What are the implications of a dual approach in a specific context? A two-part process can yield significant results.
A two-part approach, or a procedure with two distinct stages, can refer to a variety of scenarios. It may describe a manufacturing technique in which a material is cut in two distinct phases, potentially with different tools or methods for each stage. In other contexts, it could represent a dual strategic method, such as a marketing campaign employing two complementary techniques, or a formal negotiation incorporating two phases of discussion and agreement. The crucial element is the intentional execution of two distinct operations, distinct in their intended purpose and outcome, yielding a complex or multifaceted result.
The value of this dual approach lies in its potential to achieve a more refined outcome than a single action. By separating the process into two elements, the precision and efficiency in each phase can be optimized. The complexity of the task or the nature of the material being handled may necessitate this division. Historical examples of techniques employing multiple phases are prevalent across industries from construction to scientific procedures, reflecting a deep understanding of the advantages of a meticulous and methodical approach.
Further exploration of this two-part procedure might investigate the specific industry or context where this concept is relevant. Analyzing the benefits and drawbacks of the two-stage process can provide a detailed and nuanced understanding of this technique.
Double Cut
Understanding the concept of "double cut" requires examining its multifaceted nature. The term likely refers to a process, technique, or method involving two distinct actions or stages. Identifying these critical components is essential for grasping its full implications.
- Precision
- Efficiency
- Two stages
- Material properties
- Tool selection
- Quality control
- Process optimization
- Error minimization
The listed aspects, viewed holistically, reveal a methodical approach. Precision and efficiency are paramount, relying on a deep understanding of material properties. Optimal tool selection and rigorous quality control further enhance the process. A two-stage process implies careful consideration of each stage, leading to process optimization and minimized errors. For instance, a double-cut diamond sawing method might employ two specialized stages in precisely shaping the gem: first a rough shaping, then a fine detail work. This methodical approach improves the overall output and ultimately the value of the final product.
1. Precision
Precision is fundamentally intertwined with a double-cut process. A double-cut method inherently demands high precision in each of its constituent stages. This meticulous attention to detail, in each step, is crucial for achieving a desired outcome. Without precise execution in both stages, the intended quality and final result may not be achieved. Consider a surgical procedure involving two distinct steps. High precision in each incision minimizes risk and maximizes the chances of a positive outcome. Similarly, in manufacturing, a two-stage cutting process necessitates precision in both cutting stages. Inaccurate initial cuts will compromise the effectiveness of the subsequent steps, hindering the final result. Examples abound. In the microelectronics industry, the creation of intricate circuits demands exceptional precision in both the masking and etching phases. In these highly complex processes, subtle errors in either step can cascade into significant problems, affecting the overall functionality of the final product.
The importance of precision as a component of a double-cut methodology extends beyond material handling. In fields like engineering and design, precise execution in both stages enables optimization and enhances the final product's functionality. For example, in civil engineering, meticulous planning and execution in different construction phases are crucial for maintaining structural integrity. This principle of precise execution in stages extends to virtually any area requiring careful and deliberate action. A precise initial step that guides and directs subsequent actions is vital in ensuring a final result aligning with the intended design. The practical significance of this understanding is evident in the need for meticulous detail in crafting and producing anything from finely tuned mechanical components to intricate artistic masterpieces.
In conclusion, the relationship between precision and a double-cut process is undeniable. Precise execution in both stages is essential for successful outcomes. The importance extends across diverse fields, from surgery to manufacturing, highlighting the critical role of meticulous detail in achieving desired results. Recognizing this connection allows for the optimization of procedures, minimizing errors, and maximizing the potential for achieving higher quality and improved functionality.
