What are computer-controlled numerical methods, and why are they so important in modern manufacturing?
Computer-controlled numerical methods, often abbreviated, are a set of mathematical and computational techniques used to precisely control machine tools. These methods translate digital instructions into physical actions, enabling intricate and repeatable patterns in manufacturing processes. For instance, they dictate the precise movements of a milling machine to carve complex shapes into a workpiece, or direct a laser cutter to follow a pre-defined pattern. This allows for high accuracy and efficiency compared to manual methods.
The application of these methods has revolutionized manufacturing, enabling the production of high-precision parts, customized products, and improved efficiency. They allow for the creation of parts that were previously impossible to manufacture. Moreover, the standardized nature of the commands ensures consistent quality across numerous products. The methodology emerged alongside the advancement of computing power and the design of specialized software. The benefits are readily apparent, particularly in sectors requiring high precision, such as aerospace, automotive, and medical device manufacturing.
Moving forward, let's explore the diverse applications of these methods within various industries. The detailed process and considerations will form the core of the following article.
CNCs
Computer Numerical Control (CNC) systems are critical in modern manufacturing, enabling intricate and precise parts production. Understanding their fundamental components and operation is crucial for effective implementation.
- Precision
- Automation
- Repeatability
- Material Removal
- Complex Shapes
- Programmability
CNCs excel in precision due to their ability to follow detailed instructions with minimal human intervention. Automation is inherent to the process, drastically reducing operator error. Repeatability is paramount, ensuring consistent production of parts. Material removal is a key function, accomplished through controlled cutting tools. CNCs facilitate the creation of complex, multi-faceted shapes. Programmability allows for customized modifications to the production workflow, further enabling the fabrication of a vast array of objects. Taken together, these aspects provide the capability for efficient and customized manufacturing, as seen in industries like aerospace and automotive, where precise parts are essential.
1. Precision
Precision is fundamental to the efficacy of computer numerical control (CNC) systems. The ability to achieve extremely precise measurements and movements in manufacturing processes hinges on the accuracy and reliability of CNC operations.
- Dimensional Accuracy
CNCs excel in maintaining precise dimensions. This accuracy is critical in manufacturing parts that must fit together seamlessly, such as components in machinery or intricate assemblies. Highly precise tolerances, often measured in fractions of a millimeter, are routinely achieved. Examples include engine blocks in automotive manufacturing or medical implants requiring exacting dimensions for functionality and safety.
- Repeatability of Movements
The programmed instructions within CNC systems ensure consistent movement. This repeatability is essential for creating identical parts, crucial for batch production and quality control. Every machined component will be produced within the designated tolerances, assuring consistency in critical applications.
- Controlled Material Removal
CNC machining relies on precisely controlled material removal. This precision in cutting and shaping ensures parts meet exact specifications and minimizes waste. Precise control over toolpaths and speeds is paramount, leading to efficient material utilization and minimizing the generation of unwanted material.
- Reduced Manufacturing Errors
The inherent precision of CNC programming minimizes errors compared to manual methods. The direct transfer of digital instructions to machine movements results in reduced human error, especially in complex or intricate operations. This factor significantly improves consistency in the manufacturing process.
In summary, the precision offered by CNC systems is a key driver of their widespread adoption. This precision directly impacts the quality, consistency, and efficiency of manufactured products, making CNC technology indispensable in many modern manufacturing applications.
2. Automation
Automation is inextricably linked with computer numerical control (CNC) systems. The core function of CNCs is to automate the manufacturing process, leading to enhanced efficiency, reduced human error, and increased productivity. This automation is achieved through the direct translation of digital instructions to machine movements, removing the need for manual intervention in many tasks.
- Elimination of Human Error
CNC systems dramatically minimize the potential for human error, a significant advantage in high-precision manufacturing. Human operators, susceptible to fatigue, variations in technique, and occasional mistakes, are replaced by machines following rigidly defined instructions. This automated precision leads to consistent product quality and reduced rework, enhancing manufacturing output.
- Increased Production Rate
Automation via CNC significantly accelerates production rates. Machines can operate continuously, 24/7, without the need for breaks or rest, whereas human operators are constrained by physical limitations. This enhanced throughput translates to a higher volume of products in a given timeframe, and a faster turnaround for production runs.
- Improved Repeatability
The programmed nature of CNC operations guarantees consistent and repeatable results. Every part produced follows the same precise instructions, leading to consistent dimensions, shapes, and surface finishes. This ensures parts are interchangeable and fit together seamlessly, essential for assembly-line manufacturing.
