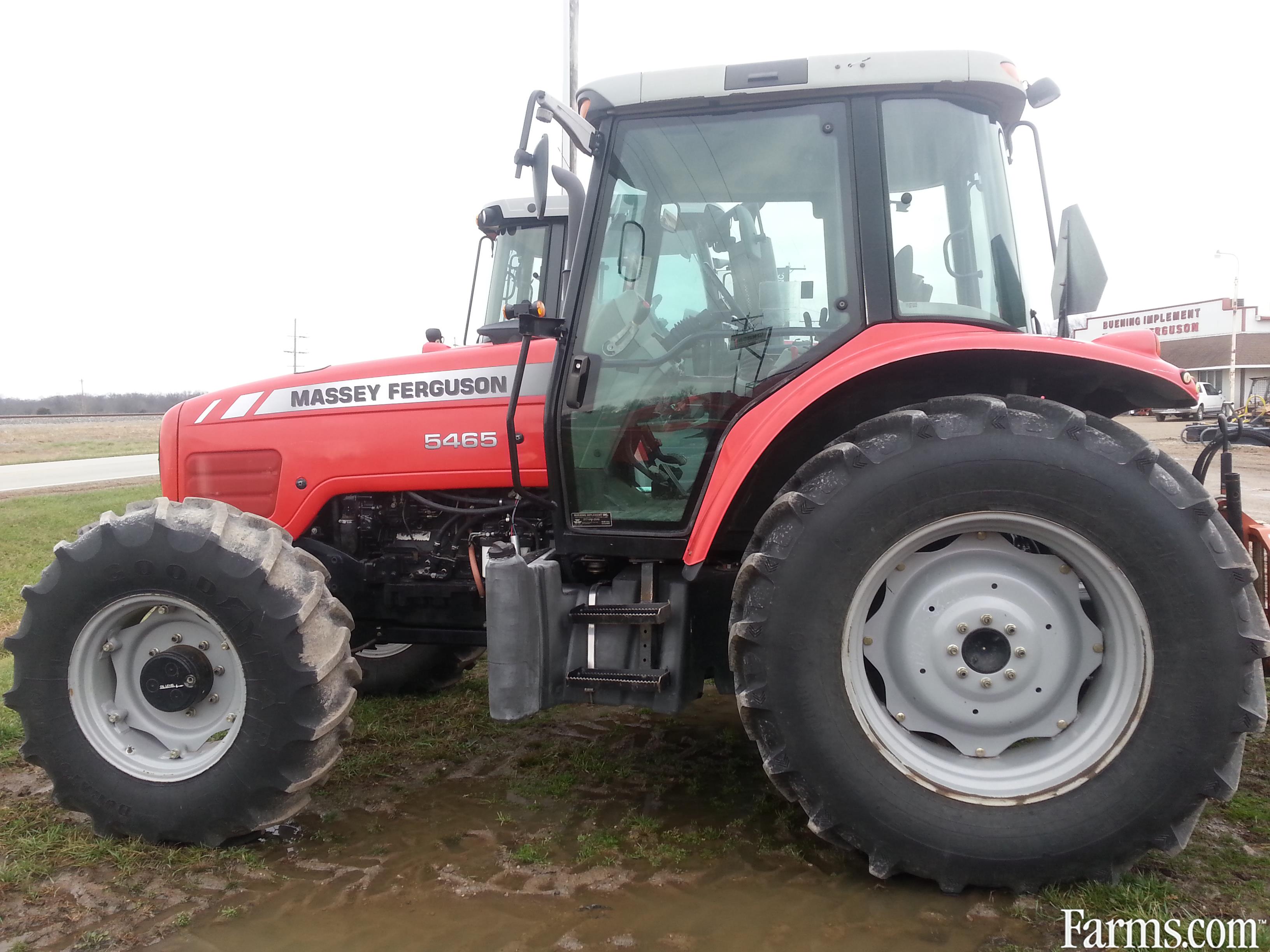