2. Efficiency
Efficiency is a critical component of a double-cut process. A two-stage approach, by its nature, demands optimization at each step. The effectiveness of the overall process hinges on the efficiency of both stages. Maximizing efficiency in each stage minimizes wasted effort, resources, and time. This, in turn, directly influences the overall outcome. For instance, a manufacturing process requiring two distinct cutting operations benefits significantly from the optimization of each stage. Streamlining the initial cutting phase reduces material waste, leading to higher yield and cost savings. Subsequent operations, performed efficiently, minimize the potential for errors and ensure higher quality products. Similarly, in project management, a project broken down into two phases can achieve optimal efficiency when each phase prioritizes time management and resource allocation.
Real-world examples illustrate the importance of efficiency in double-cut processes. In surgical procedures, a two-stage operation, such as a complex joint replacement, necessitates efficient execution in each stage to minimize patient recovery time. Efficient preparation and execution of the initial steps enable more efficient handling of the subsequent stage, reducing the overall recovery time and associated complications. In software development, a double-cut approach often manifests as a two-phase testing processunit testing and integration testing. Efficiently testing in both phases uncovers errors early, saving time and resources spent on debugging later stages. The meticulous optimization of each step contributes substantially to the project's overall efficiency.
The pursuit of efficiency in a double-cut process yields significant practical benefits across diverse fields. Improved resource utilization, reduced waste, and minimized errors are direct consequences. This efficiency directly impacts cost reduction, improved quality, and time saving. However, achieving optimal efficiency requires careful consideration of factors like resource allocation, workflow optimization, and the identification of potential bottlenecks in each stage. Understanding the interrelation between efficiency and a double-cut process empowers practitioners to develop streamlined workflows, optimizing the overall output of the project or procedure. This understanding fosters a greater appreciation for the value of methodical approaches in achieving desired results.
3. Two Stages
The concept of "two stages" is intrinsically linked to "double cut." A double-cut process, by definition, involves two distinct phases. This division is not arbitrary; it signifies a structured approach, recognizing that certain tasks or processes are best executed in sequential, well-defined steps. The necessity of two stages stems from the nature of the work, whether it involves material processing, surgical intervention, or complex problem-solving. The two stages might involve different tools, techniques, or materials, each uniquely addressing a specific aspect of the overall goal.
Consider precision metalworking. A double-cut process might involve first, a rough shaping using a milling machine, followed by a precise finishing operation with a lathe. This division allows for optimization of both stages. The rough cut removes excess material efficiently, while the subsequent stage refines the shape to exacting tolerances. The same principle applies in complex engineering projects, where a two-stage approach might include initial feasibility studies followed by detailed design and construction. This sequential approach prevents errors from propagating through the entire process. Similarly, in scientific research, a two-stage experiment might involve preliminary observations and then a controlled test to validate those observations, enhancing accuracy and reliability. The importance of two stages in a double-cut process hinges on its inherent ability to optimize efficiency and ensure accuracy.
The concept of two stages in a double-cut process demonstrates a structured methodology. It fosters a more controlled and methodical approach, enabling the task to be approached in manageable parts. Recognizing the significance of these two distinct stages offers a powerful tool for optimizing procedures, minimizing errors, and achieving desired results. This structured approach, by breaking down complex tasks into smaller, more easily manageable phases, leads to higher quality outcomes and greater overall efficiency, across numerous disciplines.
4. Material Properties
Material properties play a pivotal role in determining the suitability and effectiveness of a double-cut process. The inherent characteristics of the material directly influence the approach, tools, and techniques employed in each stage. Different materials exhibit varying degrees of hardness, ductility, and elasticity, impacting the precision and efficiency of the cutting process. For example, a brittle material might require a different cutting method than a ductile one. A brittle material, prone to fracturing under stress, necessitates careful selection of cutting tools and techniques to minimize chipping and breakage. Conversely, a ductile material might allow for greater flexibility in the cutting process, potentially enabling different cutting geometries and speeds. This sensitivity to material properties extends to the choice of cutting tools themselves. Choosing tools appropriate for the specific material's properties is critical for achieving a clean cut, minimizing material loss, and ensuring optimal results in each cutting stage.