- Enhanced Safety
Certain manufacturing processes using CNC systems involve potentially hazardous tasks. Automation can transfer these operations to machines, reducing risks to human operators. CNC-controlled machinery can perform high-speed cutting or repetitive grinding without requiring direct human contact with the equipment, mitigating safety hazards.
In conclusion, the automation inherent in CNC systems fosters efficiency, consistency, and safety in the manufacturing process. This automated precision translates into enhanced quality control, quicker production times, and a lower error rate, making CNC technology a crucial component of modern manufacturing.
3. Repeatability
Repeatability is a critical component of computer numerical control (CNC) systems. The ability of a CNC machine to consistently produce identical parts from successive machining operations is fundamental to its effectiveness. This precision stems from the programmed nature of the operations, where digital instructions dictate every movement of the cutting tools. The machine's mechanical design also plays a critical role, ensuring consistent positioning and force application. The absence of human error in these processes is a key factor underpinning repeatability.
Consider the manufacturing of engine components. The precise tolerances required for engine block cylinders necessitate high repeatability in the machining process. Variations in the size or shape of these components can lead to engine failure or reduced performance. Similarly, in the production of medical implants, repeatability ensures the implants meet the exact specifications required for functionality and safety. Each implant needs to be identical to the others for proper function and to minimize complications. The consistent quality maintained by CNC systems is pivotal in these situations, where variation can have serious consequences.
In summary, repeatability in CNC systems is essential for consistency and quality in manufactured products. This is achieved by the reliable execution of pre-programmed instructions by the machines, leading to standardized dimensions and characteristics across a batch of products. The precision and reliability of CNC systems, stemming from their repeatability, are vital for meeting the stringent demands of modern manufacturing in diverse industries, from automotive to aerospace to healthcare.
4. Material Removal
Material removal is a fundamental process inherent in computer numerical control (CNC) systems. CNCs excel in precisely controlling cutting tools to remove material, enabling the creation of intricate shapes and complex parts. The accuracy and repeatability of this material removal process are critical to the success of many modern manufacturing operations. This process involves a sophisticated interplay of programmed instructions, tool selection, and machine control to effectively and efficiently shape raw materials into desired forms. Examples include milling, drilling, and turning operations, all of which rely on controlled material removal to achieve the targeted geometry and dimensions.
The precision in material removal with CNC systems is crucial for achieving tight tolerances. In aerospace manufacturing, for example, the intricate components of aircraft engines require precise machining to ensure proper function and structural integrity. The ability of CNCs to precisely remove material ensures these components fit together seamlessly and function as intended. Likewise, in the automotive industry, CNC-based milling and drilling allow manufacturers to create high-precision engine blocks and other complex parts. This capability extends to medical device manufacturing, where consistent and accurate material removal is essential for the creation of surgical instruments and implants. In these contexts, the accuracy of material removal dictates both the functionality and safety of the final product.
Understanding the intricacies of material removal in CNC contexts is crucial for maximizing efficiency and minimizing waste. Optimal tool selection and cutting parameters are critical factors influencing the process's effectiveness. Considerations include the type of material being worked with, the desired finish, and the required tolerances. Inappropriate selection of tools and cutting conditions can lead to inaccuracies, reduced production rates, and increased material waste, impacting the overall manufacturing cost and timeline. Expertise in material removal methodology is therefore paramount in streamlining CNC operations and driving cost-effective production. The optimization of this process directly impacts the competitiveness and profitability of companies involved in machining operations.
5. Complex Shapes
The ability to manufacture complex shapes is a significant advantage of computer numerical control (CNC) systems. CNC machining's precision and programmability enable the creation of intricate parts impossible or impractical to produce using traditional methods. This capability is crucial in various industries where customized or highly detailed components are required. The connection between CNCs and complex shapes is multifaceted, involving precision in material removal and the sophistication of control algorithms.
- Enhanced Design Flexibility
CNC technology empowers designers with a wider range of design options. Complex geometries that were previously challenging or economically infeasible to manufacture are now viable with CNC. This translates into innovative product designs, leading to improved performance, enhanced aesthetics, and increased functionality. Examples include intricate aerospace components, medical implants with complex internal structures, and artistic sculptures.
- Precise Material Removal Capabilities
The programmable nature of CNC systems allows for intricate control of cutting tools, enabling the precise removal of material in complex shapes. This precision is crucial for achieving the tight tolerances and intricate details demanded by modern manufacturing. Specialized cutting tools and sophisticated algorithms are designed for specific materials and shapes. Complex geometries are handled by detailed tool paths, removing material in controlled layers to create the desired shape.