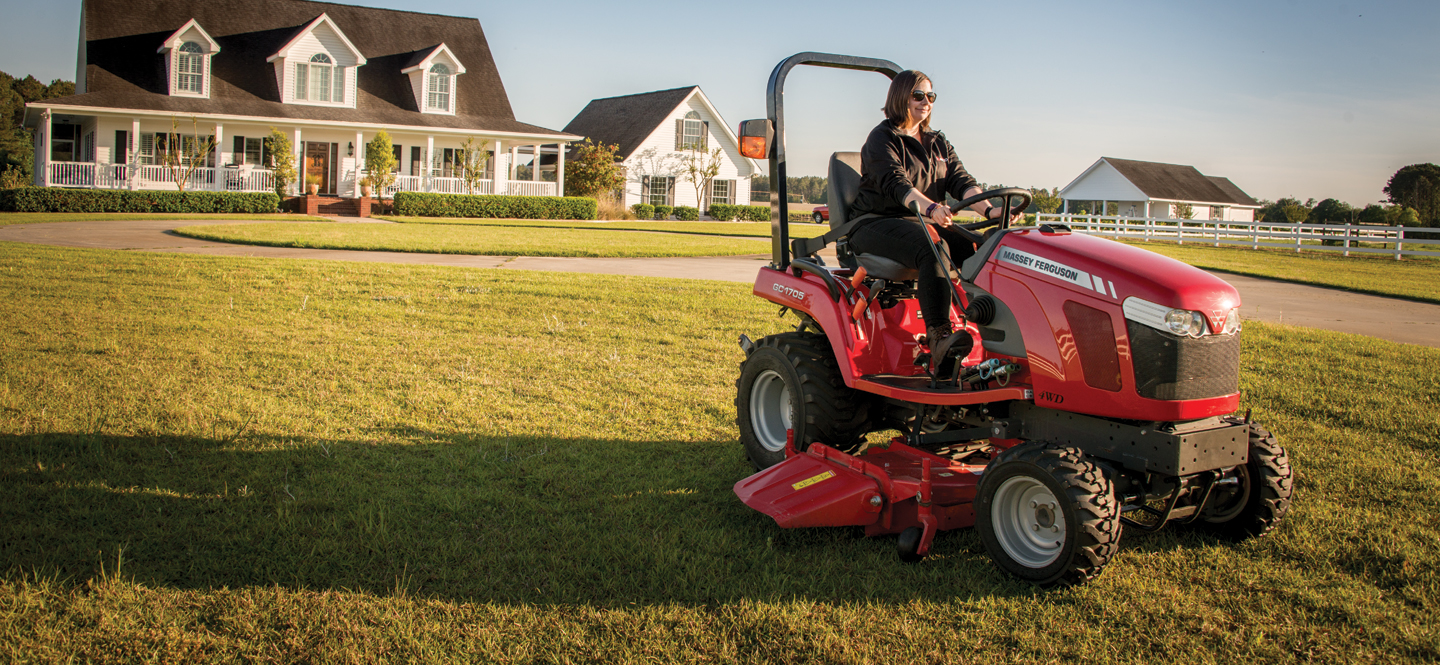
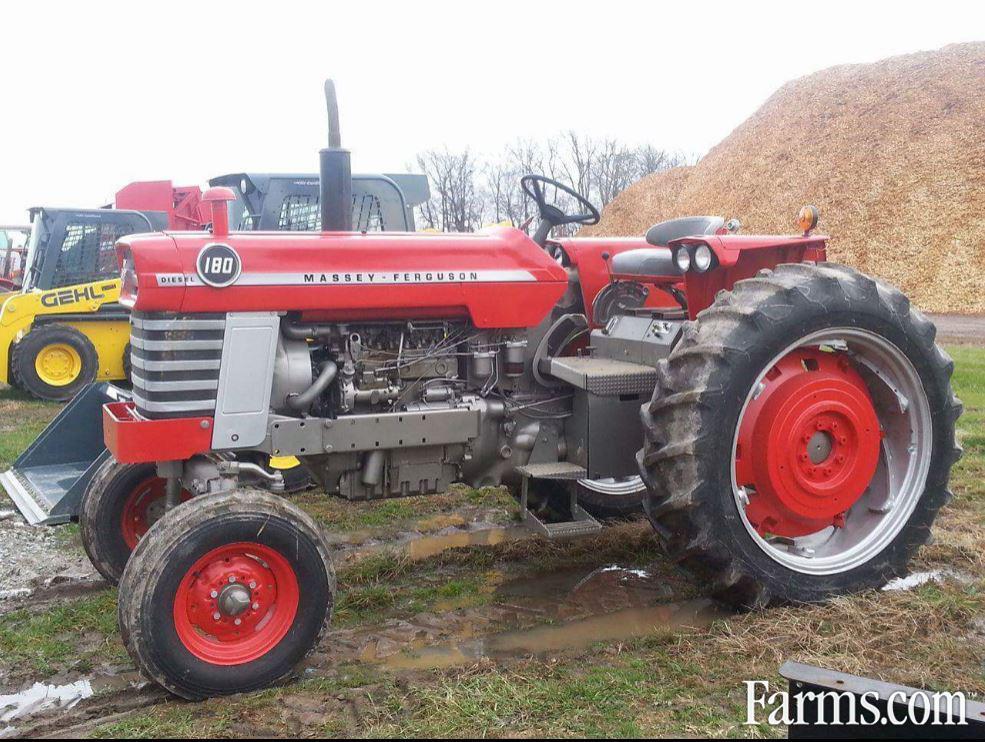