Real-world examples abound. In the manufacturing of semiconductors, the extreme precision required demands an understanding of the material's properties. The material's inherent brittleness necessitates precise and controlled cutting methods, often involving laser or focused ion beam techniques. In contrast, the fabrication of some metals may allow for more aggressive cutting tools, since the material's ductility and strength can absorb greater stress. Construction materials, like concrete or wood, also exhibit specific characteristics influencing the cutting process. Concrete's hardness requires specialized tools and procedures different from those used to cut wood, where the material's grain structure and flexibility play a role in determining the best cutting strategies. The choice of cutting instruments and the sequence of operations are inextricably linked to material characteristics in each of these contexts. Understanding these relationships is essential for preventing material damage, optimizing yield, and ensuring the quality of the final product.
Recognizing the profound connection between material properties and double-cut processes highlights the importance of material characterization in various fields. This knowledge is critical for optimizing procedures, minimizing material waste, and ensuring high-quality outcomes. Understanding material properties in relation to double-cut methods not only enhances efficiency but also enables the development of innovative techniques tailored to specific material requirements. This underscores the profound influence of material science in guiding the choice of tools, procedures, and strategies for effective and efficient double-cut operations. Careful consideration of material properties is crucial for mitigating potential issues like breakage, deformation, or contamination, leading to significant improvements in final product quality and overall project success.
5. Tool Selection
The selection of appropriate tools is inextricably linked to the success of a double-cut process. The effectiveness of each stage hinges critically on the tools employed. Appropriate tool selection ensures precision, efficiency, and safety during both stages. The chosen tools must match the material's properties and the specific requirements of each cutting stage. Inadequate tool selection can lead to significant issues, including material damage, reduced productivity, and potential safety hazards. A suboptimal tool can cause premature wear, dulling, or breakage, impacting both the quality and efficiency of the entire process.
Real-world examples underscore the importance of careful tool selection. In precision machining, the correct cutting tools are essential for achieving precise dimensions and tolerances. Selecting the wrong toolone not designed for the specific material or intended cutcan result in inaccuracies, leading to costly rework or product failure. In surgical procedures, choosing the proper instruments is paramount for minimizing tissue damage and ensuring the precision needed during each stage of the operation. The slightest misjudgment in instrument selection can have significant consequences. In construction, selecting appropriate cutting tools for concrete, wood, or metal is crucial. Using the wrong tools can damage the material, reduce efficiency, and compromise the structural integrity of the finished product. These varied contexts demonstrate the universal need for carefully considering tool selection in a double-cut approach.
Careful consideration of tool selection in a double-cut process is crucial for optimizing outcomes. Matching the tools to the material properties and stage requirements ensures precision, efficiency, and safety. Understanding this connection between tool selection and the double-cut process enables practitioners to make informed decisions, leading to higher quality outputs and minimizing potential issues. Moreover, appreciating the significance of tool selection enhances productivity by ensuring that the process can operate at its optimal level, minimizing downtime and maximizing resource utilization.
6. Quality Control
Quality control is intrinsically linked to a double-cut process. The effectiveness of the second stage in a double-cut procedure directly relies on the quality of the initial stage. A high-quality outcome hinges on meticulous quality control measures implemented throughout both stages. Defects or inaccuracies arising in the first stage can propagate through to the second, compromising the final product's quality. Rigorous quality checks in each stage ensure that defects are identified and corrected before they escalate, ultimately enhancing the quality of the final product. This preventative measure is critical for industries where precision and durability are paramount.
Real-world examples illustrate the significance of quality control in double-cut processes. In microchip fabrication, the initial stagea photolithographic processlays the foundation for the intricate circuits. Any imperfections in this stage can lead to circuit malfunctions. Subsequent stages will be similarly compromised. Rigorous quality control measures, including meticulous inspection and testing at each step, are essential to identify and correct these defects. In surgical procedures, a double-cut technique, like a complex orthopedic repair, requires meticulous quality control in both stages. Imperfections in the initial incision or bone preparation can lead to complications during the second stage and negatively affect the patient's recovery. Accurate assessment of the initial condition and meticulous execution throughout are vital to patient well-being. Similar methodologies and quality control requirements are applicable to a wide range of scenarios, from manufacturing automotive parts to constructing bridges.