- Advanced Programming Capabilities
CNC systems use sophisticated programming languages to define the precise movements of cutting tools. This programming enables the creation of complex tool paths needed for intricate shapes, eliminating the need for extensive manual intervention and reducing errors. The programming is tailored to the specific shape, the material being machined, and the desired finish, maximizing the efficiency and precision of the manufacturing process. Advanced software allows for complex geometric modeling and simulations of the machining process, further increasing the accuracy in producing complex shapes.
- Reduced Manufacturing Costs in the Long Run
While initial setup for complex shapes may seem more costly, the ability to produce customized and high-precision parts in a single process streamlines manufacturing, often leading to reduced overall costs. Minimized wasted material and a shorter lead time, compared to alternative methods, result in increased efficiency. This effect, especially in small-batch production or specialized product manufacturing, demonstrates the long-term economical advantage of CNC systems, even when dealing with complex shapes.
In conclusion, the relationship between CNCs and complex shapes is a crucial synergy. The capabilities of CNC machining extend the possibilities of design and manufacturing, enabling a wide range of complex parts. The combination of precision control, sophisticated programming, and efficient material removal allows for the production of intricate shapes, ultimately improving the functionality, aesthetics, and cost-effectiveness of manufactured products across numerous industries.
6. Programmability
Programmability is a defining characteristic of computer numerical control (CNC) systems, intrinsically linked to their operational effectiveness and versatility. The ability to program a CNC machine dictates its capabilities in terms of shaping materials. This programming is fundamental, dictating the precise movements and actions of cutting tools, resulting in the creation of intricate designs and the production of complex parts.
The importance of programmability in CNC systems extends beyond mere automation; it facilitates customization and adaptability. A single CNC machine can be programmed to execute a wide array of tasks, from drilling precise holes in metal plates to carving intricate sculptures in wood. This flexibility enables manufacturers to produce diverse parts from a single machine, optimizing efficiency and reducing the need for specialized tools or machinery for each operation. For instance, the same CNC milling machine can be programmed to create a variety of engine components for automobiles or precisely shaped components in aerospace manufacturing, without needing separate, dedicated equipment for each task. The adaptability granted by programmability makes CNC machines highly efficient in diverse manufacturing environments. Furthermore, changes in design or specifications are easily implemented by altering the program without requiring physical adjustments to the machine itself.
Understanding the relationship between programmability and CNC machines is critical for maximizing efficiency and productivity in modern manufacturing. The ability to tailor the machine's actions through detailed programming enables manufacturers to produce parts with exceptional precision and repeatability. This direct control over the machining process significantly reduces human error, leading to greater consistency in product quality and a higher yield rate. Additionally, this programmable nature allows for the creation of complex and intricate shapes that were previously unattainable or uneconomical with traditional methods, fostering innovation in design and engineering. The flexibility afforded by programmable CNC systems is a crucial driver of their widespread adoption across numerous industries, enabling manufacturers to respond quickly to changing market demands and customer needs.
Frequently Asked Questions about CNCs
This section addresses common inquiries regarding Computer Numerical Control (CNC) systems. Understanding these frequently asked questions will provide a clearer comprehension of the technology and its applications.
Question 1: What is a CNC machine?
A CNC machine is a type of machine tool controlled by a computer. Instead of manual operation, digital instructions govern the movements and actions of cutting tools, enabling precise and repeatable production of parts. This differs from traditional machine tools, which require human intervention for each movement.
Question 2: What are the benefits of using CNC machines?
CNCs offer several advantages, including high precision, enhanced repeatability, increased production speed, and reduced human error. They facilitate the creation of complex shapes and the customization of parts, contributing to improved product quality and efficiency within manufacturing processes.
Question 3: What types of materials can CNC machines work with?
CNC machines are capable of working with a wide range of materials, including metals (steel, aluminum, brass), plastics, composites, and wood. The specific capabilities depend on the machine's design and the type of cutting tool used. Selecting the appropriate tool for the material is critical for effective and safe machining.
Question 4: How does programming a CNC machine work?
Programming CNC machines involves creating a set of instructions that define the movements of cutting tools. These instructions are often generated using Computer-Aided Design (CAD) software and translated into a format understandable by the CNC machine's control system. This translation, called "numerical control," allows the machine to follow the instructions precisely.
Question 5: What are the potential drawbacks of using CNC machines?
While CNCs offer numerous benefits, potential drawbacks include the initial investment cost of purchasing and maintaining the equipment, as well as the complexity of programming for intricate designs. Specialized training for operators is also frequently necessary.