Effective quality control in a double-cut process necessitates a systematic approach. Comprehensive documentation of procedures, rigorous testing protocols, and clear communication between stakeholders are critical. Implementing these methods minimizes the likelihood of errors, ensures consistent results across various iterations, and contributes to the overall efficiency and reliability of the process. This, in turn, reduces rework, boosts productivity, and results in products meeting stringent quality standards. By incorporating thorough quality control into every stage of a double-cut process, organizations can maximize the potential for high-quality outcomes while minimizing risks. This structured approach to quality control is crucial for maintaining consistent product quality and ensuring customer satisfaction. The preventative nature of quality control, especially in double-cut processes, emphasizes the importance of addressing potential issues proactively rather than reactively, thus minimizing costs and maximizing efficiency.
7. Process Optimization
Process optimization is a crucial component of a double-cut approach. Optimizing each stage of a two-part process directly affects the overall efficiency and effectiveness. By meticulously analyzing each phaseidentifying bottlenecks, inefficiencies, and potential errorsprocesses can be streamlined. This enhanced efficiency translates into reduced costs, minimized waste, and a higher-quality end product. Consider a manufacturing scenario: optimizing the first cut in a two-stage machining process, for example, reduces material waste and improves the precision of the subsequent cutting stage, thereby increasing overall yield and reducing rework. Similarly, in a two-stage surgical procedure, process optimization, involving precise planning and preparation, minimizes complications and enhances the effectiveness of the second stage.
The importance of process optimization extends beyond individual stages to encompass the entire double-cut process. This involves analyzing the interaction between the two stages. Efficient workflows, minimized idle time, and seamless transitions between stages are essential. For instance, in software development, optimizing the unit testing phase of a two-stage testing processby employing appropriate testing frameworks and techniqueswill reduce the time spent on debugging during the integration testing phase, thus improving the overall development cycle's efficiency. Similarly, in project management, a thorough understanding of resource allocation and task sequencing during a two-phased project can lead to significant improvements in the project's overall timeline and budget. Practical application necessitates meticulous data collection and analysis to identify areas for improvement and support informed decision-making.
In conclusion, process optimization is fundamental to a successful double-cut approach. By strategically optimizing both individual phases and their interaction, organizations can significantly improve efficiency, reduce costs, and enhance the quality of the final outcome. This principle is applicable across diverse fields, from manufacturing and healthcare to software development and project management. Recognizing the symbiotic relationship between process optimization and a double-cut methodology empowers organizations to make data-driven decisions and consistently improve the effectiveness and efficiency of their processes.
8. Error Minimization
Error minimization is a critical consideration in any process employing a double-cut approach. The inherent nature of a two-stage methodology necessitates a proactive strategy to mitigate potential errors at each juncture. Minimizing errors in both stages is essential for the overall success and reliability of the final product or outcome.
- Early Detection and Correction in Stage 1
Implementing rigorous quality control at the initial stage can identify and correct errors early in the process. This preventative approach significantly reduces the likelihood of errors propagating to the subsequent stage. For example, in manufacturing, meticulously inspecting raw materials and tools at the beginning of a production line minimizes the introduction of defects. In software development, thorough unit testing in the initial stage can pinpoint and resolve errors before they affect the larger system during integration.
- Independent Validation in Stage 2
A second stage, designed independently from the first, allows for a separate validation of the outcome of the initial work. This independent verification helps to identify and correct errors introduced in the first stage. Surgical procedures, with their inherent complexity, often employ double-checks of measurements and preparations to reduce surgical risks. In construction, double-checking blueprints and measurements before a major construction phase helps to minimize errors that can affect the entire building's integrity.
- Redundancy and Backup Procedures
Redundancy in procedures and backup plans provide safety nets to address potential errors. If a critical calculation or step proves erroneous in one stage, an alternative or secondary procedure can address the problem. In data entry, the use of redundant data-entry systems and double-checking by a second operator minimizes errors. In complex financial systems, redundant security protocols and approval processes lessen the risk of fraudulent activity.
- Process Standardization and Documentation
Standardizing procedures and documenting them clearly helps maintain consistency and reduce the potential for human error. A well-defined and documented process minimizes ambiguities and ensures that everyone involved follows the same protocol. Precise documentation and standard operating procedures (SOPs) are fundamental in clinical settings, ensuring consistent treatment for patients. Manufacturing industries rely on documented procedures to prevent variation in the production process and minimize inconsistencies.
Incorporating these facets of error minimization in a double-cut process ensures a more robust and reliable outcome. By addressing potential errors proactively and through multiple layers of checks and balances in each stage, the risk of defects being propagated to later stages is significantly mitigated. This results in a higher-quality and more reliable final product or outcome, be it a manufactured good, a surgical procedure, or a software application.
Frequently Asked Questions about "Double Cut"
This section addresses common inquiries concerning the double-cut methodology, providing clear and concise answers to typical questions.
Question 1: What precisely constitutes a "double-cut" process?
A "double-cut" process describes a method involving two distinct stages or phases. This sequential approach is not arbitrary; it's a structured methodology designed to maximize precision, efficiency, and the overall quality of the final product. Crucially, each stage of a double-cut process serves a unique, often complementary, purpose within the larger procedure.
Question 2: What are the key advantages of using a double-cut approach?
A double-cut process offers several advantages, primarily through optimized precision and efficiency. By separating complex tasks into distinct stages, the meticulous execution of each stage can be optimized. This allows for error minimization, enhanced quality control, and reduced waste. The method's value also lies in its ability to allow for a more rigorous evaluation of initial results before proceeding to the final phase.
Question 3: What role do material properties play in a double-cut process?
Material properties significantly influence the methodology and tools used in each stage. Understanding the material's characteristicshardness, ductility, elasticityis crucial for selecting appropriate tools, techniques, and procedures for both stages. Failure to account for these properties can compromise the effectiveness and potentially damage the material being processed.
Question 4: How does quality control integrate into the double-cut process?
Quality control is paramount throughout both stages. Regular and thorough inspections at each stage are vital. Implementing procedures to identify and rectify errors early prevents propagation of defects to the subsequent stage, ensuring the final product aligns with established quality standards.
Question 5: Can you provide examples of double-cut processes across different fields?
Examples of double-cut processes are numerous. In manufacturing, a two-stage machining process exemplifies a double-cut approach, where initial rough shaping is followed by precise finishing. In surgical procedures, a two-stage operation, such as a complex joint replacement, showcases the structured methodology inherent in the process. The concept is applicable to numerous fields, from engineering and design to scientific research.
In summary, the double-cut process represents a structured methodology that, when properly implemented, leads to more precise, efficient, and higher-quality outcomes. Understanding the interconnectedness of the various components is critical for optimized application across various fields.
This concludes the FAQ section. The subsequent sections will delve deeper into the practical application and implications of double-cut processes in diverse contexts.
Conclusion
This exploration of the double-cut process underscores its multifaceted significance across diverse fields. Key elements such as precision, efficiency, material properties, and quality control emerge as essential components. The two-stage approach, with its methodical division of tasks, facilitates meticulous execution, minimizes errors, and optimizes outcomes. Proper tool selection, rigorous quality control measures, and a structured methodology, as seen in examples from manufacturing to surgery, contribute to the overall effectiveness and reliability of the process. Process optimization, crucial for streamlining the interactions between the distinct stages, further enhances efficiency. By analyzing the implications of the double-cut process, the importance of this methodological approach in achieving high standards of quality and reliability becomes evident. The implications extend from minimizing waste and maximizing output to enhancing accuracy and reducing the potential for errors.