In conclusion, CNC technology plays a pivotal role in modern manufacturing, offering precision, efficiency, and flexibility in part production. The technology's strengths and limitations need careful consideration within a manufacturing context. This should assist readers in better understanding the capabilities and context of CNC systems.
Next, we will delve into the specific applications of CNC technology within various industries.
Conclusion
Computer Numerical Control (CNC) systems represent a significant advancement in manufacturing. The article has explored the core principles underpinning CNC technology, including its precision, automation, repeatability, and ability to handle complex shapes. Key features like programmability and the controlled material removal process are central to its operational efficiency. CNC's adaptability to diverse materials and complex designs is highlighted, demonstrating its versatility in various industries. The discussion underscored the crucial role of precision in ensuring consistent quality and meeting rigorous tolerances, particularly in demanding sectors like aerospace and automotive manufacturing. The benefits extend to increased productivity, reduced human error, and improved safety standards within production environments.
The evolution of CNC technology continues, with ongoing advancements in software, cutting tools, and machine design. Future applications and developments in robotics, automation, and additive manufacturing will further integrate and enhance the functionalities of CNC systems. This integration promises to revolutionize production processes, leading to increased efficiency, customized solutions, and a rise in sophisticated and complex manufactured goods. Continuous exploration and adaptation of CNC methodologies will be critical to maintain competitiveness and drive innovation in the manufacturing sector.
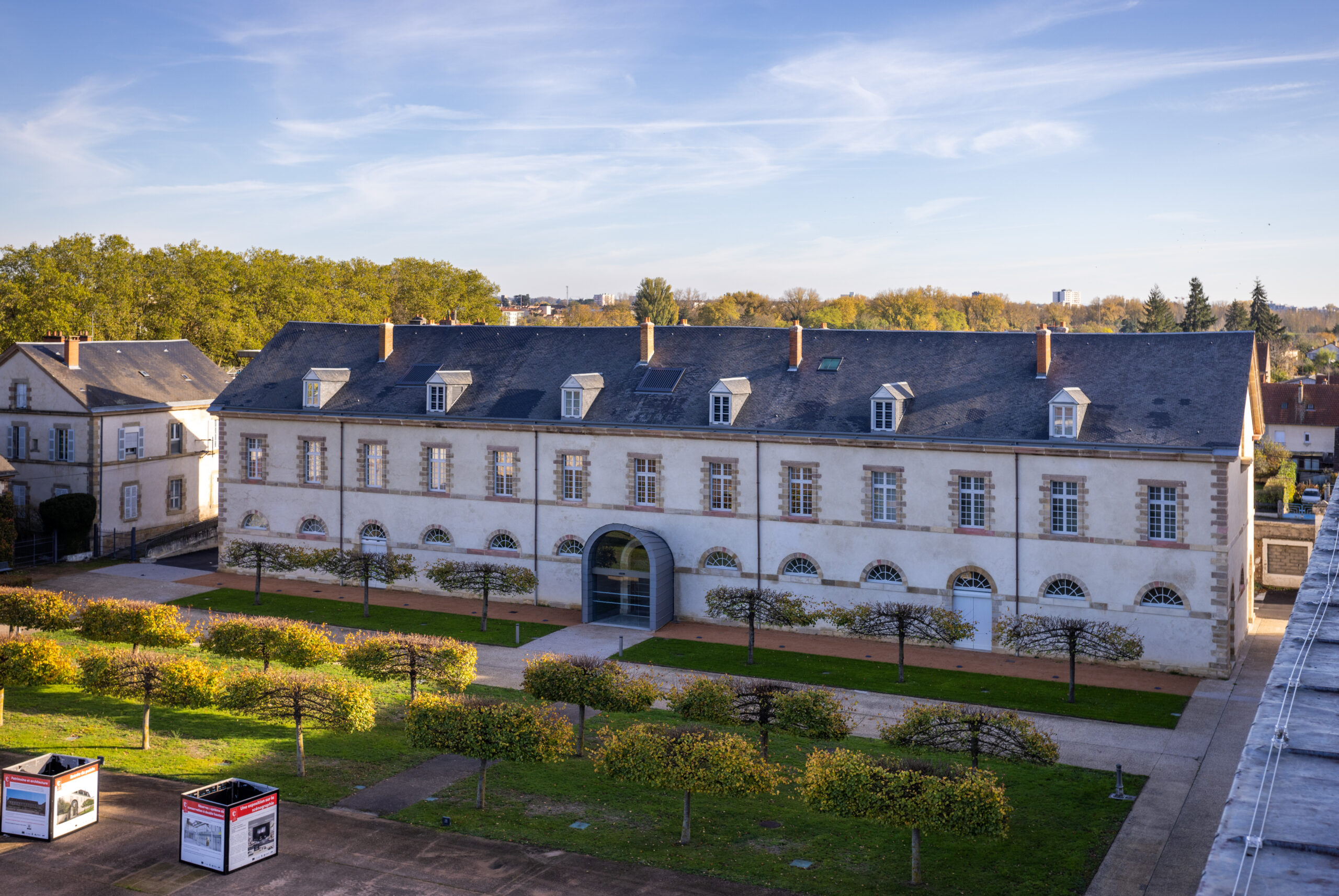
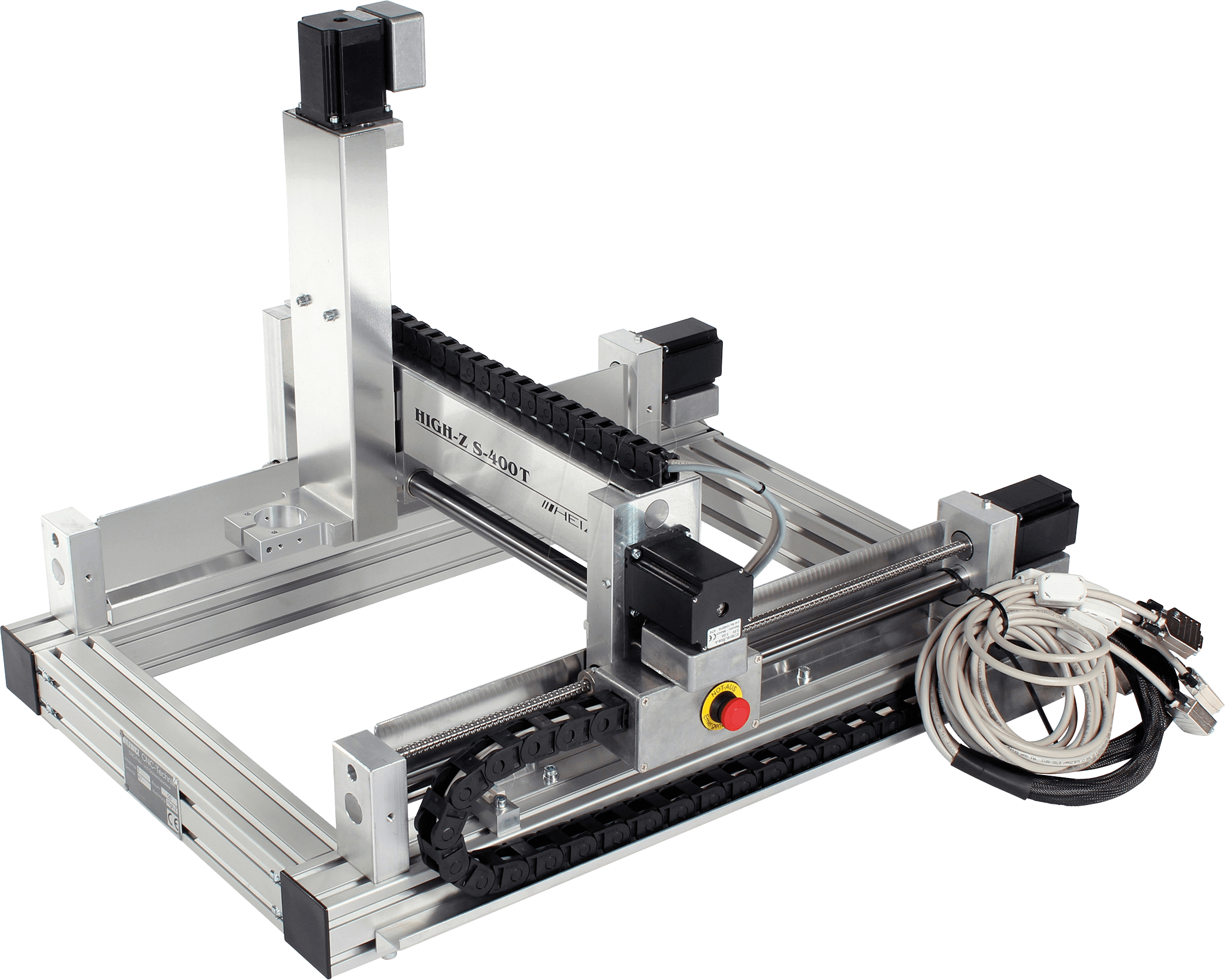