The double-cut methodology, with its emphasis on precision and meticulous execution, offers a valuable framework for problem-solving and process improvement in various domains. The exploration presented here highlights the systematic nature of the approach and its profound impact on quality and reliability. Future investigation into specific applications and further analysis of its nuances are encouraged to explore potential adaptations and improvements for complex tasks across a broader spectrum of fields. Recognizing the fundamental principles of the double-cut process empowers practitioners and stakeholders to optimize existing processes and develop innovative strategies for achieving exceptional outcomes.
- Best Osteria Consani Deals Reviews Experience Authentic Italian Cuisine
- Top Hillary Carnell Quotes Insights
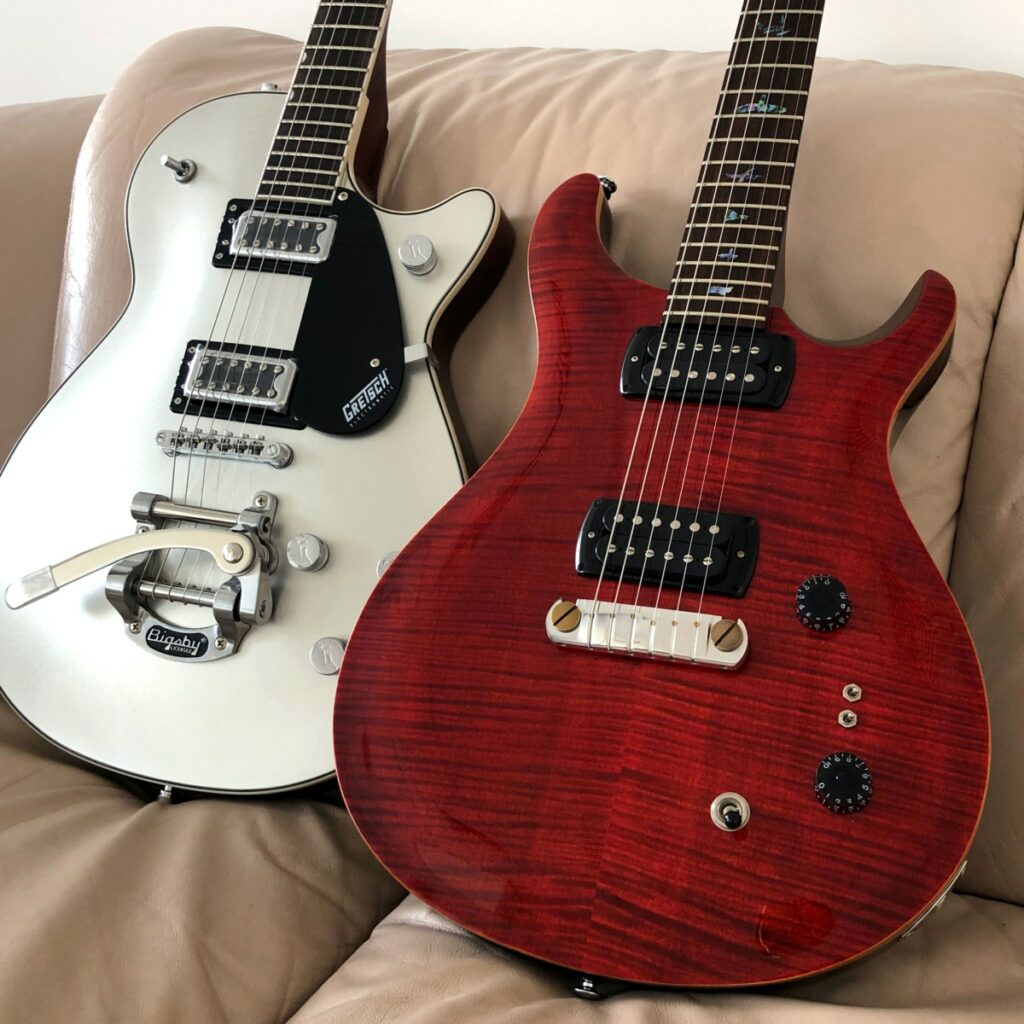
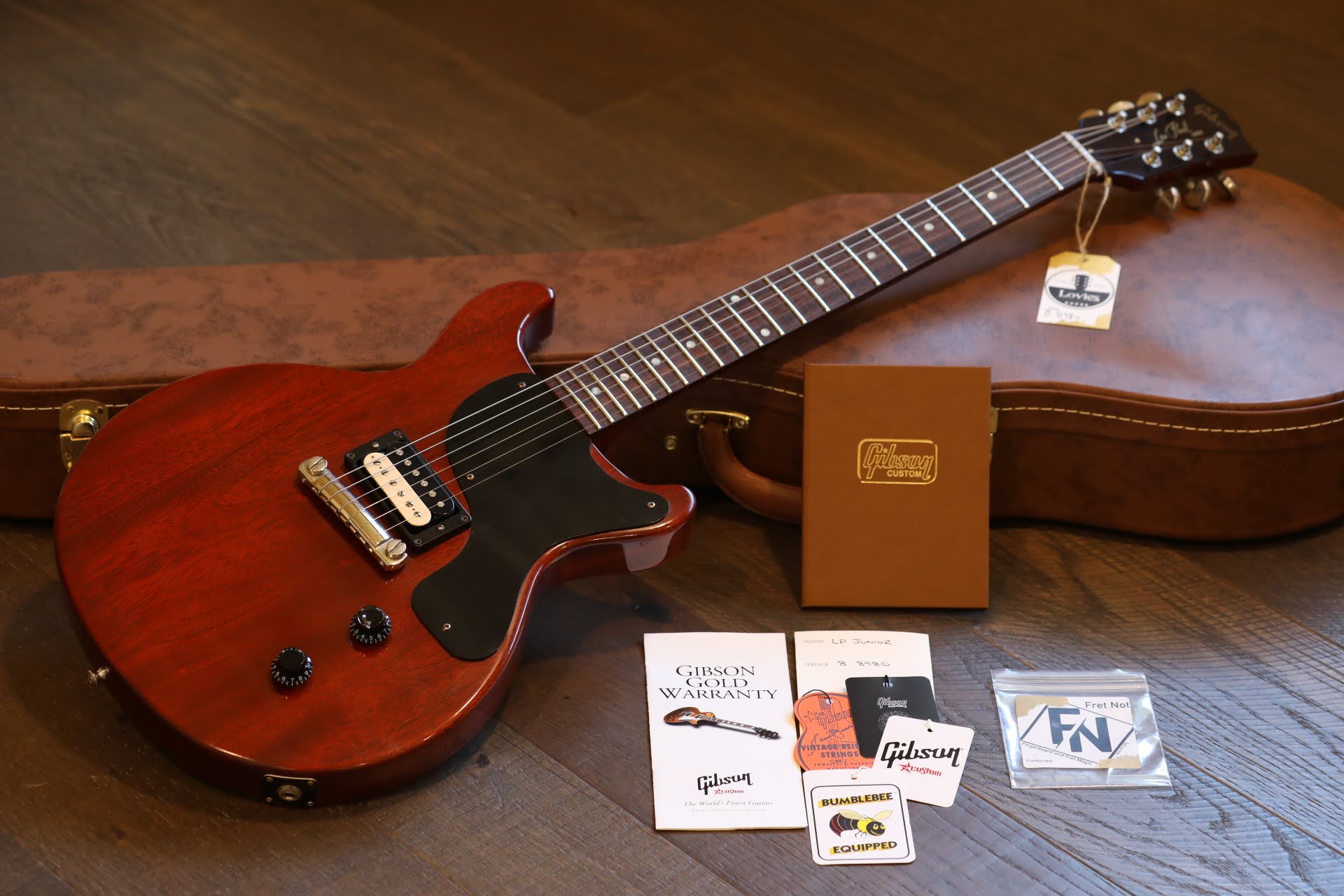
